Technical Links > Osha Technical Manual
SECTION VIII: CHAPTER 2 [New addition to OTM]
RESPIRATORY PROTECTION
Contents:
Appendix VIII:2-1. Glossary
Appendix VIII:2-2. User Seal Check
Appendix VIII:2-3. Recommended Procedures for Cleaning Respirators
Appendix VIII:2-4. NIOSH Guide to the Selection and Use of Particulate
Respirators Certified under 42 CFR 84
- INTRODUCTION.
- Wearing respiratory protective devices to reduce exposure to airborne contaminants is widespread in industry. An estimated 5.0 million workers wear respirators, either occasionally or routinely. Although it is preferred industrial
hygiene practice to use engineering controls to reduce contaminant emissions at their source, there are operations where this type of control is not technologically or economically feasible or is otherwise inappropriate.
- Since respirators are not as consistently reliable as engineering and work practice controls, and may create additional problems, they are not the preferred method of reducing exposures below the occupational exposure levels.
Accordingly, their use as a primary control is restricted to certain circumstances. In those circumstances where engineering and work practice controls cannot be used to reduce airborne contaminants below their occupational
exposure levels (e.g., certain maintenance and repair operations, emergencies, or during periods when engineering controls are being installed), the use of respirators could be justified to reduce worker exposure. In other cases,
where work practices and engineering controls alone cannot reduce exposure levels to below the occupational exposure level, the use of respirators would be essential for supplemental protection.
- There are many variables that affect the degree of protection afforded by respiratory protective devices, and the misuse of respirators can be hazardous to employee safety and health. Selection of the wrong equipment, one of
the most frequent errors made in respiratory protection, can result in the employee being exposed to increased concentrations of the harmful contaminant. This error may result in a broad range of health effects caused by the
harmful contaminants, including silicosis, asbestosis, permanent lung damage, and cancer. Respirators that are not maintained and inspected can be less effective at reducing exposure to the harmful contaminants, and can place
a greater burden on the respiratory system. Respirators that are not clean can cause dermatitis or skin irritation. Because respirator use may give the employee a false sense of security and presumed protection, an improper
respirator program can actually present a high degree of hazard for the employee.
- Respirators can only provide adequate protection if they are properly selected for the task; are fitted to the wearer and are consistently donned and worn properly; and are properly maintained so that they continue to provide
the protection required for the work situation. These variables can only be controlled if a comprehensive respiratory protection program is developed and implemented in each workplace where respirators are used. When respirator
use is augmented by an appropriate respiratory protection program, it can prevent fatalities and illnesses from both acute and chronic exposures to hazardous substances.
- The primary aim of this chapter is to give detailed instruction in the selection of the proper respirator and its use and maintenance. The emphasis is on the implementation of a respiratory protection program developed in a
logical progression of steps, outlined below:
- A clear definition of the hazards that will be encountered and the degree of protection required;
- The selection and fitting of the respirator;
- Medical evaluation for respirator selection and use;
- The required training in the correct use and care of the respirator; and
- The implementation of a maintenance program that will ensure that a high level of respiratory protection is maintained.
- HISTORY OF THE DEVELOPMENT OF RESPIRATORY PROTECTION.
- EARLY PRACTICES. The concept of using respiratory protective devices to reduce or eliminate hazardous exposures to airborne contaminants first came from Pliny (circa A.D. 23-79) who discussed the idea of
using loose fitting animal bladders in Roman mines to protect workers from the inhalation of red oxide of lead. (See proposed respiratory protection standard, 59
Federal Register 58885.) Later, in the 1700's, the ancestors of modern atmosphere-supplying devices, such as the self-contained breathing apparatus or hose mask, were developed. Although the devices
themselves have become more sophisticated in design and materials, respirators' performance is still based on one of two basic principles: purifying the air by removing contaminants before they reach the breathing zone of the
worker, or providing clean air from an uncontaminated source.
- DEVELOPMENT OF MODERN METHODS. In 1814, a particulate-removing filter encased in a rigid container was developed -- the predecessor of modern filters for air-purifying respirators. In 1854 it was recognized
that activated charcoal could be used as a filtering medium for vapors. During World War I, with the use of chemical warfare, improvements in the design of respirators was necessary. In 1930 the development of the resin-impregnated
dust filter made available efficient, inexpensive filters that have good dust-loading characteristics and low breathing resistance.
- LATEST ADVANCES. A more recent development was the high efficiency particulate filter made with very fine glass fibers. These extremely efficient filters are used for very small airborne particles and produce little breathing
resistance. Some features that are currently being incorporated into respirator design include a smaller facepiece, which translates into a better field of vision and a low profile that permits the respirator to fit under other
protective gear such as a welder's helmet. Over the years there have been continuing major developments in the basic design of respirators. Modern design improvements have created products that are both more comfortable to wear
and more protective than earlier respirators.
- GENERAL INFORMATION.
- PURPOSE. The purpose of a respirator is to prevent the inhalation of harmful airborne substances and/or an oxygen-deficient atmosphere. Functionally, a respirator is designed as an enclosure that covers the nose and mouth
or the entire face or head. Respirators are of two general "fit" types, tight-fitting and loose-fitting.
- The tight-fitting respirator (Figure VIII:2-1) is designed to form a seal with the face of the wearer. It is available in three types: quarter mask, half mask, and full facepiece. The quarter mask covers the nose
and mouth, where the lower sealing surface rests between the chin and the mouth. The half mask covers the nose and mouth and fits under the chin. The full facepiece covers the entire face from below the chin to the hairline.
- The loose-fitting respirator (Figure VIII:2-2) has a respiratory inlet covering that is designed to form a partial seal with the face. These include loose-fitting facepieces, as well as hoods, helmets,
blouses, or full suits, all of which cover the head completely. The best known loose-fitting respirator is the supplied air hood used by the abrasive blaster. The hood covers the head, neck, and upper torso,
and usually includes a neck cuff. Air is delivered by a compressor through a hose leading into the hood. Because the hood is not tight-fitting, it is important that sufficient air is provided to maintain
a slight positive-pressure inside the hood relative to the environment immediately outside the hood. In this way, an outward flow of air from the respirator will prevent contaminants from entering the hood.
FIGURE VIII:2-1. TIGHT-FITTING RESPIRATORS.
FIGURE VIII:2-2. LOOSE-FITTING RESPIRATORS.
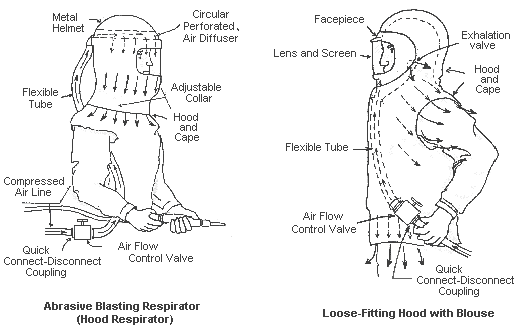
- AIRBORNE (OR RESPIRATORY) HAZARDS may result from either an oxygen deficient atmosphere or breathing air contaminated with toxic particles, vapors, gases, fumes or mists. The proper selection and use of a respirator depend
upon an initial determination of the concentration of the hazard or hazards present in the workplace, or the presence of an oxygen deficient atmosphere.
Airborne hazards generally fall into the following basic categories:
- Dusts. Particles that are formed or generated from solid organic or inorganic materials by reducing their size through mechanical processes such as crushing, grinding, drilling, abrading, or blasting.
- Fumes. Particles formed when a volatilized solid, such as a metal, condenses in cool air. This physical change is often accompanied by a chemical reaction, such as oxidation. Examples are lead oxide fumes from
smelting, and iron oxide fumes from arc-welding. A fume can also be formed when a material such as magnesium metal is burned or when welding or gas cutting is done on galvanized metal.
- Mists. A mist is formed when a finely divided liquid is suspended in the air. These suspended liquid droplets can be generated by condensation from the gaseous to the liquid state or by breaking up a liquid into
a dispersed state, such as by splashing, foaming, or atomizing. Examples are the oil mist produced during cutting and grinding operations, acid mists from electroplating, acid or alkali mists from pickling operations,
paint spray mist from spraying operations, and the condensation of water vapor to form a fog or rain.
