Disclaimer: State or local health department immunization programs may recommend or
require different inventory accounting practices and different forms from those
described here. The information presented here is meant to provide general
guidelines only. Contact the state or local health department immunization
program staff for details about inventory accounting practices and follow their
recommendations.
Limit access to the vaccine supply to authorized
personnel only. |
Limit access to the vaccine supply to authorized
personnel only. This will help protect the vaccine supply by
avoiding inappropriate removal of vaccine or inappropriate handling
of vaccine and vaccine storage units by untrained personnel.
Interpreting
Expiration Dates
All vaccines and diluents have expiration dates.
The expiration date is the date
by which the vaccine or diluent should be used. This date is printed
on all
vaccine and diluent vials and boxes. Expiration dates vary by the
type of vaccine
or diluent, and by the lot number. The vaccine or diluent may be used up to and including this date unless otherwise stated in the product package insert. Vaccine and diluent should not be used after
this date has
passed. When the expiration date is marked with only a month and
year, the
vaccine or diluent may be used up to and including the last day
of the month
indicated on the vial. Any unused vaccine or diluent should not
be used after
this month has passed.
|
|
Vaccine may be used up to and including the expiration date. |
What
to Do with Expired and Mishandled Vaccine or Diluent
Expired vaccine and diluent, even if they are only
1 day past the expiration date, should never be administered. Likewise,
vaccines that have been mishandled and lost their potency because
of inappropriate storage conditions should not be administered.
If a dose of expired or mishandled vaccine is given by mistake,
the dose should not be counted as valid and should be repeated,
unless serologic testing indicates that an adequate response to
the vaccine has been achieved. Promptly remove expired or mishandled
vaccine and diluent from the refrigerator or freezer and dispose
of it appropriately. Contact the vaccine supplier, which may be
the vaccine manufacturer or the state health department immunization
program, for specific policies regarding the disposition of mishandled
or expired vaccine. If the expired vaccine is publicly purchased,
contact your state health department immunization program for instructions on returning expired vaccine for excise tax credit.
Exceptions
to the Expiration Date
The expiration date printed on each vial or box
assumes the vaccine has been properly transported and stored at
all times and that it has not become contaminated. If vaccine has
been inappropriately exposed to excessive heat, cold, or light,
its potency may be reduced before the expiration date is reached.
The only way to determine if proper transport and storage conditions
have been maintained is to monitor vaccine and diluent temperatures
during every link in the cold chain and to safeguard HPV, MMR, MMRV,
rotavirus, varicella, and zoster vaccines from exposure to light.
The expiration date printed on each vial or box may also be invalidated
after the vial is opened or reconstituted (see Expiration of Different
Vaccine Products in this section for details).
Transferring
Vaccine or Diluent That Cannot Be Used Before Expiration
If vaccine or diluent is within 120 days of the
expiration date, determine whether or not the product can be used
within this time period given the volume of patients vaccinated
in your practice. If the product cannot be used within this time
frame, contact the vaccine supplier, which may be the vaccine manufacturer
or the state health department immunization program, for guidance.
You may be able to return the vaccine and diluent for credit or
you may be able to transfer the product to another facility where
it can be used before it expires. If the vaccine is publicly purchased,
you may be instructed to return it to the immunization program,
or transfer it to another provider. Your state immunization program
may recommend a window period different than 120 days for these
considerations.
Expiration
of Different Vaccine Products
Multidose premixed vaccine vials contain bacteriostatic
agents that prevent the growth of bacteria. These vaccines can be
used until the date of expiration printed on the vial unless they
become contaminated.
Single-dose vials are meant for one-time use only. Once the protective caps on single-dose vials have been unsealed, it may not be possible to determine if the rubber seals have been punctured. Therefore,
do not open single-dose vials until you are ready to use them. To
avoid needless waste of vaccine, always check the vial before removing
the cap to make sure you have the correct vaccine type, and remove
the cap only when you are ready to draw up and administer the vaccine.
Single-dose vials without their protective caps should be discarded
at the end of the clinic day.
|
|
Single dose vials
are meant for one-time use only.
