|
 |
U. S. Department of Labor
Occupational Safety and Health Administration
Directorate of Science, Technology and Medicine
Office of Occupational Medicine
|
Respiratory Disease Among Employees in
Microwave Popcorn Processing Plants
|
Safety and Health Information Bulletins |
|
SHIB 09-24-07 |
This Safety and Health Information Bulletin is not a standard or regulation, and it creates no new legal obligations. The Bulletin contains both
recommendations and descriptions of relevant mandatory safety and health standards. The recommendations are advisory in nature,
informational in content, and are intended to assist employers in providing a safe and healthful workplace. Pursuant to the Occupational Safety
and Health Act, employers must comply with safety and health standards promulgated by OSHA or by a state with an OSHA-approved state plan.
In addition, pursuant to Section 5(a)(1), the General Duty Clause of the Act, employers must provide their employees with a workplace free
from recognized hazards likely to cause death or serious physical harm. Employers can be cited for violating the General Duty Clause if there is a
recognized hazard and they do not take reasonable steps to prevent or abate the hazard. However, failure to implement any specific recommendation
in this Safety and Health Information Bulletin is not, in itself, a violation of the General Duty Clause. Citations can only be based on standards,
regulations, and the General Duty Clause. |
Purpose
The purpose of this Safety and Health Information Bulletin (SHIB) is to:
- Provide employees and employers in the microwave popcorn industry with
information about the potential health effects associated with exposure to butter flavorings.
- Recommend exposure controls that may be implemented by employers and used by employees at these facilities to reduce
exposures to butter flavorings.
- Inform employers of applicable mandatory OSHA standards.
Background
In 2000, the Missouri Department of Health and Senior Services (MDHSS) and the National Institute for Occupational Safety and Health
(NIOSH) conducted an investigation of a microwave popcorn processing facility where eight former employees had been diagnosed with a rare
lung disease called bronchiolitis obliterans. A ninth case was discovered later in the same Jasper, Missouri plant. All nine individuals were employed
at this microwave popcorn production facility for eight months to 17 years. They first noticed breathing problems five months to nine years
(median, 1.5 years) after starting work at this facility. Five of the former employees had worked in the mixing room where butter flavorings and oil
are mixed. The other four had worked on the packaging lines where popcorn and the oil/flavorings mixture are added to microwaveable
bags and packaged for shipment. The employees reported similar symptoms, including progressive shortness of breath, persistent cough, and unusual
fatigue. Five of the nine employees were placed on a lung transplant candidate list [1]. One of the employees died in April 2006 without receiving a
lung transplant. She had worked for 18 months at the plant during the mid-1990s.
Using information supplied by the employer for the eight original cases, the initial incidence of disease for the microwave popcorn mixing and packaging
areas was determined. The four ill employees who worked in the mixing area represented 31 percent
of the estimated 13 employees who worked in that area between 1992 and 2000. The other four ill
employees worked on the packaging line (they never worked as mixers) and represented
1.4 percent of the estimated 272 employees who worked in this area between 1992 and 2000.
Based on the results of their initial investigation, NIOSH researchers concluded that the bronchiolitis obliterans identified in the eight
former employees was most likely caused by occupational exposure to volatile butter-flavoring
ingredients. Diacetyl, a butter-flavoring chemical, was the predominant chemical isolated from air
samples in the facility and was used as a marker for volatile organic compounds (VOC) exposure
during the investigation of the Jasper plant [2]. To protect employees during the initial and subsequent
phases of the investigation, NIOSH and MDHSS recommended the installation and use of exposure
controls in the facility. These controls included general dilution ventilation, local exhaust
ventilation of tanks that contained butter flavorings, process isolation, and personal
protective equipment (respiratory, skin and eye protection). NIOSH evaluated data from several
follow-up medical and environmental surveys at this facility to assess the effects of these exposure
controls on employee health. NIOSH’s investigation and findings are summarized
later in this SHIB. NIOSH has published an Alert on flavorings-related lung disease [3] and has a
Safety and Health Topic page with additional references on this subject on its Web site [4].
Additional cases of lung disease characterized by fixed airways obstruction, including bronchiolitis
obliterans, have been recognized among employees at other microwave popcorn plants as well as
among those who manufacture flavorings for foods outside the microwave popcorn manufacturing
industry [3,
5]. A survey by NIOSH at five other microwave popcorn plants with five to 206
employees identified six additional employees with clinical findings consistent with bronchiolitis
obliterans. These involved one mixer at each of three plants and three packaging line employees at
a fourth plant [5]. Analysis of air samples for diacetyl at the plants where these six employees
worked indicated lower mean concentrations than those found in comparable areas of the Jasper plant
– 0.6 ppm (1.6 percent of the mean in Jasper) or less in the mixing areas for the three mixers and 0.3
ppm (16 percent of the mean in Jasper) in the packaging area for the three packagers [5]. These
cases occurred at lower levels of diacetyl than those initially measured in the Jasper plant.
