<<< Back to Sampling and Analytical Methods |
Printing Instructions
|
For problems with accessibility in using figures, illustrations and PDF in this method, please contact
the SLTC at (801) 233-4900. These procedures were designed and tested for internal use by OSHA personnel.
Mention of any company name or commercial product does not constitute endorsement by OSHA. |
Ethylene Oxide
[172 KB PDF]
Related Information: Chemical Sampling -
Ethylene Oxide
|
Method no.: |
1010 |
|
|
Control no.: |
T-1010-FV-01-0703-CH |
|
|
Target concentration:
OSHA PEL (TWA):
Excursion Limit:
Action Level:
ACGIH TLV: |
1.0 ppm (1.8 mg/m3)
1.0 ppm (1.8 mg/m3)
5.0 ppm (9 mg/m3) (15 min)
0.5 ppm (0.9 mg/m3)
1.0 ppm (1.8 mg/m3) |
|
|
Procedure: |
Samples are collected by drawing workplace
air through sampling tubes containing hydrobromic acid coated carbon beads
using personal sampling pumps. Samples are extracted with methanol and
analyzed by gas chromatography using an electron capture detector (GC-ECD). |
|
|
Recommended sampling time
and sampling rate:
TWA:
Excursion Limit: |
240 min at 0.05 L/min (12 L)
15 min at 0.05 L/min (0.75 L) |
|
|
Reliable quantitation limit:
TWA:
Excursion Limit: |
9.7 ppb (17.5 μg/m3)
155 ppb (279 μg/m3) |
|
|
Standard error of estimate
at the target concentration: |
5.5% |
|
|
Status of method: |
Evaluated method. This method has been
subjected to the established evaluation procedures of the Methods
Development Team. |
|
|
March 2007 |
Yogi Shah |
|
|
Chromatography
Team
Industrial Hygiene Chemistry Division
OSHA Salt Lake Technical Center
Sandy UT 84070-6406 |
1. General Discussion
For assistance with accessibility problems in using figures and illustrations presented in this method, please contact OSHA Salt Lake
Technical Center (SLTC) at (801) 233-4900. These procedures were designed and tested for internal use by OSHA personnel. Mention of any
company name or commercial product does not constitute endorsement by OSHA.
1.1 Background
1.1.1 History
OSHA Method 501 for ethylene oxide (ETO) was validated in 1985 and specifies collection of ETO using sampling tubes containing petroleum
based charcoal that had been coated with 10% hydrobromic acid (HBr). ETO reacts with HBr to form 2 bromoethanol. 2-Bromoethanol was
extracted from the charcoal with dimethylformamide. An aliquot of the extracted 2-bromoethanol was further derivatized with
heptafluorobutyrylimidazole (HFBI), and then analyzed by gas chromatography using electron capture detection (GC-ECD). The HFBI
derivatization was performed to circumvent analytical problems and had the additional benefit of increasing the sensitivity of the method.
In 2006, the supplier of HBr coated petroleum charcoal sampling tubes informed SLTC that the petroleum charcoal used to prepare the medium
was no longer available. Therefore, another base material was sought to produce the sampling medium. Carbon beads, marketed by SKC, Inc.
as Anasorb 747, was proposed for testing as a replacement base medium because it is a synthetic charcoal that is analogous to petroleum
charcoal. The carbon beads medium was coated with 10% HBr and was found to give excellent performance.
Gas chromatography column technology and electron capture detector sensitivity have advanced since Method 50 was developed in 1985. It was
decided to evaluate the analytical method and attempt to eliminate the time-consuming HFBI derivatization. The analysis in this method was
performed by capillary column GC-ECD, and analytical results show sufficient sensitivity and precision that the second derivatization with
HFBI is no longer necessary.
1.1.2 Toxic effects (This section is for information only and should not be taken as the basis of OSHA policy.)
The basis for OSHA’s ethylene oxide standard, 29 CFR 1910.1047, was a determination by OSHA, based on animal and human data, that exposure to
ETO presents a carcinogenic, mutagenic, genotoxic, reproductive, neurologic and sensitization hazard to workers. OSHA established a
permissible exposure limit for occupational exposure to ETO of 1 ppm, assessed as an 8-hour time-weighted average. The Agency also developed
an excursion limit of 5 ppm, determined during a 15-minute exposure period and also an action level of 0.5 ppm measured as an 8-hour
time-weighted average2.
Acute short-term exposure to ETO causes nausea, headache, weakness, vomiting, drowsiness, incoordination, and irritation of the eyes, nose,
throat, and lungs. Skin contact with ETO solutions can cause severe dermatitis, blisters, edema, burns, and frostbite. Chronic exposure can
cause skin sensitization, loss of the sense of smell, and susceptibility for respiratory infection3.
