2003 Progress Report: Plasma Polymerization: A Novel, Environmentally-Compatible Process for Surface Engineering of Metals
EPA Grant Number: R829579Title: Plasma Polymerization: A Novel, Environmentally-Compatible Process for Surface Engineering of Metals
Investigators: Boerio, F. James , Bengu, B. , Gupta, M.
Current Investigators: Boerio, F. James , Bengu, B. , Gupta, M.
Institution: University of Cincinnati
EPA Project Officer: Richards, April
Project Period: March 11, 2002 through March 10, 2006
Project Period Covered by this Report: March 11, 2003 through March 10, 2004
Project Amount: $300,000
RFA: Technology for a Sustainable Environment (2001)
Research Category: Pollution Prevention/Sustainable Development
Description:
Objective:The objective of this research project is to develop plasma polymerization as a novel, environmentally compatible process for surface engineering of aluminum prior to structural adhesive bonding or finishing operations. The new surface engineering process that results from this research will enable chromates and liquid wastes from surface engineering of aluminum by conventional processes to be eliminated from the Nation’s waste stream at the source. A key step in achieving the objectives of this research project involves relating the species present in the plasma to processing variables that are used in depositing plasma-polymerized films on aluminum, to the molecular structure of the films, and to the properties of the films as primers for structural adhesive bonding and for inhibiting corrosion of aluminum. This will improve process control and facilitate eventual implementation of the new processes.
Progress Summary:Plasma polymerization involves the formation of active species such as ions and free radicals in a low-pressure gas or plasma of a “monomer” by collisions between free electrons and monomer molecules when an electric field is applied to the gas. The active species react with themselves or with monomer molecules to form polymer films on the surfaces of solids that are exposed to the plasma. Plasma polymerization is an extremely attractive process for surface engineering of metals. It is efficient because it enables materials synthesis and processing to be combined into one step. High performance films can be prepared from a variety of monomers, including compounds that do not polymerize by conventional techniques. Monomers that are not harmful to the environment can be selected and, because plasma polymerization is a gas phase process, there are no liquid wastes.
In this research project, performance characteristics of the films such as the corrosion protection they impart to metal substrates, the interfacial fracture energy of films deposited on aluminum substrates, and the properties of the films as primers for structural adhesive bonding are determined using electrochemical impedance spectroscopy, fracture mechanics tests, and industrial test methods. The effect of important processing variables such as substrate temperature during film deposition, discharge power, monomer, flow rate, pressure, and substrate surface chemistry on the deposition rate, molecular structure, and morphology of the films is determined using surface analysis techniques such as x-ray photoelectron spectroscopy (XPS), Fourier-transform infrared spectroscopy (FTIR), variable-angle spectroscopic ellipsometry, scanning electron microscopy (SEM), and atomic force microscopy. Species in the plasma are being identified as a function of processing variables using optical emission spectroscopy. Gaseous effluents from the reactor are determined by residual gas analysis, and particulates are identified by FTIR.
This report describes our current results in three areas. The first area concerned the performance of plasma-polymerized silica-like films as primers for structural adhesive bonding of aluminum, and the second area concerned the effect of hydroxyl content in plasma films on adhesion. The third area concerned the difference in adhesion of epoxies cured with different curing agents. Also, the effect of metal substrates on the molecular structure formed within the interface of epoxy adhesive cured with dicyandiamide (DDA) was investigated. For this purpose, diglycidyl ether of bisphenol-A (DGEBA) was used as a model adhesive compound.
Experimental
Plasma-Polymerized Silica-Like Primers for Structural Adhesive Bonding of Aluminum. Aluminum alloy 6022 sheets having a thickness of 2.0 mm were obtained from Alcoa. Two different pretreatment processes were used to prepare the aluminum substrates for deposition of plasma-polymerized films. The first pretreatment process involved etching in a 20 percent by volume solution of ALDEOX 171 (A Brite Company) in deionized water for 10 minutes. ALDEOX 171 is a mixture of nitric acid, sulfuric acid, fluoroboric acid, and ferric nitrate, but is mostly ferric nitrate and ferric acid. Etched substrates were rinsed with hot water, deionized water, and acetone and then dried in a stream of nitrogen. In the second pretreatment process, aluminum substrates were cleaned with acetone and etched for 10 minutes in an O2 plasma using a capacitively coupled, RF-powered (13.6 MHz) reactor. The upper electrode was powered and located 3.0 cm above the lower electrode that was grounded to the case of the reactor. During plasma etching, the pressure was 0.1 torr, power was 150 W, and flow rate was 40 sccm. Substrates were placed on the lower electrode.
Plasma-polymerized silica-like films were deposited onto pretreated aluminum substrates using the same reactor. Hexamethyldisiloxane (HMDSO, Aldrich) was used as the monomer, and oxygen was used as a coreactant. Films containing relatively low concentrations of hydroxyl groups were deposited using a pressure of 0.15 torr, power of 150 W, oxygen flow rate of 39.2 sccm, HMDSO flow rate of 0.8 sccm, and time of 35 minutes. Films with relatively high-hydroxyl content were deposited for 7 minutes using pressure of 0.50 torr, power of 150 W, oxygen flow rate of 95.0 sccm, and HMDSO flow rate of 5.0 sccm (see Table 1). Substrates were again placed on the lower electrode.
In some cases, films simultaneously were deposited on ferrotype substrates
placed next to the aluminum substrates so that ellipsometry and infrared spectroscopy
of the films on ferroplate could be carried out. Ferrotype is steel sheet plated
with chromium; it is available commercially through outlets for photographic
supplies. Its surface is smooth and highly reflective, making it a nearly ideal
substrate for ellipsometry and reflection-absorption infrared (RAIR) spectroscopy.
Ferrotype substrates were prepared for plasma polymerization by rinsing in
acetone and then being passed through the flame of a Bunsen burner several
times.
Aluminum/epoxy lap joints were prepared according to American Society for
Testing and Materials standard D1002. Substrates (102.4 mm x 25.4 mm x 2
mm) were cut from a sheet of aluminum and pretreated using one of the processes
described above. One set of eight substrates then was coated with plasma-polymerized
silica-like films having low-hydroxyl content, and another set was coated
with films having high-hydroxyl content. One set of the substrates was coated
with a plasma-polymerized, low-hydroxyl, silica-like film and then with a
thin film of -glycidoxypropyltriethoxysilane (
-GPS, Aldrich). Similarly,
one set of the substrates was coated with a plasma-polymerized, high-hydroxyl,
silica-like film and then with a thin film of
-GPS. The final set of the
substrates was used without additional pretreatment. A total of 10 different
substrate pretreatment processes thus were investigated.
Thin films of -GPS were applied to selected substrates from 1 percent solutions
in deionized water.
-GPS solutions were stirred for 1 hour with a magnetic
stirrer, and an acid brush then was used to apply the solution uniformly to
the substrate surface. The solution was left standing on the substrates for
10 minutes and then was blown off using a strong stream of nitrogen. Silane
films thus obtained were dried in an oven for 1 hour at 93°C.
In a few cases, plasma-polymerized silica-like films were deposited onto pretreated aluminum substrates at a temperature of 100°C. Substrates were placed on an aluminum plate on the lower electrode of the reactor; the plate was heated using a cartridge heater. A few substrates also were prepared where the silica-like primer films were etched for 5 minutes in an O2 plasma using a pressure of 0.1 torr, power of 150 W, and total flow rate of 40 sccm (see Table 1).
Two different adhesive systems were used to prepare lap joints. One was a two-part adhesive formulated using 100 parts by weight of an epoxy resin (Epon 828, Shell Chemical Co.) and 150 parts by weight of a polyamide/amine curing agent (Epicure 3140, Shell Chemical Co.). The second adhesive was a commercial one-part adhesive (Araldite AV-3131, Ciba Specialty Chemicals) consisting of an epoxy resin and the curing agent DDA as well as other constituents such as accelerators and fillers. The one-part and two-part adhesives were cured overnight at room temperature and then post cured in an oven at 175°C for 30 minutes (one part) and at 100°C for 1 hour (two part).