Once unsealed, discard vial
at end of clinic day. |
Once lyophilized (freeze-dried) vaccines have been
reconstituted, they must be used within a specified time frame or
discarded. Consult the product insert for the most up-to-date information
about expiration times and dates following reconstitution. MMRV,
varicella, and zoster vaccines must be used within 30 minutes of
reconstitution and protected from light at all times. TriHIBit®
vaccine (DTaP/Hib) and single-dose vials of Menomune®
must be used within 30 minutes of reconstitution. MMR must be used
within 8 hours of reconstitution and protected from light at all
times. ActHIB® vaccine (Hib) must be used within
24 hours of reconstitution. Multidose vials of Menomune®
must be used within 35 days of reconstitution. Unused reconstituted
vaccines kept beyond these limits should not be
administered. The best way to avoid such waste is to reconstitute
and draw up vaccines immediately before administration (see Expiration
of Reconstituted Vaccine in the Vaccine Preparation and Disposal
section for details).
The vaccine coordinator should ensure that someone
rearranges the placement of vaccine and diluent supplies according
to the expiration dates on a weekly basis and each time a vaccine
shipment arrives. The vials and boxes with the earliest expiration
dates should be placed in front of other vials and boxes of the
same type with later expiration dates. This practice avoids waste
by ensuring that vaccines and diluents with the shortest expiration
dates are easily accessible and will be used first, thereby limiting
the amount of unused vaccine that has passed its expiration date.
Expired
vaccine and diluent should never be administered. |
Expired vaccine
and diluent should never be administered. Promptly remove
expired vaccine from the refrigerator or freezer to avoid
accidental use. Vaccine suppliers have different return policies
for outdated vaccine. Contact the vaccine manufacturer for
advice on returning privately purchased vaccine. Contact the state health department immunization program for
advice on returning publicly purchased vaccine for excise tax credit.
General
Recommendations
Inventory accounting is important for vaccine quality
management. Proper inventory management means knowing the following:
 |
what quantities of vaccines and
diluents have been received; |
 |
what quantities of vaccines and diluents have
been administered, wasted, or spoiled; |
 |
which vaccines and diluents are currently
in stock; |
 |
which vaccine and diluent vials should be
used first; |
 |
which vaccine and diluent vials are expired
and must not be administered; |
 |
how many vaccine and diluent vials are in
excess supply and may be returned for possible credit; and |
 |
which vaccines and diluents need to be ordered. |
Stock Records
Some state or local health department immunization
programs have developed stock records or other vaccine inventory
protocols and procedures for vaccine providers. Contact program
staff for information and follow their recommendations. If stock
records are not available from the state or local health department
immunization program, a Sample Stock Record can be found in the
Resources section of this toolkit. This Sample Stock Record shows
the components that you may include in your own stock record. A
blank version of the Sample Stock Record is also available in the
Resources section (see Stock Record).
Maintaining
complete and accurate stock records is a critical component
of inventory management. |
Maintaining complete and accurate stock records
is a critical component of inventory management. The balance
of doses remaining in stock as indicated on the stock records
should be updated weekly using a tally of doses administered,
wasted, spoiled, expired, or transferred that week. A stock record that is not accurate is of no value to the vaccine coordinator and can lead to over- or understocking of supplies and disruption to the immunization program.
|
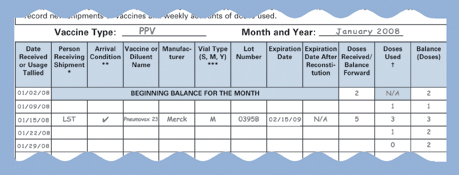
Sample Stock Record. |
Stock records may be kept in either computerized
or written formats, depending on the setting. Keep separate records
for each type of vaccine. For lyophilized (freeze-dried) vaccine
that requires reconstitution, record information for diluents on
a separate stock record. Quantities of these vaccines and diluents
must be equal at all times.
