New Jersey Case Report: 05NJ007 |
Report Date: January 29, 2007 |
Summary
On January 25, 2005, three workers at an acetylene manufacturing and bottling plant were killed and a fourth worker was seriously injured when acetylene gas collected and exploded in a shed outside the plant. The incident occurred shortly after the workers started the plant’s acetylene generator to make acetylene gas. Due to the severe winter cold, the employees regularly drained a recycled water supply line, which fed the generator, to keep it from freezing. With the failure of a critical check valve, other valves in the open position, and no water pressure in the line, this open pipe created a pathway from the acetylene generator to the lime shed, where the drain valve remained open. The acetylene collected in the shed and was most likely ignited by the hot surface of a sealed space heater inside the shed. The explosion completely destroyed the shed, killing and injuring the victims and severely damaged the adjoining buildings. NJ FACE investigators recommend following these safety guidelines to prevent similar incidents:
- Follow the recommendations issued by Federal OSHA and the US Chemical Safety and Hazard Investigative Board.
- Develop procedures and thoroughly train personnel in operating the acetylene generation system.
- Develop electronic monitoring systems for critical processes and valves.
- Ensure that process pipes are properly designed to prevent freezing, provided with proper venting, and equipped with redundant valves for critical applications.
- Use proper ventilation and an acetylene detection system to prevent and monitor for dangerous gas concentrations.
-
Conduct a job hazard analysis of all work activities with the participation of the workers.
Introduction
On January 25, 2005, NJ FACE staff received a newspaper article about an explosion at an acetylene manufacturing plant that killed three workers. NJ FACE investigators traveled to the scene the next day and initiated an investigation of the incident. During the visit, FACE investigators conferred with the investigating OSHA Compliance Officer and the company owner. Investigators briefly viewed and photographed the incident site. Due to the nature of the incident, NJ FACE investigators suspended the investigation until the conclusion of the Federal OSHA and US Chemical Safety and Hazard Investigative Board (CSB) investigations. The FACE investigation resumed with a follow-up interview of the employer conducted on December 12, 2005. The majority of this report is based on information obtained from the federal OSHA investigation and the CSB, an independent federal agency charged with investigating industrial chemical accidents. Additional information was obtained from the police and medical examiners reports. The testing of valves, heaters, and other equipment was done by the Federal OSHA Technical Center in Salt Lake City, Utah. NJ FACE gratefully acknowledges OSHA for their assistance in this investigation.
The victims’ employer was a company that manufactured and bottled acetylene gas (SIC 2813, NAICS 325120). The family-owned company operated two plants, the incident site and a second facility that bottled propane gas. The acetylene company had been in business since 1982 and employed 15 non-union workers at the time of the incident. The employer stated that job and safety training included monthly safety meetings, safety training, and safety checksheets that are completed on a daily, weekly, and monthly basis. A consultant had been hired to put together a safety program. Many of the employees at the plant spoke only Spanish, but the employer said that language was not a problem since the plant manager spoke Spanish and training was given in Spanish.
Three workers were killed in this incident:
Victim #1 was a 48-year-old Hispanic male who worked as a cylinder filler at the plant. He had lived in the United States for 14 years after emigrating from Mexico and had worked at the company for the past four years. He was survived by his three daughters and one son.
Victim #2 was a 35-year-old Hispanic male who had emigrated from the Dominican Republic. He also worked as a cylinder filler at the plant. He was a single parent to four children and a step-daughter.
Victim #3 was a 30-year-old Hispanic male who had emigrated from the Dominican Republic as a teenager. He worked as a crew supervisor at the plant and was responsible for operating the acetylene generator. He was survived by his wife, a daughter (born posthumously), and his brother, who was the plant manager at the company.
Back to Top
Investigation
The victims’ employer was an acetylene generating and bottling plant located in a zoned urban industrial area. The facility consisted of four areas: the main plant building which held the acetylene generator, bottle filling room, business offices, and employee areas. To the west of the plant was the decant tank area, which consisted of six 10,000 gallon water tanks and a small wooden shed (lime shed) which housed the pump and associated piping for delivering decant water to the acetylene generator. The lime shed also contained a space heater to prevent the pipes and equipment from freezing. The loading dock area was located in front of the main plant and decant tanks. At the time of the incident, this area was occupied by three large truck trailers holding bulk bottles of acetylene the company had purchased for repacking. Finally, a cylinder refurbishing building was located to the west of the decant tanks and loading dock.
