
Oil and Gas Well Drilling and Servicing eTool
Home | Site Preparation | Drilling | Well Completion | Servicing | Plug and Abandon Well | General Safety and Health
Site Map | Glossary of Terms | Illustrated Glossary
Oil and Gas Home Illustrated Glossary
† This is an abridged version of the Dictionary of Petroleum Terms provided by Petex and the University of Texas Austin. © Petex 2001

Equipment used in drilling.
Drilling Rig Components*
Select a name from the list or a number on the graphic to see a definition and a more detailed photo of the object. A text version is also available.
- Crown Block and Water Table
- Catline Boom and Hoist Line
- Drilling Line
- Monkeyboard
- Traveling Block
- Top Drive
- Mast
- Drill Pipe
- Doghouse
- Blowout Preventer
- Water Tank
- Electric Cable Tray
- Engine Generator Sets
- Fuel Tanks
- Electric Control House
- Mud Pump
- Bulk Mud Components Storage
- Mud Pits
- Reserve Pits
- Mud Gas Separator
- Shale Shaker
- Choke Manifold
- Pipe Ramp
- Pipe Racks
- Accumulator
Additional rig components not illustrated at right.
Drilling Rig Components†
1. Crown Block and Water Table
An assembly of sheaves or pulleys mounted on beams at the top of the derrick. The drilling line is run over the sheaves down to the hoisting drum.†

2. Catline Boom and Hoist Line
A structural framework erected near the top of the derrick for lifting material.†

3. Drilling Line
A wire rope hoisting line, reeved on sheaves of the crown block and traveling block (in effect a block and tackle). Its primary purpose is to hoist or lower drill pipe or casing from or into a well. Also, a wire rope used to support the drilling tools.†

#4. Monkeyboard
The derrickman's working platform. Double board, tribble board, fourable board; a monkey board located at a height in the derrick or mast equal to two, three, or four lengths of pipe respectively.†

#5. Traveling Block
An arrangement of pulleys or sheaves through which drilling cable is reeved, which moves up or down in the derrick or mast.†

#6. Top Drive
The top drive rotates the drill string end bit without the use of a kelly and rotary table. The top drive is operated from a control console on the rig floor.†

#7. Mast
A portable derrick capable of being erected as a unit, as distinguished from a standard derrick, which cannot be raised to a working position as a unit.†

#8. Drill Pipe
The heavy seamless tubing used to rotate the bit and circulate the drilling fluid. Joints of pipe 30 feet long are coupled together with tool joints.†

#9. Doghouse
A small enclosure on the rig floor used as an office for the driller or as a storehouse for small objects. Also, any small building used as an office or for storage.†
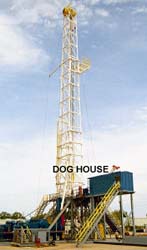
#10. Blowout Preventer
One or more valves installed at the wellhead to prevent the escape of pressure either in the annular space between the casing and the drill pipe or in open hole (for example, hole with no drill pipe) during drilling or completion operations. See annular blowout preventer and ram blowout preventer.†s

#11. Water Tank
Is used to store water that is used for mud mixing, cementing, and rig cleaning.†
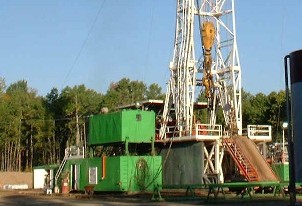
#12. Electric Cable Tray
Supports the heavy electrical cables that feed the power from the control panel to the rig motors.†

#13. Engine Generator Sets
A diesel, Liquefied Petroleum Gas (LPG), natural gas, or gasoline engine, along with a mechanical transmission and generator for producing power for the drilling rig. Newer rigs use electric generators to power electric motors on the other parts of the rig.†

#14. Fuel Tanks
Fuel storage tanks for the power generating system.†

#15. Electric Control House
On diesel electric rigs, powerful diesel engines drive large electric generators. The generators produce electricity that flows through cables to electric switches and control equipment enclosed in a control cabinet or panel. Electricity is fed to electric motors via the panel.†

#16. Mud Pump
A large reciprocating pump used to circulate the mud (drilling fluid) on a drilling rig.†

#17. Bulk Mud Components Storage
Hopper type tanks for storage of drilling fluid components.†

#18. Mud Pits
A series of open tanks, usually made of steel plates, through which the drilling mud is cycled to allow sand and sediments to settle out. Additives are mixed with the mud in the pit, and the fluid is temporarily stored there before being pumped back into the well. Mud pit compartments are also called shaker pits, settling pits, and suction pits, depending on their main purpose.†