Each stock record should contain the following information:
 |
the date each vaccine and diluent
arrived at the facility; |
 |
the initials of the person who unpacked and
checked the vaccine and diluent upon arrival (this person should
also record the shipment on the stock record); |
 |
the condition of each vaccine and diluent
upon arrival (i.e., did the vaccine arrive in good condition
at the proper temperature or was there a reason to question
its integrity); |
 |
the name of each vaccine and diluent; |
 |
the manufacturer of each vaccine and diluent; |
 |
the type of container received (i.e., single-dose
vial, multidose vial, or manufacturer-filled syringe); |
 |
the lot number(s) (note there may be more
than one lot in a shipment— each lot should be recorded
on a separate line on the stock record); |
 |
the expiration date(s) for each lot (including
the new expiration dates/times for vaccines that have been reconstituted); |
 |
the number of doses received (or the balance
of doses carried forward); |
 |
the number of doses used (i.e., administered,
wasted, spoiled, expired, or transferred - if vaccine is transferred,
note the destination beside the number of doses); and |
 |
the balance remaining (in DOSES) after subtracting
the amount used (i.e., administered, wasted, spoiled, expired,
or transferred). |
If you receive multiple vials of the same vaccine
in the same type of container (i.e., single-dose vial, multidose
vial, or manufacturer-filled syringe) from the same lot with the
same expiration date, these doses may be recorded as one entry on
the stock record. Simply indicate the total number of doses of that
particular vaccine that were received (regardless of the number
of vials or syringes those doses came in). For example, if you receive
10 single-dose vials of the same vaccine meeting the above criteria,
these 10 vials can be recorded as a single entry, noting that 10
doses were received.
Tally Sheets
Some state or local health department immunization
programs have developed tally sheets or other vaccine inventory
protocols and procedures for vaccine providers. Contact program
staff for information and follow their recommendations. If tally
sheets are not available from the state or local health department
immunization program, a Sample Tally Sheet can be found in the Resources
section of this toolkit. This Sample Tally Sheet shows the components
that you may include in your own tally sheet. A blank version of
the Sample Tally Sheet is also available in the Resources section
(see Tally Sheet).
Tally sheets are used to record vaccine doses that were removed from the vaccine storage unit. |
Tally sheets are used to record vaccine doses that were removed from the vaccine storage unit. These include doses that were administered, wasted, spoiled, expired, or transferred. Each time a dose of vaccine is removed, it should be marked on a tally sheet that is placed on the outside of the storage unit door or in some other convenient location. Tick marks can be used to record doses that have been removed from the storage unit. Alternatively, the initials of the person removing the dose may be used.
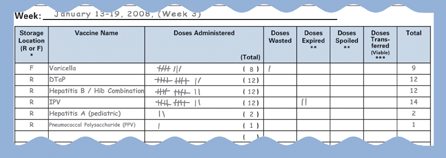
Sample Tally Sheet. |
These tally sheets can be used to keep stock records
updated. For example, place a tally sheet on the storage unit door
and record the doses removed from the unit during the week. At the
end of the week, the vaccine coordinator or a designated person
should add up the number of doses of each vaccine used and update
the stock records accordingly to determine the new stock balance
at the end of the week. The old tally sheet can then be removed
and replaced with a new tally sheet to be used for the following
week. Store used tally sheets in a file for future reference.
Recording
New Shipments
For details, see Storing and Documenting Vaccine
Shipments Upon Arrival in the Vaccine Shipments section.
Recording
Administered, Wasted, Spoiled, Expired, and Transferred Doses
Every dose of vaccine and diluent must be accounted
for. Contact state or local health department immunization program
staff for details about inventory accounting practices and follow
their recommendations. The following discussion provides general
guidelines only.
Record every dose removed from the vaccine storage
unit on the appropriate tally
sheet and stock record.
Record how many doses were administered, wasted, spoiled, expired,
or transferred. At the end of the week, use the tally sheet to update
the stock record and calculate the balance of the vaccine and diluent
remaining (i.e., the running balance of doses in stock).
While vaccines and diluents remain in storage,
expiration dates should be checked weekly and stock should be rotated
accordingly (see Expiration Dates
and Stock Rotation in this section).
Record each time vaccine or diluent doses expire. These records
will help you decide how much vaccine to order to minimize waste
in the future. Likewise, note each time doses cannot be used because
they have been exposed to inappropriate storage conditions or because
their vials have been damaged. Subtract these unusable doses from
the running balance on the stock record to calculate the new balance
of doses. Recording the number of doses that were expired, wasted,
or spoiled helps monitor vaccine waste. Contact the state health
department immunization program and the vaccine manufacturer for
instructions on how to dispose of these doses. They may have to
be discarded but sometimes unused vaccine may be returned for credit.
Some state health department immunization programs accept transfers vaccines with short expiration dates that will expire before they can be used. Occasionally, viable vaccines may also be transferred
to other facilities. Contact the state or local health department
immunization program for details if such a transfer is required.
