Alison Simon, Ph.D.
Jim Wells, Ph.D.
Sameer Abraham, Ph.D.
September 29, 2005
The Gallup Organization
Government Division
901 F St. NW
Washington, D.C. 20004
Table of Contents
1.0 Introduction
2.0 Methodology
2.1 Respondent Characteristics
3.0 Mentoring Efforts
3.1 The Overall Impact of Mentoring
3.2 Specifics About Recent Mentoring Experiences
4.0 Outreach Efforts
4.1 The Overall Impact of Outreach
4.2 Specific Outreach Activities Conducted at the Request of OSHA
4.2.2 Characteristics of Those Conducting Outreach at the Request of OSHA
4.3 Specific Outreach Activities Conducted at the Request of Other Organizations
4.3.2 Characteristics of Those Conducting Outreach at the Request of Other Organizations
5.0 Past Data Collection Efforts
5.1 "Future" TCIR and DART rates
6.0. Conclusions and Recommendations
6.1 Mentoring Program - Conclusions
6.2 Outreach Program - Conclusions
6.3 Data Analysis - Conclusions
6.4 Recommendations for Future Data Collection Efforts
7.0 Verbatims
Appendix A: Equations For Mentoring and Outreach
Appendix B: Web Questionnaire
Appendix C: Invitation Letter
Appendix D: Call Script Used for Reminder Calls
Appendix E: Full Data Tables
Appendix F: Data Analysis Plan
Table of Tables
Year of acceptance
SIC division
Size of site
Did anyone at your site conduct mentoring in the past 12 months
Mentors per site
Years your site had at least one person mentoring
Sites that no longer mentor by tenure in VPP
Number of sites mentored over time
Average # of facilities mentored since acceptance into VPP
Average # of facilities mentored that were subsequently accepted into VPP
SIC Division – number of respondents
Mean number of sites mentored since inception
Since your site was approved for VPP, on average how many sites have you mentored – by number of
employees
Does your company require you to mentor facilities within your own company
Do you conduct mentoring with non-VPP bound sites
Yearly hours spent mentoring
What type of mentoring do you conduct
Does your site plan to do more, less, or about the same amount of mentoring in the future
Additional hours willing to mentor
Did anyone at your site perform outreach activities in the past 12 months (either OSHA or for other
organizations)
Number of years conducting outreach activities
Number of employees performing outreach
Which outreach activities did you conduct in the past 12 months
Type of hours spent on event
Gallup’s estimate of activity in calendar year 2004
Percentage of activities conducted within own company
Would you do more, less, or about the same amount of outreach activities in the next 3 years
Additional hours sites are willing to spend
Companies conducting outreach at the request of OSHA
Outreach conducted at the request of OSHA by manufacturing sites
Breakdown by employee size
Outreach conducted at the request of OSHA by employee size
How many times was the activity conducted in 2004
Number of activities conducted overall
Gallup’s estimate of activity
Percentage of activities conducted within own company
Would you do more, less, or about the same amount of outreach activities in the next 3 years
Additional hours sites are willing to spend
Outreach conducted at the request of other organizations by manufacturing sites
Breakdown by employee size
Outreach conducted at the request of other organizations by employee size
TCIR and DART rates for the five years prior to acceptance into VPP
Changes in TCIR and DART rates for the five years prior to acceptance into VPP
TCIR rates for the five years prior to acceptance into VPP by employee size of site
DART rates for the five years prior to acceptance into VPP by employee size of site
TCIR rates for the five years prior to acceptance into VPP by SIC code
DART rates for the five years prior to acceptance into VPP by SIC code
Years prior to acceptance
List of events or activities and number of respondents indicating event occurred
Average number of yearly diseases by years out from VPP acceptance
Future TCIR and DART rates
DART rates of acceptance
TCIR rates after acceptance
1.0 INTRODUCTION
In November 2003, Gallup was contracted by the U.S. Department of Labor to design an evaluation of
the Voluntary Protection Programs (VPP) — cooperative programs that the Occupational Safety and
Health Administration (OSHA) uses to recognize employers who demonstrate excellent voluntary safety
and health programs. Over the ensuing year and a half, the Gallup and OSHA project teams worked in
conjunction to establish an evaluation that would accomplish the following objectives:
- Measure the overall impact of the VPP sites’ worker safety and health programs as a result of
outreach and mentoring programs on:
- the corporation overall
- other work sites
- Measure the injury and illness reductions at VPP sites from the early decision and inception
phase to full participation in the VPP process
- Assess the feasibility of doing a business case for the VPP
The following report summarizes the findings of this project in terms of the first two objectives. A
separate report was written for the third objective. The final data analysis plan (see Appendix D)
outlines the analysis that follows.
2.0 METHODOLOGY
To perform this analysis, two distinct methodologies were used. One was a Web questionnaire to
gather data for the first two objectives, measuring outreach and mentoring and measuring injury and
illness reductions, and the other was a paper questionnaire for the third objective, the feasibility
analysis. All federal VPP participants were eligible for the Web questionnaire; OSHA invited all Web
questionnaire participants to participate in the feasibility analysis and forwarded potential
participants to Gallup. This report focuses solely on the Web questionnaire data. Final results from
the feasibility analysis are in a follow-up report.
In total, OSHA provided a population of 834 names and addresses of current federal VPP sites for the
Web questionnaire. Of those 834 eligible respondents, 283 completed the questionnaire and an
additional 97 partially completed the questionnaire for a questionnaire response rate of 46%. Due to
the nature of this questionnaire (divided into three non-contiguous sections) it was determined that
a partially completed questionnaire would be acceptable. In addition, as of the December 31, 2004,
OSHA had 1,107 federal sites in their database. For extrapolation calculations contained within this
document, the 1,107 federal sites are used.
For the Web questionnaire, invitation letters with access codes were sent to eligible respondents on
February 28, 2005 (see Appendix B). Data collection occurred between March 1 through May 27, 2005.
Gallup conducted reminder phone calls 10 days after respondents received their invitations, from
March 11 through March 18 (see Appendix B for reminder call script). OSHA conducted reminder calls
on numerous occasions in April and May.