NIOSH investigators have stated that "[a]t this time, insufficient data exist on which to base
workplace exposure standards or recommended exposure limits for butter flavorings"[5].
However, in the same paper, they also cautioned that, because safe levels of occupational exposure
to butter-flavoring chemicals have not been determined, "it is important to limit worker
exposures as much as possible"[5].
Fixed Airways Obstruction and Bronchiolitis Obliterans
The lung disease identified in the NIOSH investigations is usually characterized by
spirometry (lung or pulmonary function tests, PFT) findings of fixed airways obstruction although
some employees have also had findings of restriction, a decreased ability to expand the lungs.
Airways obstruction is diagnosed when the person tested has difficulty blowing air out of the lungs. A
fixed obstruction means that there is no improvement in lung function even after
administration of asthma medication (i.e., bronchodilators). Symptoms of fixed airways
obstruction include cough, fatigue, and shortness of breath with exertion. Symptoms usually have a
gradual onset, but in some cases severe symptoms have occurred suddenly with rapid progression of
lung disease. Symptoms generally do not improve when employees go home for the weekend or go
on vacation. In some instances, lung function tests have indicated that employees had fixed airways
obstruction even in the absence of respiratory symptoms [3].
Some employees identified in the NIOSH investigations have been diagnosed with
bronchiolitis obliterans, a rare, potentially lifethreatening lung disease characterized by cough,
shortness of breath with exertion, and spirometry findings of fixed airways obstruction [1,
6]. In
constrictive bronchiolitis obliterans, the smallest airways of the lung become inflamed and scarred,
resulting in thickening and narrowing of the airways. Established occupational risk factors for
development of bronchiolitis obliterans include inhalation of toxic fumes, grain dusts, mineral
dusts, and irritant gases [3,
7].
In the NIOSH investigation, employees with severe fixed airways obstruction, including bronchiolitis
obliterans, have not improved with treatment (e.g., corticosteroid medications). Some employees
diagnosed with fixed airways obstruction noticed gradual improvement in their cough several years
after removal from the flavoring exposure, but their pulmonary function never improved and their
shortness of breath with exertion persisted. Some affected employees have developed severe,
disabling lung disease and have been placed on lung transplant waiting lists [1].
Description of Hazard
Process Description
In August 2000, NIOSH carried out its first evaluation of a microwave popcorn manufacturing
facility at a plant located in Jasper, Missouri. Seven additional surveys of the plant were
conducted from April 2001- August 2003 and the final report was published in January 2006 [8].
The plant has been in operation since 1986 and packages popcorn (microwave and plain popcorn
kernels) for both national and international distribution. Whole kernel corn from Missouri and
Nebraska is air cleaned on arrival, treated with an organophosphate insecticide, and transferred to
silos. From the silo, the corn is processed by screening and air cleaning on a gravity table. The
corn is then sent to either the polyethylene packaging area or the microwave production area.
In the polyethylene packaging area, corn is packaged in polyethylene bags by machine without
the addition of flavorings or additives. After packaging, the bags are boxed, stacked, wrapped
in plastic, and transported to the warehouse by a forklift.
In the microwave production area, the corn is prepared and packaged using a series of steps. In
the flavor mixing area - where five of the ill former employees worked - salt, butter flavorings, and
coloring agents are mixed by a single person and manually added to a large tank of heated soybean
oil. This process produces visible dust, aerosols, and vapors with a strong buttery odor. Following
mixing, the oil/flavoring mixture is piped into holding tanks in the packaging area and maintained
at a temperature of 140°F to keep the mixture from solidifying. In the packaging area – where the
other four employees worked – the oil/flavoring mixture and the kernel popcorn are added to
microwavable bags, and the bags are then wrapped in plastic and placed into boxes for distribution.
The boxes are stacked on pallets and enclosed in plastic wrap. The pallets are sent to the
warehouse. Management and clerical staff work in an office physically removed from the microwave
production area.
NIOSH Investigation
To evaluate the health condition of the employees in the Jasper plant, NIOSH collected health
information using a questionnaire and performed pulmonary function testing. Using the pulmonary
function test data, NIOSH found that the number of employees with airways obstruction on a
spirometry test was 3.3 times higher than expected, compared to national data. This discrepancy
increased to 10.8 times higher than expected for current employees who had never smoked. Results
from the health survey indicated that the number of individuals with physician-diagnosed asthma and
chronic bronchitis was about two times higher than expected from national data, and the number of
non-smokers with chronic bronchitis was 3.3 times higher than expected [8].