For each transfer, record the details in the appropriate tally sheet
and stock record. Also, record the details of the vaccines and diluents
being transferred, a contact name, and a contact telephone number
on the delivery note or packing slip which accompanies the shipment.
This helps the receiver know exactly what items are being transferred.
If vaccine transfer is necessary, contact the state health department
immunization program and vaccine manufacturer for information on
the process and procedures.
Counting Stock
An actual count of the number of doses of vaccine
and diluent in stock is an important component of inventory management
and is the responsibility of the vaccine coordinator or designee.
Vaccine and diluent doses should be counted at least once a month
and before ordering vaccine. This will ensure there are enough supplies
to meet the needs of the practice and is useful for checking the
accuracy of the running balance of doses in the stock records.
When counting vaccine doses:
 |
Review the expiration dates of all stock, looking for vaccine with a short expiration date that must be used quickly and for expired vaccine that should not be administered. |
 |
If you have vaccine
that will expire within 120 days that cannot be administered
during this time period, contact the vaccine supplier, which
may be the vaccine manufacturer or the state health department
immunization program for further instructions. If the vaccine with a short expiration date is publicly purchased vaccine, in some cases it can
be moved to another clinic where it may be used before it expires.
Your state immunization program may recommend a window period
different than 120 days for these considerations. |
 |
Promptly remove expired vaccine and diluent from the refrigerator or freezer. Contact the vaccine supplier, which may be the vaccine manufacturer or the state health department immunization program, for specific policies regarding the disposition of expired vaccine. If the expired vaccine is publicly purchased, contact your state health
department immunization program for instructions on returning expired vaccine for excise tax credit. If expired vaccine cannot be returned, dispose of the vaccine appropriately (see Disposal of Vaccine and Diluent in the Vaccine Preparation and Disposal section for details). |
 |
If the count of vaccine doses is different from the running balance in the stock records, count the stock again and recalculate the running balance to find the error. |
 |
If a discrepancy remains, the stock record is in error and should be corrected. To do this, enter the correct balance from your count on a separate line in the stock record below the old balance. Write a note with your signature beside it to indicate that your count has confirmed the new balance. Use the new corrected balance for all future stock calculations. |
 |
At the end of every month, make a summary of the amount of each vaccine and diluent used during that month and the amount of stock still available at the end of that month. This information is useful for deciding how much vaccine to order and can be used to monitor the seasonality of vaccine use. |
 |
At the end of every year, total the amount of each vaccine and diluent received and the amount used. This information is useful for determining the annual vaccine needs of the practice. |
Vaccine
Stock Calculations and Vaccine Ordering |
In general, there are three main principles to
keep in mind when calculating the
amount of vaccine supplies needed and when placing vaccine orders:
1. |
Order and stock
enough vaccine to ensure that there is an adequate supply to
meet the needs of the patients. An adequate supply
for most practices would normally be enough vaccine to last
60 days, with a re-ordering threshold of 30 days. Your state
health department immunization program may recommend different
supply levels, depending on local use. |
2. |
Do not over order vaccines. This practice leads to vaccine waste if unused vaccine expires. It also results in unnecessarily large volumes of vaccine being stored, which increases the risk of losing a large quantity of vaccine should there be a storage and handling accident (e.g., mechanical failure of the vaccine storage unit). |
3. |
Place one large order for all the vaccines required for a specific period of time rather than multiple small orders for individual vaccines. This reduces the number of vaccine shipments your practice must handle, and also reduces the risk that you will run out of a particular vaccine. If you receive vaccine from the Vaccines for Children (VFC) Program, ordering all vaccines at one time helps the program process orders efficiently. |
Contact your state or local health department immunization
program for
further information about vaccine supply management and ordering.
Follow the
specific recommendations for your state regarding methods for calculating
vaccine supply needs, amounts of vaccine inventory to keep in stock,
frequency
of ordering, and methods of ordering vaccine. While vaccine orders
usually arrive within 1-2 weeks, delays can occur. Avoid
placing last minute or rush
orders so as to minimize the risk that you will run out of vaccine.
After ordering vaccine, alert office staff that an order has been
placed. The
primary vaccine coordinator or designated backup person should be
notified
immediately upon arrival of a vaccine shipment so that the vaccine
is stored
under appropriate conditions and the cold chain is maintained (see the section onVaccine Shipments). Vaccine shipments must also
be documented
in the appropriate stock record. |