<<< Back to Sampling and Analytical Methods |
Printing Instructions |
For problems with accessibility in using figures, illustrations and PDFs in this method, please contact
the SLTC at (801) 233-4900. These procedures were designed and tested for internal use by OSHA personnel.
Mention of any company name or commercial product does not constitute endorsement by OSHA. |
2-Amino-2-Methyl-1-Propanol
[128 KB
PDF, 9 pages]
Related Information: Chemical Sampling -
2-Amino-2-Methylpropanol
|
Method no.: |
PV2145 |
|
|
Control no.: |
T-PV2145-01-9203-Ch |
|
|
Matrix: |
Air |
|
|
Target concentration: |
3 ppm (11 mg/m3) |
|
|
Procedure: |
Samples are collected by
drawing a known volume of air through glass sampling tubes containing XAD-2
resin coated with 10% (w/w) 1-naphthylisothiocyanate (NITC). Samples are
extracted with N,N-dimethylformamide and analyzed by LC using a UV detector.
|
|
|
Air volume and
sampling rate studied: |
10 L at 0.1 L/min |
|
|
Status of method: |
Partially evaluated method.
This method has been subjected to established evaluation procedures of the
Solvents Branch and is presented for information and trial use. |
|
|
March 1992 |
Mary E. Eide |
|
|
Solvents Branch
OSHA Analytical Laboratory
Sandy UT 84070-6406 |
1. General Discussion
1.1 Background
1.1.1 History
Air samples collected on tubes containing XAD-2 resin coated with NITC were received at SLTC requesting analysis for 2-amino-2-methyl-1-propanol (AMP). This compound was collected on the same media
used in OSHA Method 60 (Ref. 5.1), for diethylene triamine, so those extraction and analytical parameters were used as a starting point for AMP. The AMP was found to readily derivatize with the NITC
to form a stable derivative. The mobile phase of 80:20 isooctane:isopropanol gave a separation for the AMP peak from interferences from the NITC. The samples were extracted with N,N-dimethylformamide
(DMF), with a desorption efficiency mean of 100% for the concentration range of 224 to 11.2 µg/tube. The retention efficiency study showed no AMP on the back up section of the spiked tube or back up
tube, for tubes spiked with 224 µg through which10-L humid air had been drawn. The storage study showed no loss for samples stored for up to 14 days under both refrigerated and ambient conditions.
1.1.2 Workplace exposure (Ref. 5.2 and 5.3)
AMP is a skin irritant, severe eye irritant, and toxic by ingestion.
1.1.3 Toxic effects (This section is for information only and should not be taken as the basis of OSHA policy.) (Ref. 5.3 and 5.4)
AMP is used in the synthesis of surface-active agents, vulcanization accelerants, and pharmaceuticals. AMP is used as an emulsifying agent for cosmetic creams and lotions, mineral oil formulations,
paraffin wax, leather dressings, textile specialties, polishes, and cleaning compounds. AMP is used as an adsorbent for acidic gases.
1.1.4 Physical properties and other descriptive information (Ref. 5.2, 5.3, and 5.4)
synonyms: |
2-aminodimethylethanol; β-aminoisobutanol;
2-amino-2-methylpropanol; 2-amino-2-methylpropan-1-ol; AMP; isobutanolamine;
isobutanol-2-amine |
IMIS: |
A615 |
CAS number: |
124-68-5 |
boiling point: |
165°C |
melting point: |
30-31°C |
molecular weight: |
89.14 |
vapor pressure: |
≤1 mmHg @ 25°C |
appearance: |
clear liquid |
vapor density: |
3.0 |
molecular formula: |
C4H11NO |
odor: |
mild ammoniacal |
solubility: |
water, alcohol, acetone |
temperature: |
438°C (820°F) |
flash point: |
68°C (154.4 °F)(cc) |
density: |
0.934 |
structural formula: |
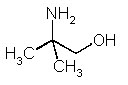 |
1.2 Limit defining parameters
1.2.1 The detection limit of the analytical procedure is 1 ng, with a 15 µL injection volume. This is the smallest amount which could be detected under normal operating conditions.
1.2.2 The overall detection limit is 0.04 ppm based on a 10 liter air volume.
1.3 Advantages
1.3.1 The sampling procedure is convenient.
1.3.2 The analytical method is reproducible and sensitive.
1.3.3 Reanalysis of samples is possible.
1.3.4 It may be possible to analyze other amines at the same time.
1.3.5 Interferences may be avoided by proper selection of column and LC parameters.
1.4 Disadvantages
None known
2. Sampling procedure
All safety practices that apply to the work area being sampled should be followed. The sampling equipment should be attached to the worker in such a manner that it will not interfere with work
performance or safety.