2.1 Respondent Characteristics
Respondents for this questionnaire were representative of the entire federal VPP population in many
respects. Overall, the majority of respondents were new entrants into VPP and were mainly in the
manufacturing sector. Characteristics of these sites including number of years in VPP, the Standard
Industrial Classification (SIC) code, and number of employees were as follows:
Year of Acceptance |
Number of sites |
Total VPP Database of Sites |
% of Total VPP Sites Received |
2004 |
35 |
175 |
20% |
2003 |
50 |
107 |
47% |
2002 |
37 |
89 |
42& |
2001 |
14 |
83 |
17% |
2000 |
19 |
91 |
21% |
1999 |
29 |
92 |
32% |
1998 |
23 |
64 |
36% |
1997 |
19 |
72 |
26% |
1996 |
8 |
67 |
12% |
<1995 |
134 |
267 |
50% |
Total Responses |
368 |
1,107 |
33% |
SIC Division |
Number of Respondents |
Total VPP Database of Sites |
% of Total VPP Sites Received |
Not given |
41 |
204 |
20% |
Division A: Agriculture, Forestry, and Fishing |
9 |
14 |
64% |
Division B: Mining |
1 |
4 |
25% |
Division C: Construction |
6 |
46 |
35% |
Division D: Manufacturing |
232 |
627 |
37% |
Division E: Transportation, Communications, Electric,
Gas, and Sanitary Services |
48 |
119 |
40% |
Division F: Wholesale Trade |
5 |
14 |
36% |
Division G: Retail Trade |
0 |
2 |
0% |
Division H: Finance, Insurance, and Real Estate |
1 |
1 |
100% |
Division I: Services |
27 |
76 |
36% |
Division J: Public Administration |
0 |
0 |
0% |
Total Respondents |
380 |
1,107 |
34% |
Size of Site |
Number of Sites |
Small (0-99 employees) |
61 |
Medium (100-499 employees) |
92 |
Large (500+ employees) |
38 |
Total Respondents |
191 |
3.0 MENTORING EFFORTS
3.1 The Overall Impact of Mentoring
Respondents were first asked about the mentoring activities that they (and their own company) had
conducted. Mentoring is one-on-one assistance from a VPP participant to a prospective participant,
either within or outside of a particular organization, to help the organization improve its safety
and health management systems, prepare an application for VPP, or prepare for an onsite evaluation
by OSHA.
NOTE: In most questions asked, at least one "outlier" was found. For these purposes, an
"outlier" is considered to be any data point more than two standard deviations from the mean." When a listing of
data are presented, all data, including outliers, are shown. However, for purposes of statistical
analysis, outliers were eliminated. Outliers throughout this document are indicated by an asterisk "*".
Of the 338 respondents who answered the question, 69% said they had conducted some mentoring
activities in the past 12 months.
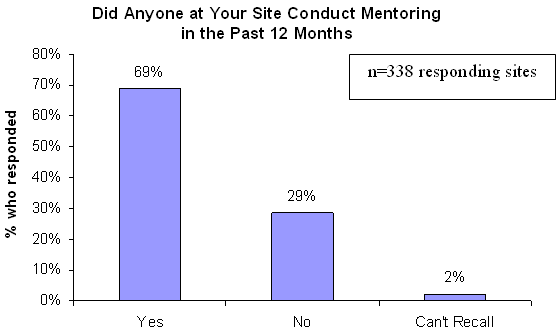
Text Version of Chart Data:
Chart Title: Did Anyone at Your Site Conduct Mentoring in the Past 12 Months
Chart Type: Vertical Bar
Chart Elements: 3 - One bar for each answer showing the percentage of responding sites
Values:
- Yes = 69%
- No = 29%
- Cant Recall = 2%
n=338 responding sites
Question asked: Did you or anyone at your site perform any mentoring activities related to the
Voluntary Protection Programs (VPP) in the one-year period from January 1, 2004 through December 31,
2004 either within or outside your company?
From there, respondents were asked specifics about their current mentoring activities.
FINDING: In the majority of cases (60%), mentoring is conducted by one or two persons per site. An
additional 18% have three persons conducting mentoring. |
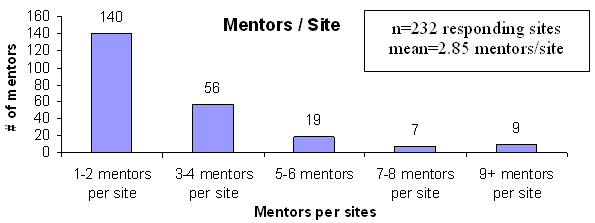
Text Version of Chart Data:
Chart Title: Mentors / Site
Chart Type: Vertical Bar
Chart Elements: 5 - One bar for each mentor range showing the number of mentors
Values:
- 1-2 mentors per site = 140
- 3-4 mentors per site = 56
- 5-6 mentors per site = 19
- 7-8 mentors per site = 7
- 9+ mentors per site = 9
n=232 responding sites
mean=2.85 mentors/site
Question asked: How many people at your site, including yourself, performed mentoring activities
related to VPP in the one-year period from January 1, 2004 through December 31, 2004 either within
or outside your company? (see full data table in Appendix C)
FINDING: In total, respondents reported 812 mentors
working during calendar year 2004. If the outlier is dropped and the mentors are extrapolated to
the entire federal VPP population, Gallup conservatively estimates that in calendar year 2004,
2,365 people mentored in some capacity. |
Finally, a last question asked the number of years the respondent’s site had been mentoring.
FINDING: Mentoring is an activity that has attracted
significantly more participation recently; over two-thirds of mentors (68%) say they have been
conducting mentoring at their site for three years or less. |

Text Version of Chart Data:
Chart Title: Years Your Site Had at Least One Person Mentoring
Chart Type: Vertical Bar
Chart Elements: 5 - One bar for each year range showing the percentage of responding sites
Values:
- < 4 yrs = 68%
- 4-6 yrs = 12%
- 7-8 yrs = 5%
- 9-10 yrs = 4%
- 11+ yrs = 2%
n=344 responding sites
mean=2.6 years/site
Question asked: Since your site was approved for VPP, how many years has your site had at least one
person conducting mentoring either within or outside of your company? (see full data table in
Appendix C)
Of the 335 sites that said they have performed mentoring in the past, 51 sites, or 15%, said they
used to conduct mentoring, but no longer do. This indicates that since inception, the VPP has lost
approximately 15% of its mentors. Looking closer at those 51 sites, 44 of them provided their date
of acceptance into VPP and we can see that one-half (50%) were in VPP between 5 and 10 years.

Text Version of Chart Data:
Chart Title: Sites That No Longer Mentor by Tenure in VPP
Chart Type: Vertical Bar
Chart Elements: 4 - One bar for each year range showing the number of sites
Values:
- 1 to <3 years = 6
- 10+ years= 11
- 3 to <5 years = 5
- 5 to <10 years = 22
n=44 of the 51 sites provided their date of acceptance
NOTE: This includes mentoring both inside and outside a site’s company.
Corresponding to the recent influx of mentors, the majority of mentoring sites have mentored a few
sites each. Over two-thirds, 66%, have mentored less than five sites since their approval into the
VPP program. Dropping the outlier, the average site has mentored 1.19 facilities since its inception
into VPP.