#19. Reserve Pits
A mud pit in which a supply of drilling fluid has been stored. Also, a waste pit, usually an excavated, earthen-walled pit. It may be lined with plastic to prevent soil contamination.†

#20. Mud Gas Separator
A device that removes gas from the mud coming out of a well when a kick is being circulated out.†

#21. Shale Shaker
A series of trays with sieves or screens that vibrate to remove cuttings from circulating fluid in rotary drilling operations. The size of the openings in the sieve is selected to match the size of the solids in the drilling fluid and the anticipated size of cuttings. Also called a shaker.†

#22. Choke Manifold
The arrangement of piping and special valves, called chokes, through which drilling mud is circulated when the blowout preventers are closed to control the pressures encountered during a kick.†

#23. Pipe Ramp
An angled ramp for dragging drill pipe up to the drilling platform or bringing pipe down off the drill platform.†

#24. Pipe Racks
A horizontal support for tubular goods.†
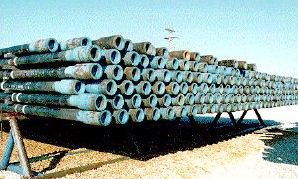
#25. Accumulator
The storage device for nitrogen pressurized hydraulic fluid, which is used in operating the blowout preventers.†


#26. Annulus
The space around a pipe in a well bore, the outer wall of which may be the wall of either the bore hole or the casing; sometimes termed the annular space.†

#27. Brake Bands
The braking device on the drawworks to stop a load being lifted.†

#28. Casing Head
A heavy, flanged steel fitting connected to the first string of casing. It provides a housing for slips and packing assemblies, allows suspension of intermediate and production strings of casing, and supplies the means for the annulus to be sealed off. Also called a spool.†

#29. Cathead
A spool-shaped attachment on a winch around which rope for hoisting and pulling is wound.†

#30. Catwalk
The ramp at the side of the drilling rig where pipe is laid to be lifted to the derrick floor by the catline or by an air hoist.†

#31. Cellar
A pit in the ground to provide additional height between the rig floor and the well head to accommodate the installation of blowout preventers, ratholes, mouseholes, and so forth. It also collects drainage water and other fluids for disposal.†

#32. Conductor Pipe
The largest diameter casing and the topmost length of casing. It is relatively short and encases the topmost string of casing.†

#33. Degasser
The equipment used to remove unwanted gas from a liquid, especially from drilling fluid.†
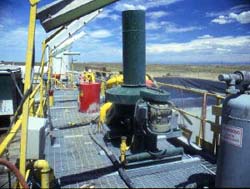
#34. Desander
A centrifugal device for removing sand from drilling fluid to prevent abrasion of the pumps. It may be operated mechanically or by a fast-moving stream of fluid inside a special cone-shaped vessel, in which case it is sometimes called a hydrocyclone.†

#35. Desilter
A centrifugal device, similar to a desander, used to remove very fine particles, or silt, from drilling fluid. This keeps the amount of solids in the fluid to the lowest possible level.†

#36. Drawworks
The hoisting mechanism on a drilling rig. It is essentially a large winch that spools off or takes in the drilling line and thus raises or lowers the drill stem and bit.†

#37. Drill Bit
The cutting or boring element used in drilling oil and gas wells. Most bits used in rotary drilling are roller-cone bits. The bit consists of the cutting elements and the circulating element. The circulating element permits the passage of drilling fluid and uses the hydraulic force of the fluid stream to improve drilling rates.†

#38. Drill Collar
A heavy, thick-walled tube, usually steel, used between the drill pipe and the bit in the drill stem. It is used to put weight on the bit so that the bit can drill.†

#39. Drillers Console
The control panel, located on the platform, where the driller controls drilling operations.†

#40. Elevators
A set of clamps that grips a stand, or column, of casing, tubing, drill pipe, or sucker rods, so the stand can be raised or lowered into the hole.†

#41. Hoisting Line
A wire rope used in hoisting operations. Must conform to the API standards for its intended uses.†

#42. Hook
A large, hook-shaped device from which the elevator bails or the swivel is suspended. It is designed to carry maximum loads ranging from 100 to 650 tons and turns on bearings in its supporting housing.†

#43. Kelly
The heavy square or hexagonal steel member suspended from the swivel through the rotary table. It is connected to the topmost joint of drill pipe to turn the drill stem as the rotary table turns.†


