<<< Back to Sampling and Analytical Methods |
Printing Instructions |
For problems with accessibility in using figures, illustrations and PDFs in this method, please contact
the SLTC at (801) 233-4900. These procedures were designed and tested for internal use by OSHA personnel.
Mention of any company name or commercial product does not constitute endorsement by OSHA. |
Sulfur Dioxide
[236 KB PDF,
23 pages]
Related Information: Chemical Sampling -
Sulfur Dioxide
|
Method no.: |
1011 |
|
|
Control no.: |
T-1011-FV-01-0711-M |
|
|
Target concentration: |
5 ppm (13 mg/m3) |
|
|
OSHA General Industry PEL:
OSHA Construction PEL:
OSHA Maritime PEL:
ACGIH TLV: |
5 ppm (13 mg/m3)
5 ppm (13 mg/m3)
5 ppm (13 mg/m3)
2 ppm (5.2 mg/m3) (TWA); 5 ppm (13 mg/m3) (STEL)
|
|
|
Procedure: |
Samples are collected by
drawing workplace air through active samplers containing sodium carbonate
coated filters connected to personal sampling pumps. During sampling sulfur
dioxide reacts with sodium carbonate forming sodium sulfite. Sulfite is
subsequently extracted from the filter in the laboratory and oxidized to
sulfate using hydrogen peroxide and analyzed by ion chromatography using a
conductivity detector. |
|
|
Recommended
sampling
parameters: |
240 min at 0.05 L/min (12 L) (TWA)
15 min at 0.5 L/min (7.5 L) |
|
|
Reliable
quantitation limit: |
0.045 ppm (0.118 mg/m3) (TWA)
0.058 ppm (0.152 mg/m3) (15 min sampling time) |
|
|
Standard error of estimate
at the target concentration: |
5.1% |
|
|
Status of method: |
Evaluated method. This method
has been subjected to the established evaluation procedures of the Methods
Development Team. |
|
|
November 2007 |
Michael K.
Simmons |
|
|
Methods Development Team
Industrial Hygiene Chemistry Division
OSHA Salt Lake Technical Center
Sandy UT 84070-6406 |
1. General Discussion
For assistance with accessibility problems in using figures and illustrations presented in this method, please contact the Salt Lake Technical Center (SLTC) at (801) 233-4900. These procedures were
designed and tested for internal use by OSHA personnel. Mention of any company name or commercial product does not constitute endorsement by OSHA.
1.1 Background
1.1.1 History
Originally, the Occupational Safety and Health Administration (OSHA) used a midget impinger containing a 0.3 N hydrogen peroxide solution to collect sulfur dioxide (SO2).1 Sulfur dioxide reacts with
the hydrogen peroxide during sampling, converting the sulfur dioxide to sulfuric acid. Initially the sulfuric acid was analyzed by volumetric titration using barium perchlorate and a thorin
indicator. In 1981 OSHA began analyzing the sulfuric acid by ion chromatography with a conductivity detector.2
Originally, the Occupational Safety and Health Administration (OSHA) used a midget impinger containing a 0.3 N hydrogen peroxide solution to collect sulfur dioxide (SO2) . Sulfur dioxide reacts with
the hydrogen peroxide during sampling, converting the sulfur dioxide to sulfuric acid. Initially the sulfuric acid was analyzed by volumetric titration using barium perchlorate and a thorin
indicator. In 1981 OSHA began analyzing the sulfuric acid by ion chromatography with a conductivity detector.
Due to the inconvenience and safety issues associated with impinger sampling, OSHA next developed in 1992 a solid-sorbent method for sampling sulfur dioxide (OSHA ID-200).3 ID-200 specifies a
sampling tube containing impregnated activated beaded carbon to collect sulfur dioxide. Sulfur dioxide is oxidized to sulfite on the medium and then slowly oxidizes further to sulfate. Samples
are extracted using a solution of 15 mM sodium hydroxide and 0.3 N hydrogen peroxide to complete oxidation of any remaining sulfite. Sample extracts are analyzed by ion chromatography with a
conductivity detector. Disadvantages of ID-200 include mass-dependent and possibly lot-dependent extraction efficiency. Also, if present, hydrogen sulfide (H2S) will collect on the sampler resulting
in a positive interference. This new method uses the sampler developed for the collection of hydrogen
sulfide, described in OSHA Method 10084 and shown in Figure 1.1.1, for the
collection of sulfur dioxide. Because sulfur dioxide collects on the silver
nitrate coated silica gel used to collect hydrogen sulfide, resulting in a
positive interference for hydrogen sulfide, it was necessary to remove any
sulfur dioxide from the sampled air.
|
|
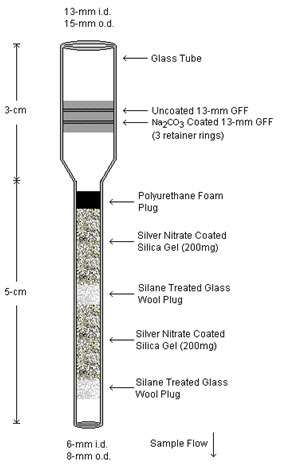
Figure 1.1.1. H2S / SO2 sampler. |
Removal of sulfur dioxide was accomplished using a sodium carbonate coated glass fiber depth filter (GFF). The use of sodium carbonate coated filters to collect sulfur dioxide
is also described in NIOSH Method 6004.5
The original preparation of the sodium carbonate coated filter described in Appendix A of Method 1008 has been slightly modified and is described in Appendix A of this method. The modification
consists of washing the GFF and using a higher grade of reagents to coat the filter to reduce the background of sulfate.
During sampling sulfur dioxide reacts with sodium carbonate to form sulfite which then slowly oxidizes further to sulfate. Sulfite and sulfate are extracted with a weak basic solution and hydrogen
peroxide to complete oxidation of any remaining sulfite. Sample extracts are analyzed for sulfate using an ion chromatograph with a conductivity detector. This method does not have a mass-dependent
extraction efficiency or have any interference from hydrogen sulfide.
The GFF prefilter used is slightly alkaline and will adsorb up to 1.6 µg of sulfur dioxide when sampling at 80% humidity. This would be equivalent to 1% of the sulfur dioxide collected at the target
concentration for a 240 min sample. See Section 4.9 for more information.
1.1.2 Toxic effects (This section is for information only and should not be taken as the basis of OSHA policy.)6
"Sulfur dioxide causes irritation of the mucous membranes, which probably results from the action of sulfurous acid formed when the highly soluble gas dissolves. Short term exposure causes
bronchoconstriction measurable as an increase in flow-resistance. The magnitude of the response is concentration-related."
Exposure to sulfur dioxide at 1 ppm for even short periods of time may result in a pulmonary response and increased expiratory flow-resistance. Exposure to 5 ppm will increase the possibility of
flow-resistance and decrease the flow of nasal mucous. Long term exposure to sulfur dioxide at concentrations greater than 1 ppm can result in reduced pulmonary function and chronic respiratory
disease.
Sulfur dioxide is not classified as a carcinogen, however there is evidence suggesting "that it may act as a promoter".
1.1.3 Workplace exposure7
"Sulfur dioxide is used in treating wood pulp for paper manufacturing; in ore and metal refining; extraction of lubricating oils; as a bleaching, disinfecting, and fumigating agent; as a
food additive and preservative; and as a reducing agent." Sulfur dioxide is also a "deleterious air pollutant, especially in the vicinity of smelters and electrical power plants burning
soft coal or high sulphur oil".