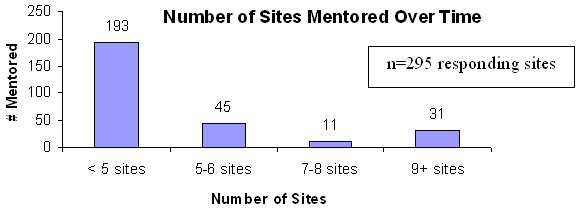
Text Version of Chart Data:
Chart Title: Number of Sites Mentored Over Time
Chart Type: Vertical Bar
Chart Elements: 4 - One bar for each site range showing the number mentored
Values:
- < 5 sites = 193
- 5-6 sites = 45
- 7-8 sites = 11
- 9+ sites = 31
n=295 responding sites
Question asked: Since your site was approved for VPP, approximately how many facilities has your VPP
site mentored either within or outside of your own company?
It is also worth considering the amount of mentoring being undertaken by length of tenure with VPP.
Gallup divided length of tenure with VPP into four categories: under 3 years, 3 to 5 years, 5 to 10
years, and over 10 years.
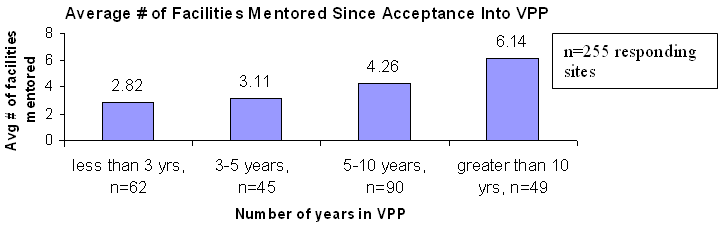
Text Version of Chart Data:
Chart Title: Average # of Facilities Mentored Since Acceptance Into VPP
Chart Type: Vertical Bar
Chart Elements: 4 - One bar for each year range and sites showing the Average number of facilities
mentored
Values:
- less than 3 yrs, n=62: = 2.82
- 3-5 yrs, n=45 = 3.11
- 5-10 years, n=90 = 4.26
- greater than 10 yrs, n=49 = 6.14
n=255 responding sites
NOTE: This includes mentoring both inside and outside a site’s company.
As the graph above shows, the longer a site is in VPP, the more facilities it is likely to mentor.
However, there appears to be a drop-off rate over time (or a decreasing rate of return) such that
older sites tend to mentor fewer facilities as they age with the program — it appears that over
time, enthusiasm for mentoring may wane among participants.
Respondents were next asked how many of those sites they mentored had been accepted into VPP
subsequent to their mentoring activities (excluding the outlier). Of the 1,295 sites reported to
have been mentored over time, 593 were accepted into VPP for a 46% acceptance rate.
FINDING: Of those reportedly mentored in the past,
46% were accepted into VPP. |
When considered by tenure, it is also the case that the longer a site has been in VPP, the more
facilities it mentored are accepted into VPP.

Text Version of Chart Data:
Chart Title: Average # of Facilities Mentored Who Were Subsequently Accepted into VPP
Chart Type: Vertical Bar
Chart Elements: 4 - One bar for each year range showing the Average number of sites mentored
Values:
- less than 3 yrs, n=31: = 0.68
- 3-5 yrs, n=29 = 1.53
- 5-10 years, n=65 = 1.99
- greater than 10 yrs, n=44 = 3.84
n=162 responding sites
NOTE: This includes mentoring both inside and outside a site’s company.
Mentoring was considered next by industry type in response to asking the question, "Does mentoring
differ by SIC code?" Because of the array of SIC codes indicating industry type, Gallup divided the
SIC codes into the 10 SIC divisions. Respondents for this questionnaire fell into the following
divisions:
SIC Division |
Number of Respondents |
Not given |
41 |
Division A: Agriculture, Forestry, and Fishing |
9 |
Division B: Mining |
1 |
Division C: Construction |
6 |
Division D: Manufacturing |
232 |
Division E: Transportation, Communications, Electric,
Gas, and Sanitary Services |
48 |
Division F: Wholesale Trade |
5 |
Division G: Retail Trade |
0 |
Division H: Finance, Insurance, and Real Estate |
1 |
Division I: Services |
27 |
Division J: Public Administration |
0 |
Total Respondents |
380 |
By SIC division, there is sufficient sample to complete an analysis for Manufacturing,
Transportation/ Communications/Electric/Gas/Sanitary Services, and Services. To conduct the analysis
by industry, Gallup held tenure constant so that the length of time with VPP would not be a factor.
Based on these three divisions, it appears that sites in the manufacturing division conduct fewer
mentoring activities than do those in the other two divisions. Manufacturing VPP sites, over time,
mentored an average of 3.4 sites while services VPP sites mentored an average of 6.1 sites.
SIC Division
|
Mean Number of Sites
Mentored Since Inception
|
Division D: Manufacturing
Division E: Transportation, Communications, Electric, Gas, and Sanitary Services
Division I: Services |
3.4 sites
5.3 sites
6.1 sites |
The number of sites mentored was also considered by the number of employees at the site. Since
Gallup did not have the exact number of current employees at a site, a proxy was used — the number
of employees at a given site the year they were approved into VPP.

Text Version of Chart Data:
Chart Title: Since Your Site Was Approved for VPP on Average How Many Sites Have You Mentored? by
Number of Employees
Chart Type: Vertical Bar
Chart Elements: 3 - One bar for each employee range showing the Average number of sites mentored
Values:
- small (<99 employees), n=45: = 2.51
- medium (100-499 employees), n=82 = 3.41
- large (500+ employees), n=34 = 6.50
n=161 responding sites
Question asked: Since your site was approved for VPP, approximately how many facilities has your VPP
site mentored either within or outside of our own company?
It appears that the larger a site is, the more mentoring it is practicing.
3.2 Specifics About Recent Mentoring Experiences
The next series of questions asked respondents about specific mentoring experiences over the past
year (2004). Respondents were asked three questions about their most recent mentoring experiences:
1) Name of the site they mentored, 2) Number of employees working at that site, and 3) If the
facility was inside or outside their own company.
Respondents reported they had mentored 544 sites in 2004. For these 544 sites, respondents noted
there were a total of 181,784 employees working at those sites for an average of 334 employees being
mentored per site.
FINDING: Of the 544 sites mentored in 2004, 50% were
reported to be within the mentor’s own company and 50% were reported to be outside of the mentor’s
company. |
If we first extrapolate the number of sites from the 544 to the entire population, we estimate that
1,584 sites were mentored in some capacity in 2004.
FINDING: An estimated 1,584 sites were mentored in
some capacity in 2004. If that number is multiplied by the employees touched by those efforts,
Gallup conservatively estimates that 529,000 employees were touched in some way by VPP mentors in
calendar year 2004. |
Respondents were asked if they were required to do mentoring
within their own companies. Almost one-third (29%) said yes, they were required to perform mentoring
activities internally.

Text Version of Chart Data:
Chart Title: Does Your Company Require You To Mentor Facilities Within Your Own Company?
Chart Type: Vertical Bar
Chart Elements: 3 - One bar for each answer showing the percentage of responding sites
Values:
- Yes = 29%
- No = 64%
- Don't Know = 6%
n=216
Question asked: Does your company require you or others at your site to mentor facilities within
your company?