#44. Kelly Bushing
A device fitted to the rotary table through which the kelly passes. It is the means by which the torque of the rotary table is transmitted to the kelly and to the drill stem. Also called the drive bushing.†
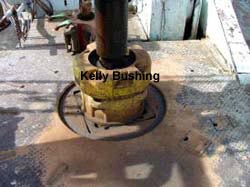
#45. Kelly Spinner
A device for spinning the drill pipe. Replaces the spinning chain.†

#46. Mousehole
Shallow bores under the rig floor, usually lined with pipe, in which joints of drill pipe are temporarily suspended for later connection to the drill string.†

#47. Mud Return Line
A trough or pipe, placed between the surface connections at the well bore and the shale shaker. Drilling mud flows through it upon its return to the surface from the hole.†

#48. Ram Blowout Preventer
A blowout preventer that uses rams to seal off pressure on a hole that is with or without pipe. It is also called a ram preventer. Ram-type preventers have interchangeable ram blocks to accommodate different O.D. drill pipe, casing, or tubing.†

#49. Rathole
A hole in the rig floor 30 to 35 feet deep, lined with casing that projects above the floor. The kelly is placed in the rathole when hoisting operations are in progress.†

#50. Rotary Hose
The hose on a rotary drilling rig that conducts the drilling fluid from the mud pump and standpipe to the swivel and kelly; also called the mud hose or the kelly hose.†

#51. Rotary Table
The principal component of a rotary, or rotary machine, used to turn the drill stem and support the drilling assembly. It has a beveled gear arrangement to create the rotational motion and an opening into which bushings are fitted to drive and support the drilling assembly.
Note the pipe spinner (in red) on the side of the swivel.†

#52. Slips
Wedge-shaped pieces of metal with teeth or other gripping elements that are used to prevent pipe from slipping down into the hole or to hold pipe in place. Rotary slips fit around the drill pipe and wedge against the master bushing to support the pipe. Power slips are pneumatically or hydraulically actuated devices that allow the crew to dispense with the manual handling of slips when making a connection. Packers and other down hole equipment are secured in position by slips that engage the pipe by action directed at the surface.†

#53. Spinning Chain
A relatively short length of chain attached to the tong pull chain on the manual tongs used to make up drill pipe. The spinning chain is attached to the pull chain so that a crew member can wrap the spinning chain several times around the tool joint box of a joint of drill pipe suspended in the rotary table. After crew members stab the pin of another tool joint into the box end, one of them then grasps the end of the spinning chain and with a rapid upward motion of the wrist "throws the spinning chain"-that is, causes it to unwrap from the box and coil upward onto the body of the joint stabbed into the box. The driller then actuates the makeup cathead to pull the chain off of the pipe body, which causes the pipe to spin and thus the pin threads to spin into the box.†

#54. Stairways
Stairs leading from one level to another. Protected with handrails.†

#55. Standpipe
A vertical pipe rising along the side of the derrick or mast. It joins the discharge line leading from the mud pump to the rotary hose and through which mud is pumped going into the hole.†

#56. Surface Casing
Usually the first casing to be run in a well. This is done after spudding-in so a blowout preventer can be installed before drilling is started.†

#57. Substructure
The foundation on which the derrick or mast and usually the drawworks sit; contains space for storage and well control equipment.†
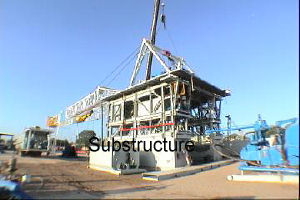
#58. Swivel
A rotary tool that is hung from the rotary hook and traveling block to suspend and permit free rotation of the drill stem. It also provides a connection for the rotary hose and a passageway for the flow of drilling fluid into the drill stem.†

#59. Tongs
The large wrenches used for turning when making up or breaking out drill pipe, casing, tubing, or other pipe; variously called casing tongs, rotary tongs, and so forth according to the specific use. Power tongs are pneumatically or hydraulically operated tools that spin the pipe up and, in some instances, apply the final makeup torque.†

#60. Walkways
An area cleared for moving through by personnel and protected with a handrail.†

#61. Weight Indicator
A device for measuring the weight of the drill string. Monthly calibration to calculated drill string weight is required by API.†

Annular Blowout Preventer
A large valve, usually installed above the ram preventers, that forms a seal in the annular space between the pipe and well bore. If no pipe is present, it forms a seal on the well bore itself. See blowout preventer.†