- Gases. Gases are formless fluids that occupy the space or enclosure and which can be changed to the liquid or solid state only by the combined effect of increased pressure and decreased temperature. Examples are
welding gases such as acetylene, nitrogen, helium and argon; and carbon monoxide generated from the operation of internal combustion engines. Another example is hydrogen sulfide, which is formed wherever there is decomposition
of materials containing sulfur under reducing conditions.
- Vapors. Vapors are the gaseous form of substances that are normally in the solid or liquid state at room temperature and pressure. They are formed by evaporation from a liquid or solid, and can be found where
parts cleaning and painting takes place and where solvents are used.
- Smoke. Smoke consists of carbon or soot particles resulting from the incomplete combustion of carbonaceous materials such as coal or oil. Smoke generally contains droplets as well as dry particles.
- Oxygen deficiency. An oxygen deficient atmosphere has an oxygen content below 19.5% by volume. Oxygen deficiency may occur in confined spaces, which include, but are not limited to, storage tanks, process vessels,
towers, drums, tank cars, bins, sewers, septic tanks, underground utility tunnels, manholes, and pits.
- RESPIRATOR CLASSIFICATIONS. Respirators provide protection either by removing contaminants from the air before they are inhaled or by supplying an independent source of respirable air. There are two major classifications
of respirators:
- Air purifying respirators (devices that remove contaminants from the air); and
- Atmosphere-supplying respirators (those devices that provide clean breathing air from an uncontaminated source).
Each class of respirator may have tight-fitting and loose-fitting facepieces. An important aspect of respirator operation and classification is the air pressure within the facepiece. When the air pressure within the facepiece
is negative during inhalation with respect to the ambient air pressure, the respirator is termed a negative-pressure respirator. When the pressure is normally positive with respect to ambient air pressure throughout
the breathing cycle, the respirator is termed a positive-pressure respirator. The concept of negative and positive pressure operation is important when considering potential contaminant leakage into the respirator.
- AIR PURIFYING RESPIRATORS are grouped into three general types: particulate removing, vapor and gas removing, and combination. Elements that remove particulates are called filters, while vapor and gas removing
elements are called either chemical cartridges or canisters. Filters and canisters/cartridges are the functional portion of air-purifying respirators, and they can generally be removed and replaced once their effective
life has expired. The exception would be filtering facepiece respirators (commonly referred to as "disposable respirators," "dust masks," or "single-use respirators"), which cannot be cleaned, disinfected, or resupplied
with an unused filter after use.
- Particulate-removing respirators are designed to reduce inhaled concentrations of nuisance dusts, fumes, mists, toxic dusts, radon daughters, asbestos-containing dusts or fibers, or any combination
of these substances, by filtering most of the contaminants from the inhaled air before they enter the breathing zone of the worker. They may have single-use or replaceable filters. These respirators may
be non-powered or powered air-purifying. A powered air-purifying respirator (PAPR) uses a blower to force the ambient atmosphere through air purifying elements to the inlet covering.
- Vapor- and gas-removing respirators are designed with sorbent elements (canisters or cartridges) that adsorb and/or absorb the vapors or gases from the contaminated air before they can enter the breathing zone
of the worker. Combination cartridges and canisters are available to protect against particulates, as well as vapors and gases.
- ATMOSPHERE-SUPPLYING RESPIRATORS are respirators that provide air from a source independent of the surrounding atmosphere instead of removing contaminants from the atmosphere. These respirators are classified by the method
that is used to supply air and the way in which the air supply is regulated. Basically, these methods are: self-contained breathing apparatus (air or oxygen is carried in a tank on the worker's back, similar to SCUBA gear);
supplied-air respirators (compressed air from a stationary source is supplied through a high-pressure hose connected to the respirator); and combination self-contained and supplied-air
respirators.
- LIMITATIONS OF RESPIRATOR USE. Not all workers can wear respirators. Individuals with impaired lung function, due to asthma or emphysema for example, may be physically unable to wear a respirator. Individuals who cannot
get a good facepiece fit, including those individuals whose beards or sideburns interfere with the facepiece seal, will be unable to wear tight-fitting respirators. An adequate fit is required for a respirator to
be effective. In addition to these problems, respirators may also be associated with communication problems, vision problems, fatigue, and reduced work efficiency.
In principle, respirators usually are capable of providing adequate protection. However, problems associated with selection, fit, and use often render them less effective in actual application; these problems prevent the assurance
of consistent and reliable protection, regardless of the theoretical capabilities of the respirator. Occupational safety and health experts have spent considerable effort over the years developing fit-testing procedures
and methods of measuring respirator effectiveness, thereby improving protection for those employees required to wear them.
- RESPIRATOR PROTECTION PROGRAM.
- THE STANDARD. Whenever respirators are required to be worn, a written respirator protection program must be developed and implemented in accordance with OSHA's respirator standard, 29 CFR 1910.134.
(Additional program requirements may be found in the standards that regulate the hazards to which the employee is exposed.) Because workplaces differ substantially, each program must be tailored to the specific conditions of
the workplace. The program must consist of worksite-specific procedures governing the selection, use, and care of respirators. The program must be updated as often as necessary to reflect changes in workplace conditions
and respirator use.
- THE WORKSITE-SPECIFIC PROCEDURES must contain all the information needed to maintain an effective respirator program to meet the user's individual requirements. These procedures are a set of step-by-step
instructions written so that a task (i.e., respirator use, fit-testing procedures, cleaning and storage, etc.) can be performed by all personnel in a uniform and consistent way, while supplying the maximum protection
for workers who use respirators in the workplace. The employer must anticipate both the routine and non-routine use of respirators, as well as any possible emergency use based on the conditions in the workplace in which they
are to be used. Worksite-specific procedures must be written so as to be useful to those who are directly involved in the respirator program: the program administrator, those fitting the respirators and training
the workers, respirator maintenance workers, and the supervisors responsible for overseeing respirator use on the job.
- ADMINISTRATION. In addition, the respirator standard requires that the respiratory protection program be administered by one qualified individual to ensure that the integrity of the respiratory protection program is maintained
through the continuous oversight of one responsible person. The program administrator must be qualified by appropriate training and/or experience in the proper selection, use, and maintenance of respirators, be responsible for
implementing the respiratory protection program, and conduct regular evaluations of the program's effectiveness.
Although responsibility for respirator program oversight rests with the program administrator, he or she may delegate responsibilities to other qualified individuals. For instance, a large facility may find it practical and
economical to have a staff of personnel involved in the respirator program, each with their own area of responsibility. However, each of these people must report to the one administrator who has overall responsibility for the
program. This approach promotes coordination of all facets of the program. The administrator should have the full support of higher level management; without it, an effective respirator program is difficult to initiate and maintain.
- ELEMENTS. The respiratory protection program must cover the following basic elements, as applicable:
- Procedures for selecting respirators for use in the workplace;
- Medical evaluations of employees required to use respirators;
- Fit testing procedures for tight-fitting respirators;
- Use of respirators in routine and reasonably foreseeable emergency situations;
- Procedures and schedules for cleaning, disinfecting, storing, inspecting, repairing, and otherwise maintaining respirators;
- Procedures to ensure adequate air quality, quantity and flow of breathing air for atmosphere-supplying respirators;
- Training of employees in the respiratory hazards to which they are potentially exposed;
- Training of employees in the proper use of respirators, including putting on and removing them, any limitations on their use, and maintenance procedures; and
- Procedures for regularly evaluating the effectiveness of the program.
- RESPIRATOR SELECTION.
Respirator selection requires correctly matching the respirator with the hazard, the degree of hazard, and the user. The respirator selected must be adequate to effectively reduce the exposure of the respirator user under all conditions
of use, including reasonably foreseeable emergency situations. Proper respirator selection involves choosing a device that fully protects the worker from the respiratory hazards to which he or she may be exposed and permits the worker
to perform the job with the least amount of physical burden.
- SELECTION FACTORS. Many factors must be considered carefully in respirator selection. In choosing the appropriate respirator, one must consider the nature and extent of the hazard, work requirements and conditions, and
the characteristics and limitations of the respirators available. The following categories of information must be taken into account:
- Nature of the hazard, and the physical and chemical properties of the air contaminant;
- Concentrations of contaminants;
- Relevant permissible exposure limit or other occupational exposure limit;
- Nature of the work operation or process;
- Time period the respirator is worn;
- Work activities and physical/psychological stress;
- Fit testing; and
- Physical characteristics, functional capabilities and limitations of respirators.
