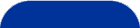
|
 |
Hospital eTool/Nursing Home eTool
Pharmacy Module
Click on the area for more specific information.
|
Common safety and health topics:
Hazard Communication Standard
|
Potential Hazard
Exposure to hazardous chemicals and drugs due to untrained or unaware workers:
- Personnel who are not aware of proper work practices and controls may be exposed to hazardous drugs through the skin, mouth, or by
inhalation.
- The OSHA Technical Manual provides guidance
regarding the adverse health effects from hazardous drugs, ranging from nausea and dizziness, to adverse pregnancy outcomes
(OTM vi.2.3).
Possible Solutions:
Implement a written program which meets the requirements of the
Hazard Communication Standard for employees handling or otherwise exposed to chemicals, including drugs that represent a health
hazard to employees. The written program must provide for worker training, warning labels, and access to Material Safety Data
Sheets (MSDSs). Employees must be informed of the requirements of the Hazard Communication Standard including:
- Any operation/procedure in their work area where drugs that present a hazard are present.
- The location and availability of the written hazard communication program.
- Any operations or procedure in their work area where other HD's are present.
- The location and availability of any other plan regarding HD's.
The HCS only applies to pharmaceuticals that the drug manufacturer has determined to
be hazardous and that are known to be present in the workplace in such a manner that employees are exposed under normal conditions
of use or in a foreseeable emergency
[OSHA Interpretation Letter
(1994, March 3)].
- There are exemptions to the standard such as:
- Drugs that are in solid, final form for direct administration to the patient, e.g., tablets, or pills
[1910.1200(b)(6)(vii)].
- Final form exemption would also apply to tablets or pills that are occasionally crushed, if the pill or tablet is not designed to
be dissolved or crushed prior to administration.
- Consumer
products that are subjected to the labeling requirements of the terms as defined in the Consumer Product Safety Act and the Federal
Hazardous Substances Act
[1910.1200(b)(5)(v)].
- Chemicals with any of the following characteristics are considered hazardous: carcinogenic, corrosive, toxic or
highly toxic, irritating, sensitizing, or target organ effecting. [Hazard Communication Standard
Appendix A and chemicals listed in
1910.1000 Table 2].
- Both human and animal data are to be used in this determination. The Hazard Communication Standard,
Appendix B lists sources of toxicity
information.
- The OSHA Technical Manual provides recommendations for
characterizing hazardous drugs.
- The National Institute for Occupational Safety and Health (NIOSH) also provides an annually updated list of drugs considered
hazardous. Appendix
A - Drugs considered Hazardous.
|
- Provide readily available
Material Safety Data Sheets (MSDSs) for all hazardous chemicals, including hazardous drugs that meet the Hazard Communication Standard criteria.
|
|
- All personnel involved in any aspect of the handling of covered hazardous drugs (physicians, nurses, pharmacists, housekeepers,
employees involved in receiving, transport or storage) must receive information and training to apprise them of the hazards presented
by hazardous drugs in the work area, [OTM5.A.2] including the
following:
- Methods and observations that may be used to detect the presence or release of an HCS-covered hazardous drug in
the work area (such as monitoring conducted by the employer, continuous monitoring devices, visual appearance or odor of covered
HD's being released, etc.).
- The physical and health hazards of the covered HD's in the work area.
- The measures employees can take to protect themselves from these hazards. This includes specific procedures that the employer
has implemented to protect the employees from exposure to such drugs, such as identification of covered drugs and those to be
handled as hazardous, appropriate work practices, emergency procedures (for spills or employee exposure).
- Personal protective equipment, and the details of the hazard communication program developed by the employer, including an
explanation of the labeling system and the MSDS, and how employees can obtain and use the appropriate hazard information.
|
|
|
|
- Any workplace exposure record created in connection with HD handling shall be kept, transferred, and made available for at least
30 years and medical records shall be kept for the duration of employment plus 30 years in accordance with the Access to Employee
Exposure and Medical Records Standard
(29 CFR 1910.1020).
|
Other Recommended Good Work Practice:
|
- Develop, implement and maintain a written hazardous drug safety and health plan to protect those employees who handle or are
otherwise exposed to drugs that pose a health hazard to them.
- The OSHA Technical Manual Part V, A#1, offers guidance in the
development of a drug safety and health plan.
|
|
- Nursing stations on floors where hazardous drugs will be administered should have spill and emergency skin and
eye decontamination kits available and relevant MSDSs for guidance.
|
|
- A list of drugs covered by hazardous drug policies and information on spill and emergency contact procedures
should be posted or easily available to employees.
|
For additional information, see HealthCare Wide Hazards -
Hazardous Chemicals.