The next set of questions asked mentors how much mentoring they did for sites that were not focused
on acceptance into the VPP.
FINDING: Seventy-five percent of respondents who
conducted mentoring reported working in some capacity with sites NOT working toward acceptance
into the VPP. |
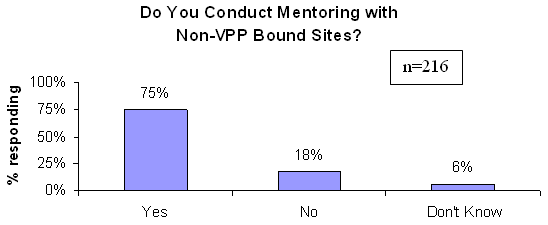
Text Version of Chart Data:
Chart Title: Do You Conduct Mentoring with Non-VPP Bound Sites?
Chart Type: Vertical Bar
Chart Elements: 3 - One bar for each answer showing the percentage of responding sites
Values:
- Yes = 75%
- No = 18%
- Don't Know = 6%
n=216
Question asked: Does your site perform any mentoring activities with facilities both within and
outside your company that are not working towards approval into the VPP, for example, facilities
that just want advice on improving the safety and health of their worksites?
The question was followed up with an hourly estimate. The following chart compares the mentoring
activities and how those respondents who conduct mentoring reported the number of hours spent per
year conducting each of the activities.
When asked about the hours they spent on each of these activities, respondents reported spending 6.7
hours per month/80.8 hours per year mentoring OUTSIDE their company sites, and 8.9 hours per
month/106.7 hours per year mentoring INSIDE their company.
FINDING: Although respondents reported an equal
number of sites being mentored within and outside of their company in the past 12 months, mentors
are spending more time mentoring within rather than outside of their own companies. |

Text Version of Chart Data:
Chart Title: Yearly Hours Spent on Mentoring
Chart Type: Vertical Bar
Chart Elements: 2 - One bar for each area time is spent showing the yearly hours
Values:
- Inside Your Company, n=216 = 106.7
- Outside Your Company, n=219 = 80.8
Among those conducting mentoring with non-VPP bound sites, the average amount of time spent was
approximately 30 hours per year (n=163 sites).
The next section analyzed whether those who were conducting the mentoring were overlapping and
conducting both internal and external mentoring. Were those who were conducting mentoring doing it
with both internal and external sites or just one type of site? It turns out, about one-half were
mentoring both internal and external sites whereas the other half were mentoring one type.
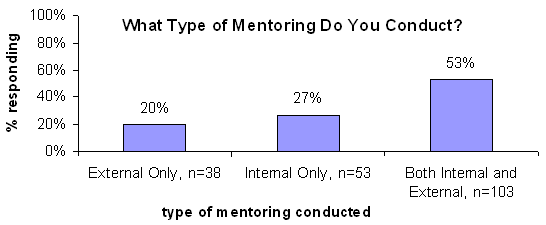
Text Version of Chart Data:
Chart Title: What Type of Mentoring Do You Conduct?
Chart Type: Vertical Bar
Chart Elements: 3 - One bar for each mentoring type showing the percentage of responding sites
Values:
- External Only, n=38 = 20%
- Internal Only, n=53 = 27%
- Both Internal and External, n=103 = 53%
A final set of questions asked respondents about the quantity of mentoring they planned on
conducting in the future. To what extent did mentors believe that they would be conducting more,
less, or about the same amount of mentoring in the future as they have in the past 12 months?
The majority of respondents said they would either do the same (43%) or more (32%) mentoring than in
the past. Only 1% respondents said they would do less.

Text Version of Chart Data:
Chart Title: Does Your Site Plan to do More, Less, or About the Same Amount of Mentoring in the
Future?
Chart Type: Vertical Bar
Chart Elements: 4 - One bar for each answer showing the percentage of responding sites
Values:
- More = 32%
- Less = 1%
- Same = 43%
- Don't Know = 24%
n=331
Question asked: In the next three years does your site plan to do more, less, or about the same
amount of mentoring that you did in the past 12 months for facilities both within and outside your
company?
Further exploration of the 32% who said they would be willing to do "more" mentoring revealed a
similar population to the current VPP population, namely newer to VPP (54% were in VPP for under
five years), and they tended to be employed at the larger sites (75% had over 100 employees).
For those respondents who planned on doing more mentoring, when asked how much more mentoring, an
average 15.78 hours per month was given by 101 respondents.

Text Version of Chart Data:
Chart Title: Additional Hours Willing To Mentor
Chart Type: Vertical Bar
Chart Elements: 6 - One bar for each hour range showing the number of sites
Values:
- 1-3 hrs = 7
- 4-6 hrs = 17
- 7-10 hrs = 32
- 11-15 hrs = 14
- 16-20 hrs = 19
- 25+ hrs = 18
n=101
mean=15.78 hrs
Question asked: How many hours per month would your site be willing to mentor other facilities both
within and outside your company in the future?
4.0 OUTREACH EFFORTS
4.1 The Overall Impact of Outreach
Respondents were asked if they conducted outreach activities in the past 12 months either at the
request of OSHA or for other organizations (non-OSHA related). Outreach includes assistance and
information provided to prospective VPP applicants such as conducting VPP workshops and training,
holding community safety days, and serving as an advocate for the VPP. Outreach also includes
assistance and information provided to internal or external corporate entities to promote safety and
health principles and practices, including OSHA Strategic Partnerships and Alliances, making
presentations on safety and health at conferences, or conducting training workshops. Outreach
includes those activities conducted at the request of OSHA or at the request of other organizations.
FINDING: One-half of respondents said they conducted
outreach activities in the calendar year 2004 at the request of OSHA and 45% conducted outreach
activities at the request of other organizations. |
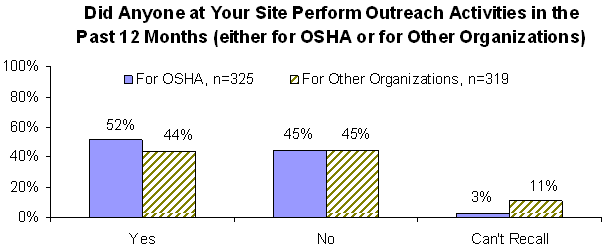
Text Version of Chart Data:
Chart Title: Did Anyone at Your Site Perform Outreach Activities in the Past 12 Months (either for
OSHA or for Other Organizations)
Chart Type: Vertical Bar
Chart Elements: 6 - Two bars for each answer showing the percentage of sites
Values:
- For OSHA, n=325
- Yes = 52%
- No = 45%
- Can't Recall = 3%
- For Other Organizations, n=319
- Yes = 44%
- No = 45%
- Can't Recall = 11%
Question asked: Did you or anyone at your site perform outreach activities either at the request of
OSHA or at the request of Other Organizations in the one year period January 1, 2004 through
December 31, 2004.