|
|
Photo 1. Satellite photo of the incident site prior to the incident
(Google Earth)
|
Graphic 1. Area of photograph detail Overview of the incident site
(Recreated & modified CSB graphic)
|
The plant’s primary product was acetylene, a colorless, highly flammable gas used for welding and cutting metal. Industrial grade acetylene has an odor similar to garlic, and is unstable and can decompose spontaneously and explosively if pressure exceeds 15 PSI. To prevent this, acetylene is dissolved in acetone and stored in cylinders containing a highly porous material. The gas is slightly lighter than air and has an explosive limit of 2.5 % to 100% (NIOSH). The plant generated acetylene by mixing calcium carbide with water in an acetylene generator. This generator was a closed reactor vessel equipped with two hoppers at the top where the calcium carbide was added. The calcium carbide was mixed with water in the vessel, creating acetylene, heat, and a hydrated lime slurry as a byproduct. The gas was passed through a series of driers and scrubbers where impurities were removed, then transferred to the filling room where the gas cylinders were filled. In 2004, the company began to purchase bulk acetylene to supplement the gas manufactured at the plant. The bulk gas was stored in tanks loaded on truck trailers at the loading dock. The company owner stated that the plant manufactured 1.8 to 2.0 million cubic feet of acetylene per month.
The acetylene generation process created a large amount of hydrated lime slurry as a byproduct. The residual lime slurry was piped out of the generator and collected in a lime pit outside the building, where it was then pumped to the six 10,000-gallon decant tanks located outside the building. These tanks were open at the top and allowed the lime to settle out from the water. This system allowed up to 70% of the water to be recycled back into the acetylene generation process, saving the cost of using the more expensive public water. The collected lime was sold to a waste hauler. Each of the six tanks was approximately 20 feet tall and 10 feet in diameter and were arranged in two rows of three tanks. Since the piping and pumps were susceptible to freezing, the company built a small wooden shed in the middle of the tanks, using the tanks themselves as part of the shed walls. This area was called the lime shed and was warmed by a new propane convection heater that had been installed a month before by a plant employee. The heater was designed with a sealed combustion system, preventing air within the shed from having direct contact with the flame and exhaust products. Propane was supplied by a 100-gallon tank located outside the shed.
The company had a prior history of three federal OSHA inspections. The first two occurred in 1996 in response to two separate fires involving acetylene tanks. According to OSHA records, the first fire was reportedly caused by a spark that eventually caused twenty to thirty acetylene tanks to catch fire. A second fire involving a single cylinder occurred eight months later, reportedly due to spontaneous combustion of the pressurized acetylene. The acetylene was allowed to burn off in both fires and there were no reported injuries. In 2002, the company was inspected and cited by OSHA for confined space violations.
Incident
The incident occurred on Monday, January 25, 2005, a cold winter day following a heavy weekend snowstorm. The evening before, workers at the plant drained the decant water system supply pipe to prevent the outdoor pipe from freezing. This pipe supplied the acetylene generator with recycled decant water and originated in the lime shed, the wooden shed built into the decant tanks. To drain the pipe, they opened the drain valve in the lime shed, which was the low point in the system. Two valves were also opened in the generator room, which let air into the system and allowed the water in the pipe to drain into the lime shed. A gurgling sound indicated that the pipe had drained. Without water in the pipe, an open pathway was created between the acetylene generator and the lime shed, as the other valves and devices in the system were either open or could not block the flow of gas. The only safety valve capable of stopping the flow of gas back to the lime shed was a check valve at the generator, which was found to have failed and stuck in the open position.
The plant manager arrived at 7:30 a.m. on the day of the incident. Three workers had been at the plant since 3:00 a.m., and eight more employees would report in later that morning. The plant manager ordered the crew to use the purchased bulk gas to fill the acetylene bottles since this system was easier to start. As the other workers shoveled snow and attended to other duties, the plant manager checked the gauges on the bulk gas tanks and found that they were running low. Sometime between 10:00 and 10:30 a.m., he ordered the generator operator to switch over to the acetylene generator, and the operator activated the hopper on the generator. This introduced the calcium carbide into the generator, where it reacted with the residual water in the vessel and produced acetylene gas. No new water had been directed to the generator, and the supply pipe to the lime shed remained drained and open. As the reaction proceeded, the heat generated caused the automatic water valve to open. The only device to prevent acetylene gas from traveling back through the water line was a “gumdrop” check valve. This valve contained a rubber-coated plug which closed off when gravity or a back flow of gas causes the plug to fall into the seat at the bottom of the valve, sealing the pipe off. (See Graphic 2). The extended stem of the valve stopper apparently caught on an interior edge of the pipe, causing it to remain open. The acetylene gas passed through this valve and past the other open valves, gauges, and other devices in the path to the lime shed. The gas exited through the open drain valve in the lime shed.