1.1.3 Workplace exposure
Most ETO is used in the production of other chemicals including ethylene glycol, polyethylene terphthalate polyester, nonionic
surface active agents, glycol ethers, ethanolamines, and choline. Less than 1% of the annual U.S. production is used for
sterilization in the health care and medical products industries4.
The National Institute for Occupational Safety and Health estimated that between 1981 and 1983 270,000 U.S. workers were potentially
occupationally exposed to ethylene oxide. Of this number, 22% were estimated to be exposed to the gas and 78% were exposed to materials
containing ethylene oxide5.
1.1.4 Physical properties and other descriptive information6
synonyms: |
Dihydrooxirene; dimethylene oxide;
1,2-epoxyethane; epoxyethane; ethane oxide; oxaycyclopropane; oxane;
oxidoethane; ETO; EtO |
IMIS7: |
1190 |
CAS number: |
75-21-8 |
boiling point: |
10.8 °C at 760 mmHg (101.3 kPa) |
melting point: |
-111 °C |
density: |
0.882 at 10 °C (liquid) |
molecular weight: |
44.05 |
appearance: |
colorless gas, ether like odor |
vapor density: |
1.5 at 20 °C |
solubility: |
soluble in water, acetone, benzene,
ethanol and diethyl ether |
vapor pressure: |
145.6 kPa at 20 °C |
flammable limit8: |
3-100% by volume in air |
flash point9: |
-2 °C (2% (w/w) in water) |
molecular formula: |
C2H4O |
structural formula: |
 |
This method was evaluated according to the OSHA SLTC "Evaluation Guidelines for Air Sampling Methods Utilizing Chromatographic Analysis".10
The Guidelines define analytical parameters, specify required laboratory tests, statistical calculations and acceptance criteria. The
analyte air concentrations throughout this method are based on the recommended sampling and analytical parameters. Masses of analyte
listed in this method are presented as ETO even though 2-bromoethanol is the actual species analyzed. Air concentrations in ppm are
referenced to 25 °C and 101.3 kPa (760 mmHg).
1.2 Limit defining parameters
1.2.1 Detection limit of the analytical procedure
The detection limit of the analytical procedure is 5.58 pg. This is the amount of ETO that will give a detector response that is
significantly different from the response of a reagent blank. (Section 4.1)
1.2.2 Detection limit of the overall procedure
The detection limit of the overall procedure is 63 ng/sample (2.92 ppb or 5.25 μg/m3). This is the amount of ETO spiked on the sampler
that will give a detector response that is significantly different from the response of a sampler blank. (Section 4.2)
1.2.3 Reliable quantitation limit
The reliable quantitation limit is 210 ng/sample (9.72 ppb or 17.5 μg/m3). This is the amount of ETO spiked on the sampler that will give
a detector response that is considered the lower limit for precise quantitative measurement. (Section 4.2)
1.2.4 Instrument calibration
The standard error of estimate is 0.121 μg over the range of 5.4 to 43.2 μg. This range corresponds to 0.25 to 2 times the target
concentration. (Section 4.3)
1.2.5 Precision
The precision of the overall procedure at the 95% confidence level for the ambient temperature 20-day storage test (at the target
concentration) is ±10.74%. This includes an additional 5% for sampling pump variability. (Section 4.4)
1.2.6 Recovery
The recovery of ETO from samples used in a 20-day storage test remained above 98.6% when the samples were stored at 23 °C. (Section 4.5)
1.2.7 Reproducibility
Six samples were collected from a controlled test atmosphere and submitted for analysis by the OSHA Salt Lake Technical Center.
The samples were analyzed according to a draft copy of this procedure after 9 days of storage at 4 °C. No individual sample
result deviated from its theoretical value by more than the precision reported in Section 1.2.5. (Section 4.6)
2. Sampling Procedure
All safety practices that apply to the work area being sampled should be followed. The sampling equipment should be attached to the
worker in such a manner that it will not interfere with work performance or safety.
2.1 Apparatus
Samples are collected with 7-cm × 4-mm i.d. × 6-mm o.d. glass sampling tubes packed with two sections of HBr coated carbon beads
(HBr-CB). The front section contains 100 mg and the back section contains 50 mg of HBr-CB. The sections are held in place and
separated with glass wool plugs. For this evaluation, commercially prepared sampling tubes were obtained from SKC, Inc.
(catalog no. 226-178).
Samples are collected using a personal sampling pump calibrated, with the sampling device attached, to within ±5% of the recommended
flow rate.
2.2 Reagents
None required
2.3 Technique
Immediately before sampling, break off the ends of the flame-sealed tube to provide an opening approximately half the internal diameter of
the tube. Wear eye protection when breaking the end of the tube. Use tube holders to minimize the hazard of sharp ends of the glass tubes.
All tubes should be from the same lot.