In November 2000, NIOSH collected air samples throughout the plant and analyzed them for volatile
organic compounds (VOCs), respirable dusts, endotoxin, bacteria, and fungi. Results from air
samples collected in the flavor mixing area indicated the presence of over 100 VOCs at
various concentrations [8]. None of the compounds identified in these samples or those
collected in the rest of the plant were known to cause bronchiolitis obliterans. Several VOCs were
present in relatively high levels in the flavor mixing area including: diacetyl, methyl ethyl ketone, 2-
nonanone, acetoin, acetaldehyde, and acetic acid. With the exception of one sample, which indicated
an acetic acid concentration of 12.4 parts pe million (ppm), all VOCs with established OSHA
PELs as well as respirable particulates (particulates not otherwise regulated or PNOR), were well
below their respective PELs. OSHA PELs are expressed as 8-hour time-weighted averages
(TWA). The 8-hour TWA PELs for acetic acid, acetaldehyde, and methyl ethyl ketone are 10 ppm,
200 ppm, and 200 ppm, respectively (29 CFR 1910.1000). The 8-hour TWA PEL for respirable
particulates is 5 milligrams per cubic meter (mg/m3) (29 CFR 1910.1000).
Diacetyl - a chemical with butter-flavoring characteristics - was the most predominant VOC
identified in air samples taken in the Jasper plant. Diacetyl levels were measured and used as an
indicator (marker) for exposure to volatile butter flavorings during investigations of working areas of
the plant [8,
9]. Area sample results indicated that diacetyl concentrations ranged from below the limit
of detection to 97.9 ppm. The mean concentration was the highest in the flavor mixing area and was
calculated as 37.8 ppm [8]. Diacetyl concentrations in the flavor mixing area were about
1,000 times higher than in the office and outdoor areas; about 100 times higher than in the
polyethylene packaging, warehouse, maintenance and quality control areas; and about 17 times
higher than in the microwave packaging area [8]. Diacetyl does not have an OSHA PEL or a NIOSH
Recommended Exposure Limit (REL).
NIOSH ranked the employees who provided health information and completed a pulmonary function
test in four groups according to their cumulative diacetyl exposure. Cumulative exposure was
estimated using work history and the air sampling data obtained by NIOSH. NIOSH found that there
was a statistically significant, positive relationship between cumulative exposure to diacetyl and the
proportion of employees (prevalence) with airways obstruction – as the cumulative diacetyl exposure
increased, the prevalence of airways obstruction increased. NIOSH concluded that the investigation
in the Jasper plant "revealed a risk for occupational lung disease in workers with inhalation exposure to
butter-flavoring chemicals" [3].
NIOSH recommended the installation and use of engineering controls, work practices, and respiratory protection. Controls implemented at
the Jasper plant resulted in a marked reduction in diacetyl levels in the mixing room, from a mean of
38 ppm in November 2000 to 0.46 ppm in July 2003. NIOSH conducted seven additional surveys
while control measures were being implemented in the facility. Engineering controls such as isolation
of the mixing processes and the heating tanks appeared to protect most employees that were part
of the follow-up investigations [9]. NIOSH’s January 2006 final report of the Jasper plant
investigation states that analysis of the data from these surveys does "provide some indication that
control of exposures to butter-flavoring chemicals has decreased the risk to most workers" [8].
NIOSH evaluated employee exposure to butter flavorings in investigations of six microwave
popcorn plants including the Jasper plant. Cases of fixed airways obstruction with clinical findings
consistent with bronchiolitis obliterans were identified in five out of the six plants. The mean
airborne concentrations of diacetyl in mixing areas with affected employees (either personal or area
measurements) ranged from 0.02 to 37.8 ppm. In one plant with an affected employee who worked
as a mixer, the average air concentration of diacetyl in the mixing area was 0.2 ppm, but air monitoring
in the employee’s breathing zone revealed peak levels of 80 ppm when the employee was pouring
liquid butter flavor into heated mixing tanks. After investigations of six microwave popcorn
manufacturing facilities, NIOSH investigators concluded that employees exposed to butter
flavorings were at risk for development of occupational lung disease and that brief exposures
to high levels may be hazardous even when ventilation maintains low average exposures [5].
Based on the evaluation of the Jasper plant, NIOSH conducted initial animal exposure studies.
Rats were exposed to vapors of one of the flavoring mixtures used in the Jasper plant,
maintained at 131°F for 6 hours. The average concentration of diacetyl in the flavoring vapors,
350 ppm, was comparable to the concentration in the air space above the heated oil/flavoring mixture
in the tanks at the Jasper plant. Necropsy of the rats showed extensive damage to nasal, tracheal,
and bronchial tissue [10]. In a different preliminary animal study, rats acutely exposed to pure diacetyl
vapors had similar, but less extensive airway damage (nasal and tracheal) at concentrations of
198.4 ppm or higher [11]. These studies demonstrate that inhalation exposure to butter
flavoring and diacetyl vapors can cause airways injury in laboratory animals exposed to these
vapors at high concentrations.
