Cobbler Jeremy
Meritt saves soles, one shoe at a time. He also mends
heels, uppers, clasps, buckles, and other components of
shoes and boots that are in need of repair.
"I rarely find something that I can’t
fix," says Jeremy. "I tend to take on more
headaches than maybe I should, and those might take a
little longer. But it’s rare that I see something I just
can’t do."
Although cobblers are shoe repairers and
sometimes shoemakers, their repertoire extends beyond
shoes. They handle everything from fabric to plastic to
wood. Jeremy, for example, once created a corkscrew tail
for a pig-shaped footstool. Working with his wife, Elaine,
he regularly repairs luggage, belts, handbags, briefcases,
and other objects; occasionally, they get calls for
in-home furniture repair.
But the bulk of Jeremy’s work involves
rebuilding or replacing the soles of shoes. Customers
bring their tattered footwear to his Morton, Illinois,
store and describe what they’d like done. Jeremy
explains how he’ll fix the problem, notes the details on
a work ticket, and reaches a price agreement with the
customer.
Like most cobblers, Jeremy has set prices
for routine jobs. He usually charges $35 per pair for full
sole replacement, for example, and about $12 per pair for
heel repair. Complex jobs are more, primarily to cover the
cost of the extra materials required.
The first step in repairing most shoes is
tearing them down: stripping away worn pieces to get to
the usable base. Jeremy begins most workdays by gathering
all the shoes, lining them up, and making his way along
the row of footwear. One by one, using a knife or other
tools, he removes old pieces and discards them.
Then, he takes the shoes to a large
sanding machine. Sanding eliminates leftover particles,
creating a clean but rough surface for rebuilding; glue
bonds better to rough surfaces than to smooth ones. He
also cuts, custom sizes, and sands the replacement parts
for each shoe.
Rebuilding is next. Jeremy prepares
adhesives for gluing the new pieces to the shoes. Rapidly
drying glues allow little room for error, so Jeremy works
down the line of shoes quickly to apply the adhesives and
assemble the parts.
Long ago, cobblers hammered nails and
stitched threads to hold the parts of a shoe together.
Some cobblers today still use those traditional methods,
but Jeremy is among those who rely on adhesives instead of
nails.
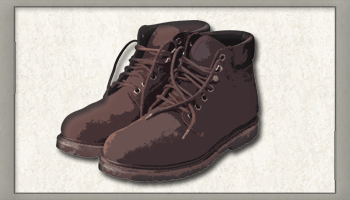
For these modern cobblers, nails are
obsolete and stitching is largely decorative. "Glue
technology has improved so much over the years," says
Jeremy, "that the bond the glue creates is actually
stronger than the shoe itself."
After the glue dries and sets, Jeremy adds
the finishing touches: trimming and sanding the new pieces
to blend with the original parts, applying polish and
sealant, and shining and buffing each shoe until it
gleams. He might also need to use ink or dye, depending on
the material, to match the new parts with the original
color.
Dyes contain acetone, a flammable liquid
that can cause eye irritation, and adhesives have
dangerous vapors in them. Cobblers wear safety goggles to
protect their eyes both from chemical splashes and from
fine dust generated by the sander. They also need to keep
their workspace well ventilated to guard against the
long-term health consequences of inhaling chemicals.
Most sole or heel replacements or repairs
take about 35 minutes from start to finish. But Jeremy
usually estimates a 2-day turnaround for customer pickup
because he prefers to group his work by task rather than
by individual project. In this way, he can divide his day
into teardowns, rebuilding or repairing, and finishing—and
still have time to work on items other than shoes.
Once in a while, a customer asks Jeremy to
create something from scratch, such as a pouch or coin
case. "Those are fun, if I have the time," he
says. But Jeremy also works as a paramedic, so on the days
he’s in his store, he’s usually busy doing repair work
and meeting with customers.
Jeremy uses communication skills and sales
ability in dealing with customers. As a store owner, he
also needs skills such as accounting and marketing to keep
up with payroll, insurance, advertising, and related tasks
of running a business. These skills are in addition to the
manual dexterity, mechanical aptitude, and mathematical
and problem-solving ability that all cobblers need to
repair shoes and other items.
Few formal training programs exist to
prepare cobblers for the occupation. Most learn on the
job; Jeremy, for example, trained under his stepfather’s
supervision and gradually took over the business when his
stepfather retired. "This is one of those trades
where you just have to dig in and do it," says
Jeremy. "Once you learn it, you could go
anywhere."
Data from the U.S. Bureau of Labor
Statistics (BLS) show that in May 2006, there were 7,450
shoe and leather workers and repairers employed throughout
the country. Their median earnings were $20,450. These
data include wage and salary workers only and do not count
those, like Jeremy, who are self-employed.
The small number of cobblers shows the
limited demand for their services. For many people, it’s
more economically feasible to buy new shoes than to repair
old ones. But for other people, it’s more practical to
refurbish expensive designer shoes than to purchase new
ones, especially if the style is no longer available. And,
says Jeremy, growing numbers of people understand the
environmental advantages of repairing used goods.
Jeremy speculates that there’s little
public awareness about what cobblers do—or that they’re
still around. He stays visible in his community by
repairing banners, supplying material scraps, and
providing other services to schools and civic groups.
His customers value this community
involvement. Jeremy has owned the store since 1998, but
the business has been a fixture in Morton since 1959.
"I get people who come in because they appreciate the
whole family-run aspect of the business," he says.
"I might be more progressive in my methods than other
shops, but it’s continuing the tradition that I like
best."
Top
|