The smaller section of adsorbent in the sampling tube is used as a back-up and is positioned nearest the sampling pump. Attach the
tube holder to the sampling pump so that the adsorbent tube is in an approximately vertical position with the inlet facing down in
the worker’s breathing zone during sampling. Position the sampling pump, tube holder, and tubing so they do not impede work
performance or safety.
Draw the air to be sampled directly into the inlet of the tube holder. The air being sampled is not to be passed through any hose or
tubing before entering the sampling tube.
After sampling for the appropriate time, remove the adsorbent tube and seal it with plastic end caps. Seal each sample end-to-end with a
Form OSHA-21 as soon as possible.
Submit at least one blank sample with each set of samples. Handle the blank sample in the same manner as the other samples except
draw no air through it.
Record sample air volumes (liters), sampling time (minutes), and sampling rate (L/min) for each sample, along with any potential interference
on the Form OSHA-91A.
Submit the samples to the laboratory for analysis as soon as possible after sampling. If delay is unavoidable, store the samples at
refrigerator temperature. Ship any bulk samples separate from the air samples.
2.4 Sampler capacity (Section 4.7)
The sampling capacity of the front section of an HBr-CB sampling tube was tested by sampling a dynamically generated test atmosphere of
ETO (3.65 mg/m3 or 2.0 ppm) at 80% relative humidity and 23 °C. The samples were collected at 0.05 L/min. No breakthrough was observed,
even after sampling for 480 min.
2.5 Extraction efficiency (Section 4.8)
It is the responsibility of each analytical laboratory to determine the extraction efficiency because the adsorbent material,
reagents and laboratory techniques may be different than those listed in this evaluation and influence the results.
The mean extraction efficiency for ETO from dry HBr-CB over the range of RQL to 2 times the target concentration (0.21 to 42.3 µg per
sample) was 97.9%. The extraction efficiency was not affected by the presence of water.
Extracted samples remain stable for at least 24 h.
2.6 Recommended sampling time and sampling rate
Sample for up to 240 min at 0.05 L/min (12 L) to collect TWA (long term) samples.
Sample for 15 min at 0.05 L/min (0.75 L) to collect excursion limit (short-term) samples.
When excursion limit samples are collected, the air concentration equivalent to the reliable quantitation limit becomes larger.
The reliable quantitation limit for excursion samples is 155 ppb (279 μg/m3).
2.7 Interferences, sampling (Section 4.9)
Retention efficiency
The mean retention efficiency was 101.3%, when HBr-CB sampling tubes containing 9.52 µg of ETO were allowed to sample 9 L of
contaminant-free air at 80% relative humidity at 23 °C.
Low humidity
The mean recovery was 98.5% when HBr-CB sampling tubes were used to sample a test atmosphere containing two times the target
concentration of ETO and having a relative humidity of 15% at 21 °C.
Low concentration
The mean recovery was 98.5% when HBr-CB sampling tubes were used to sample a test atmosphere containing 0.1 times the target
concentration of ETO and having a relative humidity of 80% at 23 °C.
Sampling interferences
The mean recovery was 99.5% when HBr-CB sampling tubes were used to sample a test atmosphere containing one times the target
concentration of ETO, 360 mg/m3 (86.3 ppm) of Freon 134 and having a relative humidity of 80% at 22 °C. Freon 134 was tested as a
sampling interference because fluorocarbons are often used to dilute commercial mixtures of ETO.
HBr-CB sampling tubes were used to sample a test atmosphere containing one times the target concentration of ETO at 0.05 L/min for 240 min.
The adsorbent from these tubes was placed into glass vials that were spiked with 2 mL of 25ppm ethylene gas. The samples were left to
equilibrate for 2 days and then analyzed. The mean recovery of ETO was 100.8%. Ethylene gas was selected for testing as a sampling
interference because it is used to produce ETO.
3. Analytical Procedure
Adhere to the rules set down in your Chemical Hygiene Plan11. Avoid skin contact and inhalation of all chemicals and review all
appropriate
MSDSs before beginning the analytical procedure.
3.1 Apparatus
Gas chromatograph equipped with an electron capture detector (ECD). An Agilent Model 6890 GC equipped with an integrator, an automatic
sample injector, and an ECD was used in this evaluation.
A GC column capable of separating 2-bromoethanol from the extraction solvent. A J&W Scientific DB-5, 60-m × 0.32-mm i.d., (1-µm df)
capillary column was used in this evaluation.
An electronic integrator or other suitable means of measuring GC detector response. A Waters Empower 2 Data System was used in this
evaluation.
Glass vials with PTFE-lined caps. Two-milliliter vials were used in this evaluation.
A dispenser or pipette capable of delivering 1.0 mL of extracting solvent to prepare standards and samples.
Class A volumetric flasks - 1-mL and other convenient sizes for preparing standards.
Calibrated 10-μL syringe for preparing standards.
A mechanical shaker. An Eberbach mechanical shaker was used to extract the ETO derivative from HBr-CB in this evaluation.