- Nature of the hazard, and the physical and chemical properties of the air contaminant. The nature of the hazard, whether it is in the form of a gas, dust, organic vapor, fume, mist, oxygen deficiency or any combination
of hazards, needs to be taken into account. The physical and chemical properties of the contaminant that affect respirator selection, and the selection of respirator components such as cartridges, canisters, and filters
must also be considered. Physical properties include such factors as particle size for dusts, and vapor pressure for gases and vapors. Chemical properties of the air contaminant that affect breakthrough times, and the
ability of the filter material to remove, adsorb, or absorb the contaminant must also be considered.
- Concentrations of contaminants. Sampling and analysis of the workplace air determines what degree of exposure is occurring, and thus what degree of protection is required. Where such sampling and analysis have
been done, the results are to be used as a point of comparison with the occupational exposure level, i.e., to determine how much the concentration must be lowered by the respirator to reduce employee exposure to a safe
level.
- The relevant permissible exposure limit or other occupational exposure limit. Respirators selected must be capable of protecting against overexposure by reducing and maintaining exposure to or below the relevant
exposure limit. In addition to the OSHA limits, employers should refer to the ACGIH (American Conference of Governmental Industrial Hygienists) recommended Threshold Limit Values (TLV's), the NIOSH (National Institute
for Occupational Safety and Health) Recommended Exposure Limits (REL's), or other occupational exposure limits.
- Nature of the work operation or process. The type of job operation, the equipment or tools that will be used, and any motion or travel the job requires can influence the type of respirator selected, particularly
when supplied-air respirators, which require a connection to a clean air source, are used.
- Time period respirator is worn. The employer must also consider the period of time during which the respirator will be used by employees during a work shift. Breakthrough times for different chemicals can vary
greatly, and are dependent on the concentrations of contaminants in the workplace air, patterns of respirator use, and environmental factors including temperature and humidity. A respirator that provides adequate protection
for one chemical may be inadequate for another chemical with a different breakthrough time. In addition, employees wearing respirators for longer periods of time may need respirators that impose the minimum possible
physical burden.
- Work activities and stress. The work activities of employees while wearing respirators are also a factor. Heavy work that is physically draining may affect an employee's capability of wearing certain types of
respirators. Temperature and humidity conditions in the workplace may also affect the physical/psychological stress level associated with wearing a respirator, as well as the effectiveness of respirator filters and cartridges.
These types of factors must be assessed in selecting the appropriate equipment for a particular work situation.
- Fit testing. Some employees may be unable to achieve an adequate fit with certain respirator models or a particular type of respirator -- such as half-mask air-purifying respirators --
so an alternative respirator model with an adequate fit or other type of respirator that provides adequate protection must be used. Therefore, it is necessary for employers to provide a sufficient number of respirator
models and sizes from which employees can choose an acceptable respirator that fits correctly.
- Physical characteristics, functional capabilities, and limitations of respirators. The last category of information to be considered when selecting respiratory protection is the physical characteristics, functional
capabilities, and limitations of the respiratory protection equipment itself. Respirators selected must not impair the worker's vision, hearing, communication, and physical movement necessary to perform jobs safely.
For example, airline respirators should not be used by mobile employees around moving machinery to avoid entanglement of the respirator in the equipment.
- SELECTION. Once the above factors have been taken into account, the employer must select a NIOSH-certified respirator. Where NIOSH has not specifically certified any respirator for use against the particular
contaminant present in the workplace, the employer must select a NIOSH-certified respirator that has no limitation prohibiting its use for that contaminant. The respirator must be appropriate for the contaminant's
physical form and chemical properties and the conditions under which it will be used. All respirators must be chosen and used according to the limitations of the NIOSH certification, which appears on the NIOSH certification
label.
- ASSIGNED PROTECTION FACTORS. Until such time as OSHA addresses the issue of assigned protection factors (APF's), employers may rely on APF's published by NIOSH and ANSI. Where there are conflicts between the NIOSH and
ANSI APF's, the employer should apply the more protective APF.
- WARNING SYSTEM. When an air-purifying respirator is selected for protection against gases and vapors, a system must be in effect that will reliably warn respirator wearers of contaminant breakthrough. These systems are:
a respirator equipped with an end-of-service life indicator (ESLI) certified by NIOSH for the contaminant, or an established and enforced cartridge/canister change schedule that is based on objective information
or data that will ensure that canisters and cartridges are changed before the end of their service life.
- ATMOSPHERES REQUIRING HIGHEST LEVEL OF PROTECTION. For atmospheres that are immediately dangerous to life and health (IDLH), the highest level of respiratory protection and reliability is required. These atmospheres,
by definition, are the most dangerous environments in which respirators are used. In these atmospheres, there is no tolerance for respirator failure. Consequently, only the following respirators must be provided and used: full-facepiece
pressure demand self-contained breathing apparatus (SCBA) certified for a minimum service life of thirty minutes, or a combination full-facepiece pressure demand supplied-air respirator
(SAR) with an auxiliary self-contained air supply.
- MEDICAL EVALUATION
- OVERVIEW. Persons assigned to tasks that require the use of a respirator must be physically able to perform the work while using the respirator. Accordingly, employers have the responsibility of ensuring that employees
are medically fit to tolerate the physical and psychological stress imposed by respirator use, as well as the physical stress originating from job and workplace conditions.
Employees must be medically evaluated and found eligible to wear the respirator selected for their use prior to fit testing or first-time use of the respirator in the workplace. Medical eligibility is to be determined
by a physician or other licensed health care professional (referred to as a "PLHCP"). A variety of qualified health care providers, besides physicians, including occupational health nurses, nurse practitioners, and physician
assistants, can perform the medical evaluations provided they are licensed to do so in the state in which they practice.
- QUESTIONNAIRE. In assessing the employee's medical eligibility to use a respirator, the PLHCP must perform a medical evaluation using a medical questionnaire (Appendix
C to 1910.134) or provide a medical examination that obtains the same information as the medical questionnaire. The medical evaluation must be administered confidentially and at a time and place, during working hours, that
is convenient to the employee. Employers are free to provide respirator users with a medical examination in lieu of the medical questionnaire if they chose to do so, but they are not required by the standard to administer a
medical examination unless the employee gives a positive response to specific questions on the questionnaire.
- MEDICAL FACTORS AND CONDITIONS. The purpose of a medical evaluation program is to determine if employees can tolerate the physiological burden associated with respirator use, including: the burden imposed by the respirator
itself (e.g., its weight and breathing resistance during both normal operation and under conditions of filter, canister, or cartridge overload); musculoskeletal stress (e.g., when the respirator to be worn is a SCBA); limitations
on auditory, visual, and olfactory sensations; and isolation from the workplace environment. Since certain jobs and workplace conditions in which a respirator is used can also impose a physiological burden on the user, the medical
evaluation must also consider the following factors: type and weight of the respirator to be worn; duration and frequency of respirator use; expected physical work effort; use of protective clothing and equipment to be worn;
and temperature and humidity extremes that may be encountered. This information must be provided to the PLHCP before the PLHCP makes a recommendation regarding an employee's ability to use a respirator.
The medical evaluation is designed to identify general medical conditions that place employees who use respirators at risk of serious medical consequences. Medical conditions known to compromise an employee's ability to tolerate
respirator-, job-, and workplace-related physiological stress include: cardiovascular and respiratory diseases (e.g., a history of high blood pressure, angina, heart attack, cardiac arrhythmias, stroke, asthma,
chronic bronchitis, emphysema); reduced pulmonary function caused by other factors (e.g., smoking or prior exposure to respiratory hazards); neurological or musculoskeletal disorders (e.g., ringing in the ears, epilepsy, lower
back pain); impaired sensory function (e.g., perforated ear drums, reduced or absent ability to smell); and psychological disorders (e.g., claustrophobia and severe anxiety).
- STANDARD OF EVALUATION. The employer must obtain a written recommendation from the PLHCP on whether the employee is medically able to wear a respirator. The recommendation must identify any limitations on the employee's
use of the respirator, as well as the need for follow-up medical evaluations that are needed to assist the PLHCP in making a recommendation. The employee must also receive a copy of the PLHCP's written recommendations.