Flavorings are complex mixtures of chemical ingredients and the inhalational toxicities of many
of the chemicals found in flavorings have not been evaluated [5]. Other volatile flavoring chemicals,
in addition to diacetyl, were found in air samples during NIOSH investigations of microwave
popcorn plants and it is possible that some of these chemicals may have a role in the development of
the lung disease found in these facilities. NIOSH, National Jewish Medical Center, the National
Institute for Environmental Health Studies (NIEHS), and other researchers are currently
investigating the role of flavoring chemicals, including diacetyl, in the development of fixed
airways obstruction and bronchiolitis obliterans.
OSHA Recommendations
Based on the NIOSH investigation of the Jasper plant, OSHA conducted an on-site review of the
process modifications and controls that had been implemented in the Jasper plant. The purpose of
the on-site visit was to determine whether the engineering controls and personal protective
equipment (PPE) measures that had been instituted could be enhanced to further reduce exposure to
the butter flavoring. Based on the findings of OSHA’s on-site review and NIOSH’s investigation,
OSHA is making recommendations in this SHIB to assist employers in addressing safety and health
concerns regarding employee exposures to butterflavoring chemicals in these facilities. Microwave
popcorn facilities are subject to a wide range of OSHA mandatory occupational safety and health
standards. Apart from the following recommendations, this SHIB in later sections also
describes those applicable OSHA standards that are particularly relevant to protecting employees from
potentially hazardous butter-flavoring chemicals at microwave popcorn plants.
Several sections of this SHIB present important information directed at the control and reduction of
exposure to butter-flavoring chemicals, such as recommendations for engineering controls and
work practices, and standards that address respiratory protection and PPE. Other sections of
the SHIB covering pulmonary function testing, environmental monitoring, and training are also key components in an overall program to protect the health of
employees working at microwave popcorn facilities that use butter-flavoring chemicals.
OSHA Recommendations: Engineering and Work Practice Controls
Engineering and work practice controls are the primary methods for controlling exposures in the
workplace and include: local exhaust and general dilution ventilation to remove contaminants,
isolation of the process or source, and restricted access to areas where hazardous materials are used
or stored. Experience has shown that occupational exposures in most situations can be controlled by
the use of these controls. A risk for occupational lung disease has been identified in NIOSH
investigations for employees who work as mixers of butter flavorings and oil and packagers working
in areas near open or nonisolated tanks of oil and butter flavorings. In the Jasper plant, five of six
employees working in quality control laboratories where many dozens of bags of product were
heated and opened also had abnormal lung function (obstruction) [5,
8].
Operations that may expose employees to intermittent, high concentrations of butter
flavorings, such as opening tanks where butter flavors are heated or mixed, or pouring butter
flavorings into containers may also pose a health risk to employees [5]. Employers should pay
particular attention to the need for additional engineering and work practice controls in the
operations described above, as well as in situations where employees report respiratory symptoms.
However, the absence of employee symptoms does not necessarily mean that adequate engineering
controls have been implemented. Employees with fixed airways obstruction may not have symptoms
early in the course of their disease [3].
Employers should consult with the plant engineers and may also want to consult with a ventilation
specialist for ways to control employee exposures to workplace contaminants, particularly in
operations where butter flavorings are heated, handled, or mixed in open processes. More
information on the topics of ventilation and engineering controls can be found in the
publications listed in the reference
section of this document [12,
13].
Some engineering and work practice controls that have been shown to help reduce employee
exposures to flavoring ingredients include:
- Isolating the mixing room from the rest of the plant using walls, doors, or other barriers.
- Providing the mixing room with a separate ventilation system or ensuring that negative
air pressure (relative to the rest of the plant) is maintained in the mixing room. Both will control the
migration of contaminated air from the mixing room to adjacent areas of the plant.
- Reducing the operating temperature of the holding and mixing tanks to the minimum temperature necessary
to prevent solidification of the flavoring mixture. This will aid in reducing the volatilization of
components of the butter flavoring and their release into the workroom air.
-
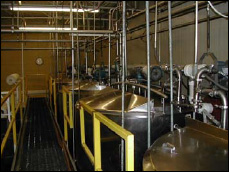
Ventilation of finished oil tanks in mixing room. |
Equipping the head space of the mixing and holding tanks where flavorings are added to
oil or held in pure form with local exhaust ventilation directed out of the plant in a
manner compliant with environmental regulations.