3.2 Reagents
Methyl alcohol [CAS no. 67-56-1], reagent grade. The methyl alcohol used in this evaluation was 99.9+% (lot no. 050340) purchased from
Fisher Scientific.
2-Bromoethanol [CAS no. 540-51-2], reagent grade. The 2-bromoethanol used in this evaluation was 97% (lot no. A014388401) purchased from
Acros Organics.
The extraction solvent used for this evaluation was neat methanol.
3.3 Standard preparation
Prepare a concentrated stock standard of 2-bromoethanol in methanol. Prepare working analytical standards by diluting this stock standard
with methanol delivered from the same dispenser used to extract the samples. For example: prepare a 2× target level stock standard
(2 ppm) by injecting 7.0 μL of 2-bromoethanol into a 1-mL volumetric flask containing about 0.5 mL of methanol and then diluting to the
mark with methanol. Prepare a working standard by spiking 10.0 μL of the stock standard into 1.0 mL of methanol delivered from the same
dispenser used to extract samples.
MW of ETO is 44.05 and for 2-bromoethanol is 124.97.
(7.0 μL × 1.76 mg/μL x 0.97 (purity) × 44.05/124.97)/1.00 mL = 4.21 mg/mL as ETO
(10.0 μL × 4.21 mg/mL × mL/1000 μL × 1000 μg/mg/(1.01 mL) = 41.68 μg/mL as ETO
Bracket sample concentrations with standard concentrations. If upon analysis, sample concentrations fall outside the range of prepared
standards, prepare and analyze additional standards to confirm instrument response, or dilute high samples with methanol and reanalyze
the diluted samples.
3.4 Sample preparation
Remove the plastic end caps from the sample tube and carefully transfer the front section of HBr-CB along with the front glass wool
plug to a 2-mL vial. Transfer the center glass wool plug and back-up section of HBr-CB to a separate 2-mL vial. Discard the glass
tube.
Add 1.0 mL of methanol to each vial and immediately seal the vials with PTFE-lined caps.
Shake the vials on a shaker for 30 min. Shaking is recommended to obtain complete sample extraction.
3.5 Analysis
GC conditions:
|
|
column: |
initial 100 °C, hold 9 min,
program at 5 °C/min to 150 °C, hold 1 min |
injector: |
200 °C |
detector: |
250 °C |
run time: |
20 min |
column gas flow: |
2.1 mL/min (hydrogen) |
injection size: |
1.0 µL (20:1 split) |
column: |
DB-5 60-m × 0.32 mm i.d.
capillary (df = 1.0 µm) |
|
|
Note: Periodically
check the injection port liner for contamination built up. |
|
|
ECD conditions:
|
|
constant makeup
mode |
nitrogen makeup flow: |
40 mL/min |
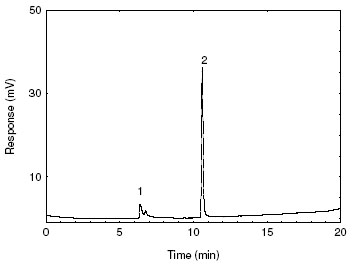
Figure 3.5.1. A chromatogram of 2-bromoethanol at 21.2 µg/mL in methanol.
[Key: 1) methanol, 2) 2-bromoethanol] |
|
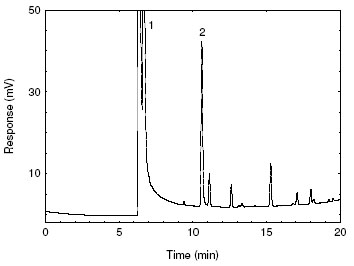
Figure 3.5.2. A chromatogram of 2-bromoethanol at 21.2 µg/mL in methanol
with HBr-CB added to show impurities from the medium. [Key: 1) methanol and
HBr, 2) 2-bromoethanol] |
An external standard calibration method is used. A calibration curve can be constructed by plotting response of standard injections versus
micrograms of analyte per sample. Bracket the samples with freshly prepared analytical standards over the range of concentrations.
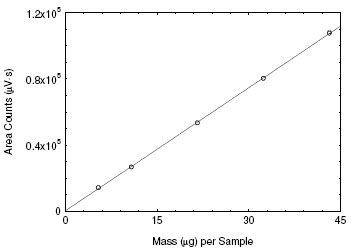
Figure 3.5.3. Calibration curve for ETO. (y = 2484x + 209) |
3.6 Interferences (analytical)
Any compound that produces an ECD response and has a similar retention time as 2-bromoethanol is a potential interference. If any
potential interferences were reported, they should be considered before samples are extracted. Generally, chromatographic conditions
can be altered to separate an interference from the analyte.