1.1.4 Physical properties and other descriptive information8,9
synonyms: |
sulfurous anhydride; sulfurous oxide |
IMIS:10 |
2290 |
CAS number: |
7446-09-5 |
boiling point: |
-10 oC (14 oF) |
melting point: |
-72 oC (-97.6 oF) |
molecular weight: |
64.065 |
vapor pressure: |
2538 mm at 21.1 °C |
appearance: |
colorless gas |
vapor density: |
2.264 at 0 °C (air = 1.0) |
molecular formula: |
SO2 |
odor: |
strong suffocating pungent order |
solubility: |
soluble in alcohol and water |
structural formula: |
 |
This method was evaluated according to the OSHA SLTC "Evaluation Guidelines for Air Sampling Methods Utilizing Chromatographic Analysis".11 The Guidelines define analytical parameters, specify
required laboratory tests, statistical calculations and acceptance criteria. The analyte air concentrations throughout this method are based on the recommended sampling and analytical parameters.
Air concentrations in ppm are referenced to 25 °C and 101.3 kPa (760 mmHg).
1.2 Limit defining parameters
1.2.1 Detection limit of the analytical procedure
The detection limit of the analytical procedure is 0.33 ng sulfur dioxide (0.50 ng sulfate). This is the amount of sulfate that will give a detector response that is significantly different from the
response of a calibration blank. (Section 4.1)
1.2.2 Detection limit of the overall procedure
The detection limit of the overall procedure is 0.42 µg sulfur dioxide per sample (0.013 ppm or 0.035 mg/m3). This is the amount spiked onto the sampler that will give a detector response that is
significantly different from the response of a sampler blank. (Section 4.2)
1.2.3 Reliable quantitation limit
The reliable quantitation limit is 1.41 µg sulfur dioxide per sample (0.045 ppm or 0.118 mg/m3). This is the amount spiked onto the sampler that will give a detector response that is considered the
lower limit for precise quantitative measurements. (Section 4.2)
1.2.4 Instrument calibration
The standard error of estimate is 2.33 μg/mL sulfate over the range of 5.9 μg/mL to 47 μg/mL. This range corresponds to approximately 0.25 to 2 times the target concentration. (Section 4.3)
1.2.5 Precision
The precision of the overall procedure at the 95% confidence level for the ambient temperature 16-day storage test (at the target concentration) is ± 9.96%. This includes an additional 5% for
sampling pump variability. (Section 4.4)
1.2.6 Recovery
The recovery of sulfur dioxide from samples used in a 16-day storage test remained above 101.2% when the samples were stored at ambient temperature. (Section 4.5)
1.2.7 Reproducibility
Six samples collected from a controlled test atmosphere were submitted for analysis by the OSHA Salt Lake Technical Center. The samples were analyzed according to a draft copy of this procedure after
9 days of storage at ambient temperature. No individual sample result deviated from its theoretical value by more than the precision reported in Section 1.2.5. (Section 4.6)
2. Sampling Procedure
All safety practices that apply to the work area being sampled should be followed. The sampling equipment should be attached to the worker in such a manner that it will not interfere with work
performance or safety.
2.1 Apparatus
Samples are collected using the sampler described in Appendix A of OSHA Methods 1008 and 1011 and shown in Figure 1.1.1. The 8-cm long glass sampling tube consisting of a 3-cm × 13-mm i.d. × 15-mm o.d
section containing a 13-mm uncoated GFF and a 13-mm sodium carbonated coated GFF followed by a 5-cm × 6-mm i.d. × 8-mm o.d. section consisting of two sections of silver nitrate coated silica gel.
For this evaluation samplers were prepared in-house, however, samplers are also available for purchase through SKC, Inc. (cat. no. 226-177).
Samples are collected using a personal sampling pump calibrated, with the sampling device attached, to within ±5% of the recommended flow rate.
2.2 Reagents
None required
2.3 Technique
All samplers should be from the same lot.
Attach the sampler to the sampling pump with flexible tubing so that the sampler is in an approximately vertical position with the inlet (large end) facing down in the worker’s breathing zone during
sampling. Position the sampling pump, sampler and tubing so they do not impede work performance or safety.
Draw air directly into the inlet of the sampler. The air being sampled should not pass through any hose or tubing before entering the sampler.
After sampling for the appropriate time, remove the sample and seal it with plastic end caps. Seal each sample end-to end with a Form OSHA-21.
Submit at least one blank sample with each set of samples. Handle the blank sample in the same manner as the other samples except draw no air through it.
Record sample air volume (L), sampling time (min) and sampling rate (L/min) for each sample, along with any potential interferences on the Form OSHA-91A.
Submit the samples to the laboratory for analysis as soon as possible after sampling. If a delay is unavoidable, store the samples in a refrigerator. Ship any bulk samples separate from the air
samples.
2.4 Sampler capacity (Section 4.7)
The sampling capacity of the sampler was tested by sampling a dynamically generated test atmosphere of sulfur dioxide (57.9 mg/m3 or 22.1 ppm) with an average relative humidity of 78% at 23 °C.
The samples were collected at a sampling rate of approximately 0.05 L/min for 480 min. No breakthrough was observed.
2.5 Extraction efficiency (Section 4.8)
It is the responsibility of each analytical laboratory to determine the extraction efficiency because the adsorbent material, reagents and laboratory techniques may be different than those listed in
this evaluation and influence the results.
The mean extraction efficiency for sulfur dioxide over the range of RQL to 2 times the target concentration (1.41 to 314 µg per sample) was 99.5%. The extraction efficiency was not affected by the
presence of water.
Extracted samples remain stable for at least 24 h.
2.6 Recommended sampling time and sampling rate
Sample for up to 240 min at 0.05 L/min (12 L) to collect TWA (long-term) samples.
Sample for up to 15 min at 0.5 L/min (7.5 L) to collect TWA (short-term) samples.
When short-term samples are collected, the air concentration equivalent to the reliable quantitation limit becomes larger. For example, the reliable quantitation limit is 0.058 ppm (0.152 mg/m3) for
sulfur dioxide when 7.5 L are collected.
2.7 Interferences, sampling (Section 4.9)
Retention
The retention efficiency for all samples was above 95.5% of theoretical, when samplers containing approximately 78 µg of sulfur dioxide were allowed to sample 9 L of contaminant-free air having an
average relative humidity of 80% at 21 °C. Samples were collected at a sampling rate of 0.05 L/min.
Low humidity
The collection efficiency for all samples was above 96.8% of theoretical, when the samplers were used to sample a test atmosphere containing two times the target concentration of sulfur dioxide
having an average relative humidity of 20% at 22 °C. Samples were collected at a sampling rate of 0.05 L/min for 240 min.
Low concentration
The collection efficiency for all samples was above 92.8% of theoretical, when the sampler was used to sample a test atmosphere containing approximately 0.1 times the target concentration of hydrogen
sulfide with an average relative humidity of 80% at 22 °C. Samples were collected at a sampling rate of 0.05 L/min for 240 min.
The collection efficiency for all samples was above 91.5% of theoretical, when the sampler was used to sample a test atmosphere containing approximately 0.15 times the target concentration of hydrogen
sulfide with an average relative humidity of 80% at 23 °C. Samples were collected at a sampling rate of 0.5 L/min for 15 min.