As with mentoring activities, a majority of respondents noted they have been conducting outreach
activities recently. The average is 3.87 years of outreach activities per site.
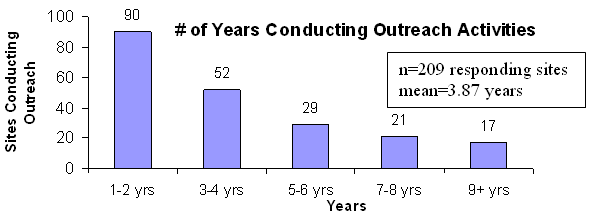
Text Version of Chart Data:
Chart Title: # of Years Conducting Outreach Activities
Chart Type: Vertical Bar
Chart Elements: 5 - One bar for each year range showing the number of sites
Values:
- 1-2 yrs = 90
- 3-4 yrs = 52
- 5-6 yrs = 29
- 7-8 yrs = 21
- 9+ yrs = 17
n=209 responding sites
mean=3.87 years
Question asked: Since your site was approved for VPP, how many years has your site had at least one
person conducting outreach activities either at the request of OSHA or at the request of other
organizations? Please only count years when outreach occurred?
Of the 209 sites who said they have performed outreach in the past, 52% said they conducted outreach
in the past 12 months for OSHA (the other 48% said they did not) while an additional 44% said they
conducted outreach in the past 12 months for other, non-OSHA related organizations (the other 56%
said they did not).
FINDING: Among those who said they have conducted
outreach in the past, one-half have done some outreach in the past 12 months for either OSHA or
other organizations. |
When asked how many employees conducted outreach at the request of OSHA, over one-half said one
person.
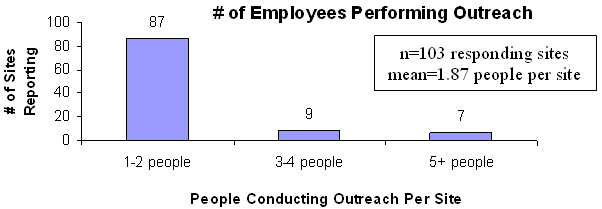
Text Version of Chart Data:
Chart Title: # of Employees Performing Outreach
Chart Type: Vertical Bar
Chart Elements: 3 - One bar for each employee range showing the number of sites
Values:
- 1-2 people = 87
- 3-4 people = 9
- 5+ people = 7
n=103 responding sites
mean=1.87 years
Question asked: How many people at your site, including yourself performed outreach activities at
the request of OSHA in the one year period January 1, 2004 through December 31, 2004
4.2 Specific Outreach Activities Conducted at the Request of OSHA
Respondents were asked what kind of activities they had conducted in the 2004 calendar year at the
request of OSHA. Eight specific activities were queried and an additional open-ended answer allowed
respondents to add more activities.

Text Version of Chart Data:
Chart Title: Which Outreach Activities Did You Conduct in the Past 12 Months
Chart Type: Vertical Bar
Chart Elements: 9 - One bar for each outreach activity showing the number of sites
Values:
- Providing Training in Support of VPP = 185
- Safety and Health Workshops = 118
- Advocate in the Business Community = 112
- Presentations on Safety and Health issues at conferences = 68
- Other = 41
- Community Safety Days/Outreach Days = 26
- Strategic Partnerships and Alliances = 24
- Strengthening Star Quality Workshops = 18
- VPP Application Workshops = 15
n=209 responding sites
Question asked: How many times in the one year period January 1, 2004, through December 31, 2004 did
you and others at your site conduct the following activities at the request of OSHA.
Note: Multiple responses were allowed by each site.
These numbers can be extrapolated to the VPP population at large.
FINDING: Gallup estimates that among all VPP
participants, some 2,200 activities were conducted during calendar year 2004 at the request of
OSHA. |
Of the 753 activities mentioned by respondents (multiple responses were allowed by each site),
one-quarter were for providing training in support of VPP.
For those sites that conducted additional "other" outreach activities (29 mentions), the following
list provided the additional outreach activities.
Outreach events reported at the request of OSHA
- Advocate at Pratt & Whitney
- Attended VPPPA workshop/conference (2 mentions)
- Calls to discuss VPP program (6 mentions)
- Electrical workshop at TSTC Safety Expo; mentored two out-of-state electrical utilities; local
safety seminars
- Hispanic taskforce presentation
- Hosting Region 5 VPP meeting
- Onsite and conference call
- Providing info for safety team (3 mentions)
- Region 6 VPPPA Web site
- Serving as VPPPA board members
- Serving on Region 3 VPPPA Board of Directors – aiding in annual conference
- SGE duties (11 mentions)
- The site, at the request of OSHA, hosted a delegation from Ireland who have now adopted their own
version of VPP
When asked how much time the outreach coordinators spent on outreach activities, responses varied by
type of activity. The table below has each of the eight activities listed and information about
each. However, respondents did not necessarily report information for every event. The table shows
the number of times that activity was conducted overall, and then information on hours and attendees
for some of the events. An average was calculated for those who reported information on a given
event.
Extrapolated outreach information at the request of OSHA |
|
Total Events Reported |
(A) Total hours reported |
(B) # events where hours were
reported in (A) |
(C) = (A)/(B) Avg # of hours spent
per event |
(D) Total attendance reported |
(E) # of events where attendance is
reported in (D) |
(F) = (D)/(E) avg # of people per
event reported |
Providing training in support of VPP |
185 |
3,787 |
164 |
23.09 |
6,272 |
105 |
60 |
Community Safety Days/Outreach Days |
68 |
1,070 |
63 |
16.98 |
9,406 |
64 |
147 |
Advocate in the business community |
112 |
957 |
101 |
9.48 |
3,731 |
88 |
42 |
Strengthening Star Quality Workshops |
26 |
597 |
22 |
27.14 |
837 |
20 |
42 |
Safety and health workshops |
118 |
1,888 |
98 |
19.27 |
5,861 |
89 |
66 |
Strategic Partnerships and Alliances |
41 |
319 |
21 |
15.19 |
849 |
26 |
33 |
Presentations on safety and health issues at
conferences |
109 |
1,665 |
96 |
17.34 |
9,416 |
94 |
100 |
VPP application workshops |
20 |
166 |
16 |
10.38 |
796 |
4 |
199 |
Other |
71 |
1,827 |
67 |
27.27 |
3,166 |
48 |
66 |
|
743 |
12,276 |
648 |
|
40,334 |
538 |
|
When the number of activities, the hours, and attendance were extrapolated to the entire VPP
population, the table below shows Gallup’s estimate of activity in calendar year 2004 at the request
of OSHA.
|
(G)
# events extrapolated to entire VPP population |
(H)=(G) × (C)
Total hours spent on this event extrapolated to entire VPP population |
(I) =(G) × (F)
Total attendance at activity, extrapolated to entire VPP population |
Providing training in support of VPP |
539 |
12,446 |
32,340 |
Community Safety Days/Outreach Days |
198 |
3,362 |
29,106 |
Advocate in the business community |
326 |
3,090 |
13,692 |
Strengthening Star Quality Workshops |
76 |
2,063 |
3,192 |
Safety and health workshops |
344 |
6,629 |
22,704 |
Strategic Partnerships and Alliances |
119 |
1,808 |
3,927 |
Presentations on safety and health issues at conferences |
318 |
5,514 |
31,800 |
VPP application workshops |
58 |
602 |
11,542 |
Other |
216 |
5,890 |
14,256 |
|
2,194 events |
41,404 hrs |
162,599 attendees |
NOTE: Column G is calculated by multiplying the total extrapolated number of events (see above in
FINDINGS box) by the percentage of occurrence for that event in 2004.