A powered air-purifying respirator (PAPR) must be provided to an employee if information from the medical evaluation indicates that the employee can use a PAPR but not a negative pressure respirator. If, subsequent
to this evaluation, the PLHCP determines that the employee is able to wear a negative pressure respirator, the employer is no longer required to provide a PAPR to that employee.
In addition, the standard requires the employer to medically re-evaluate an employee when:
- That employee reports medical signs or symptoms that are related to the employee's ability to use a respirator;
- A PLHCP, supervisor, or the respirator program administrator observes that the employee is having a medical problem during respirator use and they inform the employer of their observation;
- Information from the respiratory protection program, including observations made during fit testing and program evaluation, indicates a need for employee re-evaluation; or
- A change occurs in workplace conditions (e.g., physical work effort, type of respirator used, protective clothing, temperature) that may result in a substantial increase in the physiological burden placed on an employee.
- FIT TESTING.
It has long been recognized that respirators must fit properly to provide protection. To obtain adequate respiratory protection, there must be a proper match between respirator and wearer. Respirators that don't seal properly around
the face offer only the illusion of protection. To accommodate the variability of face size characteristics among individuals, a number of manufacturers offer facepieces in several sizes and models.
- PURPOSE. The primary purpose of fit testing is to identify the specific make, model, style, and size of respirator best suited for each employee. In addition, fit testing also provides an opportunity to check on problems
with respirator wear, and reinforces respirator training by having wearers review the proper methods of donning and wearing the respirator.
- REQUIREMENT. Fit testing is required for all negative or positive pressure tight-fitting facepiece respirators. The OSHA respiratory protection standard requires that fit testing be performed before an employee first
starts wearing a respirator in the work environment, whenever a different respirator facepiece is used, and at least annually thereafter.
- METHOD. Prior to the actual fit test, the employee must be shown how to put on a respirator, position it on the face, set strap tension, and determine an acceptable fit. Next, the employee must be allowed to choose a
respirator from a sufficient number of models and sizes so that the employee can find an acceptable and correctly fitting respirator. Once an acceptable respirator has been found -- which takes into account the position of the
mask on the face, nose, and cheeks; room for eye protection; and room to talk -- a user seal check must be conducted (refer to on "Use of Respirators").
- TYPES OF FIT TESTING. Fit testing may either be qualitative (QLFT) or quantitative (QNFT), and must be administered using an OSHA-accepted QLFT or QNFT protocol. These protocols are described
in mandatory Appendix A to 1910.134. Prior to the commencement of the fit test, the employee must be given a description of the fit test and a description
of the exercises that he or she will be performing during fit testing. The respirator to be tested must be worn for at least five minutes before the start of the fit test. The employee must be fit tested with the same make,
model, style, and size of respirator that will be used in the workplace.
- Qualitative fit testing (QLFT). Qualitative fit testing involves the introduction of a gas, vapor, or aerosol test agent into an area around the head of the respirator user. A determination is then made as to
whether or not the wearer can detect the presence of the test agent through means such as odor, taste, or nasal irritation. If the presence of the test agent is detected inside the mask, the respirator fit is considered
to be inadequate.
There are four qualitative fit test protocols approved in OSHA's standard. The isoamyl acetate (IAA) test determines whether a respirator is protecting a user by questioning whether the user can smell the distinctive
odor of IAA. Both the saccharin and BitrexTM tests involve substances with distinctive tastes that should not be detected through an effective respirator. The irritant smoke (e.g., stannic chloride)
test involves a substance that elicits an involuntary irritation response in those exposed to it.
Before conducting a qualitative test, the worker must undergo a sensitivity test to determine if he or she can taste, smell or react to the substance. When performing the isoamyl acetate test, the protocol requires that
separate rooms be used for the odor screening and fit tests, and that the rooms be sufficiently ventilated to ensure that there is no detectable odor of IAA prior to a test being conducted. This will prevent olfactory
fatigue among workers being fit tested by preventing a buildup of IAA in the general room air.
- Quantitative fit testing (QNFT). In a quantitative fit test, the adequacy of respirator fit is assessed by numerically measuring the amount of leakage into the respirator. This testing can be done by either generating
a test aerosol as a test atmosphere, using ambient aerosol as the test agent, or using controlled negative pressure (CNP) to measure the volumetric leak rate. Appropriate instrumentation is required to quantify respirator
fit.
- FIT TEST EXERCISES. The following test exercises must be performed for all fit testing methods described in the OSHA standards, except the CNP method which has its own fit testing exercise regimen:
- Normal breathing in a normal standing position, without talking;
- Deep breathing in a normal standing position, breathing slowly and deeply, taking precaution not to hyperventilate;
- Turning the head slowly from side to side, while standing in place, with the employee holding his/her head momentarily at each extreme so that the employee can inhale at each side;
- Moving the head up and down slowly, while standing in place, inhaling in the up position when looking toward the ceiling;
- Talking out loud slowly, reading from a prepared text such as the Rainbow Passage (see Appendix A of the standard), counting backward from 100, or reciting a memorized poem or song;
- Grimacing by smiling or frowning (only for QNFT testing);
- Bending at the waist as if to touch toes (jogging in place can be done when the fit test enclosure doesn't permit bending at the waist); and
- Normal breathing (as described above).
Each test exercise must be performed for one minute, except for the grimace exercise which must be performed for 15 seconds. The respirator must not be adjusted once the fit test exercises begin. Any adjustment voids the test,
and the fit test must be repeated.
The employee must perform exercises in the test environment while wearing any applicable safety equipment that may be worn during actual respirator use and that could interfere with respirator fit. If the employee exhibits breathing
difficulty during the fit test, he or she must be referred to a physician or other licensed health care professional to determine whether the employee can wear a respirator while performing his or her duties.
- RETESTING. If the employee finds the fit of the respirator unacceptable, he or she must be given a reasonable opportunity to select a different respirator and to be retested. In addition, retesting is required whenever
an employee reports, or the employer, PLHCP, supervisor, or program administrator observe changes in an employee's physical condition that could affect respirator fit. Such conditions include, but are not limited to, facial
scarring, dental changes (e.g., wearing new dentures), cosmetic surgery, or an obvious change in body weight.
- USE OF RESPIRATORS.
- CONDITIONS. Once the respirator has been properly selected and fitted, it is necessary to ensure that the respirator is used properly in the workplace. The following conditions may compromise the effective use of the
respirator and jeopardize worker protection: facepiece seal leakage; removing the respirator at the wrong times in hazardous atmospheres; not properly performing user seal checks; or not properly repairing defective parts. In
these circumstances, there is the danger that employees may have a false sense of security in feeling that they are protected when they are not.
The employer must also be aware of the conditions in the work areas where employees are using respirators. Employers are required to routinely evaluate workplace conditions, the degree of employee exposure, and physical stress
so that they can provide additional or different respiratory protection when necessary. By observing respirator use under actual workplace conditions, employers can note problems such as changes in the fit of a respirator due
to the use of other protective equipment, or conditions leading to skin irritation.
- FACEPIECE SEAL PROTECTION.
- Seal of Tight-Fitting Respirators and Valve Function. The employer must not permit respirators with tight-fitting facepieces to be worn by employees who have conditions that would compromise the facepiece-to-face
seal. Examples of these conditions include facial hair that interferes with the facepiece seal or valve function, absence of normally worn dentures, facial deformities (e.g., scars, deep skin creases, prominent cheekbones),
or the use of jewelry or headgear that projects under the facepiece seal.
- Corrective Glasses or Goggles. Corrective glasses or goggles, or other personal protective equipment, must be worn in such a way that they do not interfere with the seal of the facepiece to the face. Since eye
glasses or goggles may interfere with the seal of half-facepieces, it is strongly recommended that full-facepiece respirators be worn where either corrective glasses or eye protection is required,
since corrective lenses can be mounted inside a full-facepiece respirator. In addition, the full-facepiece respirator may be more comfortable, and less cumbersome, than the combination of a half-mask and
chemical goggles. OSHA's current standard on respiratory protection, unlike the previous one, allows the use of contact lenses with respirators where the wearer has successfully worn such lenses before.