When necessary, the identity or purity of an analyte peak can be confirmed with additional analytical data. (Section 4.10)
3.7 Calculations
The amount of analyte per sample is obtained from the appropriate calibration curve in terms of micrograms per sample, uncorrected for
extraction efficiency. The back section is analyzed primarily to determine the extent of sampler saturation. If any analyte is found
on the back section, it is added to the amount on the front section. The total amount is then corrected by subtracting the combined
amount (if any) found on the front and back sections of the blank. The air concentration is calculated from the total amount using the
following formulas.
CM = |
M |
Where |
CM is concentration by weight
(mg/m3)
M is micrograms per sample
V is liters of air sampled
EE is extraction efficiency in decimal form |
|
VEE |
|
|
|
CV = |
VMCM |
Where |
CV is concentration by volume (ppm)
VM is 24.46 (molar volume at NTP)
CM is concentration by weight (mg/m3)
Mr is molecular weight = 44.05 |
|
Mr |
4. Backup data
General background information about the determination of detection limits and precision of the overall procedure is found in the "Evaluation
Guidelines for Air Sampling Methods Utilizing Chromatography Analysis"12. The Guidelines define analytical parameters specify
required laboratory tests, statistical calculations and acceptance criteria.
4.1 Detection limit of the analytical procedure (DLAP)
DLAP is measured as the mass of analyte introduced onto the chromatographic column. Ten analytical standards were prepared with equally
descending increments with the highest standard containing 1.32 µg/mL. This is the concentration that would produce a peak approximately 10
times the response of a reagent blank near the elution time of the analyte. These standards, and the reagent blank were analyzed with the
recommended analytical parameters (1-µL injection with a 20:1 split), and the data obtained were used to determine the required parameters
(standard error of estimate and slope) for the calculation of the DLAP. Values of 125 and 232 were obtained for the slope and standard error
of estimate respectively. DLAP was calculated to be 5.58 pg.
Table 4.1
Detection Limit of the Analytical Procedure
|
|
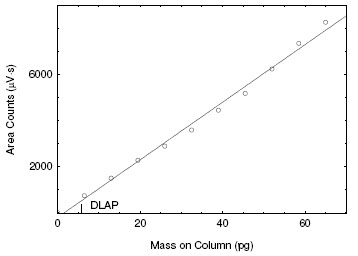
Figure 4.1. Plot of data to determine the DLAP. (y = 125x - 197) |
concentration (µg/mL) |
mass on column (pg) |
area counts
(µV∙s) |
|
0
0.13
0.26
0.39
0.52
0.65
0.78
0.91
1.04
1.17
1.32 |
0.0
6.5
13.0
19.5
26.0
32.5
39.0
45.5
52.0
58.5
65.0 |
0
740
1500
2284
2893
3585
4453
5175
6238
7345
8264 |
|
4.2 Detection limit of the overall procedure (DLOP) and reliable quantitation limit (RQL)
DLOP is measured as mass per sample and expressed as equivalent air concentrations, based on the recommended sampling parameters. Ten
samplers were spiked with equally descending increments of analyte, such that the highest sampler loading was 1.32 µg/sample. This is the
amount spiked on a sampler that would produce a peak approximately 10 times the response of a sample blank. These spiked samplers, and the
sample blank were analyzed with the recommended analytical parameters, and the data obtained used to calculate the required parameters
(standard error of estimate and the slope) for the calculation of the DLOP. Values of 6172 and 130 were obtained for the slope and standard
error of estimate respectively. The DLOP for ETO was calculated to be 63 ng/sample (2.92 ppb or 5.25 μg/m3).
Table
4.2
Detection Limit of the Overall Procedure
|
|
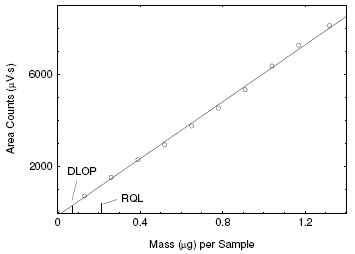
Figure 4.2.1. Plot of data to determine the DLOP/RQL.
(y = 6172x – 136) |
mass per sample
(µg) |
area counts
(µV∙s)
|
|
0
0.13
0.26
0.39
0.52
0.65
0.78
0.91
1.04
1.17
1.32 |
0
712
1518
2290
2932
3747
4525
5320
6353
7252
8110 |
|
The RQL is considered the lower limit for precise quantitative measurements. It is determined from the regression line parameters obtained
for the calculation of the DLOP, providing 75% to 125% of the analyte is recovered. The RQL was 210 ng/sample (9.7 ppb or 17.5 μg/m3).
The recovery at this level was 99.9%. A chromatogram of the RQL is shown in Figure 4.2.2, and a chromatogram of sampler blank is shown in
Figure 4.2.3.
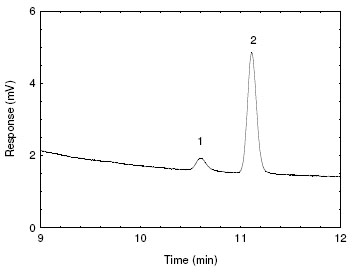
Figure 4.2.2. Chromatogram of the RQL.