Interference
The collection efficiency for all samples was above 97.7% of theoretical, when the sampler was used to sample a test atmosphere containing approximately one times the target concentration of sulfur
dioxide and 14.1 mg/m3 of hydrogen sulfide with an average relative humidity of 80% at 22 °C. Samples were collected at a sampling rate of 0.05 L/min for 240 min.
The GFF prefilter will adsorb up to 1.6 µg of sulfur dioxide when sampling at 80% humidity. This is equivalent to 1% of the sulfur dioxide collected at the target concentration for a 240 min sample
and is considered negligible. The amount of sulfur dioxide adsorbed on the prefilter is humidity dependent and decreases as humidity decreases.
If present sulfur trioxide can cause a positive interference.
See Section 4.9 for more information on other potential interferences that were evaluated.
3. Analytical Procedure
Adhere to the rules set down in your Chemical Hygiene Plan.12 Avoid skin contact and inhalation of all chemicals and review all appropriate MSDSs.
3.1 Apparatus
Ion chromatograph with a conductivity detector and autosampler. A Dionex DX-500 ion chromatograph with a GP50 gradient pump, an ED40 with a conductivity cell, an ASRS-ULTRA II 4-mm anion suppressor
and a Waters 717plus autosampler were used in this evaluation.
IC column and guard column that can separate sulfate from potential interferences. A Dionex IonPac AS14 analytical column (250-mm × 4-mm i.d.) and a Dionex IonPac AG14 guard column
(50-mm × 4-mm i.d.) were used in this evaluation.
A means to integrate chromatograms. Dionex Peaknet 5.1 software was used in this evaluation.
Autosampler Vials. Waters 4-mL clear glass vials with plastic caps were used in this evaluation.
Water purifier. A Barnstead NANOpure Diamond system was used to produce 18.0 MΩ-cm DI water in this evaluation.
Glass 20-mL scintillation vials used to prepare samples. Wheaton glass liquid scintillation vials, rinsed several times with DI water and dried, were used in this evaluation.
Water bath. A Precision Scientific model 66643 (5 – 100 °C range) water bath was used in this evaluation.
Scintillation vial racks. Polypropylene Scienceware scintillation racks were used in this evaluation.
A means to dispense and dilute solutions. A Hamilton Microlab 540B dual syringe diluter/dispenser and an Eppendorf Series 2100 Research pipette (100 – 1000 µL) were used in this evaluation.
A mechanical shaker. An Eberbach heavy-duty mechanical shaker was used in this evaluation.
Filters certified for ion chromoatography for the filtration of sample solutions prior to analysis. Pall Corporation ion chromatography certified Acrodisc® 25 mm syringe filters with 0.45 µm Supor®
(PES) membranes were used in this evaluation.
Septum puller. A Restek septum puller, catalog number 20117, was used to remove the plastic retainer rings from the sampler.
Class A 2-L volumetric flasks.
Class A 20-mL volumetric pipets.
3.2 Reagents and Standards
DI water, 18.0 MΩ-cm.
30% Hydrogen Peroxide (H2O2), [CAS no. 7722-84-1], A.C.S. grade or higher. The hydrogen peroxide used in this evaluation was 30% ULTREX II Ultrapure Reagent (lot no. B17467) purchased from J.T. Baker.
Sulfate (SO42-) 1000 mg/L standard solution. The 1000 mg/L sulfate standard used in this evaluation was (lot no. 041007) purchased from Dionex Corporation.
AS14 Eluent Concentrate, containing 350 mM sodium carbonate (Na2CO3) [CAS no. 497-19-8] and 100 mM sodium bicarbonate (NaHCO3) [CAS no. 144-55-8]. AS14 Eluent Concentrate was purchased from Dionex
Corporation.
Eluent [3.5 mM Na2CO3 / 1.0 mM NaHCO3]: Add approximately 500 mL of DI water to a 2-L volumetric flask, followed by 20 mL of AS14 Eluent Concentrate, and then dilute to mark with DI water and mix
well. Degas the solution and transfer to appropriate container(s). It is recommended that fresh eluent be prepared for each sample set analyzed.
3.3 Standard preparation
Prepare a concentrated stock standard of 100 mg/L using the 1000 mg/L sulfate standard and the eluent as the diluent. From the stock standard prepare 3 or more working standards also using the eluent
as the diluent. It is recommended that working range standards be prepared in the range of 1 - 40 mg/L sulfate.
If upon analysis, sample concentrations fall outside the range of prepared standards, prepare and analyze additional standards to confirm instrument response, or dilute high samples with eluent and
reanalyze the diluted samples.
3.4 Sample preparation
Note: During sampling, sulfur dioxide reacts with sodium carbonate on the coated filter forming sulfite; the sulfite will slowly oxidize to sulfate. During sample preparation sulfite and sulfate are
extracted from the filter and any remaining sulfite is oxidized to sulfate.
Starting from the wide end of the sampler carefully remove and discard the first plastic retainer ring, the prefilter and the middle retainer ring. Remove second filter (coated filter) and place it
into a clean 20-mL scintillation vial. (The coated silica gel can be analyzed, if requested, for hydrogen sulfide following the preparation procedure described in OSHA Method 1008. Otherwise the
coated silica gel should be disposed of properly.)
Add 9.9 mL of eluent and 100 µL of hydrogen peroxide to each vial, for a final solution volume of 10 mL, and cap tightly.
Place the scintillation vials in a scintillation rack and place rack in a 100 °C water bath. Use clean DI water in the bath with the water level no higher than the bottom third of the scintillation
vials.
Remove the scintillation rack from the water bath after 20 min, or transfer scintillation vials to a dry rack, and secure on a mechanical shaker. Shake samples for 30 min.
Remove the scintillation rack from the shaker and allow samples to sit for 2 hours to insure that all of the sulfite is oxidized to sulfate.
Filter each sample and transfer approximately 3 mL to a 4-mL autosampler vial and cap. Puncture the cap of each vial using a small needle to reduce pressure buildup in the vial
prior to analysis. Failure to puncture the cap could cause results to be low.
Analyze samples for sulfate as described in section 3.5.
3.5 Analysis
It is recommended that each sample be injected twice to insure that a pressure buildup in the vial has not occurred due to the hydrogen peroxide.
3.5.1 Analytical Conditions
IC conditions
|
columns: |
IonPac AS14 column (250-mm x 4-mm i.d.) and
AG14 guard column (50-mm x 4-mm i.d.) |
|
|
flow rate: |
1.2 mL/min |
|
|
eluent: |
3.5 mM Na2CO3 / 1.0 mM NaHCO3 |
|
|
pump
pressure: |
~1600 psi |
|
|
injection
volume: |
50 µL |
|
|
retention
time: |
10.7 min (each column varies
slightly) |
|
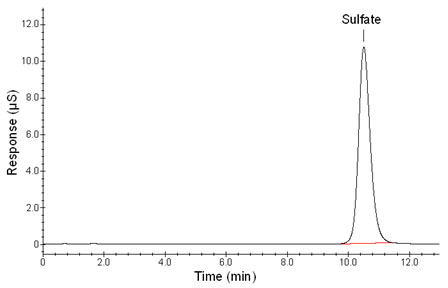
Figure 3.5.1. Chromatogram obtained at target concentration with
recommended
conditions. |
3.5.2 Calibration
An external standard calibration method is used. A calibration curve can be constructed by plotting response of standard injections versus µg/mL of sulfate per sample. Bracket the samples with
freshly prepared analytical standards over the range of concentrations.