- Automating the mixing process and using closed processes to transfer flavorings.
- Covering the flavoring and finished oil tanks and ventilating the headspace to
reduce emissions into the room.
- Eliminating spillage from overfilling tanks, leaks in seals and fittings, and manual
transfer of materials - all have been identified as sources of emissions. Ventilation of finished oil tanks in mixing room.
- Installing commercially available bagdumping stations equipped with local exhaust ventilation (three-sided canopy
hood) and bag disposal. This will reduce dust exposure during this operation.
- Pumping flavoring from smaller to larger tanks to avoid manual transfer or putting
lids on the transfer buckets or placing the buckets in a ventilated area following
transfer to avoid residual vapor release.
- Adding flavorings at room temperature or, if preheating is necessary, transferring the
heated flavoring to the mixing tank using a pumping system rather than manual transfer.
- Providing additional general dilution ventilation using axial flow wall fans
(requires adequately tempered make-up air during cold weather). Caution should be
used to assure that general dilution ventilation does not spread contaminants to
other areas in the facility.
- Establishing standard procedures for cleaning the workplace, tanks and
containers, and spills. For example, isolate cleaning areas, rinse tanks or containers
with cold water before sanitizing, and avoid cleaning powdered butter-flavoring
chemicals with compressed air. When vessel entry is necessary, ensure compliance
with the confined space entry requirements.
- Maintaining good housekeeping in any areas where flavorings substances or their
ingredients are handled.
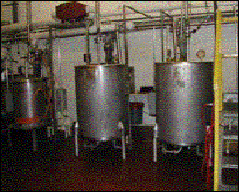
Flavor tank ventilation.
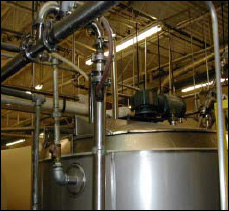
Covered/Ventilated flavor tank ventilation. |
Pulmonary Function Testing
Spirometry, or pulmonary function testing (PFT), measures the breathing capacity of the lungs and is
the best available test for early detection of decreasing or abnormal lung function among
exposed employees [3]. Decreased lung function has been observed in employees exposed to
flavorings before the onset of the symptoms of bronchiolitis obliterans [3]. For this reason,
diminished breathing capacity, particularly among younger employees in the plant population, may
indicate potential problems with exposure to volatile butter flavorings or respirable dust and
should signal the need for further investigation.
Since decreased lung function is an important identifying factor for the presence of the disease, OSHA recommends that all newly-hired employees
have a baseline PFT and be asked to complete a health questionnaire before they start work in areas
where butter flavorings are used. This baseline information is necessary for comparison during
subsequent evaluations. Employers may seek medical expertise to develop their own
questionnaire which should focus on respiratory symptoms and a history of preexisting lung disease.
Questionnaires used by NIOSH during investigations of microwave popcorn
manufacturing plants are found in the
NIOSH
Health Hazard Evaluations. OSHA recommends that new employees with pre-existing
lung diseases and abnormal PFT results be further assessed by a physician to evaluate the potential for
adverse health effects from exposure to volatile flavorings or dust.
OSHA recommends, at a minimum, an annual evaluation for symptoms (i.e., health questionnaire)
and annual PFT for all employees exposed to volatile butter flavorings and their ingredients.
More frequent evaluation and pulmonary function testing may be indicated (i.e., every three to six
months) if employees report symptoms or develop PFT abnormalities. Testing should follow criteria
established by the American Thoracic Society (ATS) guidelines for standardization of spirometry
(PFT) (see the
ATS
Web site).

Spirometer. |
Employers should encourage all employees to immediately report respiratory symptoms or
symptoms of eye, nose, throat, or skin irritation. Employers should promptly refer employees with
abnormal PFT findings, accelerated loss of lung function, respiratory symptoms or evidence of eye,
nose, throat, or skin irritation to a physician for further medical evaluation. The physician should
advise the employee about any suspected or confirmed medical conditions that may be caused
or aggravated by work exposures. The physician can also assist the employer and employee with
recommendations addressing continued workplace exposures and use of respirators and PPE.
Physician recommendations regarding employee exposures or use of PPE should be communicated
to both the employer and the employee.
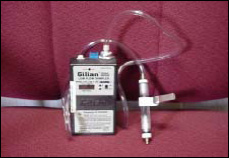
Sampling pump and sampling tube. |
OSHA Recommendations: Environmental Monitoring
NIOSH identified diacetyl, a ketone with butter flavor characteristics, as the predominant volatile
organic compound (VOC) present during mixing room and other related operations. Diacetyl can be
measured as an indicator of butter flavoring exposure.