After curing, some lap joints were cooled to room temperature and then pulled to failure on an Instron at a speed of 0.2 in/min to determine their initial breaking strength. Other lap joints were immersed in deionized water at 60°C for 2 weeks and then pulled to failure on the Instron to determine their residual strength and thus their short-term durability.
Long-term durability of lap joints was determined by immersing joints in deionized water at 60°C, removing three joints every week for 5 weeks, and pulling the joints on an Instron to determine their residual strength. Stressed durability of lap joints was carried out at Alcoa. Lap joints were stressed to 6.9 MPa and exposed to a cyclically varying corrosive environment. Each cycle lasted 24 hours and consisted of immersion in a 5 percent aqueous solution of NaCl for 15 minutes, drying at room temperature for 1 hour and 45 minutes, and exposure to 50°C and 90 percent relative humidity for 22 hours. On weekends, joints were maintained at 50°C and 90 percent relative humidity. The stressed durability was measured as the number of cycles needed to produce complete failure of the joints.
XPS was used to examine as-prepared silica-like films.
XPS spectra were obtained using a Perkin-Elmer Model 5300 XPS spectrometer
and Mg K x-rays (h
= 1253.6
eV). Survey spectra were obtained at a pass energy of 89.45 eV; high-resolution
spectra were obtained at pass energy of 35.75 eV. Most spectra were obtained
at a take-off angle of 45°; however, take-off angles of 15° and 75° were
used in a few cases. XPS also was used to conduct failure analysis of lap joints
after durability testing.
RAIR spectroscopy was used to characterize as-deposited, plasma-polymerized films on ferroplate substrates and pretreated aluminum substrates. RAIR spectra were obtained using a Nicolet Magna 760 FTIR spectrometer and a Nicolet FTS-85 external reflection accessory that provided one reflection at an angle of incidence of 85°. Each spectrum was collected by averaging 256 scans of the sample at a resolution of 4 cm-1. The spectrum of a film was obtained by subtracting the spectrum of an uncoated substrate from the spectrum of a film-covered substrate.
A Hiatachi S-4000 SEM was used to investigate the failure surfaces of some lap joints after durability tests. Charging occurred because some specimens were nonconducting. In those cases, the specimens were sputter coated with a thin layer of gold.
RAIR spectroscopy also was used to determine the effect of substrates on the curing of a model adhesive consisting of DGEBA and DDA in a mole ratio of 7:1. Aluminum and ferrotype substrates (25.4 mm.x 25.4 mm) were used in these investigations. The aluminum substrates were ground on 800 and 1,200 grit silicon carbide paper and then polished to a mirror finish using aqueous slurries of 2 µm MgO particles. After polishing, the aluminum substrates were rinsed with deionized water and dried in a stream of nitrogen. Ferrotype substrates were prepared as described earlier by rinsing in acetone and then being passed through the flame of a Bunsen burner.
Thin films of the model adhesive were spin coated onto aluminum and ferroplate substrates from 5 percent solutions in N,N-dimethylformamide (DMF). These thin films were cured in an oven at 150°C under nitrogen for different times. After curing, the substrates were rinsed in DMF for 30 minutes to remove any compounds that were not tenaciously bound to the substrates and then blown dry with nitrogen. Bulk samples of the model adhesive were prepared by mixing DGEBA and DDA in a mole ratio of 7:1 and curing the mixture overnight at 150°C.
Results and Discussion
Structure of Plasma-Polymerized Films Formed at Room Temperature. The RAIR spectra of low-hydroxyl and high-hydroxyl plasma-polymerized silica-like films that were deposited onto ferroplate substrates in the RF reactor using HMDSO as the monomer and oxygen as coreactant are shown in Figure 1. The spectrum of the low-hydroxyl film was dominated by a strong band near 1,240 cm-1 that was assigned to the longitudinal optical (LO) phonon typical of a silica-like structure. Weak bands near 825 and 497 cm-1 also were attributed to LO modes of the silica-like structure. A very weak band characteristic of the OH stretching mode of isolated silanol groups in which the hydrogen atoms were hydrogen bonded to oxygen atoms in Si-O-Si groups was observed near 3,647 cm-1. The band near 938 cm-1 was assigned to the Si-O stretching mode of the isolated silanol groups. No bands that could be associated with the methyl groups of HMDSO were observed, indicating that most methyl groups were removed from the monomer during plasma polymerization.
Parameters |
|||||||
Process | Oxygen % |
Argon % |
HMDSO % |
Total Flow sccm |
Power Watts |
Pressure Torr |
Time Minutes |
Oxygen Etching | 100 |
- |
- |
40 |
150 |
0.10 |
10 |
Low-Hydroxyl Silica-Like Film | 98 |
- |
2 |
40 |
150 |
0.15 |
35 |
High-Hydroxyl Silica-Like Film | 95 |
- |
5 |
100 |
150 |
0.50 |
7 |
Infrared spectra of the high-hydroxyl films were similar except that there were two bands characteristic of OH stretching modes in hydrogen-bonded silanol groups (see Figure 1). One of these bands was near 3,647 cm-1 and was similar to the band observed for the low-hydroxyl films; the other band was near 3,345 cm-1 and was related to adjacent silanol groups in which the hydrogen atom of one was hydrogen bonded to the oxygen atom of the other. The band near 3,345 cm-1 was broad because of the wide distribution of hydrogen bonding environments of the silanol groups. A band related to the Si-O stretching mode of silanol groups was observed near 912 cm-1; this band was much stronger in intensity for the high-hydroxyl films than for the low-hydroxyl films.
XPS survey spectra of the plasma-polymerized high-hydroxyl and low-hydroxyl silica-like films deposited onto ferroplate substrates at room temperature are shown in Figure 2. These spectra were virtually identical and mostly consisted of peaks near 104 and 154 eV that were attributed to silicon, a peak near 532 eV that was attributed to oxygen, and a weak peak near 285 eV that was characteristic of carbon.
XPS spectra of the same films were obtained using different electron take-off angles. Small take-off angles result in XPS spectra that are more sensitive to atoms on the surface of the films, and larger angles make the spectra more sensitive to atoms that are somewhat below the surface. Thus, obtaining XPS spectra at different take-off angles provided information on the way in which the composition of the films changed as a function of distance from the surface and into the films. Reference to Table 2 shows that the carbon concentration of the low-hydroxyl films decreased from 17.7 percent to 6.8 percent when the take-off angle was increased from 15° to 75°, indicating that much of the carbon was on the surface of the films and was probably related to adsorbed contaminants from the atmosphere. Similar results were obtained for the high-hydroxyl films. In that case, the carbon concentration decreased from 15.3 percent to 4.9 percent when the take-off angle was increased from 15° to 75°.
Atomic concentrations obtained from the XPS spectra of the films at a take-off angle of 75° showed that the O/Si ratio was 2.56 for the low-hydroxyl films and 2.62 for high-hydroxyl films (see Table 2). Because the O/Si ratio is 2.0 for pure silica, it was concluded that both types of films deposited at room temperature had considerable numbers of nonbridging oxygen atoms within their silica-like structures that were associated with hydroxyl groups. The number of nonbridging oxygen atoms, however, was somewhat less for the low-hydroxyl films.
The plasma-polymerized silica-like films deposited at room temperature were sputtered with argon ions, and XPS spectra were obtained as a function of sputtering time. Sputtering in this way provided profiles showing the concentrations of carbon, oxygen, and silicon as a function of distance from the surface and into the films. As shown in Table 3, the silicon and oxygen concentrations increased and the carbon concentration decreased as the films were sputtered. After sputtering for 60 minutes, the O/Si ratio decreased from 2.6 to 2.3 for low-hydroxyl films. The O/Si ratio, however, remained approximately equal to 2.6 for high-hydroxyl films. These results indicated that the number of nonbridging oxygen atoms was high throughout the high-hydroxyl films. The number of nonbridging oxygen atoms also was high at the surface of the low-hydroxyl films, but it decreased significantly below the surface of the films.
High-resolution Si(2p) XPS spectra of plasma-polymerized films were curve fit to identify the chemical states of silicon in the films. Figure 3 shows the high-resolution Si(2p) spectra obtained for the low-hydroxyl and high-hydroxyl plasma-polymerized silica-like films. Both spectra were fitted with peaks at 103.4 and 102.8 eV that were characteristic of silicon in the fully oxidized state (Si4), as in crystalline quartz or SiO2, and of a suboxide of silicon (Si3+). There were more silicon atoms in the Si3+ oxidation state for high-hydroxyl films, however, than for low-hydroxyl films. This was consistent with the relatively high intensity of the bands resulting from hydroxyl groups in the infrared spectra of the high-hydroxyl films.