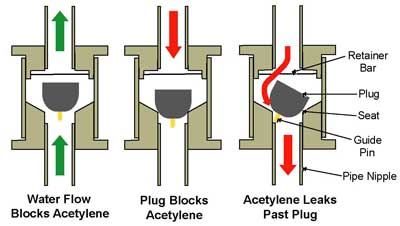 |
Graphic 2. Diagram of failed check valve
Left- Plug open with water flowing. Water blocks gas backflow.
Center- Plug properly seated, gas flow is blocked.
Right- Plug failure. Pin hangs on pipe nipple, gas flows past plug.(Recreated & modified CSB Graphic) |
The acetylene generator operated for approximately thirty to sixty minutes. During this time, the plant manager checked on the men shoveling snow, then returned to his office through the generator room. As he passed the acetylene generator, he heard an unusual noise coming from the water meter, which he found to be running backwards or erratically. He then asked the generator operator if the decant water supply pump was on, and was told it was not. The plant manager asked the operator to check and clean a filter in the lime shed, and returned to the generator room. The explosion occurred a few moments later at 10:36 a.m. The first arriving police and fire units found the dead and injured around the immediate blast area. The blast completely destroyed the lime shed, reducing the wooden building to splinters. The generator operator, who was apparently about to enter the shed, was killed immediately, as was a second worker who was shoveling snow about ten feet away. A third worker died shortly after being air-lifted to the hospital. A fourth worker was severely injured but survived the blast. Subsequent arriving rescue and investigative teams included Federal OSHA, CSB, NJ State Police, NJ Department of Environmental Protection, US Coast Guard, US Environmental Protection Agency, and the county Medical Examiner’s office.
|
|
Photo 2. Incident site, facing north
(NJFACE Photo)
|
Photo 3.
Incident site, facing south
(Police Photo)
|
Federal OSHA and the CSB conducted detailed investigations following the incident. The force of the blast was so severe that it drove wood splinters into nearby cinderblock and cracked a cinderblock wall on a neighboring building 57 feet away. It was determined through the type and extent of the blast damage and other physical evidence that the explosion was caused by acetylene and not propane from the heater. The gas apparently ignited when it contacted the heating surface of the propane heater in the lime shed. Federal OSHA issued 43 citations to the company after the incident, including 39 serious and four unclassified violations. Many of the citations dealt with violations of the OSHA Process Safety Standard, 29 CFR 1910.119.
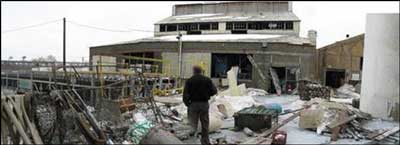 |
Photo 4.
Panoramic photograph of the incident site, facing east
(NJFACE Photo) |
Back to Top
Recommendations/Discussion
Recommendation #1: Follow the recommendations issued by Federal OSHA and the US Chemical Safety and Hazard Investigative Board.
Discussion: Federal OSHA and the CSB conducted thorough investigations of this incident and issued a number of recommendations for preventing acetylene explosions and fires. The following is a list of recommendations as provided by OSHA and the CSB:
OSHA Recommendations:
- Post operator instructions at the generator explaining in English and Spanish the proper procedures and sequence for generating acetylene. These instruction should be posted so the operator can see them from anywhere in the generator room and should be numbered for easy reference. Instructions should address the sequence of steps to initiate process and the consequences of violating the sequence.
- Ensure that buildings or enclosures that could potentially contain acetylene are suitable for acetylene service by:
- Use low temperature heating equipment as per National Fire Protection Agency (NFPA) Standard 51 A, Standard for Acetylene Cylinder Charging Plant.
- Provide appropriately classified electrical components.
- Provide ventilation.
- Locate all venting equipment for acetylene away from possible sources of ignition.
- Maintain check valves in good working order by establishing maintenance schedules and inspections.