Before conducting exposure monitoring, workplace control measures and work practices
should be reviewed. OSHA recommends that employers collect full-shift industrial hygiene air
samples (when applicable) to measure the concentration of diacetyl in the work environment.
Personal full-shift monitoring provides information about employee exposures during workplace
operations. Short-term personal sampling is recommended for operations that involve open
handling of flavoring substances (i.e., pouring, mixing, transfer, and packing operations). Area
sampling is also recommended and can provide information about the general work environment
and identify processes that may be sources of butter flavoring exposures. However, area
sampling is not a substitute for personal sampling.
Samples collected before engineering and administrative controls are implemented can be
used to determine the concentration and location of diacetyl and other VOCs throughout the work area
and can be compared with exposure monitoring results reported in NIOSH health hazard evaluations. Once controls are in place, subsequent samples should be
collected to determine the effect of these controls in reducing potential exposure to diacetyl and other
VOCs. OSHA does not have a PEL for diacetyl.
While OSHA recommends that all areas of the plant be initially evaluated, it is of particular
importance that samples be collected in the following plant areas or operations:
- Mixing rooms
- Rooms where flavoring tanks are located
- Production lines
- Quality control laboratory
- During maintenance and cleaning operations
Since the composition of butter flavorings varies among manufacturers, consult with the flavoring
manufacturer and an industrial hygiene laboratory before conducting environmental monitoring.
When applicable, air monitoring should also include sampling for particulates (total and respirable dust) and flavoring substances with
OSHA PELs. A list of flavoring substances that have OSHA PELs is found in the Appendix of
NIOSH’s Alert [3].
Applicable Standards of Special Importance
Microwave popcorn facilities are subject to a wide range of OSHA occupational safety and health
standards. The following discussion focuses on applicable OSHA standards that are particularly
relevant to protecting employees from potentially hazardous chemicals at microwave popcorn plants.
OSHA Applicable Standards: Respiratory Protection
Engineering controls are the preferred method for protecting employees from hazardous respiratory
exposures in the workplace. Respirators are the least preferred method of exposure control because
employees may still be exposed to respiratory hazards if respirators are improperly used or
incorrectly fitted [5, 29 CFR 1910.134]. When effective engineering controls are not feasible or
while they are being instituted, OSHA’s Respiratory Protection standard, 29 CFR 1910.134(a), requires employers to provide and
require the use of respirators when "necessary to protect the health of the employee" from exposure
to harmful airborne substances. The employer must provide respirators that are "applicable and suitable for the purpose
intended."
The NIOSH finding of severe lung disease in some employees at several microwave popcorn
manufacturing plants demonstrates that butterflavoring chemicals can pose severe respiratory
hazards in certain circumstances. Different formulations of butter flavoring (powder, liquids or
pastes) may represent potential respiratory hazards via inhalation of volatile chemicals or respirable
particles [14]. Accordingly, a microwave popcorn manufacturing facility using these ingredients must
determine whether respirators are necessary to protect its employees’ health. Where a substance is
used that may pose a respiratory hazard, the employer must assess the nature and magnitude of
the hazard in the conditions of use in its workplace, considering normal operating conditions and
reasonably foreseeable emergencies. See 29 CFR 1910.134(d)(1)(iii) and 63 Fed. Reg. 1152 1198-
99 (discussion of Paragraph (d) – Selection of Respirators in the preamble to Respiratory
Protection Final Rule). This assessment will guide the employer in determining whether respirators
are necessary and in selecting the appropriate respirator(s).
Employers in microwave popcorn manufacturing facilities that use butter-flavoring ingredients must
conduct the evaluation required by 1910.134(d)(1)(iii) of the Respiratory Protection
standard. The hazard evaluation requirement is performance-oriented, and a variety of estimation
techniques may be used to characterize employee exposures, depending upon the nature of the
chemical products, processes, operating environment, and other factors. The preamble to
the Respiratory Protection Final Rule contains further guidance on the hazard assessment
requirement and outlines several alternative estimation approaches that may be useful (63 Fed.
Reg. 1198-1200, see discussion of Paragraph (d) – Selection of Respirators).
Employers must ensure that the hazard evaluation results in a reasonably accurate estimate of the
nature and extent of the respiratory hazards in the workplace (See 29 CFR 1910.134(d)(1)(iii)).