Figure 1. RAIR Spectra of (A) Low-Hydroxyl and (B) High-Hydroxyl Plasma-Polymerized Silica-Like Films Deposited on Ferroplate Substrates in the RF Reactor at Room Temperature Using HMDSO as Monomer and Oxygen as a Carrier Gas

Figure 2. XPS Survey Spectra of (A) Low-Hydroxyl and (B) High-Hydroxyl Plasma-Polymerized Silica-Like Films Deposited on Ferroplate Substrates in the RF Reactor at Room Temperature Using HMDSO as Monomer and Oxygen as a Carrier Gas
Table 2. Atomic Concentrations of Plasma-Polymerized HMDSO Films Deposited at Room Temperature Onto Aluminum Substrates That Were Etched in an O2 Plasma and Coated With Silica-Like Films. The atomic concentrations were obtained from XPS spectra acquired at different electron take-off angles.
Plasma-Polymerized Primer Films | Angle |
C% |
O% |
Si% |
O/Si |
15° |
17.7 |
59.6 |
22.7 |
2.63 |
|
Low-Hydroxyl Silica-Like Film | 45° |
8.7 |
66.3 |
25.0 |
2.65 |
75° |
6.8 |
67.0 |
26.2 |
2.56 |
|
15° |
15.3 |
61.7 |
23.0 |
2.68 |
|
High-Hydroxyl Silica-Like Film | 45° |
6.4 |
67.7 |
25.9 |
2.61 |
75° |
4.9 |
68.8 |
26.3 |
2.62 |
Table 3. Atomic Concentrations After Sputtering Low-Hydroxyl and High-Hydroxyl Plasma-Polymerized Silica-Like Films Deposited Onto Aluminum Substrates That Were Etched in an Oxygen Plasma. The atomic concentrations were determined from XPS spectra acquired at an electron take-off angle of 45°.
Plasma-Polymerized Primer Films | Sputtering Time Minutes |
C% |
O% |
Si% |
O/Si |
0 |
8.7 |
66.3 |
25.0 |
2.65 |
|
Low-Hydroxyl Silica-Like Film | 30 |
2.4 |
67.8 |
29.8 |
2.28 |
60 |
2.2 |
68.0 |
29.8 |
2.28 |
|
0 |
6.4 |
67.7 |
25.9 |
2.61 |
|
High-Hydroxyl Silica-Like Film | 30 |
3.9 |
69.5 |
26.6 |
2.61 |
60 |
3.7 |
69.3 |
27.0 |
2.57 |

Figure 3. High-Resolution Si(2p) XPS Spectrum Obtained at a Take-Off Angle of 45° on an Aluminum Substrate That Was Etched in an O2 Plasma and Then Primed With (A) Low-Hydroxyl and (B) High-Hydroxyl Plasma-Polymerized Silica-Like Films
Structure of Plasma-Polymerized Films Deposited at 100°C. The effect of temperature on the structure of plasma-polymerized silica-like films was determined by preparing films on ferroplate substrates at 100°C using the same reaction parameters as were used to deposit low-hydroxyl and high-hydroxyl films at room temperature (see Table 1). The RAIR spectra of the films deposited at 100°C were quite similar (see Figure 4), although they were deposited using different reaction parameters and were characterized by a strong band near 1,240 cm-1 and by weak bands near 820 and 495 cm-1 that were related to LO phonons of a silica-like structure. Neither film showed significant absorption bands that were characteristic of hydroxyl groups, although a weak band was observed near 3,647 cm-1 in the spectrum of the film that was made using reactor parameters that lead to low-hydroxyl films at room temperature.
XPS survey spectra of films deposited at 100°C using the reaction parameters used to deposit high-hydroxyl and low-hydroxyl films at room temperature are shown in Figure 5. These spectra were virtually identical to those obtained for the high-hydroxyl and low-hydroxyl films at room temperature.
The atomic concentrations that were determined from the XPS spectra acquired at 15°, 45°, and 75° take-off angles from films deposited at 100°C using the same reaction parameters as were used to deposit low-hydroxyl and high-hydroxyl films at room temperature (see Table 1) are summarized in Table 4. Comparing the results shown in Table 4 with those shown in Table 2 indicates that films deposited at the higher temperature had less carbon and more oxygen and silicon than films deposited at room temperature. Because XPS is more sensitive to elements on the surface of the films at a take-off angle of 15° and more sensitive to the elements in the bulk of the films at a take-off angle of 75°, it was concluded that much of the carbon was on the surface of the films, perhaps from adsorption of carbonaceous contaminants during exposure of the films to the laboratory atmosphere. Moreover, films deposited at 100°C using the "low-hydroxyl" parameters had a significantly lower O/Si ratio (2.33 at 75° take-off angle) than films deposited at room temperature (2.56 at 75° take-off angle) and thus had significantly fewer nonbridging oxygen atoms.
Mechanical Testing of Lap Joints Prepared From Aluminum Substrates
Initial strength of joints with silica-like primer films. Lap joints prepared
from aluminum adherends that were pretreated in various ways and then bonded
using the two-part adhesive were tested using an Instron to determine their
initial strength (see Figure 6). Joints prepared from aluminum substrates that
were etched in an O2 plasma had an average initial strength of 22.7 MPa. The
initial strengths of joints prepared from aluminum substrates that were etched
in an O2 plasma and coated with low-hydroxyl or high-hydroxyl films were 26.0
and 16.1 MPa, respectively. Joints prepared from aluminum substrates that were
etched in an O2 plasma, primed with a low-hydroxyl film, and then coated with
a thin film of -GPS silane had a strength of 25.5 MPa, whereas joints prepared
from substrates that were pretreated similarly, but with high-hydroxyl primer
films, had a strength of 18.6 MPa.
Joints prepared from aluminum substrates that were etched in the acid had
initial strengths of 20.0 MPa (see Figure 6). By comparison, joints prepared
from acid-etched aluminum substrates that were coated with low-hydroxyl or
high-hydroxyl films had strengths of 19.6 and 16.7 MPa, respectively. Joints
prepared from aluminum substrates that were etched in the acid, primed with
either a low-hydroxyl or high-hydroxyl film, and coated with a thin film of
-GPS silane had strengths of 22.0 MPa.

Figure 4. RAIR Spectra of Plasma-Polymerized Silica-Like Films Deposited on Ferrotype Substrates at 100°C. The films were deposited using the same reaction parameters as used to deposit (A) low-hydroxyl and (B) high-hydroxyl films at room temperature.