Additional Information:
|
|
Some examples of Antineoplastic (cancer) drugs, include, Vincristine, Dacarbazine, Mitomycin, Cytosine
Arabinoside, and Fluorouracil
|
Potential Hazard
Exposure to hazardous drugs during preparation due to ineffective engineering/work practice controls and PPE:
Possible Solutions:
- PPE: OSHA 1910.132
requires the employer to assess potential hazards and then select and ensure the use of appropriate PPE to protect employees from
hazardous chemicals, including hazardous drugs as defined by the
Hazard Communication Standard.
- Eye and Face Protection: OSHA
1910.133 requires the use of
chemical-barrier face and eye protection whenever splashes, sprays, or aerosols of HD's may be generated that could result in eye,
nose, or mouth contamination.
Other Recommended Good Work Practice:
- Biological Safety Cabinets: Approved Biological Safety Cabinets
(BSC) should be used when preparing hazardous medications. (OSHA Technical Manual
Part V, Section B, #2).
- Class II, type B, or Class III BSCs that vent to the outside are recommended.
(Part V, Section B, #3, c).
|
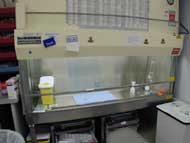
Vertical Flow-Laminar Hood |
|
- OSHA does not recommend Horizontal BSCs for the preparation of hazardous drugs, since they increase the likelihood of
drug exposure. (Part IV, Section A, #3).
|

Horizontal Flow Laminar Hood |
|
- The BSC should also contain:
|
|
- Covered needle containers for needle disposal.
|
|
- Covered waste container for excess fluids disposal.
|
|
Personal Protective Equipment (PPE) The OSHA Technical Manual,
describes the effective use of gloves and gowns when working with Hazardous Drugs
(Part V, Section B, #6).
|
|
- The thickness of the gloves used in handling hazardous drugs is more important than the type of material. The best results have
been seen with latex gloves.
|
|
- Double gloving is recommended because all gloves are permeable to some extent, and their permeability increases with time.
- When double gloving, one glove should be placed under the gown cuff and one over. The glove-gown interface should be such that no
skin on the arm or wrist is exposed.
- To limit transfer of contamination from the BSC into the work area, the outer gloves should be removed after each task or batch,
and should be placed in "zipper" - closure plastic bags or other sealable containers for disposal.
|
|
- Gloves should be changed regularly (hourly) or immediately if they are torn, punctured, or contaminated with a spill.
|
|
- Thicker, longer, latex gloves that cover the gown cuff are recommend with minimal or no powder since the powder may absorb
contamination.
|
|
- The worker should wear a protective disposable gown made of lint-free, low-permeability fabric, with a solid front,
long sleeves and tight-fitting elastic or knit cuffs.
|
|
- Hand washing: Hands should be washed before gloves are put on, and after they are removed.
|
- Restricted Preparation areas:
OSHA and the American Society of Hospital Pharmacists recommend that hazardous drug preparation be performed in a
restricted area, with signs restricting the access of unauthorized personnel prominently displayed
(Part V, Section B, #1).
|
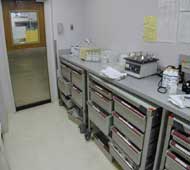
Restricted Drug Preparation Room |
- Restricted Activities: Smoking, drinking, applying cosmetics, or eating where
hazardous drugs are prepared, stored, or used, increases the chance of exposure, and should be prohibited
(Part V, Section B, #1).
|
|
Additional Information:
|
|
|
Handling Practices
|
Potential Hazard
Exposure to hazardous drugs (HDs) through improper:
Possible Solutions:
When handling hazardous drugs good work practice includes:
|
- Hazardous Drugs should be prepared by pharmacists, not by nurses or physicians without proper PPE and
engineering controls. The risk of exposure to hazardous drugs through inhalation or direct skin contact, is present in procedures
such as:
- Transferring hazardous drugs from one container to another, reconstituting or manipulating them.
- Withdrawal of needles from drug vials.
- Expulsion of air from a drug-filled syringe.
- Expelling air from syringes should be done in the biological safety cabinet, not by the health care worker giving the injection.