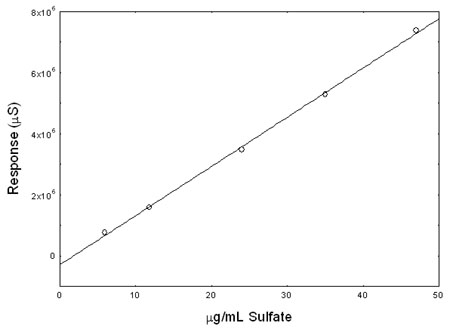
Figure 3.5.2. Calibration curve of sulfate. (Y = 160960X – 284839) |
3.6 Interferences (analytical)
Any compound that produces a response and has a similar retention time as sulfate is a potential interference. If any potential interferences were reported, they should be considered before samples
are extracted. Generally, chromatographic conditions can be altered to separate any interference from the analyte.
When necessary, the identity of an analyte peak can be confirmed by additional analytical techniques or alternate columns such as a Dionex IonPac AS4 analytical column.
3.7 Calculations
The air concentration is calculated using the following formulas:
Micrograms of sulfur dioxide per sample is:
M=[(FxDF)-B]xSVxGF
Where:
M is µg of sulfur dioxide per sample
F is the sulfate (µg/mL) found on filter
DF is dilution factor applied (if appropriate)
B is the sulfate (µg/mL) found on a blank sampler
SV is solution volume of sample (10 mL)
GF is the gravimetric factor (0.6669 SO2/SO42-)
Concentration by weight of sulfur dioxide (mg/m3) is:
Where:
CM is concentration by weight of sulfur dioxide (mg/m3)
M is µg of sulfur dioxide per sample
EE is extraction efficiency in decimal form
V is L of air sampled
Concentration by volume of sulfur dioxide (ppm) is:
Where:
CV is concentration by volume of sulfur dioxide (ppm)
CM is concentration by weight of sulfur dioxide (mg/m3)
VM is molar volume at NTP (24.46 L/mole)
Mr is molecular weight of sulfur dioxide (64.065 g/mole)
4. Backup data
General background information about the determination of detection limits and precision of the overall procedure is found in the "Evaluation Guidelines for Air Sampling Methods Utilizing
Chromatography Analysis".13 The Guidelines define analytical parameters, specify required laboratory tests, statistical calculations and acceptance criteria.
4.1 Detection limit of the analytical procedure (DLAP)
The DLAP is measured as mass of analyte introduced onto the chromatographic column. Ten analytical standards were prepared with equally descending increments with the highest standard containing
0.4 µg/mL sulfate. This is the concentration that would produce a peak approximately 10 times the response of a calibration blank. These standards, and the calibration blank were analyzed with the
recommended analytical parameters (50-µL injection), and the data obtained were used to determine the required parameters (standard error of estimate and slope) for the calculation of the DLAP.
Values of 2372 and 392 were obtained for the slope and standard error of estimate respectively. The DLAP was calculated to be 0.330 ng sulfur dioxide (0.495 ng sulfate).
Table 4.1
Detection Limit of the Analytical Procedure
|
concentration
(µg/mL SO42-) |
mass
on column (ng) |
area
counts
(µS) |
|
0
0.040
0.080
0.120
0.160
0.200
0.240
0.280
0.320
0.360
0.400 |
0
2.00
4.00
6.00
8.00
10.0
12.0
14.0
16.0
18.0
20.0 |
0
5024
8657
14297
18406
22942
27991
33181
37662
42486
47532 |
|
|
|
Figure 4.1. Plot of data to determine the DLAP. (Y = 2372X + 251) |
4.2 Detection limit of the overall procedure (DLOP) and reliable quantitation limit (RQL)
The DLOP is measured as mass per sample and expressed as equivalent air concentrations, based on the recommended sampling parameters. Ten samplers were spiked with equally descending increments of
sodium sulfite, such as the highest sampler loading was equivalent to 4.88 µg of sulfur dioxide per sample. This is the amount spiked on a sampler that would produce a peak approximately 10 times
the response of a calibration blank. These spiked samplers, and the calibration blank were analyzed with the recommended analytical parameters (50-µL injection), and the data obtained were used to
determine the required parameters (standard error of estimate and slope) for the calculation of the DLOP. Values of 14365 and 2024 were obtained for the slope and standard error of estimate
respectively. The DLOP was calculated to be 0.423 µg sulfur dioxide per sample (0.013 ppm or 0.035 mg/m3 for a TWA sample).
Table 4.2
Detection Limit of the Overall Procedure
|
|
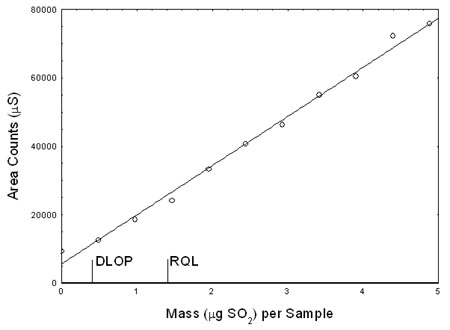
Figure 4.2.1. Plot of data to determine the DLOP/RQL.
(Y = 14365X + 5636) |
mass
per sample
(µg SO2) |
area
counts
(µS) |
|
0
0.488
0.977
1.465
1.954
2.442
2.931
3.419
3.907
4.396
4.884
|
9236
12534
18492
24122
33240
40688
46224
54996
60373
72167
75811
|
The RQL is considered the lower limit for precise quantitative measurements. It
is determined from the regression line parameters obtained for the calculation
of the DLOP, providing 75% to 125% of the analyte is recovered. The RQL is 1.41
µg sulfur dioxide per sample (0.045 ppm or 0.118 mg/m3 for a TWA sample).
Recovery at this concentration is 87.8%. |
|

Figure 4.2.2. Chromatogram of the RQL. |
4.3 Instrument calibration
The standard error of estimate was determined from the linear regression of data points from standards over a range that covers 0.25 to 2 times the TWA target concentration. A calibration curve was
constructed and shown in Section 3.5.2 from the three injections of five standards. The standard error of estimate is 2.33 µg/mL sulfate.
Table 4.3
Instrument Calibration
|
standard concn
(µg/mL SO42-) |
area counts
(µS) |
|
5.9
11.8
24.0
35.0
47.0 |
767149
1585665
3480350
5285257
7376833 |
766179
1583575
3473558
5278117
7349652 |
761827
1589967
3475773
5284695
7401092 |
|
4.4 Precision (overall procedure)
The precision at the 95% confidence level is obtained by multiplying the standard error of estimate by 1.96 (the z-statistic from the standard normal distribution at the 95% confidence level).
In Section 4.5, 95% confidence intervals are drawn about their respective regression lines in the storage graph figures. The precision of the overall procedure of ± 9.96% was obtained from the
standard error of estimate of 5.08% in Figure 4.5.1. The precision includes an additional 5% for sampling error.