Figure 5. XPS Survey Spectra of the (A) Low-Hydroxyl and (B) High-Hydroxyl Plasma-Polymerized Silicia-Like Films Deposited on Ferrotype Substrate at 100°C
Table 4. Atomic Concentrations of Low-Hydroxyl and High-Hydroxyl Plasma-Polymerized Silica-Like Films Deposited on Aluminum Substrate at 100°C. The atomic concentrations were determined from XPS spectra acquired at different take-off angles.
Plasma-Polymerized Primer Films | Take-Off Angle |
C% |
O% |
Si% |
O/Si |
15° |
6.8 |
66.6 |
26.8 |
2.48 |
|
Low-Hydroxyl Silica-Like Film at 100°C | 45° |
4.0 |
67.7 |
28.3 |
2.39 |
75° |
3.0 |
67.9 |
29.1 |
2.33 |
|
15° |
10.7 |
66.7 |
22.6 |
2.95 |
|
High-Hydroxyl Silica-Like Film at 100°C | 45° |
4.2 |
69.8 |
26.0 |
2.69 |
75° |
2.7 |
70.2 |
27.1 |
2.59 |
These results showed that applying the silane to the plasma-polymerized primer films before bonding generally resulted in an increase in initial strength of joints prepared using the two-part adhesive. The reason for this was relatively poor adhesion between the two-part adhesive and the silica-like films. Joints prepared from substrates that were coated with plasma-polymerized primers and bonded with the two-part adhesive tended to fail near the adhesive/plasma polymer interface; application of the silane to the surface of the primer films eliminated these interfacial failures (see below).
Joints prepared using the one-part adhesive generally failed at stress levels that were somewhat lower than those obtained when using the two-part adhesive (see Figure 7). In fact, the initial strengths of all joints prepared using the one-part adhesive were between 15 and 20 MPa and did not depend much on the substrate pretreatment before bonding. The reason for this was that joints prepared using the one-part adhesive always failed cohesively within the adhesive. Moreover, because none of the joints prepared using the one-part adhesive failed near the primer/adhesive interface, the silane was not expected to have a significant effect.

Figure 6. Initial Strength of Lap Joints Prepared Using the Two-Part Adhesive and Aluminum Substrates That Were Pretreated by (A) Oxygen Plasma Etching and (B) Etching in 20 Percent by Volume Solution of ALDEOX 171
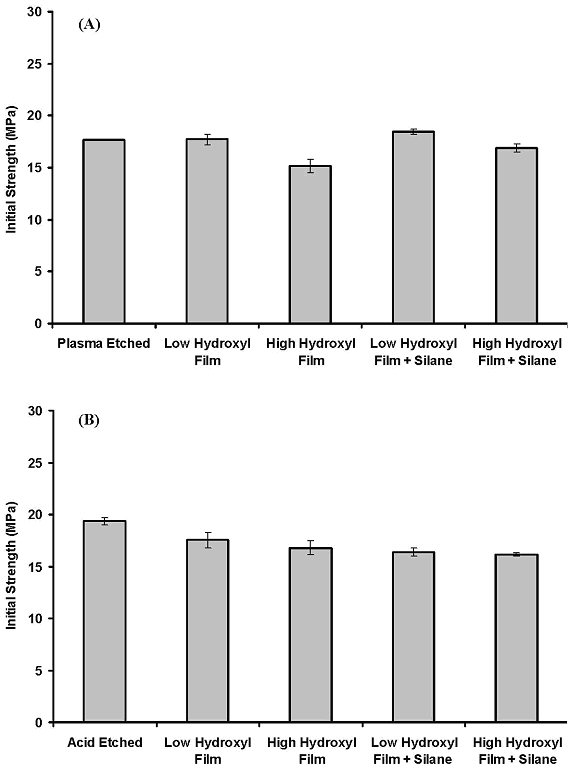
Figure 7. Initial Strength of Lap Joints Prepared Using the One-Part Adhesive and Aluminum Substrates That Were Pretreated by (A) Oxygen Plasma Etching and (B) Etching in 20 Percent by Volume Solution of ALDEOX 171
XPS analysis of failure surfaces of joints with silica-like primer films. XPS analysis was carried out on the failure surfaces of lap joints that were prepared using the two-part adhesive and pulled to failure. The goal was to determine how the joints failed. XPS analysis was not done on the failure surfaces of joints made using the one-part adhesive because those joints clearly failed cohesively within the adhesive, leaving a layer of adhesive on both the "adhesive" and "substrate" failure surfaces. Figure 8 shows the XPS survey spectrum of the neat two-part adhesive after curing in an oven for 1 hour at 100°C. As expected, the spectrum consisted of peaks characteristic of carbon, nitrogen, and oxygen near 285, 400, and 530 eV, respectively. Carbon and oxygen were expected in both the epoxy resin and the curing agent; however, nitrogen was characteristic only of the curing agent. The atomic concentrations of the two-part epoxy adhesive were 86.2 percent carbon, 5.2 percent oxygen and 8.2 percent nitrogen; a trace amount of fluorine was present as a contaminant.
XPS survey spectra of the substrate and adhesive failure surfaces of a joint that was prepared from aluminum substrates that were etched in an O2 plasma are shown in Figure 9. Weak peaks characteristic of aluminum were observed near 74 and 124 eV in the spectrum of the substrate failure surface. A small concentration of nitrogen was observed on the substrate failure surface. The substrate failure surface also had a high atomic concentration of magnesium (see Table 5). The adhesive failure surface of this joint showed no evidence of aluminum or magnesium. These results showed that joints prepared from aluminum substrates that were etched in an O2 plasma and bonded using the two-part adhesive tended to fail near the aluminum/adhesive interface. Similar results were obtained for joints prepared from acid-etched aluminum (see Table 6).
The XPS survey spectrum of the substrate failure surface of a lap joint prepared from aluminum substrates that were etched in an O2 plasma and then primed with a low-hydroxyl film consisted of peaks characteristic of carbon, oxygen, silicon, and nitrogen near 285, 530, 104 and 154, and 400 eV, respectively (see Figure 10). Peaks related to carbon, oxygen, and nitrogen were observed in the XPS spectrum of the adhesive failure surface; the concentrations of these elements were in the same ratios as found in the neat two-part adhesive. This implied that failure occurred near the interface between the adhesive and the silica-like film. Similar results were obtained for lap joints that were prepared from substrates that were acid-etched aluminum and primed with low-hydroxyl films before bonding with the two-part adhesive. These results showed that the interface between the low-hydroxyl film and the aluminum substrate was strong and adhesion of the silica-like films to the substrates was excellent. However, the two-part adhesive did not adhere well to the plasma-polymerized films and failure occurred predominantly at the adhesive/primer film interface.
The substrate failure surface of a joint prepared from aluminum substrates that were etched in an O2 plasma and coated with a high-hydroxyl film had a relatively high concentration of silicon, whereas the adhesive failure surface of the same joint had a small amount of silicon present (see Figure 11). Also, a small amount of nitrogen from the adhesive was seen on the substrate failure surface. These results showed that failure occurred very near to the adhesive/silica-like film interface. The substrate failure surface of joints made with acid-etched aluminum that was primed with high-hydroxyl films had a high percentage of aluminum and a small percentage of silicon, whereas the adhesive failure surface had a low aluminum concentration and a high silicon concentration (see Table 6). This showed that failure occurred near the aluminum/film interface and suggested that either the high-hydroxyl film was cohesively weak or that the bond at interface between the high-hydroxyl film and the aluminum substrate was weak.
The XPS survey spectra obtained from the substrate and adhesive failure surfaces
of lap joints prepared from aluminum that was etched in an O2 plasma, primed
with a low-hydroxyl film, and then coated with a thin film of -GPS are shown
in Figure 12. The atomic concentration of carbon, oxygen, and nitrogen on both
failure surfaces was approximately the same and there was no trace of silicon
or aluminum on either. This showed that failure occurred cohesively within
the adhesive. Moreover, the mechanical strength of the silane/primer and primer/substrate
interfaces was greater than the cohesive strength of the adhesive. Failure
surfaces of joints made with acid-etched aluminum substrates that were primed
with low-hydroxyl films and then coated with a thin silane film showed a small
percentage of silicon (see Table 6). This suggested that failure occurred in
the adhesive, but close to the silane/adhesive interface.
XPS spectra of the adhesive and substrate failure surfaces of joints prepared
from aluminum that was etched in an O2 plasma, primed with a high-hydroxyl
film, and then coated with a thin film of -GPS were similar (see Figure 13).
Significant concentrations of nitrogen and silicon were observed on both failure
surfaces (see Table 5). This showed that failure was cohesive, but partly in
the adhesive and partly in the silane. Spectra of the adhesive and substrate
failure surfaces of joints prepared from acid-etched aluminum that was primed
with a high-hydroxyl film and then coated with a thin silane film also were
similar. Peaks related to nitrogen were observed in both spectra, and a small
peak characteristic of silicon was present on the substrate failure surface
(see Table 6), suggesting that failure occurred cohesively in the adhesive
(but close to the silane/adhesive interface).