2.1 Apparatus
2.1.1 Samples are collected using a personal sampling pump calibrated, with the sampling device attached, to within ±5% of the recommended flow rate.
2.1.2 Samples are collected with 7-cm × 4-mm i.d. × 7-mm o.d. glass sampling tubes packed with two sections (80/40 mg) of XAD-2 resin coated with 10% by weight 1-naphthylisothiocyanate. The
sections are held in place and separated with glass wool plugs. For this evaluation, commercially prepared sampling tubes were purchased from SKC, Inc. (catalog no. 226-30-18).
2.2 Technique
2.2.1 Immediately before sampling, break off the ends of the flame-sealed tube to provide an opening approximately half the internal diameter of the tube. Wear eye protection when breaking ends.
Use tube holders to minimize the hazard of broken glass. All tubes should be from the same lot.
2.2.2 The smaller section of the adsorbent tube is used as a back-up and is positioned nearest the sampling pump. Attach the tube holder to the sampling pump so that the adsorbent tube is in an
approximately vertical position with the inlet facing down during sampling. Position the sampling pump, tube holder and tubing so they do not impede work performance or safety.
2.2.3 Draw the air to be sampled directly into the inlet of the tube holder. The air being sampled is not to be passed through any hose or tubing before entering the sampling tube.
2.2.4 After sampling for the appropriate time, remove the adsorbent tube and seal it with plastic end caps. Seal each sample end-to-end with an OSHA-21 form as soon as possible.
2.2.5 Submit at least one blank sample with each set of samples. Handle the blank sample in the same manner as the other samples except draw no air through it.
2.2.6 Record sample air volumes (liters), sampling time (minutes) and sampling rate (L/min) for each sample, along with any potential interferences on the OSHA-91A form.
2.2.7 Submit the samples to the laboratory for analysis as soon as possible after sampling. If delay is unavoidable, store the samples at refrigerator temperature. Ship any bulk samples separate
from the air samples.
2.3 Desorption efficiency
2.3.1 A loading of 112 µg corresponds to 3.07 ppm based on a 10 liter air volume and a 2 mL desorption volume.
2.3.2 Sampling tubes were spiked with 224, 112, 56, and 11.2 µg AMP. They were allowed to equilibrate at room temperature overnight. They were opened, each section placed in a labeled 4 mL vial,
and 2 mL of dimethylformaide was added. They were allowed to desorb for 30 minutes on a shaker, then analyzed by HPLC. The desorption efficiency averaged
100% (Table 1)
Table 1
Desorption Efficiency (%) AMP
|
tube # |
% Recovered
224 µg |
% Recovered
112 µg |
% Recovered
56 µg |
% Recovered
11.2 µg |
|
1
2
3
4
5
6
average |
101
99.5
98.3
102
99.5
99.1
99.9 |
100
102
99.2
98.4
101
102
100 |
99.4
98.8
101
102
99.6
100
100 |
102
99.3
98.9
101
101
98.5
100 |
|
overall average
standard deviation |
100
±1.29 |
|
|
|
|
2.4 Retention efficiency
2.4.1 Six NITC-coated XAD-2 tubes were spiked with 224 µg (6.15 ppm) of AMP and allowed to equilibrate for 4 h. Each spiked tube was placed in series with a second NITC-coated XAD-2 tube. Each
sampling train had 10-L humid air (80% relative humidity at 22°C) pulled through it at 0.1 L/min. The samples were extracted and analyzed. The mean recovery was 99.8%. There was no analyte found on
the backup section of any of the spiked tubes or on the second tubes.
Table 2
Retention Efficiency (%) of AMP
|
|
|
sample number
|
|
section |
1 |
2 |
3 |
4 |
5 |
6 |
mean |
|
front of spiked
tube
rear of spiked tube
front of series tube
back of series tube
total |
99.8
0.0
0.0
0.0
99.8 |
100
0.0
0.0
0.0
100 |
101
0.0
0.0
0.0
101 |
99.6
0.0
0.0
0.0
99.6 |
98.9
0.0
0.0
0.0
98.9 |
99.6
0.0
0.0
0.0
99.6 |
99.8
0.0
0.0
0.0
99.8 |
|
2.5 Sample storage
2.5.1 Fifteen NITC-coated XAD-2 tubes were each spiked with 112 µg (3.07 ppm) of AMP . They were allowed to equilibrate for 4 h, then 10-L of air ( 80% relative humidity at 23°C), was drawn through
them. Three samples were analyzed immediately. The remaining tubes were sealed and six were stored at room temperature (23 °C), while the other six were stored at refrigerated temperature (4°C).