- User Seal Check. A user seal check (formerly known as a fit check) must be performed every time a tight-fitting respirator is put on or adjusted to ensure proper seating of the respirator to the face.
The user seal check conducted must be either the positive and/or negative pressure checks described in Appendix VIII:2-2 of this chapter,
or the manufacturer's recommended procedures (when equally protective). If the employee fails the user seal check test, another facepiece must be selected.
The employee must not have any hair growth (e.g., beard stubble, sideburns, or beard) that comes between the sealing surface of the respirator facepiece and the face, as well as hair that interferes with valve function,
or any other condition that might interfere with the face-to-facepiece seal such as jewelry or facial makeup. The user seal check must be used for all respirators on which such checks are possible. If a user seal check
cannot be performed on a tight-fitting respirator, the OSHA standard prohibits that respirator from being used.
- CONTINUING RESPIRATOR EFFECTIVENESS.
- Skin or Eye Irritation. Skin or eye irritation can result from wearing a respirator in hot, humid conditions, as well as in contaminated environments. Such irritation can be distressing to workers, causing them
to remove or adjust the respirator, or to refrain from wearing the respirator altogether. Therefore, to prevent skin or eye irritation associated with respirator use, employees must be permitted to leave the respirator
use area to wash their faces and respirator facepieces as needed.
- Filter, Canister, and Cartridge Elements for Air-Purifying Respirators. Whenever the respirator user can detect vapor or gas breakthrough (by odor, taste, and/or irritation effects), a change in breathing resistance
or leakage of the facepiece, the worker must be allowed to leave the respirator use area to replace the respirator or the filter, cartridge, or canister elements. Similarly, employees must be permitted to leave the respirator
use area if they are replacing cartridge or canister elements according to a change schedule, or when the end-of-service-life indicator shows that the canister or cartridge(s) must be changed.
- Repair, Disposal, and Replacement of Respirators. Since respirators must be in good working condition to function, it is imperative that they not be used if they have been impaired in any way. Impairments include
a broken strap, loss of respirator shape, and a face seal that can no longer be maintained. Therefore, respirators that are not properly functioning must be replaced, repaired, or discarded. The respirator manufacturers
can supply replacement parts for damaged parts on elastomeric respirators. Only when the respirator has been replaced or repaired can the employee return to the respirator use area.
- IMMEDIATELY DANGEROUS TO LIFE OR HEALTH (IDLH) ATMOSPHERES. Atmospheres are IDLH when they pose an immediate threat to life, would cause irreversible adverse health effects, or would interfere with an individual's ability
to escape from a dangerous atmosphere. Care must be exercised in these situations since failure of the respirator to provide the appropriate protection may result in serious injury or death. Consequently, the employer must develop
and implement specific procedures for the use of respirators in IDLH atmospheres that include the following provisions:
- At least one employee (referred to as the "standby employee") is to be located outside the IDLH atmosphere and maintain visual, voice, or signal line communication with the employee(s) in the IDLH atmosphere;
- The standby employee(s) located outside the IDLH atmosphere must be trained and equipped to provide effective emergency rescue;
- The employer or authorized designee is to be notified before the standby employees(s) enter the IDLH atmosphere to provide emergency rescue;
- The employer or authorized designee, once notified of such entry, must provide the necessary assistance appropriate to the situation;
- Standby employee(s) must be equipped with pressure demand or other positive pressure SCBA, or a pressure demand or other positive pressure supplied-air respirator with auxiliary SCBA; and
- Standby employee(s) must be equipped with appropriate retrieval equipment for lifting or removing the employee from the hazardous atmosphere, or, when such retrieval equipment cannot be used because it would increase
the overall risk resulting from entry, ensure that equivalent provisions for rescue have been made.
- INTERIOR STRUCTURAL FIREFIGHTING. In the ultra-hazardous situation of interior structural firefighting, firefighters must operate using a buddy system. Safeguards that may be adequate for well-controlled
and well-characterized IDLH situations are not adequate in the uncontrolled and unpredictable situation characterized by a burning building. Therefore, in addition to the above safeguards for IDLH atmospheres, the
following requirements apply to interior structural fire fighting:
- Two or more firefighters must always be sent in together and remain in visual or voice contact with one another at all times;
- At least two standby personnel are to be located outside the fire area; and
- All personnel engaged in interior structural firefighting must use SCBA.
The "two-in/two-out" requirement does not take effect until firefighters begin to perform interior structural fire fighting. While the fire is in the incipient stage (as determined by the commander or other person in charge),
or when emergency rescue operations are required before the entire team has assembled, the standard does not require two-member teams inside and outside the structure.
- MAINTENANCE AND CARE.
- REQUIREMENTS. The OSHA standard requires that employers provide each respirator user with a respirator that is clean, sanitary, and in good working order. These requirements are a vital part of any successful respiratory
protection program. To ensure that the respirator remains serviceable and delivers effective protection, a maintenance program must be in place prior to respirator use.
The OSHA respirator standard strongly emphasizes the importance of a good maintenance program, but permits its tailoring to the type of facilities, working conditions, and hazards involved. However, all programs are required
to include at least:
- Cleaning and disinfecting procedures;
- Proper storage;
- Regular inspections for defects (including leak check); and
- Repair methods.
In addition to the OSHA requirements, the manufacturer's instructions for inspection, cleaning, and maintenance of respirators should be consulted to ensure that the respirator continues to function properly. A proper maintenance
program ensures that the worker's respirator remains as effective as when it was new.
- CLEANING AND DISINFECTING.
- Cleaning and sanitizing respirators are necessary to prevent skin irritation, dermatitis, and to encourage worker acceptance. Where the contaminant is a dust, mist, or fume, build-up on the respirator face-to-facepiece
seal or within the respirator will reduce the protection provided by the respirator because the contaminant is in the breathing zone or has compromised the seal. In addition, the build-up of contamination
on the respirator can contribute to the deterioration of the respirator's materials, which can lead to reduced protection. Full facepieces must be cleaned to ensure that employees can see through the facepiece.
- Respirators that are issued for the exclusive use of an employee must be cleaned and disinfected as often as necessary to be maintained in a sanitary condition. Respirators used by more than one employee must be cleaned
and disinfected prior to being used by a different individual. Respirators maintained for emergency use as well as respirators used in fit testing and training, must be cleaned and disinfected after each use. The employer
must use either the OSHA cleaning and disinfecting procedures recommended in Appendix VIII:2-3 of this chapter or the procedures recommended
by the respirator manufacturer, as long as they are equivalent in effectiveness to the OSHA method.
- STORAGE.
- All respirators must be stored so that they are protected against damage, contamination, dust, sunlight, extreme temperatures, excessive moisture, and damaging chemicals. When respirators are packed or stored, the facepiece
and exhalation valve must be stored in a manner that will prevent deformation. Each respirator should be positioned so that it retains its natural configuration. Synthetic materials and even rubber will warp if stored
in an unnatural shape, thus affecting the fitting characteristics of the facepiece.
- Respirators intended for emergency use must be kept accessible to the work area, but not in an area that might itself be involved in the emergency because such an area may become contaminated or inaccessible. Emergency-use
respirators must be stored in compartments or covers that are clearly marked to indicate that they contain emergency respirators, and stored according to any applicable manufacturer instructions.
- INSPECTION. To ensure the continued reliability of respiratory equipment, it must be inspected on a regular basis. The frequency of inspection and the procedures to be followed depend on whether the respirator is intended
for non-emergency, emergency, or escape use only.
- The OSHA standard requires that all respirators used in non-emergency situations be inspected before each use and during cleaning. Respirators designated for use in an emergency situation are to be
inspected at least monthly and in accordance with the manufacturer's instructions, and checked for proper function before and after each use. Emergency escape-only respirators must be inspected before
being carried into the workplace.
- For all respirators, inspections must include a check of respirator function, tightness of connections, and the condition of the various parts including, but not limited to, the facepiece, head straps, valves, connecting
tube, and cartridges, canisters, or filters. In addition, the elastomeric parts must be evaluated for pliability and signs of deterioration.
- For SCBA's, which require monthly inspections, the air and oxygen cylinders must be maintained in a fully charged state and recharged when the pressure falls to 90% of the manufacturer's recommended pressure
level. In addition, the regulator and warning devices must be inspected to ensure that they function properly.