Figure 8. XPS Survey Spectrum of Two-Part Epoxy Adhesive on Polished Aluminum Substrate After Curing Overnight and Then Post Curing in an Oven for 1 Hour at 100°C

Figure 9. The XPS Survey Spectra of the (A) Substrate and (B) Adhesive Failure Surfaces of Joints Prepared Using the Two-Part Adhesive and Aluminum Substrates That Were Etched in an O2 Plasma
Table 5. Atomic Concentrations of Elements on the Adhesive and Substrate Failure Surfaces of Adhesive Joints Prepared From Aluminum Substrates That Were Etched in an O2 Plasma and Bonded Using the Two-Part Adhesive. The atomic concentrations were determined from the XPS spectra.
Joint Condition |
Side |
C% |
O% |
N% |
Al% |
Si% |
F% |
Mg% |
Failure Mode |
Plasma Etched | Metal |
43.3 |
29.8 |
4.7 |
6.8 |
- |
5.3 |
10.1 |
Al/Adhesive Interface |
Adhesive |
76.9 |
15.0 |
7.3 |
- |
- |
0.8 |
- |
||
Plasma Etched + Low-Hydroxyl Film | Metal |
48.2 |
33.6 |
4.8 |
- |
13.4 |
- |
- |
Film/Adhesive Interface |
Adhesive |
80.2 |
12.3 |
7.3 |
- |
0.2 |
- |
- |
||
Plasma Etched + High-Hydroxyl Film | Metal |
55.2 |
28.8 |
4.6 |
- |
10.7 |
0.7 |
- |
Film/Adhesive Interface |
Adhesive |
80.9 |
10.6 |
6.7 |
- |
0.7 |
1.1 |
- |
||
Plasma Etched + Low-Hydroxyl Film + Silane | Metal |
94.5 |
3.2 |
2.3 |
- |
- |
- |
- |
Cohesive Within Adhesive |
Adhesive |
94.5 |
3.3 |
2.2 |
- |
- |
- |
- |
||
Plasma Etched + High-Hydroxyl Film + Silane | Metal |
67.9 |
20.6 |
5.8 |
- |
4.8 |
0.9 |
- |
Cohesive in Adhesive and in Silane |
Adhesive |
72.0 |
17.5 |
6.0 |
- |
3.1 |
1.4 |
- |
Table 6. Atomic Concentrations of Elements on the Adhesive and Substrate Failure Surfaces of Adhesive Joints Prepared From Aluminum Substrates That Were Etched in an Acid and Bonded Using the Two-Part Adhesive. The atomic concentrations were determined from the XPS spectra.
Joint Condition |
Side |
C% |
O% |
N% |
Al% |
Si% |
F% |
Failure Mode |
Acid Etched | Metal |
70.4 |
18.1 |
6.4 |
5.1 |
- |
- |
Al/Adhesive Interface |
Adhesive |
78.6 |
13.5 |
7.2 |
0.8 |
- |
- |
||
Acid Etched + Low-Hydroxyl Film | Metal |
63.3 |
22.9 |
5.3 |
- |
8.4 |
- |
Film/Adhesive Interface |
Adhesive |
81.5 |
11.3 |
7.2 |
- |
- |
- |
||
Acid Etched + High-Hydroxyl Film | Metal
|
21.7
|
48.7
|
1.2
|
20.5
|
1.8
|
5.8
|
Al/Adhesive Interface
|
Adhesive
|
28.8
|
49.8
|
3.4
|
2.6
|
15.4
|
-
|
||
Acid Etched + Low-Hydroxyl Film + Silane | Metal |
77.5 |
14.1 |
6.5 |
- |
1.9 |
- |
Cohesive in Adhesive |
Adhesive |
80.4 |
12.3 |
7.1 |
- |
0.2 |
- |
||
Acid Etched + High-Hydroxyl Film + Silane | Metal |
78.3 |
13.4 |
7.0 |
- |
1.3 |
- |
Cohesive in Adhesive |
Adhesive |
81.3 |
11.5 |
7.2 |
- |
- |
- |
Durability and failure analysis of adhesive joints. The durability of aluminum/epoxy lap joints was expressed as the residual strength after immersion for 2 weeks in deionized water at 60°C. Many of the joints made using the two-part adhesive had a residual strength of only about 2-3 MPa after this test. Included were joints made from substrates that were just plasma etched, substrates that were just acid etched, and substrates that were acid etched and then coated with either a low-hydroxyl or high-hydroxyl plasma-polymerized primer film. When joints were made from substrates that were simply etched in acid or an O2 plasma, failure clearly resulted from hydration of the oxide, and the failure surfaces were covered with grey corrosion products. Two sets of joints, including those made from substrates that were etched in an O2 plasma and then coated with either low-hydroxyl or high-hydroxyl silica-like films, failed after only 6 days in water at 60°C. Failure of these joints was related to poor adhesion at the interface between the plasma-polymerized films and the adhesive.
The joints that had the best durability were those prepared from substrates
that were plasma etched or acid etched, coated with low-hydroxyl films, and
then coated with a thin film of -GPS. Those joints had residual strengths
between 10 and 20 MPa. The reason for the good durability of these joints was
related to the use of the silane primer, which prevented debonding at the interface
between the two-part adhesive and the primer, and to the low-hydroxyl primer,
which prevented hydration of the oxide.
Durability was evaluated in the same way for joints prepared using the one-part adhesive (see Figure 14). Regardless of the substrate pretreatment, the strength of most of these joints increased slightly after 2 weeks in deionized water at 60°C, probably because of post curing of the adhesive. Small areas of the failure surfaces were corroded near the edges of the bonded joints. Moreover, all joints prepared using the one-part adhesive failed cohesively within the adhesive, making XPS analysis of the failure surfaces unnecessary.
XPS was conducted on the failure surfaces of joints prepared using the two-part adhesive and plasma-etched substrates after the durability test; the atomic concentrations of elements found on the failure surfaces are shown in Table 7. The substrate failure surface of joints prepared from aluminum substrates that were etched in an O2 plasma had 6.4 percent aluminum. A small concentration of aluminum was present on the adhesive failure surfaces of these joints. It was evident from the XPS spectra and from visual observations of the failure surfaces that corrosion of the substrate had occurred, resulting in failure near the adhesive/substrate interface.