[Key: 1) 2-bromoethanol, 2) impurity] |
|
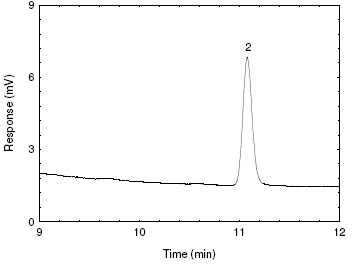
Figure 4.2.3. Chromatogram of blank HBr-CB.
[Key: 2) impurity] |
4.3 Instrument calibration
The standard error of estimate was determined from the linear regression of data points from standards over a range that covers 0.25 to 2
times the TWA target concentration. A calibration curve was constructed and shown in Section 3.5 from the three injections of five
standards. The standard error of estimate is 0.121 µg.
Table 4.3
Instrument Calibration
|
×OSHA PEL
μg/mL |
0.25×
5.4 |
0.5×
10.8 |
1.0×
21.6 |
1.5×
32.4 |
2.0×
43.2 |
|
area
counts
(μV∙s) |
14230
14187
14329 |
26684
26783
26645 |
53374
53487
53380 |
80390
80450
80334 |
107770
108450
107689 |
|
4.4 Precision (overall procedure)
The precision at the 95% confidence level is obtained by multiplying the standard error of estimate by 1.96 (the z-statistic from the standard normal distribution at the 95% confidence level). In Section 4.5, 95% confidence intervals are drawn about their respective regression lines in the storage graph figures. The precision of the overall procedure of ±10.74% was obtained from the standard error of estimate of 5.48% in Figure 4.5.1. The precision includes an additional 5% for sampling error.
4.5 Storage test
Storage samples for ETO were prepared by collecting samples from a controlled test atmosphere using the recommended sampling conditions. The concentration of ETO was at the target concentration and the relative humidity was 80% at 23 °C. Thirty-three storage samples were prepared. Three samples were analyzed on the day of generation. Fifteen of the samples were stored at reduced temperature (4 °C) and the other fifteen were stored in a closed drawer at ambient temperature (about 23 °C). At 2-5 day intervals, three samples were selected from each of the two storage sets and analyzed. Sample results are not corrected for extraction efficiency.
Table 4.5
Storage Test for ETO
|
time
(days) |
ambient storage
recovery (%) |
refrigerated
storage
recovery (%) |
|
0
4
7
11
15
20 |
99.8
97.7
96.3
100.7
97.2
97.8 |
99.2
97.9
101.4
103.9
98.8
98.6 |
101.0
100.7
104.3
100.9
97.2
98.1 |
96.4
98.6
96.9
102.1
95.5 |
101.4
105.3
102.8
104.7
101.5 |
100.9
103.3
101.8
98.5
102.6 |
|
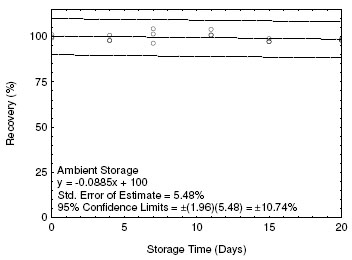
Figure 4.5.1. Ambient storage for ETO. |
|

Figure 4.5.2. Refrigerated storage test for ETO. |
4.6 Reproducibility
Six samples were collected from a controlled test atmosphere
similar to that which was used in the collection of the storage samples.
The samples were submitted to the OSHA Salt Lake Technical Center for
analysis, along with a draft copy of this method. The samples were
analyzed after being stored for 17 days at 4 °C. Sample results were
corrected for extraction efficiency. No sample result for ETO had a
deviation greater than the precision of the overall procedure determined
in Section 4.4. |
|
Table 4.6
Reproducibility Data for ETO
|
theoretical
(μg/sample)
|
recovered
( μg/sample) |
recovery
(%) |
deviation (%) |
|
21.78
21.83
22.60
21.87
21.50
21.88 |
21.24
20.87
23.27
22.20
22.60
22.19 |
97.5
95.6
102.9
101.5
105.1
101.4 |
-2.5
-4.4
2.9
1.5
5.1
1.4 |
|
4.7 Sampler capacity
The sampling capacity of the front section of an HBr-CB sampling tube was tested by sampling a test atmosphere containing twice the PEL
of ETO (3.65 mg/m3 or 2.0 ppm) with a relative humidity of 80% at 21 °C. Sampling trains were prepared by removing the back sections of
three sampling tubes and connecting each front section tube to a complete HBr-CB sampling tube. Sampling was begun and the back tubes
were changed after sampling for 4, 5, 6, 7, and 8 hours at 0.05 L/min. No breakthrough was observed for any of the sampling trains;
therefore, sampler capacity was never exceeded. This test was repeated and similar results were obtained.