- For respirators that are maintained for use in emergencies, the OSHA standard requires certifying the respirator by documenting the date that the inspection was performed, the name or signature of the inspector, the
findings of the inspection, any required remedial action, and a serial number or other means of identifying the inspected respirator. This information must be provided on a tag or label that is attached to the storage
compartment for the respirator, is kept with the respirator, or is stored in the form of inspection reports (paper or electronic). The information must be maintained until it is replaced following a subsequent certification.
- REPAIR. Respirators that fail to pass inspection or are otherwise found to be defective, must be removed from service, and discarded, repaired, or adjusted. Repairs or adjustments to respirators must be done only by
appropriately trained personnel, using only the respirator manufacturer's NIOSH-approved parts designed for that respirator. The repairs also must be made in accordance with the manufacturer's recommendations and
specifications regarding the type and extent of repairs to be performed. Because components such as reducing and admission valves, regulators, and alarms are complex and essential to the safe functioning of the respirator, they
are required to be adjusted and repaired only by the manufacturer or a technician trained by the manufacturer.
- BREATHING AIR QUALITY AND USE.
- STANDARDS AND SPECIFICATIONS.
- Breathing air for atmosphere-supplying respirators must be of high purity, meet quality levels for content, and not exceed certain contaminant levels and moisture requirements. Compressed air, compressed oxygen, liquid
air, and liquid oxygen used for respiration must be in accordance with the following requirements:
- Compressed and liquid oxygen must meet the United States Pharmacopoeia for medical or breathing oxygen.
- Compressed breathing air must meet at least the requirements for Grade D breathing air as described in the ANSI/Compressed Gas Association Commodity Specification for Air, G-7.1-1989.
- Compressed oxygen must not be used in atmosphere-supplying respirators, including open circuit SCBA's, that have previously used compressed air. This prohibition is intended to prevent fires and explosions that could
result if high-pressure oxygen comes into contact with oil or grease that has been introduced to the respirator or the air lines during compressed-air operations. In addition, oxygen in concentrations greater
than 23.5% can only be used in equipment designed for oxygen service or distribution.
- Breathing air may be supplied to respirators from cylinders or air compressors. Where cylinders are used, they must be tested and maintained as prescribed in the Shipping Container Specification Regulations of the Department
of Transportation (49 CFR parts 173 and 178). Cylinders of purchased breathing air must have a certificate of analysis from the supplier stating that the air meets the requirements for Grade D breathing air. The moisture
content of the compressed air in the cylinder cannot exceed a dew point of -50°F (-45.6°C) at 1 atmosphere pressure. This requirement will prevent respirator valves from freezing,
which can occur when excess moisture accumulates on the valves. All breathing gas containers must be marked in accordance with the NIOSH respirator certification standard, 42 CFR part 84.
- OTHER SPECIFIC REQUIREMENTS.
- Where compressors are used for supplying air, the compressor must be constructed and situated so contaminated air cannot enter the air-supply system. The location of the air intake is very important, and
must be in an uncontaminated area where exhaust gases from nearby vehicles, the internal combustion engine that is powering the compressor itself (if applicable), or other exhaust gases being ventilated from the plant
will not be picked up by the compressor air intake.
- In addition, compressors must be equipped with suitable in-line, air-purifying sorbent beds and filters to further ensure breathing air quality, and to minimize moisture content so that the
dew point at 1 atmosphere pressure is 10°F (5.56°C) below the ambient temperature. Sorbent beds and filters must be maintained and replaced or refurbished periodically according to the manufacturer's recommendations,
and a tag must be kept at the compressor indicating the most recent change date and the signature of the person authorized by the employer to perform the change.
- For compressors that are not oil-lubricated, the employer must ensure that carbon monoxide levels do not exceed 10 ppm. This requirement can be met by several different methods, including the use of continuous carbon
monoxide alarms, carbon monoxide sorbent materials, proper air intake location in an area free of contaminants, frequent monitoring of air quality, or the use of high-temperature alarms and automatic shutoff
devices, as appropriate. Employers have flexibility in selecting the method(s) most appropriate for conditions in their workplace. Since no single method will be appropriate in all situations, several methods may be
needed. For example, it may be necessary to combine the use of a carbon monoxide alarm with a carbon monoxide sorbent bed where conditions are such that a reliable carbon monoxide-free area for air intake
cannot be found.
- Oil-lubricated compressors can produce carbon monoxide if the oil enters the combustion chamber and is ignited. This problem can be particularly severe in older compressors with worn piston rings and cylinders. Consequently,
if an oil-lubricated compressor is used, it must have a high-temperature or carbon monoxide alarm, or both, to monitor carbon monoxide levels. If only a high-temperature alarm is used, the air
from the compressor must be tested for carbon monoxide at intervals sufficient to prevent carbon monoxide in the breathing air from exceeding 10 ppm.
- Breathing air couplings must be incompatible with outlets for non-respirable plant air or other gas systems to prevent accidental servicing of air line respirators with non-respirable gases or oxygen. Also, no asphyxiating
substance must be allowed in the breathing air lines.
- PROGRAM LOGISTICS.
- IDENTIFICATION OF FILTERS, CARTRIDGES, AND CANISTERS. The employer must ensure that all filters, cartridges, and canisters used in the workplace are labeled and color coded with the NIOSH approval label, and ensure that
the label is not removed and remains legible.
- TRAINING AND INFORMATION.
- Employee training is an important part of the respiratory protection program and is essential for correct respirator use. The OSHA respiratory protection standard requires employers to provide training before the employee
uses a respirator in the workplace. For the training to be effective, the training information must be comprehensive and presented in an understandable way.
- Employers should develop training programs based upon the employees' educational level and language background. Such an approach will ensure that all employees receive training that enables them to maximize the effectiveness
of the respirators they use. As a result of this training, the employee will be able to understand the operation of the respirator and demonstrate the ability to properly use the respirator.
- Employee training must include a discussion of why the use of the respirator is necessary. Such training would address the identification of the hazards involved, the extent of employee exposures to those hazards, and
the potential health effects of such exposures.
- Information regarding the consequences of improper fit, usage, or maintenance on respirator effectiveness must also be provided to employees. Inadequate attention to any of these program elements would obviously defeat
the effectiveness of the respirator. Proper fit, usage, and maintenance of respirators are critical to ensure employee protection.
- Employees must also be provided with an explanation of the limitations and capabilities of the respirator selected for employee use. A discussion of the limitations and capabilities of the respirator must address how
the respirator operates. This training would include, for example, an explanation of how the respirator provides protection by either filtering the air, absorbing the vapor or gas, or providing clean air from an uncontaminated
source. Where appropriate, it should include limitations on the use of the equipment, such as prohibitions against using an air-purifying respirator in IDLH atmospheres and an explanation of why such a respirator
should not be used in these situations.
- Employees must also know how to use the respirator effectively in emergency situations, including those in which the respirator malfunctions. Comprehensive training is necessary where respirators are used in IDLH situations,
including oxygen-deficient atmospheres such as those that occur in fire fighting, rescue operations, and confined-area entry.
- Training must include the procedures for inspecting the respirator, donning and removing it, checking the fit and respirator seal, and actually wearing the respirator. Employees must also be capable of recognizing any
problems that may threaten the continued protective capability of the respirator. The training must include the steps employees are to follow if they discover any problems during inspection, that is, who the problems
are to be reported to and where they can obtain replacement equipment if necessary.
- Instructions must be given to respirator users regarding the proper procedures for maintenance and storage of respirators. The extent of training may vary according to workplace conditions. In some cases, where employees
are responsible for performing some or all respirator maintenance and for storing respirators while not in use, detailed training in maintenance and storage procedures may be necessary. In other facilities, where specific
personnel or central repair facilities are assigned to perform these tasks, most employees may need to be informed only of the maintenance and storage procedures without having to learn detailed technical information.
By providing this training, respirator users will be able to identify respirator deficiencies that can result from improper maintenance and storage of respirators so that they will not use improperly functioning respirators.
- The training program must also provide employees with medical information that is sufficient for them to recognize the signs and symptoms of medical conditions (e.g., shortness of breath, dizziness) that may limit or
prevent the effective use of respirators. Employee knowledge of this information is important to ensure implementation of a successful respirator program.