Figure 10. XPS Survey Spectra of the (A) Substrate and (B) Adhesive Failure Surfaces of Joints Prepared Using the Two-Part Adhesive and Aluminum Substrates That Were Etched in an O2 Plasma and Coated With Low-Hydroxyl Plasma-Polymerized Silica-Like Films

Figure 11. XPS Survey Spectra of the (A) Substrate and (B) Adhesive Failure Surfaces of Joints Prepared Using the Two-Part Adhesive and Aluminum Substrates That Were Etched in an O2 Plasma and Coated With High-Hydroxyl Plasma-Polymerized Silica-Like Films

Figure 12. XPS Survey Spectra of the (A) Substrate and (B) Adhesive Failure
Surfaces of Joints Prepared Using the Two-Part Adhesive and Aluminum Substrates
That Were Etched in an O2 Plasma, Coated With Low-Hydroxyl Silica-Like Films,
and Coated With -GPS
XPS results showed that there was a large amount of silicon and a small amount
of nitrogen on the substrate failure surface and a small amount of silicon
and a large amount of nitrogen on the adhesive failure surface of joints
prepared using the two-part adhesive and aluminum substrates that were etched
in an O2 plasma and coated with low-hydroxyl films. This indicated that failure
occurred near the interface between the adhesive and the silica-like film.
Joints prepared from aluminum substrates that were etched in an O2 plasma
and coated with high-hydroxyl silica-like films had significant amounts of
silicon and nitrogen on both substrate and adhesive failure surfaces, showing
that failure mostly was cohesive within the adhesive and the film. The substrate
and adhesive failure surfaces of joints prepared using the two-part adhesive
and aluminum substrates that were etched in an O2 plasma, primed with a low-hydroxyl
film, and coated with a thin film of -GPS
appeared similar and were covered with a visible layer of adhesive; failure
in this case was totally cohesive
within the adhesive. XPS spectra of joints prepared from aluminum substrates
that were etched in an O2 plasma, primed with a high-hydroxyl film, and coated
with a thin silane film were characterized by peaks related to nitrogen and
silicon on both substrate and adhesive failure surfaces (see Table 7). It
was concluded that failure was cohesive within the adhesive, but close to
the silane/adhesive interface.

Figure 13. XPS Survey Spectra
of the (A) Substrate and (B) Adhesive Failure Surfaces of Joints Prepared
Using the Two-Part Adhesive and Aluminum Substrates
That Were Etched in an O2 Plasma, Primed With High-Hydroxyl Silica-Like Films,
and Coated With -GPS
XPS spectra of the failure surfaces of joints prepared using the two-part adhesive and acid-etched aluminum substrates that were primed with low-hydroxyl or high-hydroxyl films were similar; there were large amounts of silicon and nitrogen on the substrate failure surfaces and large amounts of nitrogen on the adhesive failure surfaces (see Table 8). Failure was near the film/adhesive interface for these joints but there were patches of adhesive left on the substrate surface. XPS spectra also were obtained from the failure surfaces of joints prepared using the two-part adhesive and aluminum substrates that were acid etched, primed with low-hydroxyl film or high-hydroxyl films, and covered with thin silane films. Significant amounts of nitrogen were found on both failure surfaces; a small amount of silicon also was observed on the substrate failure surface (see Table 8). This showed that failure was cohesive within the adhesive, but near the silane/adhesive interface.
Long-term and stressed durability tests also were conducted. The long-term tests consisted of immersing joints in water at 60°C and determining their residual strength as a function of immersion time. Stressed durability tests involved applying a load to lap joints, exposing them to a cyclically varying environment, and determining the number of cycles required to produce failure. Results of these tests are shown in Figure 15 and Table 9. The strength of joints prepared using the two-part adhesive and aluminum substrates that were etched in an O2 plasma decreased from 23.0 MPa to 1.7 MPa after 1 week and then remained approximately the same for the rest of the test. When joints were prepared from similar substrates, but using the one-part adhesive, the residual strength decreased slowly from 19.7 MPa to 13.2 MPa in the first 4 weeks of the test and then quickly decreased to 1.0 MPa.
Joints prepared using the two-part adhesive and plasma-etched substrates that were coated with low-hydroxyl, plasma-polymerized films with a thickness of about 600 Å failed after 6 days. Similar joints prepared using the one-part adhesive had the best durability in this test and had retained strength of about 17.7 MPa after 5 weeks. The effect of silica-like film thickness was determined by preparing joints using the two-part adhesive and aluminum substrates that were etched in an O2 plasma, primed with low-hydroxyl silica-like films having thickness of 600 Å or 1,230 Å, and then coated with thin silane films. In both cases, the strength decreased significantly during the first 2 weeks of the test and then remained approximately constant. Joints with the thicker silica-like primer films had somewhat less strength.
Results of the stressed durability tests also are presented in Table 9. Stressed durability is a very severe test. The only joints that had significant stressed durability were those prepared using the one-part adhesive and aluminum substrates that were etched in an O2 plasma and coated with a low-hydroxyl film having a thickness of about 600 Å; those joints failed after 15 cycles. All of the other joints failed after five or less cycles. Failure in the long-term durability and stressed durability tests always involved corrosion of the substrates.
The initial strengths of joints prepared using the two-part and one-part adhesives and aluminum substrates that were etched in an O2 plasma and then primed with low-hydroxyl films deposited at 100°C were 26.2 and 19.0 MPa, respectively (see Figure 16). Similarly, the initial strengths of joints prepared using the two-part and one-part adhesives and aluminum substrates that were etched in an O2 plasma and then primed with high-hydroxyl films deposited at 100°C were 25.0 and 19.0 MPa, respectively (see Figure 16). Reference to Figures 6 and 7 indicates that the initial strengths of joints prepared using the two-part and one-part adhesives and aluminum substrates that were etched in an O2 plasma and then primed with low-hydroxyl films deposited at room temperature were very similar. However, the initial strengths of joints prepared using either of the adhesives and aluminum substrates that were etched in an O2 plasma and then primed with high-hydroxyl films deposited at room temperature were significantly lower, 16.0 and 15.0 MPa, respectively. Thus, the temperature at which the primer films were deposited did not have a significant effect on the initial strength of lap joints prepared using either adhesive and aluminum substrates that were etched in an O2 plasma and then primed with low-hydroxyl films. The temperature at which the primer films were deposited, however, did have a significant effect on the initial strength of lap joints prepared using either adhesive and aluminum substrates that were etched in an O2 plasma and then primed with high-hydroxyl films. Differences in the initial strengths that were observed for joints made with either adhesive and substrates that were etched in an O2 plasma and then coated with low-hydroxyl or high-hydroxyl primers at room temperature (see Figures 6 and 7) disappeared when the primers were deposited at 100°C (see Figure 16).
The short-term durability of lap joints prepared using the two-part adhesive and aluminum substrates that were etched in an O2 plasma and primed with low-hydroxyl or high-hydroxyl films deposited at 100°C was determined. All joints failed within 6 days, that is, well before completion of the test. This does not mean, however, that films deposited at elevated temperatures may not be useful. These films do have low O/Si ratios and should provide superior corrosion protection to aluminum substrates when used with the one-part adhesive or when used with the two-part adhesive and a silane.
XPS spectra were obtained from the failure surfaces of adhesive joints prepared using the two-part adhesive and aluminum substrates that were etched in an O2 plasma and primed with low-and high-hydroxyl films deposited at 100°C. XPS analysis was conducted on the failure surfaces before and after durability testing (see Tables 10 and 11). Significant amounts of nitrogen and silicon were found on the substrate failure surfaces of as-prepared joints. A large concentration of nitrogen, but no silicon, was found on the adhesive failure surfaces, indicating that failure was near the adhesive/primer interface but with patches of adhesive remaining on the substrate failure surface. Similar results were obtained from the failure surfaces of joints after durability testing. Reference to Tables 5 and 7 indicates that very similar results also were obtained for joints prepared from the two-part adhesive and aluminum substrates that were etched in an O2 plasma and primed with low- or high-hydroxyl films deposited at room temperature. It was concluded that deposition of silica-like primers at elevated temperatures did not have a significant effect on the failure mode of joints prepared using the two-part adhesive. Primer films deposited at elevated temperatures, however, are expected to have significantly better performance in stressed durability tests than films deposited at ambient temperatures because they have less nonbridging oxygen atoms.
Effect of substrate on the interfacial chemistry of epoxy/DDA system. One of our main objectives is to identify reactions occurring at the interface between epoxy adhesives and the substrates to which they are applied. We have used FTIR, therefore, to investigate reactions at the interface between a model DGEBA/DDA adhesive and aluminum substrates. Transmission FTIR spectra of DGEBA and DDA are shown in Figures 17(A) and 17(B), respectively. In the spectrum of DGEBA, bands near 2,961 and 2,868 cm-1 were characteristic of the CH3 groups, and the band near 2,924 cm-1 was related to CH2 groups. Bands near 1,607, 1,505, 1,186, and 831 cm-1 were related to the p-disubstituted aromatic rings of DGEBA, and the strong bands near 1,237 and 1,031 cm-1 also were assigned to ether groups in DGEBA. A band related to the epoxy rings in DGEBA appeared near 919 cm-1.
Bands near 3,428, 3,382, 3,181, and 3,145 cm-1 in spectra of DDA resulted from NH and NH2 stretching vibrations of the amine and amide groups. Strong bands near 2,164 and 2,205 cm-1 were assigned to the salt form of DDA (-N=C=N+) and to nitrile (C=N) groups, respectively. Bands near 1,639 and 1,561 cm-1 were related to amide groups.
Infrared spectroscopy was used to follow the course of the curing reaction of the model epoxy. As shown in Figure 17(C), the intensity of the band near 919 cm-1 that was related to epoxy groups and the intensity of the nitrile peak near 2,205 cm-1 that was characteristic of DDA decreased during curing, indicating that the epoxy groups were consumed by reaction with DDA. A strong band related to carbonyl groups in oxazaline and its derivatives appeared at approximately 1,751 cm-1.