4.5 Storage test
Storage samples for sulfur dioxide were prepared by collecting samples from a controlled test atmosphere using the recommended sampling conditions. The concentration of sulfur dioxide was at the
target concentration (4.83 ppm) with an average relative humidity of 80% at 21 °C. Thirty-three storage samples were prepared. Three samples were analyzed on the day of generation. Fifteen of the
tubes were stored at reduced temperature (1 °C) and the other fifteen were stored in a closed drawer at ambient temperature (about 21 °C). At 3-4 day intervals, three samples were selected from each
of the two storage sets and analyzed. Sample results were not corrected for extraction efficiency.
Table 4.5
Storage Test for Sulfur Dioxide
|
time
(days) |
ambient storage
recovery (%) |
refrigerated
storage
recovery (%) |
|
0
3
6
9
13
16 |
100.4
98.9
100.6
98.8
100.9
101.2 |
100.4
98.8
100.1
100.3
101.1
101.6 |
100.2
98.7
99.5
99.3
LIA
102.6 |
100.4
98.7
99.0
94.2
98.2
98.5 |
100.4
103.2
96.9
94.4
100.6
99.0 |
100.2
100.3
99.3
94.2
99.8
101.0 |
|
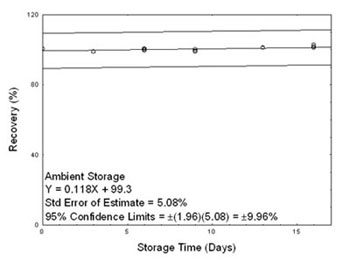
Figure 4.5.1. Ambient storage test for sulfur dioxide. |
|

Figure 4.5.2. Refrigerated storage test for sulfur dioxide. |
4.6 Reproducibility
Six samples were prepared by collecting them from a controlled test atmosphere similar to that which was used in the collection of the storage samples.
The samples were submitted to the OSHA Salt Lake Technical Center for analysis along with a draft copy of this method. The samples were analyzed after being stored for 9 days at ambient
temperature (about 21 °C). Sample results were corrected for extraction efficiency. No sample result for sulfur dioxide had a deviation greater than the precision of the overall procedure
determined in Section 4.4. |
|
Table 4.6
Reproducibility Data for Sulfur Dioxide
|
theoretical
(µg/sample) |
recovered
(µg/sample) |
recovery
(%) |
deviation
(%) |
|
187
186
182
185
188
187 |
192
193
191
190
191
194 |
102.7
103.8
104.9
102.7
101.6
103.7 |
2.7
3.8
4.9
2.7
1.6
3.7 |
|
|
4.7 Sampler capacity
The sampling capacity of the sampler was tested by sampling from a dynamically generated test atmosphere of sulfur dioxide at 4.4 times the target concentration (58.1 mg/m3 or 22.2 ppm) with an
average relative humidity of 78% at 22 °C. The samples were collected at a sampling rate of 0.05 L/min. All samplers in this test had the two sections of silver nitrate coated silica gel removed.
Backup samplers were placed in-line behind the front sampler and were changed every 60 min after the initial collection of 240 min. No breakthrough was observed; even after sampling for 480 min.
4.8 Extraction efficiency and stability of extracted samples
Extraction efficiency
Table 4.8.1
Extraction Efficiency of Sulfur Dioxide
|
level
|
sample number
|
x target
concn |
µg SO2
per sample |
1 |
2 |
3 |
4 |
mean |
|
RQL
0.25
0.5
1.0
1.5
2.0
1.0 (wet) |
1.41
39.0
79.0
157
236
314
157 |
97.7
96.5
98.8
99.1
99.4
98.4
108 |
109
96.6
99.0
99.2
98.8
98.8
100 |
99.5
96.0
99.0
99.5
98.9
98.4
100 |
98.9
95.4
111
99.7
98.3
99.1
99.3 |
101
96.1
102
99.4
98.9
98.7
102 |
|
Several other extraction procedures were investigated and the data is presented below:
An extraction efficiency of 84.7% was obtained if sodium sulfite spiked samples were extracted by adding the eluent and hydrogen peroxide, shaking for 30 min and analyzing 2 hours later.
An extraction efficiency of 92.4% was obtained if sodium sulfite spiked samples were extracted by adding the eluent, heating for 20 minutes in a water bath, adding the hydrogen peroxide, and then
shaking for 30 min followed by analysis 2 hours later. When samples were extracted this way and allowed to sit overnight the extraction efficiency was 96.6%.
The recovery of samples prepared using the test atmosphere generator did not, however, change when different extraction procedures were used. For example, the recovery of the six retention efficiency
samples was 95.7% using the recommended extraction procedure versus 96.2% using the cold extraction procedure. However, to insure complete extraction the recommended extraction procedure was chosen.
Stability of extracted samples
The stability of extracted samples was investigated by reanalyzing the target concentration samples 24 h after initial analysis. After the original analysis was performed two vials were recapped
with new septa while the remaining two retained their punctured septa. The samples were reanalyzed with fresh standards. The average percent change was +0.40% for samples that were resealed with
new septa and +0.80% for those that retained their punctured septa. The test was performed at room temperature (about 21 °C).
Table 4.8.2
Stability of Extracted Samples for Sulfur Dioxide
|
punctured septa
replaced
|
punctured septa
retained
|
initial
(%) |
after
one day
(%) |
difference
(%) |
initial
(%) |
after
one day
(%) |
difference
(%) |
|
99.5
99.7
99.6 |
100.7
99.2
(mean)
100.0 |
+1.2
-0.5
+0.4 |
99.1
99.2
99.2 |
99.5
100.5
(mean)
100.0 |
+0.4
+1.3
+0.8 |
|
4.9 Interferences (sampling)
Retention
The ability of the sampler to retain sulfur dioxide was tested by sampling from a dynamically generated test atmosphere of sulfur dioxide (26.8 mg/m3 or 10.2 ppm)
with an average relative humidity of 80% at 21 °C. Six samplers had
contaminated air drawn through them at 0.05 L/min for 60 min. |
|
Table 4.9.1
Retention Efficiency (%) of Sulfur Dioxide
|
set no. |
1 |
2 |
3 |
mean |
|
first
second
second/first |
95.6
96.4
|
94.6
95.5
|
96.6
95.7
|
95.6
95.9
100.3 |
|
|
Sampling was discontinued and three samples set aside (first set). The
generation system was flushed with contaminant-free air. Sampling resumed with
the other three samples having contaminant-free air drawn through them at 0.05
L/min for 180 min and then all six samplers were analyzed. The mean of the
samples in the second set had retained more than 100.3% of the mean collected by
the first three samples.
Low humidity
The ability of the sampler to collect sulfur dioxide from a relatively dry atmosphere was tested by sampling from a dynamically generated test atmosphere of sulfur dioxide (29.0 mg/m3 or 11.1 ppm)
with an average relative humidity of 20% at 22 °C. Samples were collected at a sampling rate of 0.05 L/min for 240 min. The samplers collected 96.8%, 98.1% and 98.2% of theoretical.
Low concentration
The ability of the sampler to collect sulfur dioxide at low concentrations was tested by sampling from a dynamically generated test atmosphere of 0.10 times the target concentration of sulfur dioxide
(1.35 mg/m3 or 0.52 ppm) with an average relative humidity of 80% at 22 °C. Three samplers had contaminated air drawn through them at 0.05 L/min for 240 min. All of the samples were immediately
analyzed. The samplers collected 92.8%, 93.1% and 94.0% of theoretical.