Three of the samples stored at room temperature and three of the samples stored at refrigerated temperature were analyzed after 7 days and the remaining three of each group after 14 days. The
results indicate good storage stability for the time period studied.
Table 3
Storage Test for AMP
|
time
(days) |
ambient storage
recovery (%) |
|
refrigerated
storage
recovery (%) |
|
0
7
14 |
99.8
100
99.1 |
101
99.5
98.8 |
98.9
99.8
101 |
|
99.8
99.7
99.1 |
101
99.3
98.6 |
98.9
101
100 |
|
2.6 Precision
2.6.1 Precision was calculated using the area counts from six injections of each standard at concentrations of 5.6, 56, and 112 µg/mL AMP (based on a 10 liter air volume and 2 mL desorption volume
these concentrations correspond to 0.31, 3.07, and 6.15 ppm) (Table 4).
Table 4
Precision
|
injection
number |
5.6 µg/mL
0.31 ppm |
5.6 µg/mL
0.31 ppm |
5.6 µg/mL
0.31 ppm |
|
1
2
3
4
5
6
average
standard deviation |
460890
470011
468965
466134
467035
466670
466618
3170 |
4671239
4692392
4689481
4701042
4681923
4690513
4687765
10153 |
9320122
9203344
9319256
9265619
9134092
9234715
9262858
48226 |
|
2.7 Air volume and sampling rate studied
2.7.1 The air volume studied was 10 liters.
2.7.2 The sampling rate studied was 0.1 L/min.
2.8 Interferences (sampling)
2.8.1 There are no known compounds which will severely interfere with the collection of AMP. Other primary and secondary amines will collect on this medium, and form derivatives with the NITC,
affecting the ability of the tube to collect AMP, so sampling time should be adjusted if high concentrations of amines are expected.
2.8.2 Suspected interferences should be reported to the laboratory with submitted samples.
2.9 Safety precautions
2.9.1 Sampling equipment should be paced on an employee in a manner that does not interfere with work performance or safety.
2.9.2 Safety glasses should be worn at all times.
3. Analytical Procedure
Adhere to the rules set down in your Chemical Hygiene Plan. Avoid skin contact and inhalation of all chemicals and review all appropriate MSDSs.
3.1 Apparatus
3.1.1 A liquid chromatograph equipped with a UV detector capable of detecting 254 and 280. The response is most sensitive at 254 nm. For this evaluation, a Waters M-6000A
controller and pump were used,
with a Waters 440 Absorbance Detector, and a Waters 717 plus Autosampler was used.
3.1.2 An LC column capable of separating AMP from the extraction solvent and any potential interferences. A 4.6 × 250 mm column packed with 5-µm Bakerbond cyanopropyl (JT Baker, Phillipsburg, NJ)
was used in the evaluation.
3.1.3 An electronic integrator or some other suitable means of measuring peak areas. A Waters Millennium32 Data System was used in this evaluation.
3.1.4 Glass vials with poly(tetrafluoroethylene)-lined caps. For this evaluation 4-mL vials were used.
3.1.5 A dispenser capable of delivering 2.0 mL of extracting solvent to prepare standards and samples. If a dispenser is not available, a 2.0-mL volumetric pipet may be used.
3.1.6 Volumetric flasks - 10-mL and other convenient sizes for preparing standards.
3.2 Reagents
3.2.1 2-Amino-2-methyl-1-propanol, reagent grade.
3.2.2 N,N-Dimethyl formamide (DMF), reagent grade.
3.2.3 Isopropyl alcohol, HPLC grade.
3.2.4 Isooctane, HPLC grade.
3.2.5 1-Naphthylisothiocyanate (NITC), reagent grade
3.2.6 Mobile phase was 80:20 isooctane:isopropyl alcohol.
3.3 Sample preparation
3.3.1 Remove the plastic end caps from the sample tubes and carefully transfer the adsorbent sections to separate labeled 4-mL vials. Discard the glass tube and glass wool plugs.
