An IEMS Checklist for Lead Organizations
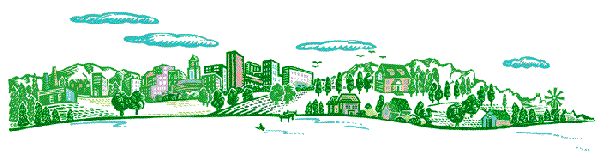
A lead organization is an association, technical assistance provider, large company, or other organization that is in a position to facilitate the development of an Integrated Environmental Management System (IEMS) among its members, clients, or small suppliers.
This fact sheet presents a step-by-step list of the actions lead organizations should take to spearhead the development of an IEMS for a particular industry sector or organizational niche. It also provides a success story of how one association served as a lead organization for its members. en español -- Un Lista de Verificación de un SIAA para Organizaciones Lideres.
Utilize DfE's self-directed IEMS publications and tools to help with this process.
Checklist

-
Provide a "gaps analysis" with questions related to your industry sector's environmental consequences. A "gaps analysis" is a list of questions that, when answered, helps to determine how much work a company would have to do to achieve an IEMS.
Develop a detailed process map showing processes typical for your sector.
Identify environmental aspects, or issues, that are typical to your industry sector. Environmental aspects are the ways in which an organization or company impacts the environment. Similar concerns usually span companies within a given industry sector.
Organize and lead participating companies to develop an IEMS.
Identify and encourage companies to participate in the process of developing an IEMS.
Develop participation agreements for those companies that want to be involved.

-
Set deadlines and monitor progress.
Hold focused workshops.

-
Provide regulatory baseline information (federal and state) related to the environment for your industry.
Provide health and safety information for your industry.
Provide chemical process information for your industry.
Help companies with an assessment of cleaner alternatives for those concerns identified. Support ranges from consultation to training to performing assessments.

-
Establish your association's targets and measures of success.
Help companies establish their own targets and measures.
Monitor and evaluate companies' success.
Establish environmental benchmarks and goals.

-
Provide a forum to publicize environmental improvements accomplished by companies' participation in the development of an IEMS.
Communicate IEMS benefits to companies' supply chain customers.
Lead Organization Success Story
Serving as a lead organization for the screen printing industry, the Screenprinting and Graphic Imaging Association International (SGIA) worked with DfE and seven small screen printing companies to develop a customized IEMS program. In less than a year, the companies were able to see environmental improvements as a result of their IEMS. In addition, because of the success of the pilot project, SGIA is extending the IEMS to more screen printers across the country as well as in Canada.
Tools
SGIA adapted each of the generic essential tools provided by DfE to reflect the screen printing industry's profile and needs. SGIA provided a "gaps analysis" with questions tailored to the environmental concerns typical in the screen printing industry, and also developed a detailed process map for a typical screen printing operation. Then SGIA customized the IEMS Implementation Guide and the IEMS Company Manual Template to its members.
Leadership
SGIA identified and encouraged seven screen printing companies to develop IEMSs and then developed participation agreements that outlined the commitment of each participant. Together, SGIA and the pilot companies set deadlines for accomplishing each step. The association also monitored the companies' progress and provided support through bi-weekly conference calls. Three workshops, held over the course of a year, trained the pilot companies' representatives in how to implement an IEMS.
SGIA is also organizing a network of IEMS companies that can provide ongoing mutual support in developing and maintaining IEMSs. Because of this, the pilot participant companies have agreed to assist other companies participating in a series of workshops offered internationally by SGIA.
Information
Though previous participation in the DfE Screen Printing Project, SGIA had developed regulatory baseline information (federal and state) related to the environment. In addition, when the pilot companies wanted to obtain health, safety, and environmental information on chemicals in products from their suppliers, SGIA helped manage this effort. The association also created a list of chemicals commonly used in this industry and requested environmental information about them from the DfE Program. This information will be used to help screen printers identify significant environmental issues and evaluate cleaner alternatives.
Recognition
Both the DfE Program and SGIA formally recognized the participants in the screen printing pilot program.