Because there is no PEL for diacetyl, employers need to consider a variety of factors when
performing their evaluations. They should consider the relevant available information from NIOSH and
other sources on the hazards of volatile butterflavoring ingredients, including diacetyl, and use
informed professional judgment in estimating the nature and magnitude of the hazards to employees
under existing plant conditions. Additional information is provided below:
- Information on the health effects of exposure to volatile butter-flavoring
ingredients in microwave popcorn processing plants is provided in the sources
listed in the references
section of this SHIB. Employers need to evaluate this and other available relevant
information to determine whether their processes are similar to those in plants
studied by NIOSH. NIOSH investigations found that employees working in mixing
rooms and in areas near non-isolated tanks of oil and butter-flavoring ingredients had a
higher prevalence of respiratory symptoms and airways obstruction [5]. Employers
should give special attention to these situations when performing hazard
evaluations. Other production processes involving employee exposure to flavoring
dusts, aerosols and/or vapors should also be evaluated.
- Respiratory symptoms or eye, nose, throat, or skin irritation in exposed employees may
be a significant indication of a hazard requiring respiratory protection. If
employees develop abnormal PFT findings, have PFT evidence of accelerated loss of
lung function, or are diagnosed with lung disease, employers need to take reasonable
steps to determine whether employees are exposed to volatile butter-flavoring
ingredients and have developed occupational lung disease. The recommendations in the Pulmonary
Function Testing section of this SHIB may assist employers in identifying relevant
health effects. NOTE: Do not rely only on the presence or absence of symptoms as the
sole consideration for implementation of a respiratory protection program. Employees
with fixed airways obstruction may not have symptoms early in the course of their
illness.
- In performing the hazard evaluation, employers can use a variety of methods to
estimate employee exposures to airborne concentrations of volatile butter-flavoring
ingredients. As such, OSHA strongly recommends that employers conduct
exposure monitoring to measure the concentration of diacetyl in the workplace.
Air sampling results may be used to gauge the effectiveness of environmental and
work practice controls in reducing employee exposures to volatile butterflavoring
ingredients. Employers may also compare their exposure monitoring results
with
NIOSH Health Hazard Evaluation (HHE)
recommendations for respiratory protection in other microwave popcorn
manufacturing facilities. Recommendations for collecting and using
air samples are contained in the Environmental Monitoring section of this SHIB.
- Given that lung disease has been found in some employees exposed to butter
flavorings containing diacetyl and given that no exposure limits have been
established at this time for butter flavoring and diacetyl, OSHA recommends that
employers should err on the side of caution when evaluating when employees need to
wear respirators, especially when employees work in such situations as
flavoring mixing rooms, quality control laboratories, or near open or nonisolated
tanks of oil and butter flavorings.
If respiratory protection is necessary or if the employer requires that respirators be used, the
employer must comply with the Respiratory Protection standard at 29 CFR 1910.134. In
compliance with this standard, the employer must select a suitable respirator in accordance with the
criteria in 29 CFR 1910.134(d)(2) and (3). Based on the NIOSH investigations of microwave
popcorn plants, a NIOSH-certified air-purifying respirator equipped with organic vapor cartridges
in combination with particulate filters would provide the minimum level of protection. Supplied
air respirators can also be used in these facilities. Powered air-purifying respirators (PAPRs) (with
organic vapor cartridges and particulate filters) are also acceptable alternatives and may be easier for
employees to wear in hot mixing rooms [3]. If
air purifying respirators are provided, employers must
implement a change-out schedule for canisters and cartridges to ensure that they do not exceed their
operational lifespan. Employers must also develop and implement a respiratory protection program
outlining how respirators will be selected, used, and maintained. In addition, employers must
ensure that employees are trained, medically evaluated, and fit tested before using respiratory
protection. The elements required in the written program are outlined in 29 CFR 1910.134(c);
medical evaluation is discussed in paragraph (e), fit testing requirements are provided in paragraph (f),
and training and other employee information requirements are located in paragraph (k). OSHA
has a number of useful resources related to respiratory protection on the
agency’s Web site.
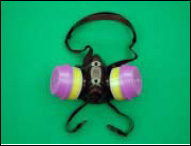
Half-mask air-purifying respirator.
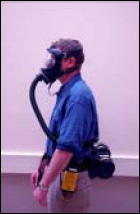
Powered air-purifying respirator. |
OSHA Applicable Standards: Eye and Skin Protection
OSHA’s PPE standards require employers to assess their workplaces to determine if hazards are
present, or are likely to be present, which necessitate the use of PPE (29 CFR 1910.132). If
such hazards are present or are likely to be present, employers must ensure that employees use the
appropriate PPE to protect their eyes, face, hands, and extremities, depending on the nature of the
hazard (29 CFR 1910.132, .133, .138). The employer is accountable both for the quality of the
hazard assessment and for the adequacy of the PPE selected (59 Fed. Reg. 16336, see preamble
discussion of 1910.132(d)).