Figure 14. Residual Strength After Durability Test of Lap Joints Prepared Using the One-Part Adhesive and Aluminum Substrates That Were Pretreated by (A) Oxygen Plasma Etching and (B) Acid Etching in 20 Percent by Volume Solution of ALDEOX 171
Table 7. Atomic Concentrations From the XPS Spectra of the Adhesive and Substrate Failure Surfaces of Joints Prepared Using the Two-Part Adhesive and Aluminum Substrates That Were Etched in an O2 Plasma. The XPS spectra were acquired after durability testing.
Joint Condition |
Side |
C% |
O% |
N% |
Si% |
Al% |
Failure Mode |
Plasma Etching | Metal |
72.9 |
18.9 |
1.8 |
- |
6.4 |
Al/Adhesive Interface |
Adhesive |
84.7 |
9.0 |
6.3 |
- |
- |
||
Plasma Etched + Low-Hydroxyl Film | Metal |
59.6 |
26.1 |
4.1 |
10.1 |
- |
Film/Adhesive Interface |
Adhesive |
76.9 |
14.9 |
6.8 |
1.4 |
- |
||
Plasma Etched + High-Hydroxyl Film | Metal
|
70.2
|
17.8
|
6.0
|
5.2
|
0.8
|
Cohesive Within Adhesive and Film
|
Adhesive
|
75.1
|
14.7
|
6.2
|
2.9
|
1.1
|
||
Plasma Etched + Low-Hydroxyl Film + Silane | Metal |
Adhesive on Both Sides of Failed
Surfaces |
Cohesive Within Adhesive |
||||
Adhesive |
|||||||
Plasma Etched + High-Hydroxyl Film + Silane | Metal |
52.8 |
30.0 |
5.4 |
11.7 |
- |
Cohesive Within Adhesive |
Adhesive |
78.2 |
13.5 |
7.0 |
1.2 |
- |
Table 8. Atomic Concentrations From the XPS Spectra of the Adhesive and Substrate Failure Surfaces of Joints Prepared Using the Two-Part Adhesive and Aluminum Substrates That Were Etched in an Acid. The XPS spectra were acquired after durability testing.
Joint Condition |
Side |
C% |
O% |
N% |
Si% |
Al% |
Failure Mode |
Acid Etching | Metal |
38.5 |
44.8 |
3.1 |
- |
13.6 |
Al/Adhesive Interface |
Adhesive |
78.6 |
12.6 |
7.8 |
- |
0.9 |
||
Acid Etched + Low-Hydroxyl Film | Metal |
57.8 |
24.2 |
6.2 |
11.8 |
- |
Film/Adhesive Interface |
Adhesive |
84.5 |
7.8 |
7.3 |
0.4 |
- |
||
Acid Etched + High-Hydroxyl Film | Metal
|
49.3
|
30
|
5.9
|
14.8
|
-
|
Film/Adhesive Interface
|
Adhesive
|
84.0
|
8.6
|
7.4
|
-
|
-
|
||
Acid Etched + Low-Hydroxyl Film + Silane | Metal |
78.0 |
13.3 |
6.6 |
2.2 |
- |
Cohesive Within Adhesive |
Adhesive |
83.1 |
9.4 |
7.5 |
- |
- |
||
Acid Etched + High-Hydroxyl Film + Silane | Metal |
75.9 |
13.8 |
6.9 |
3.3 |
- |
Cohesive Within Adhesive |
Adhesive |
84.4 |
8.3 |
7.3 |
- |
- |

Figure 15. Average Strength Versus Immersion Time in Deionized
Water at 60°C
for Lap Joints Prepared From Aluminum Substrates That Were Etched in an O2
Plasma and Then Primed: (-) One-Part Adhesive, No Primer; () Two-Part
Adhesive, No Primer; (
) One-Part Adhesive and Low-Hydroxyl Primer
Film (600 Å); (
) Two-Part Adhesive and Low-Hydroxyl Primer Film (600 Å);
(
) Two-Part
Adhesive, Low-Hydroxyl Film (600 Å), and Thin Silane Film; (
) Two-Part
Adhesive, Low-Hydroxyl Film (1,230 Å), and Thin Silane Film
Pretreatment Used |
Adhesive |
Residual Strength (MPa)a |
Stress Durability (cycles)b |
|||||
0 Week |
1 Week |
2 Weeks |
3 Weeks |
4 Weeks |
5 Weeks |
|||
Plasma Etched | One-part |
19.7 |
18.0 |
18.3 |
16.3 |
13.2 |
1.0 |
5 |
Plasma Etched | Two-part |
23.0 |
1.7 |
1.8 |
2.1 |
2.7 |
2.9 |
2 |
Plasma Etched + Low Hydroxyl (600 Å) | One-part |
17.6 |
19.0 |
19.5 |
19.1 |
17.7 |
17.0 |
15 |
Plasma Etched + Low Hydroxyl (600 Å) | Two-part |
26.6 |
0.0 |
0.0 |
0.0 |
0.0 |
0.0 |
1 |
Plasma Etched + Low Hydroxyl (600 Å) + Silane | Two-part |
23.6 |
19.8 |
11.1 |
10.3 |
9.9 |
9.0 |
1 |
Plasma Etched + Low Hydroxyl (1,230 Å) + Silane | Two-part |
20.0 |
15.7 |
6.8 |
6.2 |
7.2 |
- |
1 |
a Joints were immersed in deionized water at 60°C. b Joints were stressed to 6.9 MPa and then exposed to a cyclically varying environment. Each cycle consisted of 15 minutes in 5 percent NaCl at room temperature, 105 minutes drying at room temperature, and then exposure to 90 percent relative humidity at 50°C for 22 hours. |