FINDING: Gallup estimates that, at the REQUEST OF
OSHA, approximately 2,200 outreach activities were conducted at a cost of 41,400 hours of activity
for 163,000 attendees during calendar year 2004. |
The next question in this section asked respondents if the activities they were conducting were
within their company or outside of their company. The responses varied by activity. For example,
just under one-half (45%) of those conducting safety and health workshops did so within their own
companies.
|
% of activities conducted within own
company |
Providing training in support of VPP |
45% |
Community Safety days/Outreach days |
39% |
Advocate in the business community |
13% |
Strengthening Star Quality workshops |
9% |
Safety and health workshops |
48% |
Strategic partnerships and alliances |
18% |
Presentations on safety and health issues at
conferences |
31% |
VPP application workshops |
28% |
Other |
8% |
Question asked: Was this activity within your own company?
The final question asked respondents if they are planning on doing more, less, or about the same
amount of outreach activities at the request of OSHA in the next three years as they have done in
the past year.
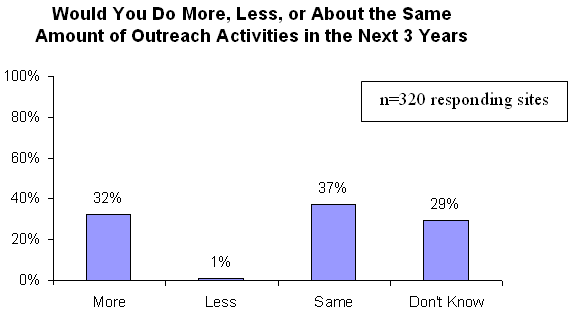
Text Version of Chart Data:
Chart Title: Would You Do More, Less, or About the Same Amount of Outreach Activities in the Next 3
Years
Chart Type: Vertical Bar
Chart Elements: 4 - One bar for each answer showing the percentage of sites
Values:
- More = 32%
- Less = 1%
- Same = 37%
- Don't Know = 29%
n=320 responding sites
Question asked: In the next three years does your site plan to do more, less, or about the same
amount of outreach activities at the request of OSHA than you did in the past 12 months?
When people were asked how much more outreach activities they were interested in conducting, the
following chart outlines the responses. The average was an additional 11.5 hours a year that
respondents were willing to spend.
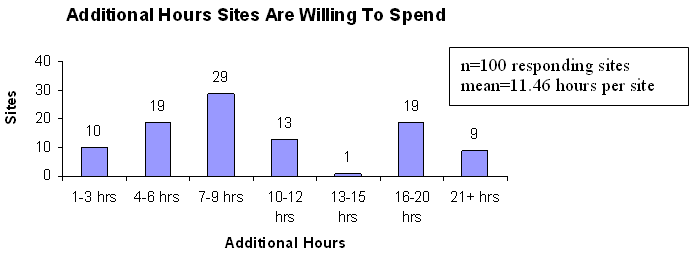
Text Version of Chart Data:
Chart Title: Additional Hours Sites Are Willing To Spend
Chart Type: Vertical Bar
Chart Elements: 7 - One bar for each hour range showing the number of sites
Values:
- 1-3 hrs = 10
- 4-6 hrs = 19
- 7-9 hrs = 29
- 10-12 hrs = 13
- 13-15 hrs = 1
- 16-20 hrs = 19
- 21+ hrs = 9
n=100 responding sites
mean=11.46 hours per site
Question asked: On average, how many hours per month would your site be willing to provide related
outreach activities at the request of OSHA in the future?
Further exploration of the 32% who said they would be willing to do "more" outreach activities
revealed a similar population to the current VPP population, namely newer to VPP (57% were in VPP
for under five years), and they tended to be employed at the larger sites (75% had over 110
employees).
4.2.2 Characteristics of Those Conducting Outreach at the Request of OSHA
We next considered who the people were that were conducting outreach activities at the request of
OSHA, what characteristics did they share, and what types of activities and amount of activities
were they conducting.
Segmentation by SIC code was considered, however, due to the lack of diversity in SIC codes, only
one division was available for further analysis namely, manufacturing. However, from the graph
below, we see that all SIC divisions did, in fact, participate about equally in outreach activities
with construction companies participating slightly more than other divisions.

Text Version of Chart Data:
Chart Title: Companies Conducting Outreach At The Request of OSHA
Chart Type: Vertical Bar
Chart Elements: 4 - One bar for each SIC Division showing the number of sites
Values:
- Construction = 5
- Manufacturing = 80
- Transportation, Communication = 11
- Services = 7
% of Total Questionnaire Respondents in Divisional Category:
- Construction = 38%
- Manufacturing = 35%
- Transportation, Communication = 23%
- Services = 26%
n=104 responding sites
Among manufacturing sites, those that performed outreach were providing more
training in support of VPP and presentations on safety and health issues at conferences
than other outreach activities.
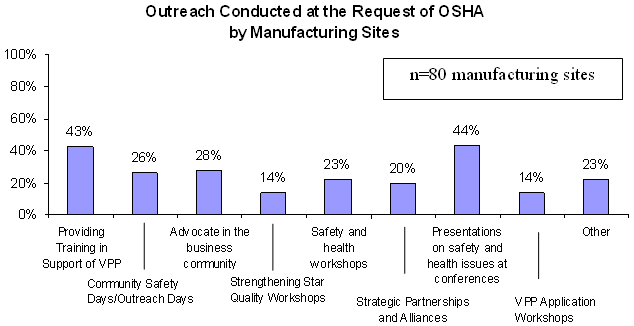
Text Version of Chart Data:
Chart Title: Outreach Conducted at the Request of OSHA by Manufacturing Sites
Chart Type: Vertical Bar
Chart Elements: 9 - One bar for each Outreach Activity showing the percentage of sites
Values:
- Providing Training in Support of VPP = 43%
- Community Safety Days/Outreach Days = 26%
- Advocate in the business community = 28%
- Strengthening Star Quality Workshops = 14%
- Safety and health workshops = 23%
- Strategic Partnerships and Alliances = 20%
- Presentations on safety and health issues at conferences = 44%
- VPP Application Workshops = 14%
- Other = 23%
n=80 manufacturing sites
Another way to consider these outreach data are by employee size. It appears
that those that performed outreach work at sites of various sizes, as seen below.