The ability of the sampler to collect sulfur dioxide at low concentrations and low humidity was tested by sampling from a dynamically generated test atmosphere of 0.12 times the target concentration
of sulfur dioxide (1.52 mg/m3 or 0.58 ppm) with an average relative humidity of 20% at 19 °C. Three samplers had contaminated air drawn through them at 0.05 L/min for 240 min. All of the samples
were immediately analyzed. The samplers collected 94.1%, 96.8% and 93.9% of theoretical.
The ability of the sampler to collect sulfur dioxide at low concentrations when taking short term samples was tested by sampling from a dynamically generated test atmosphere of 0.15 times the target
concentration of sulfur dioxide (1.91 mg/m3 or 0.73 ppm) with an average relative humidity of 80% at 23 °C. Three samplers had contaminated air drawn through them at 0.5 L/min for 15 min. All of
the samples were immediately analyzed. The samplers collected 91.5%, 95.1% and 94.7% of theoretical.
Interferences
The ability of the sampler to collect sulfur dioxide in the presence of hydrogen sulfide was tested by sampling from a dynamically generated test atmosphere containing 16.0 mg/m3 (6.1 ppm) of sulfur
dioxide and 14.1 mg/m3 (10.1 ppm) of hydrogen sulfide with an average relative humidity of 79% at 22 °C. Three samplers had contaminated air drawn through them at 0.05 L/min for 240 min. All of the
samples were immediately analyzed. The samplers collected 97.7%, 98.6% and 99.4% of theoretical.
Sulfur trioxide has been reported as a potential positive interference for sulfur dioxide when using sodium carbonate coated filters.14 However, because sulfur trioxide has a high affinity for water
and will quickly react with any moisture in the air resulting in the formation of sulfuric acid,15 it would only be expected to be present in extremely dry atmospheres. Due to the extremely reactive
nature of sulfur trioxide it was only possible to perform a qualitative test. Three sampling trains consisting of a drying tube followed by a sampler with air being drawn through at a sampling rate
of 0.05 L/min were used. Sulfur trioxide gas was injected into the sampling train between the drying tube and sampler and contaminant-free air was continued to be drawn through the samplers for an
additional 15 min. Both the front prefilter and the coated filter were analyzed using the recommended analytical parameters. Sulfate was found on both the front and back filter indicating that if
sulfur trioxide is present it can cause a positive interference.
Prefilter adsorption
The glass fiber prefilter used is slightly alkaline and will adsorb sulfur dioxide16 resulting in some loss of sulfur dioxide. Several tests were performed to experimentally determine how much sulfur
dioxide would be lost on the prefilter. Using the test atmosphere generator described in Section 4.10 three samples were collected for each test and the prefilters analyzed using the recommended
analytical parameters for sulfur dioxide.
Sulfur dioxide in the presence of water will form sulfuric acid. In order to distinguish between the effect of residence time of sulfur dioxide in the test atmosphere (i.e. the amount of time sulfur
dioxide had to interact with water vapor present in the test atmosphere), and the adsorption capacity of the filter, various dilution air flow rates were used. The effect of humidity on the
adsorption capacity of the prefilter was also examined. All samples were collected at ambient temperate (~21 °C).
The adsorption capacity of the prefilter was tested by sampling from a dynamically generated test atmosphere of approximately 2× the target concentration of
sulfur dioxide with average relative humidities of 80% and 30% with
various dilution flow rates. Samplers had contaminated air drawn through
them at 0.05 L/min for 240 min. All of the samples were immediately
analyzed. Results are shown in Table 4.9.2. The results illustrate that as
the dilution air flow rate of the test atmosphere increases, meaning the
amount of time sulfur dioxide had to interact with water vapor present in
the test atmosphere decreases, less sulfur dioxide is found on the
prefilter. |
|
Table
4.9.2
Sulfur Dioxide Collected on Prefilter
when Sampling at 2× Target Concn
|
dilution flow rate
(liters/min) |
% relative humidity |
mean µg SO2 recovered |
standard
deviation |
|
12.1
54.8
5.9
12.1
56.2
117.6 |
30
30
80
80
80
80 |
0.59
0.34
2.19
1.81
1.68
1.58 |
0.13
0.06
1.47
0.23
0.08
0.16 |
|
|
The results also demonstrate that as the humidity decreases the amount of sulfur
dioxide collected on the prefilter decreases.
A plot of the test results for the data
at 80% humidity are shown in Figure 4.9.1. As the dilution flow rate
continues to increase the X term in the line equation can be ignored and
the amount of sulfur dioxide that could be adsorbed by the prefilter is
calculated to be 1.57 µg. This is nearly the same amount of sulfur dioxide
that was found on the prefilter at a dilution flow rate of 117.6 liters
per minute (1.58 µg). This amount would be equivalent to 1% of the sulfur
dioxide collected at the target concentration for a 240 min sample.
The adsorption capacity of the prefilter at low concentrations was tested
by sampling from a dynamically generated test atmosphere of approximately
0.1× the target concentration of sulfur dioxide with average relative
humidities of 80% using various dilution flow rates. |
|
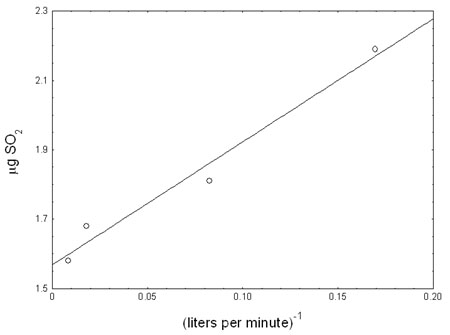
Figure 4.9.1. Plot of μg SO2 found on prefilter at 2× the target
concn and 80% humidity. (Y = 3.56X + 1.57) |
Samplers had contaminated air drawn through
them at 0.05 L/min for 240 min. All of the samples were immediately
analyzed. Results are shown in Table 4.9.3. The results indicate that about
8% of the sulfur dioxide collected at 0.1× the target concentration for a
240 min sample would be adsorbed by the prefilter. The adsorption capacity
of the prefilter at low concentrations was further tested by sampling from a
dynamically generated test atmosphere of 0.1× the target concentration of
sulfur dioxide with an average relative humidity of 80% and a dilution flow
rate of 100 liters. |
|
Table 4.9.3
Sulfur Dioxide Collected on Prefilter
when Sampling at 0.1× Target Concn
|
dilution
flow rate
(liters/min) |
% relative
humidity |
mean µg SO2
recovered |
standard
deviation |
|
58.0
122.5
153.2 |
80
80
80 |
1.26
1.11
1.30 |
0.14
0.01
0.04 |
|
|
Samplers had contaminated air drawn through them at 0.5 L/min for 15 min. All of the samples were immediately analyzed. The prefilters had a mean recovery of 0.750 µg sulfur dioxide with a standard
deviation of 0.028. The results indicate that about 8% of the sulfur dioxide collected at 0.1× the target concentration for a 15 min sample would be adsorbed by the prefilter.
In summary the data indicates that the amount of sulfur dioxide adsorbed on the prefilter is humidity dependent decreasing as humidity decreases. The data also indicates that the amount of sulfur
dioxide adsorbed on the prefilter is concentration dependent decreasing as concentration decreases. The loss of 1% of the sulfur dioxide collected at the target concentration for a 240 min sample at
80% humidity is considered negligible.