- In addition to specific training requirements regarding the proper use of respirators, employees must be informed of the general requirements of the OSHA respiratory protection standard. This discussion could simply
inform employees that employers are obligated to develop a written program, properly select respirators, evaluate respirator use and correct deficiencies in use, conduct medical evaluations, provide for the maintenance,
storage, and cleaning of respirators, and retain and provide access to specific records. Thus, employees will know in general what the employer's obligations are under the standard with respect to employee protection.
- At a minimum, annual training is required by the OSHA respiratory protection standard. With few exceptions, a new employee must be provided with respirator training prior to using a respirator in the workplace. OSHA
believes that annual training is necessary and appropriate to ensure that employees know about the respiratory protection program and that they cooperate and actively participate in the program. Training and interaction
with respirator instructors on at least an annual basis reinforces employee knowledge about the correct use of respirators and other pertinent elements of the respiratory protection program. It also builds employee confidence
when using respirators.
- Under some conditions, additional training will be required to supplement the annual training. Circumstances which require additional training include situations where changes in the workplace (e.g., process changes,
increase in exposure, emergence of new hazards) or the type of respirator used by the employee render previous training obsolete. Additional training is also required when the employee has not retained the requisite
understanding or skill to use the respirator properly, or when any other situation arises in which retraining appears necessary.
- PROGRAM EVALUATION.
- The employer must conduct evaluations of the workplace as necessary to ensure that the provisions of the current written respirator program are being properly implemented for all employees required to use respirators.
In addition, evaluations must be conducted to ensure the continued effectiveness of the program. Evaluations of the workplace will determine whether the correct respirators are being used and worn properly, and will
also serve to determine whether the training program is effective.
- The employer must regularly consult with employees wearing respirators to ascertain the employees' views on program effectiveness and to identify any problems. This assessment must determine if the respirators are properly
fitted. It must also evaluate whether: employees are able to wear the respirators without interfering with effective workplace performance; respirators are correctly selected for the hazards encountered; respirators
are being worn when necessary; and respirators are being maintained properly. The employer must correct any problems associated with wearing a respirator that are identified by employees, or that are revealed during
any other part of this evaluation.
- RECORDKEEPING. The OSHA respiratory protection standard requires the employer to establish and retain written information regarding medical evaluations, fit testing, and the respirator program. This information will
promote employee involvement in the respirator program, assist the employer in auditing the adequacy of the program, and provide a record for compliance determinations by OSHA.
- The employer must retain a medical evaluation record for each employee subject to medical evaluation. This record is to include the result of the medical questionnaire and, if applicable, a copy of the PLHCP's written
opinion and recommendations, including the results of relevant medical examinations and tests. Records of medical evaluations must be retained and made available as required by 29 CFR 1910.1020,
OSHA's Access to Employee Exposure and Medical Records rule.
- Fit test records must be retained for respirator users until the next fit test is administered. These records consist of:
- Name or identification of the employee tested;
- Type of fit test performed (QLFT, QNFT -- irritant smoke, saccharin, etc.);
- Make, model, and size of the respirator fitted;
- Date of the fit test;
- Pass/fail results if a QLFT is used; or
- Fit factor and strip chart recording or other record of the test results if quantitative fit testing was performed.
- If the employee's use of a respirator is discontinued (e.g., because of a change of duties or successful implementation of engineering controls), fit test records need not be retained for the employee. Fit test records
must be maintained to determine whether annual fit testing has been done, and whether the employee who was tested passed the QLFT, or passed the QNFT with a fit factor that was appropriate for the type of respirator
being used.
- All written materials required to be maintained under the recordkeeping requirements must be made available, upon request, to the employee who is subject of the records and to the Assistant Secretary for OSHA or designee
for examination and copying.
- NIOSH GUIDELINES FOR THE SELECTION AND USE OF PARTICULATE RESPIRATORS. In June 1995, NIOSH updated and modernized the Federal Regulation for certifying air-purifying particulate respirators [42 CFR part 84].
As a consequence of this new regulation, NIOSH developed a User's Guide to familiarize respirator users with the new Part 84 certification regulations for particulate respirators, and to provide guidance for the selection and
use of the new particulate respirators. The new regulation became effective on July 10, 1995, and replaces 30 CFR part 11 under which NIOSH and the Mine Safety and Health Administration (MSHA) jointly certified respirators before
that date. The respirators certified under this new regulation are tested under much more demanding conditions than under the old regulation to provide increased worker protection. See Appendix
VIII:2-4 of this chapter for a summary of the NIOSH Guide to the Selection and Use of Particulate Respirators Certified Under 42 CFR 84.
APPENDIX VIII: 2-1. GLOSSARY.
Air-purifying respirator a respirator with an air-purifying filter, cartridge, or canister that removes specific air contaminants by passing ambient air through the air-purifying element.
Assigned protection factor (APF) [reserved]
Atmosphere-supplying respirator a respirator that supplies the respirator user with breathing air from a source independent of the ambient atmosphere, and includes supplied-air respirators (SAR's) and self-contained
breathing apparatus (SCBA) units.
Canister or cartridge a container with a filter, sorbent, or catalyst, or a combination of these items, that removes specific contaminants from the air passed through the container.
Demand respirator an atmosphere-supplying respirator that admits breathing air to the facepiece only when a negative pressure is created inside the facepiece by inhalation.
Emergency situation any occurrence such as, but not limited to, equipment failure, rupture of containers, or failure of control equipment that may or does result in an uncontrolled substantial release of an airborne contaminant.
Employee exposure an exposure to a concentration of an airborne contaminant that would occur if the employee were not using respiratory protection.
End-of-service-life indicator (ESLI) a system that warns the respirator user of the approach of the end of adequate respiratory protection; for example, that the sorbent is approaching saturation or is no longer effective.
Escape-only respirator a respirator intended to be used only for emergency exit.
Filtering facepiece (dust mask) a negative pressure particulate respirator with a filter as an integral part of the facepiece or with the entire facepiece composed of the filtering medium.
Filter or air purifying element a component used in respirators to remove solid or liquid aerosols from the inspired air.
Fit factor a quantitative estimate of the fit of a particular respirator to a specific individual, and typically estimates the ratio of the concentration of a substance in ambient air to its concentration inside the respirator
when worn.
Fit test the use of a protocol to qualitatively or quantitatively evaluate the fit of a respirator on an individual. See also "Qualitative fit test (QLFT)" and "Quantitative fit test (QNFT)."
Helmet a rigid respiratory inlet covering that also provides head protection against impact and penetration.
High efficiency particulate air (HEPA) filter a filter that is at least 99.97% efficient in removing monodisperse particles of 0.3 micrometers in diameter and larger. The equivalent NIOSH 42 CFR part 84 particulate filters are
the N100, R100, and P100 filters.
Hood a respiratory inlet covering that completely covers the head and neck, and may also cover portions of the shoulders and torso.
Immediately dangerous to life or health (IDLH) an atmosphere that poses an immediate threat to life, would cause irreversible adverse health effects, or would impair an individual's ability to escape from a dangerous atmosphere.
Interior structural firefighting the physical activity of fire suppression, rescue or both, inside of buildings or enclosed structures that are involved in a fire situation beyond the incipient stage.
Loose-fitting facepiece a respiratory inlet covering that is designed to form a partial seal with the face.
Maximum use concentration (MUC) [reserved]
Negative pressure respirator (tight fitting) a respirator in which the air pressure inside the facepiece is negative during inhalation with respect to the ambient air pressure outside the respirator.
Oxygen deficient atmosphere an atmosphere with an oxygen content below 19.5% by volume.
Physician or other licensed health care professional (PLHCP) an individual whose legally permitted scope of practice (i.e., license, registration, or certification) allows him or her to independently provide, or be delegated the
responsibility to provide, some or all of the health care services required by 29 CFR 1910.134(e), "Medical evaluation."
Positive-pressure a respirator in which the pressure inside the respiratory inlet covering exceeds the ambient air pressure outside the respirator.
Powered air-purifying respirator (PAPR) an air-purifying respirator that uses a blower to force the ambient air through air-purifying elements to the inlet covering.
Pressure demand respirator a positive pressure atmosphere-supplying respirator that admits breathing air to the facepiece when the positive pressure is reduced inside the facepiece by inhalation.