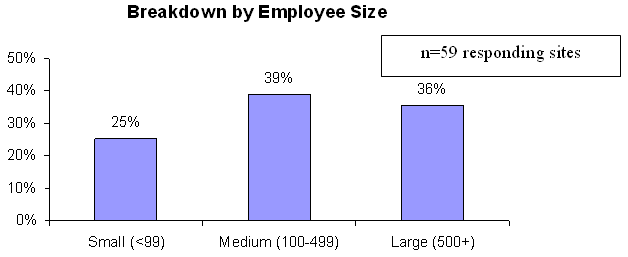
Text Version of Chart Data:
Chart Title: Breakdown by Employee Size
Chart Type: Vertical Bar
Chart Elements: 3 - One bar for each employee range showing the percentage of sites
Values:
- Small (<99) = 25%
- Medium (100-499) = 39%
- Large (500+) = 36%
n=59 responding sites
Having looked at the specific outreach activities by employee size, some
differentiation was apparent.
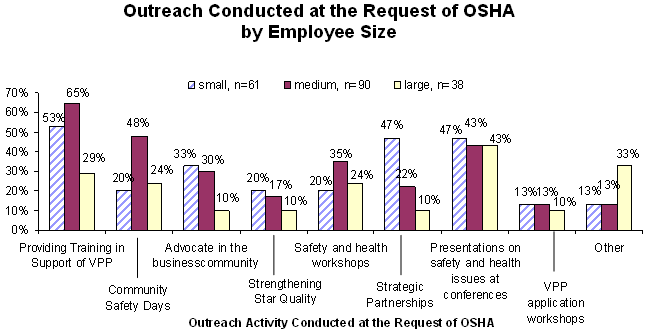
Text Version of Chart Data:
Chart Title: Outreach Conducted at the Request of OSHA by Employee Size
Chart Type: Vertical Bar
Chart Elements: 27 - Three bars for each Outreach Activity showing the percentage of sites
Values:
- Small, n=61
- Providing Training in Support of VPP = 53%
- Community Safety Days = 20%
- Advocate in the business community = 33%
- Strengthening Star Quality Workshops = 20%
- Safety and health workshops = 20%
- Strategic Partnerships and Alliances = 47%
- Presentations on safety and health issues at conferences = 47%
- VPP Application Workshops = 13%
- Other = 13%
- Medium, n=90
- Providing Training in Support of VPP = 65%
- Community Safety Days = 48%
- Advocate in the business community = 30%
- Strengthening Star Quality Workshops = 17%
- Safety and health workshops = 35%
- Strategic Partnerships and Alliances = 22%
- Presentations on safety and health issues at conferences = 43%
- VPP Application Workshops = 13%
- Other = 13%
- Large, n=38
- Providing Training in Support of VPP = 29%
- Community Safety Days = 24%
- Advocate in the business community = 10%
- Strengthening Star Quality Workshops = 10%
- Safety and health workshops = 24%
- Strategic Partnerships and Alliances = 10%
- Presentations on safety and health issues at conferences = 43%
- VPP Application Workshops = 10%
- Other = 33%
Smaller and medium-sized sites preferred providing
training in support of VPP and presentations on safety and health issues at conferences,
while larger sites preferred presentations on safety and
health issues at conferences and other activities. Smaller
sites also showed a preference for strategic partnerships while
medium-sized sites did more community safety and outreach days.
4.3 Specific Outreach Activities Conducted at the Request of Other Organizations
Respondents were asked what kind of activities they had conducted in the 2004 calendar year at the
request of other organizations (not OSHA). Eight specific activities were queried and an additional
open-ended answer allowed respondents to add more activities.
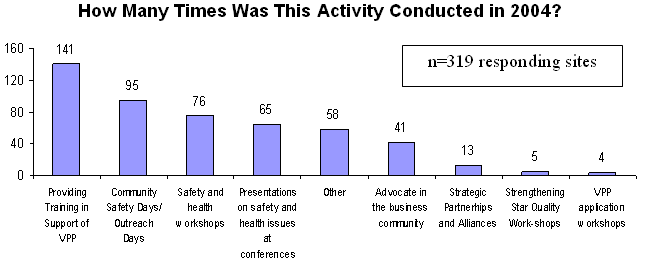
Text Version of Chart Data:
Chart Title: How Many Times Was This Activity Conducted in 2004?
Chart Type: Vertical Bar
Chart Elements: 9 - One bar for each activity showing the number of sites
Values:
- Providing Training in Support of VPP = 141
- Community Safety Days/Outreach Days = 95
- Safety and health workshops = 76
- Presentations on safety and health issues at conferences = 65
- Other = 58
- Advocate in the business community = 41
- Strategic Partnerships and Alliances = 13
- Strengthening Star Quality Workshops = 5
- VPP application workshops = 4
n=319 responding sites
Question asked: How many times in the one year period January 1, 2004, through December 31, 2004 did
you and others at your site conduct the following activities at the request of Other Organizations.
Note: Multiple responses were allowed by each site.
These numbers can be extrapolated to the population at large.
FINDING: Gallup estimated that among all federal VPP
participants, some 1,551 outreach activities were conducted during calendar year 2004 at the
request of organizations other than OSHA. |
Of the 498 activities mentioned by respondents (multiple responses were allowed by each site), over
one-quarter (28%) were for providing training in support of VPP.
For those sites that conducted additional "other" outreach activities (58 mentions), the following
activities were mentioned as comprising that category (not all respondents filled in the outreach
activities they completed).
Outreach events reported at the request of organizations other than OSHA
- Advocate at local business safety meetings
- Assisted in work permit system development
- Assisted with planning safety workshop
- Contractor safety meetings
- Earth Day, and other community activities
- Gave other business perspective on how we attained VPP (2 mentions)
- Helped with OSHA Challenge through ABC and Mid-America OSHA
- Logging safety
- Mentored (2 mentions)
- Middle Georgia Occupation Health Nurse Association
- OSHA requested we participate at local corporate training session
- Other training on different safety topics
- Outreach for SRP Centennial Power; Weststar Energy; (3) Texas Genco Power Plants
- Preparation for VPPPA regional conference
- Provided information to other sites applying for OSHA Star (2 mentions)
- Region 6 VPPPA Web site
- Site safety audit (2 mentions)
- Spoke to Hattiesburg chapter of ASSE
- TCC Outreach Committee
- Conducted tours
When asked how much time the outreach coordinators spent on outreach activities, responses varied by
type of activity. The table below has each of the eight activities listed and information about
each. However, respondents did not necessarily report information for every event. The table shows
the number of times that activity was conducted overall, and then information on hours and attendees
for some of the events. An average was calculated for those who reported information on a given
event.