Other interferences
The data presented in this section was collected during the development and testing of the sampler for hydrogen sulfide as presented in OSHA method 1008. Samples were prepared for analysis by placing
the filter in a 20 mL scintillation vial. Ten mL of eluent was added along with 100 µL of hydrogen peroxide. Samples were placed on a shaker and shaken for 30 min, allowed to settle for 1 hour and
then analyzed.
Methanethiol was tested as a potential
interferent. Three samplers, with Gastec total mercaptan detector tubes (SKC
Inc., cat. no. 810-70L) attached in series downstream, having
contaminant-free air drawn through them at 0.5 L/min (RH of 80% at 21 °C),
had 42.5 µg of methanethiol gas (42.5 µg/7.5 L = 5.67 mg/m3 or 2.88 ppm)
injected directly upstream of the samplers. Contaminant-free air continued
to be drawn through the samplers for an additional 15 min at a rate of 0.5
L/min. |
|
Table 4.9.4
Methanethiol Interference Test
|
sample no. |
theoretical
(µg/sample) |
recovered
(µg/sample) |
recovery
(%) |
equivalent
µg SO2 |
|
1
2
3 |
42.5
42.5
42.5 |
0.20
0.10
0.03 |
0.47
0.24
0.07 |
0.27
0.13
0.03 |
|
|
After injection of the methanethiol the detector tube quickly changed color
providing a visual demonstration that the compound was passing though the
sampler. The samples were stored overnight and then analyzed the next day. The
samples collected 0.27, 0.13 and 0.03 equivalent µg of sulfur dioxide
demonstrating that methanethiol is not a significant interferent.
Carbonyl sulfide was tested as a potential interferent. Three samplers having contaminant-free air drawn through them at 0.5 L/min (RH of 80% at 21 °C), had 63.0 µg of carbonyl sulfide gas
(63.0 µg / 7.5 L = 8.4 mg/m3 or 3.42 ppm) injected directly upstream of the samplers. Contaminant-free air continued to be drawn through the samplers for an additional 15 min at a rate of 0.5 L/min.
The samples were stored overnight and then analyzed. Results for the three samples were 0.03, 0.1 and 0.13 µg sulfur dioxide demonstrating that carbonyl sulfide is not a significant interferent.
Ethanethiol, 1-butanethiol, thiophenol, and carbon disulfide were also tested as potential interferents, with each compound being tested separately (4 separate tests for a total of 12 samples).
A sampling train consisting of an 8-cm long glass tube (6-mm i.d. x 8-mm o.d.) containing a quartz wool plug followed by a sampler, and in the case of ethanethiol, 1-butanethiol and thiophenol,
followed by a total mercaptan detector tube. Thirty µL of the neat compound (as a liquid) was injected into the quartz wool plug and then contaminant-free air (RH of 80% at 21 °C) was drawn through
the sampling train at 0.05 L/min for 240 min. In the case of ethanethiol, 1-butanethiol and thiophenol the detector tube changed color providing a visual demonstration that the compound was passing
through the sampler. The samples were stored overnight and then analyzed. Results are shown in Table 4.9.5.
Table 4.9.5
Ethanethiol, 1-Butanethiol, Thiophenol and Carbon Disulfide
|
|
ethanethiol
|
1-butanethiol
|
thiophenol
|
carbon disulfide
|
sample no. |
equivalent
µg SO2 |
equivalent
µg SO2 |
equivalent
µg SO2 |
equivalent
µg SO2 |
|
1
2
3
|
0.00
0.00
0.20 |
0.57
0.30
0.83 |
0.00
0.74
0.57 |
0.33
0.60
0.50 |
|
The compounds listed in Table 4.9.5 represent an extreme challenge to the sampler. For example, ethanethiol has a density of 0.839 g/mL at 25 °C, that would mean 30 µL would be equivalent to
approximately 25170 µg as follows:
|
|
mL |
|
0.839g |
|
1000mg |
|
1000ug |
|
|
30 uL |
X |
|
X |
|
X |
|
X |
|
= |
25170ug |
|
|
1000uL |
|
mL |
|
1g |
|
1mg |
|
|
This would give an equivalent air concentration of 2098 mg/m3 (25170 µg / 12 L = 2098 mg/m3 or 825 ppm) which is obviously not an amount that would be expected in a workplace environment. However,
these tests show that even when the sampler is exposed to extreme amounts of potential interferences, that the sampler and/or analytical method do not have much capacity to collect and detect these
compounds and that they do not create significant interferences.
4.10 Generation of test
atmospheres
A test atmosphere generator, as diagramed in Figure 4.10, was set up in a
walk-in hood. House air was dried, purified and then regulated using a
Miller Nelson Model 401 Flow-Temperature-Humidity Control System. A measured
flow of 5% sulfur dioxide gas, flowing through stainless steel lines from a
gas cylinder, was introduced into a measured flow of dilution air (set at
~10, 50, or 100 liters per minute depending on the concn needed) coming from
the Miller Nelson control system. The sulfur dioxide gas and dilution air
flowed into a mixing chamber (76-cm × 15-cm) and then into a sampling
chamber (56-cm × 9.5-cm). Samples were collected through sampling ports on
the sampling chamber. Temperature and humidity were measured near the exit
of the sampling chamber using an Omega Digital Thermo-hygrometer model
RH411. The sulfur dioxide used in this evaluation was purchased from
Praxair, Inc (primary standard containing 5% SO2 in a nitrogen balance).
|
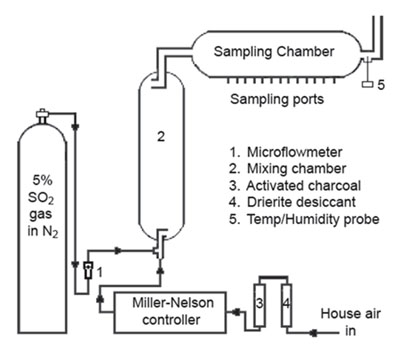
Figure 4.10. Diagram of apparatus used to generate test atmospheres.
|
|
A direct reading PAC III Dräger meter with a sulfur dioxide sensor, that was calibrated using an independent source of sulfur dioxide, was attached to a sampling port on the sampling chamber. The PAC III was used to monitor the concentration of the test atmosphere during generation. The PAC III was also used as a check on the calculated theoretical concentration of the test atmosphere
generator (the calculated concentration was used as the theoretical value for all tests performed in this evaluation).
Appendix A
A.1 Sampler preparation
For this evaluation samplers were prepared in-house, however, samplers are also available for purchase through SKC, Inc. (cat. no. 226-177).
The instructions for the preparation and construction of the sampler are described in detail in Appendix A of OSHA Method 1008. The instructions in Method 1008 should be followed exactly except
where modified as described below. The modification of the sampler consist of a washing procedure for cleaning the glass fiber depth filters and using higher grade reagents to coat the filters in
order to reduce the background levels of sulfate. The concentration of the reagents and the amount of coating solution used is the same as described in Method 1008.
Below are instructions on how the glass fiber depth filters were cleaned and coated for this evaluation.
A.1.1 Apparatus
Binder free 13-mm (1.0 µm pore size) glass fiber depth filters (GFF). The GFF used in this evaluation (lot no. 4170403) were purchased from SKC, Inc. (cat. no. 225-16).
Glass 20-mL scintillation vials. Wheaton glass liquid scintillation vials were used in this evaluation.