Qualitative fit test (QLFT) a pass/fail fit test to assess the adequacy of respiratory fit that relies on the individual's response to the test agent.
Quantitative fit test (QNFT) an assessment of the adequacy of respirator fit by numerically measuring the amount of leakage into the respirator.
Respiratory inlet covering the portion of a respirator that forms the protective barrier between the user's respiratory tract and an air-purifying device or breathing air source, or both. It may be a facepiece, helmet,
hood, suit, or a mouthpiece respirator with nose clamp.
Self-contained breathing apparatus (SCBA) an atmosphere-supplying respirator for which the breathing air source is designed to be carried by the user.
Service life the period of time that a respirator, filter or sorbent, or other respiratory equipment provides adequate protection to the wearer.
Supplied-air respirator (SAR) or airline respirator an atmosphere-supplying respirator for which the source of breathing air is not designed to be carried by the user.
Tight-fitting facepiece a respiratory inlet covering that forms a complete seal with the face.
User seal check an action conducted by the respirator user to determine if the respirator is properly seated to the face.
APPENDIX VIII:2-2. USER SEAL CHECK.
A. Facepiece Positive and/or Negative Pressure Checks
Positive Pressure Check
Close off the exhalation valve and exhale gently into the facepiece. The face fit is considered satisfactory if a slight positive pressure can be built up inside the facepiece without any evidence of outward leakage of air at the seal. For
most respirators, this method of leak testing requires the wearer to first remove the exhalation valve cover before closing off the exhalation valve, and then carefully replacing it after the test.
Negative Pressure Check
Close off the inlet opening of the canister or cartridge(s) by covering it with the palm of the hand(s) or by replacing the filter seal(s). Inhale gently so that the facepiece collapses slightly, and hold your breath for ten seconds. The design
of the inlet opening of some cartridges cannot be effectively covered with the palm of the hand, which requires that the test be performed by covering the inlet opening of the cartridge with a thin latex or nitrile glove. If the facepiece remains
in its slightly collapsed condition, and no inward leakage of air is detected, the tightness of the respirator is considered satisfactory.
B. Manufacturer's Recommended User Seal Check Procedures
The respirator manufacturer's recommended procedures for performing a user seal check may be used instead of the positive and/or negative pressure check procedures, provided that the employer demonstrates that the manufacturer's procedures
are equally effective in detecting seal leakage compared to the positive pressure and negative pressure checks described above.
APPENDIX VIII:2-3. RECOMMENDED PROCEDURES FOR CLEANING RESPIRATORS.
These procedures are provided for employer use when cleaning respirators. They are general in nature, and the employer, as an alternative, may use the cleaning recommendations provided by the manufacturer of the respirators used by their employees,
provided such procedures are as effective as those listed here. Equivalent effectiveness simply means that the procedures used must accomplish the objectives set forth in this Appendix (i.e., must ensure that the respirator is properly cleaned
and disinfected in a manner that prevents damage to the respirator and does not cause harm to the user).
- Remove filters, cartridges, or canisters. Disassemble facepieces by removing speaking diaphragms, demand or pressure-demand valve assemblies, hoses, or any components recommended by the manufacturer. Discard or repair any defective
parts.
- Wash components in warm (43°C/110°F maximum) water with a mild detergent or with a cleaner recommended by the manufacturer. A stiff bristle (not wire) brush may be used to facilitate the removal of dirt.
- Rinse components thoroughly in clean, warm (43°C/110°F maximum), preferably running, water. Drain the components.
- When the cleaner used does not contain a disinfecting agent, respirator components should be immersed for two minutes in:
- Hypochlorite solution (50 ppm of chlorine) made by adding approximately one milliliter of laundry bleach to one liter of water at 43°C/110°F; or
- Aqueous solution of iodine (50 ppm iodine) made by adding approximately 0.8 milliliters of tincture of iodine (6-8 grams ammonium and/or potassium iodine/100 cc of 45% alcohol) to one liter of water at 43°C/110°F;
or
- Other commercially available cleansers of equivalent disinfectant quality when used as directed, if their use is recommended or approved by the respirator manufacturer.
- Rinse components thoroughly in clean, warm (43°C/110°F maximum), preferably running, water. Drain the components. The importance of thorough rinsing cannot be overemphasized. Detergents or disinfectants that dry on facepieces
may result in dermatitis. In addition, some disinfectants may cause deterioration of rubber or corrosion of metal parts if not completely removed.
- Components should be hand-dried with a clean, lint-free cloth, or air-dried.
- Reassemble facepiece, replacing filters, cartridges, and canisters where necessary.
- Test the respirator to ensure that all components work properly.
APPENDIX VIII:2-4. NIOSH GUIDE TO THE SELECTION AND USE OF PARTICULATE RESPIRATORS CERTIFIED UNDER 42 CFR 84.
Summary for Respirator Users
This summary presents a brief overview of what the respirator user needs to know about the new categories of particulate respirators certified by the National Institute for Occupational Safety and Health (NIOSH).
NIOSH has developed a new set of regulations in 42 CFR 84 (also referred to as "Part 84") for testing and certifying nonpowered, air-purifying, particulate-filter respirators. The new Part 84 respirators have passed
a more demanding certification test than the old respirators (e.g., dust and mist [DM], dust, fume and mist [DFM], spray paint, pesticide, etc.) certified under 30 CFR 11 (also referred to as "Part 11").
Changes in the new regulations involve only nonpowered, air-purifying, particulate-filter respirators. Certification requirements for all other classes of respirators (e.g., chemical cartridges, self-contained breathing
apparatus [SCBA], airlines, gas masks without a particulate filter, powered air-purifying respirators [PAPR's] equipped with high-particulate air [HEPA] filters, etc.) have been transferred to Part 84 without change.
Until further notice, the Occupational Safety and Health Administration (OSHA) is allowing the continued use of Part 11 particulate-filter respirators. Under Part 84, NIOSH is allowing manufacturers to continue selling and shipping Part 11
particulate filters as NIOSH-certified until July 10, 1998.
The new Part 84 regulation provides for nine classes of filters (three levels of filter efficiency, each with three categories of resistance to filter efficiency degradation). The three levels of filter efficiency are 95%, 99%, and 99.97%.
The three categories of resistance to filter efficiency degradation are labeled N, R, and P. The class of filter will be clearly marked on the filter, filter package, or respirator box. For example, a filter marked N95 would mean an N-series
filter that is at least 95% efficient. Chemical cartridges that include particulate filter elements will carry a similar marking that pertains only to the particulate filter element.
Filter efficiency is the stated percentage of particles removed from the air. Filter efficiency degradation is defined as a lowering of filter efficiency or a reduction in the ability of the filter to remove particles as a result of workplace
exposure.
The new classes of nonpowered particulate respirators require new decision logic for selection of the proper respirator. The selection process for using the new particulate classification is outlined as follows and is discussed in Section II
of NIOSH Guide to the Selection and Use of Particulate Respirators Certified Under 42 CFR 84:
1. The selection of N-, R-, and P-series filters depends on the presence or absence of oil particles, as follows:
- If no oil particles are present in the work environment, use a filter of any series (i.e., N-, R-, or P-series).
- If oil particles (e.g., lubricants, cutting fluids, glycerine, etc.) are present, use an R-or P-series filter.
Note: N-series filters cannot be used if oil particles are present.
- If oil particles are present and the filter is to be used for more than work shift, use only a P-series filter.
Note: To help you remember the filter series, use the following guide:
N for Not resistant to oil
R for Resistant to oil
P for oil-Proof
2. Selection of filter efficiency (i.e., 95%, 99%, or 99.97%) depends on how much filter leakage can be accepted. Higher filter efficiency means lower filter leakage.
3. The choice of facepiece depends on the level of protection needed -- that is, the assigned protection factor (APF) needed.
Call 1-800-35-NIOSH (1-800-356-4674) for additional information or for free single copies of the complete document NIOSH Guide to the Selection and Use of Particulate Respirators Certified Under 42 CFR 84 [DHHS (NIOSH) Publication
No. 96-101].
NIOSH is the National Institute for Occupational Safety and Health, Centers for Disease Control and Prevention, Public Health Service, U.S. Department of Health and Human Services.
|