- Provide a more reliable check valve for the back flow of acetylene at the generator. (The current design allows a 20 % failure rate).
- Establish a training program that includes what to do in the event of possible mishaps. Each possible mishap should be specified with the proper action to take. Complete records of all training must be kept including the signature of the trained employee and a detailed list of the topics addressed.
- Provide advanced training for the operators assigned to each job. This training should include procedures to check and double check all critical equipment before it is used, during the set-up phase of operations, and during the operation. The operator must be knowledgeable in what actions to take in the event of leaks, spill, and equipment malfunctions in each possible location. The operator should be made aware that he should not be distracted by any other duty that will interfere with his safe operation of the acetylene generating process.
- Establish and maintain an atmosphere of “safety first”. Employees at each level of this company, must concern themselves with the economics and social ramifications of an unsafe attitude and the value of recognizing and addressing commonly anticipated hazards.
CSB Recommendations:
- Maintain up-to-date operating procedures and checklists for the entire operating process.
- Train staff on the operating procedures and require them to demonstrate their ability to correctly follow them.
- Relocate drains and vents connected to flammable gas-containing equipment to safe, preferable outside, locations.
- Ensure that building and enclosures that could potentially contain acetylene meet the requirements of NFPA Standard 51A, Standard for Acetylene Cylinder Charging Plant.
- Inspect, test, and maintain check valves and block valves.
- Provide positive isolation on lines connected to the process to ensure that back flow of explosive gases cannot occur.
Recommendation #2: Develop procedures and thoroughly train personnel in operating the acetylene generation system.
Discussion: In this incident, the water was drained from the feed line; this action removed the backpressure, which allowed the gas to flow back through the line. As long as there was water in the line, even if the check valve failed in the open position the gas would not have entered an enclosed space. To prevent these types of errors, specific procedures for operating and maintaining the acetylene generator and other plant systems should be developed. All plant personnel should be trained in the procedures that apply to their operations. To assist plant personnel, the procedures should include detailed checklists to ensure that all steps are done in the proper order.
Recommendation #3: Develop electronic monitoring systems for critical processes and valves.
Discussion: The plant personnel were unaware until too late that there was a dangerous situation caused by the open valves. NJ FACE recommends using electronic monitoring of processes and valves which is reported to a central and satellite stations. Such a system would provide visual green lights indicating valves are in the proper position for safe process operation along with critical gas flows and pressures. The system should be designed to provide a warning alarm when system operation is out of normal parameters and include an automatic shutdown for potentially dangerous situations.
Recommendation #4: Ensure that process pipes are properly designed to prevent freezing, provided with proper venting, and equipped with redundant valves for critical applications.
Discussion: The water pipes at this plant were prone to freezing, requiring that they be routinely drained in very cold weather. There was only one automatic safety valve to prevent the acetylene from backflowing out of the generator, and this valve failed. NJ FACE recommends that the entire process be reviewed to ensure that all process pipes are properly placed and protected against the elements and other physical hazards, such as being struck by vehicles. Critical safety valves should be equipped with a redundant system to ensure against the failure of a single valve.
Recommendation #5: Use proper ventilation and an acetylene detection system to prevent and monitor for dangerous gas concentrations.
Discussion:The explosion occurred when acetylene gas collected and ignited in a closed area of the plant. To prevent this, the buildings should be designed with a ventilation system that would allow the acetylene to escape before reaching dangerous levels. NJ FACE also recommends using commercially available acetylene gas monitoring systems in all areas where acetylene gas could potentially collect. The detectors should be wired into the monitoring system and provide an audible and visual alarm in the event of an acetylene release.
Recommendation #6:Conduct a job hazard analysis of all work activities with the participation of the workers.
Discussion: To prevent incidents such as this, NJ FACE recommends that employers conduct a job hazard analysis (JHA) of all work areas and job tasks with the employees. A JHA is a procedure that breaks a job or task into specific steps, analyzes each step for specific hazards, and uses this information to develop safe work procedures to eliminate or reduce those hazards. A JHA should begin by reviewing the work activities that the employee is responsible for and the equipment that is needed. Each task is further examined for mechanical, electrical, chemical, or any other hazard that the worker may encounter. The results of the analysis can be used to design or modify the written standard operating procedures for the job. Additional information is available in the publication, Job Hazard Analysis, which is available on the Federal OSHA website at www.osha.gov/Publications/osha3071.pdf.