3.3.2 Add 2.0 mL of DMF to each vial.
3.3.3 Immediately seal the vials with poly(tetrafluoroethylene)-lined caps.
3.3.4 Agitate the vials on a shaker, or a rotator, for 30 minutes.
3.4 Standard preparation
3.4.1 Freshly prepare two stock standards. A stock standard of 2 mg/mL may be prepared by a) weighing out about 30 mg of NITC in a 10-mL flask, b) weigh out 20 mg AMP by placing the drops on top of the NITC in the flask, and c) weigh out about 30 mg more NITC on top of the AMP, making sure that the AMP is covered on all sides by the NITC. Allow the AMP to react with the NITC for at least 1/2 hour before adding the DMF. Partially fill the volumetric flask with DMF and allow to sit 30 minutes to begin dissolving the derivative, then swirl the contents until all of the solids are dissolved, and fill to the mark with DMF. Do not place the flask in a sonic bath to try to get the derivative to go into solution, as it will destroy the derivative. There must always be an excess of the NITC for the derivative to be completely formed. For example, the amount of NITC needed for the above stock standard would be calculated:
20 mg AMP × (NITC MW=185.25/AMP MW=89.14) = 42 mg
(Note: there should be an excess of NITC to insure that all of it is reacted, so weigh out at least 10 mg extra)
In the above stock standard preparation a total of 60 mg NITC was weighed out so that an excess of NITC was present.
3.3.2 Diluted standards are prepared with a solution of 1 mg/mL NITC in DMF, so that an excess of NITC is always present. Bracket sample concentrations with working standard concentrations. If sample concentrations are higher than the concentration range of prepared standards, either analyze higher standards, or dilute the sample. The higher standards should be at least as high in concentration as the highest sample. Diluted samples should be prepared with a solution of 1 mg/mL NITC in the DMF. The range of standards used in this study was from 0.5 to 224 µg/mL. The instrument is calibrated on the amount of AMP in each standard.
3.5 Analysis
3.5.1 Liquid chromatograph conditions
column: |
Bakerbond cyanopropyl (CN)
column 4.6 × 250 mm |
injection size: |
10 µL |
mobile phase: |
2 mL/min 80:20
isooctane: isopropyl alcohol |
detector: |
UV at 254 and 280 nm |
run time: |
10 min |
retention
times: |
1.8 min NITC
4.2 min DMF
5.2 min AMP |
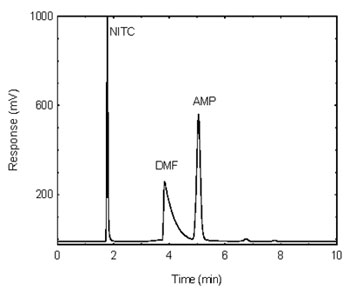
Figure 3.5.1. A chromatogram of 112 µg/mL AMP in DMF with NITC at 254 nm. |
3.5.2 Peak areas are measured by an integrator or other suitable means.
3.5.3 An external standard (ESTD) calibration method is used. A calibration curve can be constructed by plotting response of standard injections versus micrograms of analyte per sample. Bracket
the samples with freshly prepared analytical standards over a range of concentrations.
3.6 Interferences (analytical)
3.6.1 Any compound that produces a LC response and has a similar retention time as the analyte is a potential interference. If any potential interferences were reported, they should be considered
before samples are extracted. Generally, chromatographic conditions can be altered to separate an interference from the analyte.
3.6.2 When necessary, the identity or purity of an analyte peak may be confirmed by a photodiode array scan of the peak, by wavelength ratioing, or by LC/mass spec.
3.7 Calculations
The amount of analyte per sampler is obtained from the appropriate calibration curve in terms of micrograms per sample, uncorrected for extraction efficiency. This total amount is then corrected by
subtracting the total amount (if any) found on the blank. The air concentration is calculated using the following formulas.
|
|
Where: |
CM is concentration by weight
(mg/m3)
M is micrograms per sample
V is liters of air sampled
EE is extraction efficiency, in decimal
|
|
|
Where: |
CV is concentration by volume
(ppm)
VM is molar volume at 25°C and 760 mm = 24.46
CM is concentration by weight
Mr is molecular weight = 89.14 |
4. Recommendations for further study
Collection, reproducibility, and other detection limit studies need to be performed to make this a validated method.
5. References
5.1 Elskamp, C., OSHA Method 60 Ethylenediamine, Diethylenetriamine, and Triethylenetetramine, Organic methods evaluation Branch, OSHA Salt Lake Technical Center, 1986.
5.2 MSDS 2-Amino-2-methyl-1-propanol, Sigma-Aldich Chemical Co., http:www.sigmaaldrich.com (accessed 2/10/92).
5.3 Sax, N.I.; Lewis, R.J.; Hawley’s Condensed Chemical Dictionary, 11th ed., Van Nostrand Reinhold Co., New York, 1987, p 59.
5.4 Budavari, S., Ed., The Merck Index, Merck & Co., Inc., Rahway, NJ, 1989, p 73.
|
|
|