Rotary evaporator, heating bath, vacuum pump and 250-mL flat-bottom evaporation flask. The rotary evaporator used in this evaluation was a Buchi Rotavapor R-205S, with a Buchi B-490 heating bath, a model no. 8805 DirecTorr vaccum pump and a 250 mL flat bottom evaporation flask.
Water purifier. A Barnstead NANOpure Diamond system was used to produce 18.0 MΩ-cm DI water in this evaluation.
Analytical balance capable of weighing at least 0.01 mg and weighing paper. An Ohaus Galaxy 160D balance was used in this evaluation.
Glass 50-mL beaker.
Class-A 50-mL volumetric flask.
A means to dispense solutions. A Eppendorf Series 2100 Research pipette (100 – 1000 µL) was used in this evaluation.
Desiccator. A Plas-Labs amber acrylic desiccator cabinet model 860-CGA was used in this evaluation.
PTFE coated forceps.
Forty place polypropylene 15-mm tube rack with 10-mm diameter holes on the bottom.
Nitrogen gas.
A.1.2 Reagents
Sodium carbonate anhydrous (Na2CO3), [CAS no. 497-19-8]. The sodium carbonate used in this evaluation was Trace Select™, anhydrous, ≥ 99.999% (metal basis) containing ≤ 0.001% sulfate
(lot no. 1298052) purchased from Sigma-Aldrich.
Ethanol anhydrous (C2H6O), [CAS no 64-17-5]. The ethanol used in this evaluation was ethanol anhydrous, 200 proof, ≥ 99.5% (lot no. 02459CD) purchased from Sigma Aldrich.
Glycerol (C3H8O3) [CAS no. 56-81-5]. The glycerol used in this evaluation was BioChemika Ultra, for molecular biology, anhydrous, ≥ 99.5% containing ≤ 0.001% sulfate (lot no. 1243001) purchased from
Sigma Aldrich.
GFF coating solution: Add approximately 10 mL of DI water to a 50-mL volumetric flask. Weigh out 2.5 g of sodium carbonate and carefully add to the volumetric flask. Next add 10 mL of ethanol
and 1 mL of glycerol, dilute to the mark with DI water, mix well, and transfer to an appropriate storage bottle. It is recommended that the solution be stored and used for no longer than six months.
A.1.3 Procedure for washing GFF
Set the temperature of the rotary evaporator water bath to 75 °C.
Place 200 GFF’s in a 250-mL flat-bottom evaporation flask.
Carefully add approximately 200 mL of DI water to the flask.
Attach the evaporating flask to the rotary evaporator, partially submerging flask in the water bath, and apply a vacuum of approximately 250 mbar. Rotate the flask at 20 rpm for 30 min.
Remove the flask from the rotary evaporator and carefully pour off the DI water.
Carefully add approximately 200 mL of DI water to the flask, gently swirl, and pour off the DI water. Repeat for a total of three times.
Again add approximately 200 mL of DI water to the flask and attach to the rotary evaporator, partially submerging flask in the water bath, and apply a vacuum of approximately 250 mbar. Rotate the
flask at 20 rpm for 30 min.
Remove the flask from the rotary evaporator and carefully pour off the DI water.
Carefully add approximately 200 mL of DI water to the flask, gently swirl, and pour off the DI water. Repeat for a total of three times.
Purge flask containing wet filters continuously with ~ 0.5 L/min clean dry nitrogen until filters are dry.
When filters are dry carefully remove from flask and store in a clean scintillation vial.
A.1.4 Preparation of coated filters
Place a GFF over each of the forty 10-mm wide holes on the bottom of an overturned polypropylene 15-mm tube rack.
Pipette 100 µL of coating solution onto each filter.
Place rack in a desiccator, purge desiccator with nitrogen and allow filters to dry overnight.
Place coated filters in scintillation vial and store in desiccator.
Assemble sampler as described in OSHA Method 1008.
References
1.
NIOSH Manual of Analytical Methods (NMAM), 2nd ed.; DHEW/NIOSH Pub. No. 78-175; U.S. National Institute of Occupational Safety and Health (NIOSH): Cincinnati, OH, 1978; Vol. 4, pp S308-1 – S308-7.
2.
Wilczek, T.; Zimowski, E.
Sulfur Dioxide in Workplace Atmospheres (Bubbler),
1981. U.S. Department of Labor, Occupational Safety and Health Administration
Web Site. (accessed 2007).
3.
Ku, J. C.
Sulfur Dioxide in Workplace Atmospheres (Impregnated Activated Beaded Carbon),
1992. U.S. Department of Labor, Occupational Safety and Health Administration
Web Site. (accessed 2007).
4.
Simmons, M. K.
Hydrogen Sulfide,
2006. U.S. Department of Labor, Occupational Safety and Health Administration
Web Site. (accessed 2007).
5.
Eller, P. M., Cassinelli, M. E.; Sulfur Dioxide. NIOSH Manual of Analytical Methods (NMAM), 4th ed.; U.S. National Institute of Occupational Safety and Health: Cincinnati, OH, 1994; Vol. 3.
6.
Sulfur Dioxide. Documentation of the Threshold Limit Values and Biological Exposure Indices, 7th ed.; American Conference of Governmental Industrial Hygienists, Inc.: Cincinnati, OH, 2001; Vol. 3.
7.
Sulfur Dioxide. Documentation of the Threshold Limit Values and Biological Exposure Indices, 7th ed.; American Conference of Governmental Industrial Hygienists, Inc.: Cincinnati, OH, 2001; Vol. 3.
8.
The Merck Index; 12th ed.; Budavari, S., Ed.; Merck & Co. Inc.: Whitehouse Station, NJ, 1996; pp 1534 -1535.
9.
Lewis, R. J. Sr.; Hazardous Chemicals Desk Reference, 4th ed.; Van Nostrand Reinhold Co.: New York, 1997, pp 1096.
10.
Sulfur Dioxide.
OSHA Chemical Sampling Information. (accessed 2007).
11.
Burright, D.; Chan, Y.; Eide, M.; Elskamp, C.; Hendricks, W.; Rose, M. C.;
Evaluation Guidelines For Air Sampling Methods Utilizing Chromatographic
Analysis. (accessed 2005), OSHA Salt Lake Technical Center, U.S. Department of Labor: Salt Lake City, UT, 1999.
12.
Occupational Exposure to Hazardous Chemicals in Laboratories. Code of Federal Regulations, Part 1910.1450, Title 29, 2003.
13.
Burright, D.; Chan, Y.; Eide, M.; Elskamp, C.; Hendricks, W.; Rose, M. C.;
Evaluation Guidelines For Air Sampling Methods Utilizing Chromatographic
Analysis. (accessed 2005), OSHA Salt Lake Technical Center, U.S. Department of Labor: Salt Lake City, UT, 1999.
14.
Eller, P. M., Cassinelli, M. E.; Sulfur Dioxide. NIOSH Manual of Analytical Methods (NMAM), 4th ed.; U.S. National Institute of Occupational Safety and Health: Cincinnati, OH, 1994; Vol. 3, pp 1.
15.
The Merck Index; 12th ed.; Budavari, S., Ed.; Merck & Co. Inc.: Whitehouse Station, NJ, 1996; pp 1536.
16.
Lee, K. W.; Mukund, R. Filter Selection. In Aerosol Measurement, 2nd ed.; Baron, P. A., Willeke, K., Eds.; John Wiley & Sons, Inc.: New York, 2001; pp 223.
|
|
|