4.8 Extraction efficiency and stability of extracted samples
The extraction efficiency is dependent on the extraction solvent. Other extraction solvents can be used provided that the new extraction
solvent is tested. The new extraction solvent should be tested as described below.
Extraction efficiency
The extraction efficiencies of ETO were determined by liquid-spiking four HBr-CB sampling tubes at each concentration level with
2-bromoethanol from the RQL to 2 times the target concentration. These samples were stored overnight at ambient temperature and
then analyzed. The mean extraction efficiency over the working range of the RQL to 2 times the target concentration is 97.9%. The
extraction efficiency for the wet medium was not included in the overall mean because it would bias the results. Wet medium was
prepared by pulling 12 L of 80% humid air at 21 °C through sampling tubes.
Table 4.8.1
Extraction Efficiency (%)
|
level
|
sample
number
|
mean
|
× target
concn |
µg per
sample |
1 |
2 |
3 |
4 |
|
|
RQL
0.25
0.5
1.0
1.5
2.0
1.0 (wet) |
0.210
5.29
10.59
21.17
31.76
42.34
21.17 |
100.5
93.2
93.4
99.9
94.8
95.8
96.5 |
101.7
97.2
96.0
100.4
94.7
98.2
99.7 |
100.8
97.9
99.0
100.2
96.0
102.4
103.9 |
96.4
97.6
95.5
100.2
98.2
99.6
100.9 |
99.9
96.5
95.9
100.2
95.9
99.0
100.3 |
|
Stability of extracted samples
The stability of extracted samples was investigated by reanalyzing the target concentration samples 24 h after initial analysis. After the
original analysis was performed two vials were recapped with new septa while the remaining two retained their punctured septa. The samples
were reanalyzed with fresh standards. The average percent change was 102.2% for samples that were resealed with new septa and 98.2% for
those that retained their punctured septa. Each septum was punctured 5 times for each injection.
Table 4.8.2
Stability of Extracted Samples for ETO
|
punctured septa
replaced
|
punctured septa
retained
|
initial
(%) |
after one day (%) |
difference
(%) |
initial
(%) |
after one day (%) |
difference
(%) |
|
99.9
100.4
100.2 |
100.7
103.6
(mean)
102.2 |
0.8
3.2
2.0 |
100.2
100.2
100.2 |
98.7
97.6
(mean)
98.2 |
-1.5
-2.6
-2.0 |
|
4.9 Interferences (sampling)
Retention
The ability of HBr-CB sampling
tubes to retain ETO after it has been collected was tested by sampling an
atmosphere containing 3.22 mg/m3 (1.79 ppm) of ETO at a relative
humidity of 80% at 23 °C. Six samplers had contaminated air drawn through
them at 0.05 L/min for 60 min. Sampling was discontinued and three samples
were set aside. The generation system was flushed with contaminant-free air.
Sampling resumed with the other three samples having contaminant-free air
drawn through |
|
Table 4.9
Retention of ETO
|
|
percent recovery
(%) |
set |
1 |
2 |
3 |
mean |
|
first
second
second/first |
101.8
100.2
98.4 |
95.5
100.9
105.6 |
98.5
98.3
99.8 |
98.6
99.8
101.3 |
|
them at 0.05 L/min for 180 min and then all six samplers
were analyzed. The mean of the samples in the second set had retained more than 101% of the
mean collected by the first three samples. |
Low humidity
The ability of HBr-CB sampling tubes to collect ETO from a relatively dry atmosphere was tested by sampling an atmosphere containing
3.22 mg/m3 (1.79 ppm) of ETO at a relative humidity of 15% at 21 °C. Three samplers had contaminated air drawn through them at 0.05
L/min for 240 min. All of the samples were immediately analyzed. The samples had collected 95.8%, 101.5% and 98.3% of theoretical.
Low concentration
The ability of HBr-CB sampling tubes to collect ETO at low concentration was tested by sampling an atmosphere containing 0.198 mg/m3
(0.11 ppm) of ETO at a relative humidity of 80% at 23 °C. Three samplers were collected by drawing air through them at 0.05 L/min for
240 min. All of the samples were immediately analyzed. The samples had collected 96.0%, 99.5% and 100.0% of theoretical.
Interference
The ability of HBr-CB sampling tubes to collect ETO was tested when another potential interference was present by sampling an
atmosphere containing 360 mg/m3 of Freon 134 and 1.79 mg/m3 (1 ppm) of ETO at a relative humidity of 80% at 23 °C. Three samples
were collected at 0.05 L/min for 240 min. All of the samples were immediately analyzed. The samples had collected 98.2%, 100.5% and
99.7% of theoretical. There was no ETO on the backup portion of the sampling tubes.