Technical Chapter Part V, Section C, #1 and #2.
|
Sharps Handling: OSHA and the American Society of Hospital
Pharmacists (ASHP) recommend that all syringes and needles used in the course of preparation be placed in "sharps"
containers for disposal without being crushed, clipped or capped. Technical Chapter
Part V, Section C, #1, b.
Priming of tubing for hazardous drugs: The OSHA Technical Manual
Part V, Section C, #1, c, recommends that drug administration sets
be attached and primed within the BSC prior to addition of the drug. This eliminates the need to prime the set in a less
well-controlled environment. It also states that the priming should be done with non-drug containing solution or that a back-flow
closed system be used.
Labeling Practices: In addition to standard pharmacy labeling practices, all
syringes and IV bags containing hazardous drugs should be labeled with a warning label such as: Special
Handling/Disposal Precautions. Technical Chapter Part V,
Section C, #1, a.
|
Ribavirin an antiviral drug used to treat some infants and young children with lower respiratory syncytial
virus (RSV) infections. This drug is aerosolized to a respirable size of approximately 1.3 microns and is usually administered to
the patient in an oxygen tent or face mask. This is when exposure can occur.
|
Potential Hazard
Exposure of administering personnel to hazardous drugs during administration including
aerosolized drugs, (e.g., Ribavirin).
Possible Solutions:
Good work practice recommends:
- Personnel administering Hazardous Drugs wear gowns, latex gloves, and chemical splash goggles or
equivalent safety glasses. OSHA's Technical Manual Chapter (Part V,
Section C, #2) and the National Study Commission on Cytotoxic Exposure.
- When administering aerosolized drugs additional precautions may be necessary to protect the employee
from exposure such as:
- Wearing NIOSH-approved respirators.
- The use of treatment booths with local exhaust ventilation systems, or isolation rooms with separate HEPA filtered ventilation
systems.
The American Society of Hospital Pharmacists (ASHP) recommends these guidelines when administering hazardous
drugs:
- Only those trained to administer hazardous drugs should be allowed to perform this function.
- Disposable gloves and gowns should be worn. The glove and gown cuffs should be worn in a manner that produces a tight fit (e.g.,
loose glove tucked under gown cuff; tight glove fitted over gown cuff).
- Intravenous containers designed with venting tubes should not be used.
- The use of plastic backed absorbent liners under I.V. tubing during administration of hazardous drugs to absorb any leakage and
prevent the solution from spilling onto patient skin.
- Work at waist level, if possible; avoid working above the head or reaching up for connections or ports.
- Until the reproductive risks associated with handling Hazardous Drugs have been substantiated, staff who are pregnant or
breast-feeding should avoid contact with these drugs.
|
Hazardous Drugs During Care Giving
|
Potential Hazard
Exposure to Hazardous Drugs during care giving:
- When dealing with excreta that may contain high concentrates of hazardous drugs.
Possible Solutions:
Special precautions need to be taken by personnel while caring for the patient who
has been taking hazardous drugs.
OSHA requires:
- If personnel are unable to differentiate between body fluid types, care should be given in accordance with the
Bloodborne
Pathogens Standard.
- Universal precautions must be observed to prevent contact with blood or other potentially infectious materials.
Other Recommended Good Practices:
- Personnel (nursing, housekeeping) dealing with excreta, primarily urine, from patients who have received Hazardous Drugs in the
last 48 hours, should wear PPE, gloves, and gowns.
- The American Society of Hospital Pharmacists (ASHP) recommends:
- Gloves be discarded after each use and immediately if contaminated.
- Gowns should be discarded on leaving the patient-care area and immediately if contaminated.
- Hands must be washed thoroughly after hazardous drugs are handled.
- Disposable linen or protective pads should be used for incontinent or vomiting patients.
- Contaminated non-disposable linen or protective pads require pre-washing.
|
Disposal of Hazardous Drugs
|
Potential Hazard
Exposure to Hazardous Drugs during disposal:
Possible Solutions:
Bagging and labeling:
OSHA requires:
Other Recommended Good Practices:
- Thick, leak-proof plastic bags, colored differently from other hospital trash bags, should be used for routine collection of
discarded gloves, gowns and other disposable material, and labeled as Hazardous Drug-related wastes.
- The Technical Chapter suggests the waste bag should be kept inside a covered waste container clearly labeled "Hazardous
Drug WASTE ONLY." At least one such receptacle should be located in every area where the drugs are prepared or administered.