Recommended Resources
It is extremely important that employers obtain accurate information on health, safety, and applicable
OSHA standards. NJ FACE recommends the following sources of information which should help both employers
and employees:
U.S. Department of Labor, Occupational Safety & Health Administration (OSHA)
Federal OSHA will provide information on safety and health standards on request. OSHA has four area offices in
New Jersey that cover the following counties:
Hunterdon, Middlesex, Somerset, Union, and Warren counties
Telephone: (732) 750-3270
Essex, Hudson, Morris, and Sussex counties
Telephone: (973) 263-1003
Bergen and Passaic counties
Telephone: (201) 288-1700
Atlantic, Burlington, Cape May, Camden, Cumberland, Gloucester, Mercer,
Monmouth, Ocean, and Salem counties
Telephone: (856) 757-5181
Federal OSHA
Web site: http://www.osha.gov
New Jersey Public Employees Occupational Safety and Health (PEOSH) Program
The PEOSH Act covers all NJ state, county, and municipal employees. Two state departments administer the act;
the NJ Department of Labor and Workforce Development (NJDLWD), which investigates safety hazards, and the NJ
Department of Health and Senior Services (NJDHSS) which investigates health hazards. PEOSH has information
available that may also benefit private employers.
NJDLWD, Office of Public Employees Safety
Telephone: (609) 633-3896
Web site:
http://www.nj.gov/labor/lsse/lspeosh.html
NJDHSS, Public Employees Occupational Safety & Health Program
Telephone: (609) 984-1863
Web site:
http://www.state.nj.us/health/eoh/peoshweb/
New Jersey Department of Labor and Workforce
Development, Occupational Safety and Health On-Site Consultation Program
This program provides free advice to private businesses on improving safety and health in the workplace
and complying with OSHA standards.
Telephone: (609) 984-0785
Web site:
http://www.nj.gov/labor/lsse/lsonsite.html
New Jersey State Safety Council
The NJ State Safety Council provides a variety of courses on work-related
safety. There is a charge for the seminars.
Telephone: (908) 272-7712.
Web site: http://www.njsafety.org
Internet Resources
Other useful internet sites for occupational safety and health information:
References
-
Safety Bulletin: Explosion at {name deleted}, Dangers of Flammable Gas Accumulation. US Chemical Safety and Hazard Investigative Board, Washington DC 20037.
-
Standard for Acetylene Cylinder Charging Plants. Pamphlet G-1-4, Compressed Gas Association, New York, NY.
- Standard for Acetylene Cylinder Charging Plants. NFPA 51A, 1989. National Fire Protection Association, Quincy MA.
- Job Hazard Analysis. US Department of Labor Publication # OSHA-3071, 2002 (revised). U.S. Department of Labor, OSHA Publications, P.O. Box 37535, Washington D.C. 20013-7535.
New Jersey FACE Program
Fatality Assessment and Control Evaluation (FACE)
Project
Investigation # 05-NJ-090 Staff members of the New Jersey Department of Health and Senior
Services, Occupational Health Service, perform FACE investigations when there is a report of a targeted
work-related fatal injury. The goal of FACE is to prevent fatal work injuries by studying the work
environment, the worker, the task and tools the worker was using, the energy exchange resulting in the
fatal injury, and the role of management in controlling how these factors interact. FACE gathers information
from multiple sources that may include interviews of employers, workers, and other investigators; examination
of the fatality site and related equipment; and reviewing OSHA, police, and medical examiner reports, employer
safety procedures, and training plans. The FACE program does not determine fault or place blame on
employers or individual workers. Findings are summarized in narrative investigation reports that include
recommendations for preventing similar events. All names and other identifiers are removed from FACE reports
and other data to protect the confidentiality of those who participate in the program.
Please visit the NJ FACE Web site at
http://www.state.nj.us/health/eoh/survweb/face.htm
or the CDC/NIOSH FACE Web site
at http://www.cdc.gov/niosh/face/ for more information.
This NJ FACE report is supported by Cooperative Agreement # 3-U60-OH008485 from the Centers for Disease
Control and Prevention (CDC). Its contents are solely the responsibility of the authors and do not
necessarily represent the official views of the CDC.
To contact New
Jersey State FACE program personnel regarding State-based FACE reports,
please use information listed on the Contact Sheet on the NIOSH FACE web
site. Please contact In-house
FACE program personnel regarding In-house FACE reports and to gain
assistance when State-FACE program personnel cannot be reached.
|