Figure 16. Initial Strength Lap Joints Prepared From Aluminum Substrates That Were Etched in an O2 Plasma and Then Coated With Low-Hydroxyl or High-Hydroxyl Silica-Like Films
Table 10. Atomic Concentration Obtained From the XPS Analysis of the Adhesive and Substrate Failure Surfaces of Lap Joints Prepared From the Two-Part Adhesive and Aluminum Substrates That Were Etched in an Oxygen Plasma and Then Coated With Low-Hydroxyl Plasma-Polymerized Films at 100°C. The XPS spectra were obtained before and after durability testing of the joints.
Joint Condition | Failure Surface |
C% |
O% |
N% |
Si% |
Failure Mode |
Before Durability Test | Substrate |
67.8 |
19.3 |
4.6 |
8.3 |
Film/Adhesive Interface |
Adhesive |
84.2 |
8.6 |
7.2 |
- |
||
After Durability Test | Substrate |
52.9 |
30.4 |
4.8 |
11.8 |
Film/Adhesive Interface |
Adhesive |
79.6 |
12.2 |
7.5 |
0.7 |
Table 11. Atomic Concentrations Obtained From the XPS Analysis of the Adhesive and Substrate Failure Surfaces of Lap Joints Prepared From the Two-Part Adhesive and Aluminum Substrates That Were Etched in an Oxygen Plasma and Then Coated With High-Hydroxyl Plasma-Polymerized Films at 100°C. The XPS spectra were obtained before and after durability testing of the joints.
Joint Condition | Failure surface |
C% |
O% |
N% |
Si% |
Failure Mode |
Before Durability Test | Substrate |
79.7 |
11.7 |
6.5 |
2.2 |
Film/Adhesive Interface |
Adhesive |
83.4 |
9.4 |
7.2 |
- |
||
After Durability Test | Substrate |
52.9 |
30.4 |
4.8 |
11.8 |
Film/Adhesive Interface |
Adhesive |
79.6 |
12.2 |
7.5 |
0.7 |
Thin films of the epoxy system then were spin coated onto aluminum substrates from a 5 percent solution in DMF and cured at 150°C under nitrogen for times ranging from 2.5 minutes to 2.5 hours. After curing, the films were rinsed vigorously in DMF to remove any DDA or DGEBA that was not bound strongly to the aluminum substrate and then dried. RAIR spectra then were obtained from the films. Films were formed on ferroplate substrates using the same procedures so that the effect of substrate on the structure of the films could be determined.
For relatively long cure times, spectra of films that were formed on aluminum and ferroplate and cured at 150°C under nitrogen were similar to each other and to spectra of the model adhesive (see Figure 18). The most significant difference between spectra of films formed on aluminum and ferroplate was that films formed on aluminum were about twice as thick as films formed on ferroplate, regardless of the curing time.
For relatively short cure times, spectra of films formed on aluminum and ferroplate also were similar (see Figure 19). Some differences, however, were noted. Bands in spectra of films on aluminum were about double the intensity of those on ferroplate, indicating that films formed on aluminum were about twice as thick as those on ferroplate. A band near 957 cm-1 was observed in spectra of films formed on aluminum, but not in spectra of films formed on ferroplate. This band was attributed to an increase in the thickness of the oxide on aluminum during curing. Bands resulting from the nitrile group of DDA and the salt form of DDA were seen near 2,194 and 2,157 cm-1 in spectra of films formed on aluminum, but not in spectra of films formed on ferroplate. Well-resolved bands were observed near 1,653, 1,559, and 1,510 cm-1 in spectra of films formed on aluminum. By comparison, only a broad continuous absorption was observed between 1,750 and 1,450 cm-1 for films formed on ferroplate.
We still are investigating the structure of films formed on aluminum and other substrates. However, the results obtained so far indicate that the substrate does have a significant effect on the structure of epoxy/DDA adhesives.
Conclusions
• Low-hydroxyl, plasma-polymerized silica-like films are more inorganic and dense than high-hydroxyl films. Films deposited at high substrate temperatures are even more inorganic in nature.
• Low-hydroxyl, plasma-polymerized silica-like films are more effective than high-hydroxyl films in protecting aluminum substrates from corrosion.
• The hydroxyl content of silica-like primer films has a significant effect on the breaking strength of aluminum/epoxy lap joints for a given adhesive; increasing the hydroxyl content of the primer film results in a decrease in strength.
• Two-part epoxy adhesives with a polyamide/amine curing agent formed weak bonds with poor durability to low-hydroxyl and high-hydroxyl plasma-polymerized silica-like films.
• Application of a silane coupling agent such as -GPS to a silica-like
film enabled the two-part adhesive to form strong, durable bonds to plasma-polymerized
silica-like films.
• The one-part adhesive with a dicyandiamide curing agent formed strong, durable bonds to plasma-polymerized silica-like films.
• Long-term and stress durability tests show that the one-part adhesive forms more stable bonds to silica-like films than the two-part adhesive.
• Lap joints prepared using the one-part adhesive with a dicyandiamide curing agent always failed cohesively within the adhesive, but joints prepared using the two-part adhesive failed mostly at the substrate/adhesive or primer/adhesive interface.
• Oxygen plasma etching processes were very aggressive in removing nearly all of the adsorbed surface contaminants from aluminum surfaces, but were not effective in removing magnesium oxide layers.
• The substrate plays a significant role in the curing of epoxy/dicyandiamide adhesive systems.

Figure 17. Infrared Spectra of (A) DGEBA, (B) DDA, and (C) Model Epoxy Adhesive Obtained by Curing a 7:1 Mixture of DGEBA and DDA at 150°C Overnight

Figure 18. RAIR Spectra of Films Formed by Spin Coating 5 Percent Solutions of DDA and DGEBA in DMF Onto Polished Metal Substrates, Curing the Films for 2.5 Hours at 150°C Under Nitrogen, and Then Rinsing the Films in Neat DMF for 30 Minutes. The substances were (A) ferroplate and (B) aluminum. The ratio of DDA to DGEBA was 7:1.

Figure 19. RAIR Spectra of Films Formed by Spin Coating 5 Percent Solutions of DDA and DGEBA in DMF Onto Polished Metal Substances, Curing the Films for 10 Minutes at 150°C Under Nitrogen, and Then Rinsing the Films in Neat DMF for 30 Minutes. The substrates were (A) ferroplate and (B) aluminum. The ratio of DDA to DGEBA was 7:1.
Future Activities:We will continue to investigate the molecular structure of interfaces between adhesive systems and the substrates to which they are applied. These investigations will help us to determine the mechanisms involved in adhesion and will help us to devise improved primer films.
Plasma-polymerized silica-like films deposited onto aluminum substrates at elevated temperatures have lower O/Si ratios and fewer nonbridging oxygen atoms than films deposited at room temperature. These films are less porous than films formed at room temperature and are expected to be improved primers. Therefore, we will carry out long-term durability and stressed durability on joints prepared using substrates that are coated with silica-like films deposited at elevated temperatures.
It is very desirable to carry out all pretreatment processes in the plasma reactor. Therefore, we will continue to investigate plasma techniques for pretreating aluminum before the deposition of plasma-polymerized films. One candidate consists of etching in an argon/H2 plasma.
Journal Articles:No journal articles submitted with this report: View all 7 publications for this project
Supplemental Keywords:waste reduction, waste minimization, clean technologies, plasma polymerization, clean manufacturing, coating processes, engineering, green design, environmentally benign coating, x-ray photoelectron spectroscopy, XPS, aluminum, Al, low hydroxyl, high hydroxyl, silica-like films, ferroplate, adhesive, acid etched. , Sustainable Industry/Business, Scientific Discipline, RFA, Technology for Sustainable Environment, Sustainable Environment, Chemical Engineering, Environmental Engineering, Environmental Chemistry, clean manufacturing designs, industrial design for environment, environmental sustainability, waste reduction, clean technologies, green design, plasma polymerization, coating processes, engineering, waste minimization, environmentally conscious manufacturing, industrial innovations, environmentally benign coating, metal surface engineering, alternative materials, metal finishing, innovative technology, environmentally conscious design, pollution prevention
Progress and Final Reports:
2002 Progress Report
Original Abstract
2004 Progress Report
Final Report