NIOSH found that, in addition to inhalation hazards, butter flavorings also created eye and skin
hazards for employees. NIOSH identified eye injuries which occurred when employees at one
microwave popcorn plant were exposed to vapors from a new flavoring mixture. These volatile
organic compounds may affect the eyes and skin due to their irritant properties. NIOSH also
indicated that many employees at the Jasper plant reported the development of skin problems, such as
rashes, after they started working there [3]. Skinpatch testing of one of the mixers from the Jasper
plant with various butter-flavoring mixtures used at that plant indicated the presence of a skin allergy
(dermatitis) in addition to his fixed obstructive airways disease [1].
Employers should consider a variety of factors when performing their hazard assessments, including
the degree of employee exposure to butter flavorings, relevant information from NIOSH and
other sources on the eye and skin hazards associated with butter-flavoring ingredients, and
the presence of eye or skin irritation in exposed employees. If the results of the hazard assessment
performed by an employer at a facility using butter flavoring indicate that PPE is necessary to protect
employees from eye or skin hazards, the employer must ensure that employees use appropriate equipment.
Employers must ensure that employees use chemical goggles or other appropriate eye protection
when working with diacetyl and liquid food flavorings containing diacetyl when exposure to
these chemicals is likely to cause injury to the eye (29 CFR 1910.133). Goggles that fit over
corrective lenses are available. Chemical-resistant gloves and sleeves, or other protection for exposed
skin must be used when handling liquid, paste, or powdered flavoring ingredients that could cause
dermal injury. The employer must also provide training for exposed employees as indicated in 29 CFR 1910.132. Since butter flavorings vary
among manufacturers, employers should communicate with both their flavoring
manufacturer and glove vendor to select the appropriate glove material.
OSHA Applicable Standards: Training
The Hazard Communication standard requires employers to train their employees on the hazards
of chemicals in the workplace. 29 CFR 1910.1200(h)(3). Employers must ensure that all
Material Safety Data Sheets (MSDS) are available to employees and provide training to employees
who may be exposed to volatile butter-flavoring ingredients, including diacetyl. This training must
include information about the potential for respiratory, eye, and skin problems from workplace
exposure to hazardous butter-flavoring chemicals. OSHA recommends that this training include the
signs and symptoms of the lung disease discussed in this document. Employers must also train
employees on when and how to use appropriate PPE. In addition, employers must provide
information on the value, limitations and maintenance of this equipment in accordance with
29 CFR 1910.132 and 134.
Edwin G. Foulke, Jr.
Assistant Secretary
Occupational Safety and Health Administration
References
- Akpinar-Elci, M., et al. Bronchiolitis obliterans syndrome in popcorn production plant workers. Eur. Respir. J. 24(2):298-302, 2004.
- Kreiss, K., et al. Clinical bronchiolitis obliterans in employees at a microwave-popcorn plant. New Engl. J. Med. 347(5): 330-338, 2002.
- NIOSH Alert.
Preventing Lung Disease in Workers Who Use or Make Flavorings. NIOSH
Publication No. 2004-110.
- NIOSH Safety and Health Topic:
Flavorings-Related Lung Disease.
- Kanwal, R., et al. Evaluation of flavoringsrelated
lung disease risk at six microwave popcorn
plants. J. Occup. Environ. Med. 48(2):149-157,
2006.
- Centers for Disease Control and
Prevention. Fixed obstructive lung disease in
employees at a microwave popcorn factory —
Missouri, 2000-2002. MMWR Weekly 51(16):
345-347, 2002.
- King, T., Jr. Overview of bronchiolitis. Clinics in Chest Medicine 14(4):
607-610, 1993.
- Kanwal, R., et al.
NIOSH Health Hazard
Evaluation Report, HETA #2000-0401-2991,
Gilster-Mary Lee Corporation, Jasper, Missouri,
January 2006.
- Kreiss, K., Flavoring-related bronchiolitis
obliterans. Curr. Opin. Allergy Clin. Immunol
7:162-167, 2007.
- Hubbs, A., et al. Necrosis of nasal and
airway epithelium in rats inhaling vapors of
artificial butter flavoring. Toxicol. Appl.
Pharmacol. 185(2): 128-135, 2002.
- Hubbs, A., et al. Inhalation toxicity of the
flavoring agent, diacetyl (2,3- butanedione), in
the upper respiratory tract of rats [Abstract]
Toxicologist 78(Suppl. 1): 438-439, 2004. [Accessed February 27,
2007].
- Industrial Ventilation: A Manual of
Recommended Practice, 25th Edition, ACGIH
Worldwide Signature Publications 2004.
- Technical Manual (OTM), TED 1-00-015 [TED 1-0.15A],
Section III Chapter 3 (Ventilation Investigation).
- Boylstein R., et al. Diacetyl emission and
airborne dust from butter flavorings used in
microwave popcorn production. J. Occup. Environ. Hygiene 3(10): 530- 535, 2006.
|
|