Waste should not be moved from one area to another. The bag should be sealed when filled and the covered waste container taped.
- Hazardous Waste Disposal and Containers: The OSHA Hazardous Drugs Technical Chapter
(Part IV), Section C recommends:
- Labeling needle containers and breakable items of hazardous waste as Hazardous Drug waste only.
- The use of properly labeled, sealed and covered disposal containers, handled by trained and protected personnel, as required under
the Bloodborne Pathogens Standard if such items are contaminated with blood or other potentially infectious materials.
Hazardous drug-related wastes should be disposed of according to EPA, state and local regulations for hazardous waste.
This disposal can occur at either an incinerator or a licensed sanitary landfill for toxic wastes, as appropriate. Commercial waste
disposal is performed by a licensed company. While awaiting removal, the waste should be held in a secure area in covered, labeled
drums with plastic liners.
|
|
Potential Hazard
Exposure to hazardous drugs during storage.
Possible Solutions:
The OSHA Technical Manual recommends:
|
- Storage of Hazardous Drugs: Access to areas where Hazardous Drugs are prepared
and stored is limited to authorized personnel only, with signs restricting entry.
|
|
|
- Storage Area for Hazardous Drugs: Bins or shelves where Hazardous Drugs are stored
should be designed to prevent breakage and to limit contamination in the event of leakage, with bins with barrier fronts, or other
design features that reduce the chance of drug containers falling to the floor.
- Warning labels should be applied to all HD containers, shelves, and bins, where these containers are stored.
- The American Society of Hospital Pharmacists (ASHP) recommends hazardous drugs requiring refrigeration be stored separately from
non-hazardous drugs in individual bins designed to prevent breakage and contain leakage.
|
|
|
Some employees develop latex allergy from exposure to latex in products like latex gloves. This can cause
reactions from irritant contact dermatitis, and allergic contact sensitivity to immediate possible life threatening sensitivity.
|
Potential Hazard
|
Developing latex allergies from exposure to latex products.
|
Possible Solutions:
OSHA requires:
- Bloodborne Pathogen Standard states, The employer shall ensure that appropriate personal protective equipment
in the appropriate sizes is readily accessible at the worksite or is issued to employees. Hypoallergenic gloves, glove liners,
powderless gloves, or other similar alternatives shall be readily accessible to those employees who are allergic to the gloves
normally provided
[1910.1030(d)(3)(iii)].
- Please note that hypoallergenic gloves, glove liners, or powderless gloves are not to be assumed to be non-latex
or latex free.
Other Recommended Good Practices:
- Research indicates the thickness of the gloves used in handling hazardous drugs is more important than the type of material used.
Non latex gloves and other latex free products are available.
- If latex is used, choose a low protein, powder free glove. (Powder free gloves seem to reduce systemic allergic responses.)
For additional information, see HealthCare Wide Hazards -
Latex Allergy.
|
Ergonomics
|
Potential Hazard
|
Pharmacists may be exposed to Musculoskeletal Disorders (MSDs) such as Carpel Tunnel Syndrome, Tendonitis,
and Tenosynovitis from activities that involve repetitive tasks, forceful exertions, awkward postures or contact stress (e.g.,
opening/closing bottle lids, or computer tasks such as typing).
|
Possible Solutions:
- Use assistive devices, to eliminate the need to do the task, (e.g., use devices designed to open bottle lids for Pharmacist).
|
|
- Modification of pharmacy tasks to decrease incidence of work-related musculoskeletal disorders.
- Redesign the process to incorporate variation into the task (e.g., alternate repetitive tasks with those that do not
require high repetition).
|
|
- Provide ergonomically comfortable work stations including, wrist pads, adjustable padded chairs, and keyboard tray, and
monitors at a comfortable height.
|
|
|
Workplace Violence
|
Potential Hazard
|
Pharmacists may be exposed to workplace violence due to the availability of drugs and money in the pharmacy
area, making them possible robbery targets.
|
Possible Solutions:
OSHA recommends that employers establish and maintain a violence prevention program as part of their facility's safety and health
program which could include:
- Installing plexi-glass in the payment window in the pharmacy area.
- Providing better visibility and lighting in the pharmacy area.
- Providing training for staff in recognizing and managing hostile and assaultive behavior.
- Implementing security devices such as panic buttons, beepers, surveillance cameras, alarm systems, two-way mirrors, card-key
access systems, and security guards.
For additional information, see HealthCare Wide Hazards -
Workplace Violence.
|
|