In another test, three HBr-CB sampling tubes were used to sample an atmosphere containing 1.8 mg/m3 (1 ppm) ETO and 80% relative
humidity at 23 °C at 0.05 L/min for 240 min. The sampling media were transferred to glass vials and each vial was spiked with 2 mL of
25 ppm ethylene gas. All of the samples were analyzed after 2 days. The recoveries were 99.9%, 104.6% and 97.8% of theoretical.
This test showed that ethylene gas did not form a reaction product with HBr that interfered with the analysis of ETO.
4.10 Qualitative analysis
When necessary, the identity or purity of an analyte peak can be confirmed by GC-mass spectrometry or by another analytical procedure.
A mass spectrum for 2-bromoethanol is shown in Figure 4.10.
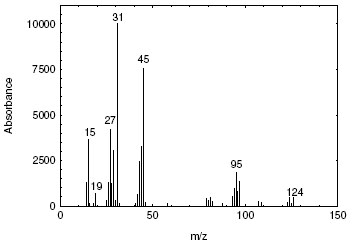
Figure 4.10. Mass spectrum of 2-bromoethanol. |
4.11 Generation of test atmospheres
A test atmosphere generator, as diagramed in Figure 4.11, was set up in a
walk-in hood. House air was dried, purified and then regulated using a
Miller Nelson Model 401 Flow-Temperature-Humidity Control System. A
measured flow of certified standard ETO gas was introduced into a measured
flow of dilution air coming from the Miller Nelson control system. The ETO
gas and dilution air flowed into a mixing chamber (76-cm X 15-cm) and then
into a sampling chamber (56-cm X 9.5-cm). Samples were collected through
sampling ports on the sampling chamber. Temperature and humidity were
measured near the exit of the sampling chamber using an Omega Digital
Thermo-hygrometer model RH411. ETO (1000 ppm in nitrogen certified
standard) used in this evaluation was purchased from SPECGAS INC, Ivy
land, PA 18974. |
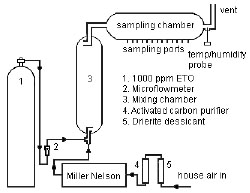
Figure 4.11. Diagram of apparatus used to generate ETO test atmospheres. |
References
1. Cummins, K.
Ethylene Oxide. (accessed 2006), OSHA Salt Lake Technical Center, U.S. Department of Labor: Salt Lake City, UT, 1985.
2.
Occupational Exposure to Ethylene Oxide; Final Standard- Federal Register #
49:25734. (accessed 2/2007), OSHA Salt Lake Technical Center, U.S. Department of Labor: Salt Lake City, UT.
3. Ethylene Oxide. Documentation of the Threshold Limit Values and Biological Exposure Indices, 7th ed.; American Conference of Governmental Industrial Hygienists, Inc.: Cincinnati, OH, 2001; Vol. 2.
4. Ethylene Oxide. Documentation of the Threshold Limit Values and Biological Exposure Indices, 7th ed.; American Conference of Governmental Industrial Hygienists, Inc.: Cincinnati, OH, 2001; Vol. 2.
5. International Agency for Research on Cancer, IARC Monographs on the Evaluation of Carcinogenic Risks to Humans, Some Industrial Chemicals, Vol. 60, Ethylene Oxide, IARC: Lyon, France, 1994, pp 73-159.
6. International Agency for Research on Cancer: ETHYLENE OXIDE, IARC Monographs on Evaluation of Carcinogenic Risk in Chemicals to Humans, Some Industrial chemicals and Dyestuffs, IARC,Lyon, France Vol 29, 1982 pp 73-83.
7.
Ethylene Oxide.
OSHA Chemical Sampling Information, (accessed 2/2007).
8. Ethylene Oxide. Documentation of the Threshold Limit Values and Biological Exposure Indices, 7th ed.; American Conference of Governmental Industrial Hygienists, Inc.: Cincinnati, OH, 2001; Vol. 2.
9. Ethylene Oxide. Documentation of the Threshold Limit Values and Biological Exposure Indices, 7th ed.; American Conference of Governmental Industrial Hygienists, Inc.: Cincinnati, OH, 2001; Vol. 2.
10. Burright, D.; Chan, Y.; Eide, M.; Elskamp, C.; Hendricks, W.; Rose, M. C.
Evaluation Guidelines For Air Sampling Methods Utilizing Chromatographic
Analysis. (accessed August 2006), OSHA Salt Lake Technical Center, U.S. Department of Labor: Sandy UT, 1999.
11. Occupational Exposure to Hazardous Chemicals in Laboratories. Code of Federal Regulations, Part 1910.1450, Title 29, 1998.
12. Burright, D.; Chan, Y.; Eide, M.; Elskamp, C.; Hendricks, W.; Rose, M. C.
Evaluation Guidelines For Air Sampling Methods Utilizing Chromatographic
Analysis. (accessed August 2006), OSHA Salt Lake Technical Center, U.S. Department of Labor: Sandy UT, 1999.
|
|
|