Extrapolated outreach information at the request of
organizations other than OSHA |
|
Total Events Reported |
(A) Total hours reported |
(B) # events where hours were
reported in (A) |
(C) = (A)/(B) avg # of hours spent
per event |
(D) Total attendance reported |
(E) # of events where attendance is
reported in (D) |
(F) = (D)/(E) avg # of people per
event reported |
Providing training in support of VPP |
141 |
2,519 |
119 |
21.17 |
4,422 |
119 |
37 |
Community Safety Days/Outreach Days |
95 |
1,470 |
64 |
22.97 |
9,217 |
72 |
128 |
Advocate in the business community |
41 |
287 |
35 |
8.20 |
859 |
41 |
21 |
Strengthening Star Quality Workshops |
5 |
38 |
5 |
7.60 |
138 |
5 |
28 |
Safety and health workshops |
76 |
1,087 |
71 |
15.31 |
3,395 |
71 |
48 |
Strategic Partnerships and Alliances |
13 |
62 |
11 |
5.64 |
295 |
11 |
27 |
Presentations on safety and health issues at
conferences |
65 |
1,249 |
65 |
19.22 |
3,908 |
64 |
61 |
VPP application workshops |
4 |
78 |
4 |
19.50 |
796 |
4 |
199 |
Other |
58 |
1,422 |
57 |
24.95 |
1,627 |
55 |
30 |
|
498 |
8,212 |
431 |
|
24,657 |
442 |
|
When the number of activities, the hours, and attendance were extrapolated to the entire VPP
population, the table below shows Gallup’s estimate of activity in calendar year 2004 at the request
of other organizations.
|
(G)
# events extrapolated to entire VPP population |
(H)=(G) × (C)
Total hours spent on this event extrapolated to entire VPP population |
(I) =(G) × (F)
Total attendance at activity, extrapolated to entire VPP population |
Providing training in support of VPP |
411 |
8,700 |
15,273 |
Community Safety Days/Outreach Days |
377 |
8,657 |
48,261 |
Advocate in the business community |
119 |
976 |
2,493 |
Strengthening Star Quality Workshops |
15 |
114 |
414 |
Safety and health workshops |
221 |
3,383 |
10,568 |
Strategic Partnerships and Alliances |
38 |
214 |
1,019 |
Presentations on safety and health issues at conferences |
189 |
3,632 |
11,541 |
VPP application workshops |
12 |
234 |
2,388 |
Other |
169 |
4,216 |
4,999 |
|
1,551 events |
30,129 hours |
96,956 people |
NOTE: Column G is calculated by multiplying the total extrapolated number of events (see above in
FINDINGS box) by the percentage of occurrence for that event in 2004
FINDING: Gallup estimates that at the REQUEST OF
ORGANIZATIONS OTHER THAN OSHA approximately 1,500 outreach activities were conducted at a cost of
30,000 hours of activity for 100,000 attendees during calendar year 2004. |
The next question in this section asked respondents if the activities they were conducting were
within their company or outside of their company. The responses varied by activity. For example,
about one-half (49%) of those conducting safety and health workshops did so within their own
companies.
|
% of activities conducted within own
company |
Providing training in support of VPP |
49% |
Community Safety days/Outreach days |
21% |
Advocate in the business community |
24% |
Strengthening Star Quality workshops |
20% |
Safety and health workshops |
50% |
Strategic partnerships and alliances |
36% |
Presentations on safety and health issues at
conferences |
22% |
VPP application workshops |
0% |
Other |
22% |
The final question in this section asked respondents if they were planning on doing more, less, or
about the same amount of outreach activities at the request of other organizations in the next three
years as they have done in the past year. Just under one-third (29%) said they would be willing to
do more outreach.
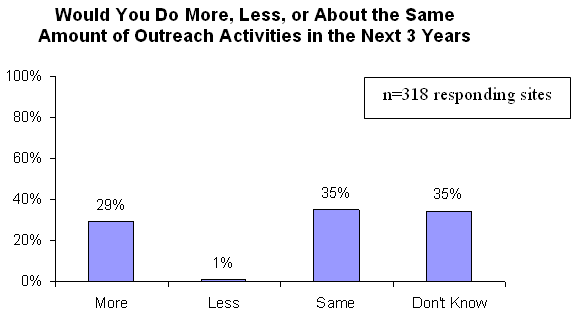
Text Version of Chart Data:
Chart Title: Would You Do More, Less, or About the Same Amount of Outreach Activities in the Next 3
Years
Chart Type: Vertical Bar
Chart Elements: 4 - One bar for each answer showing the percentage of sites
Values:
- More = 29%
- Less = 1%
- Same = 35%
- Don't Know = 35%
n=318 responding sites
Question asked: In the next three years does your site plan to do more, less, or about the same
amount of outreach activities at the request of other organizations than you did in the past 12
months?
When those who said they were willing to do more outreach activities were queried as to how much
more, the following chart shows their responses.
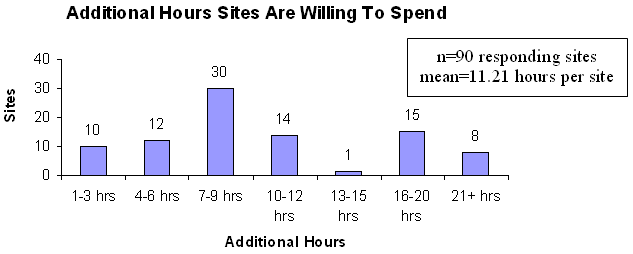
Text Version of Chart Data:
Chart Title: Additional Hours Sites Are Willing To Spend
Chart Type: Vertical Bar
Chart Elements: 7 - One bar for each hour range showing the number of sites
Values:
- 1-3 hrs = 10
- 4-6 hrs = 12
- 7-9 hrs = 30
- 10-12 hrs = 14
- 13-15 hrs = 1
- 16-20 hrs = 15
- 21+ hrs = 8
n=90 responding sites
mean=11.21 hours per site
Question asked: On average, how many hours per month would your site be willing to provide related
outreach activities at the request of organizations other than OSHA in the future?
Those who said they would be willing to conduct more outreach tended to be newer to VPP (61% were in
VPP for under five years). They also tended to work in slightly larger companies (75% had over 125
employees).
4.3.2 Characteristics of Those Conducting Outreach at the Request of Other
Organizations
As with sites conducting outreach at the request of OSHA, the vast majority of sites were in
manufacturing, which provided the only adequate sample that can be used to analyze the type of
outreach activities performed.
Similar to those manufacturing sites conducting outreach at the request of OSHA, most activities
provided at the request of other organizations are for providing training in
support of VPP and presentations on safety and health issues at conferences.
However, this group appeared to do less advocating in the business community
than was done for OSHA. This group also conducted fewer strategic partnership
and alliance work but more VPP application workshop work than
they did at the request of OSHA.
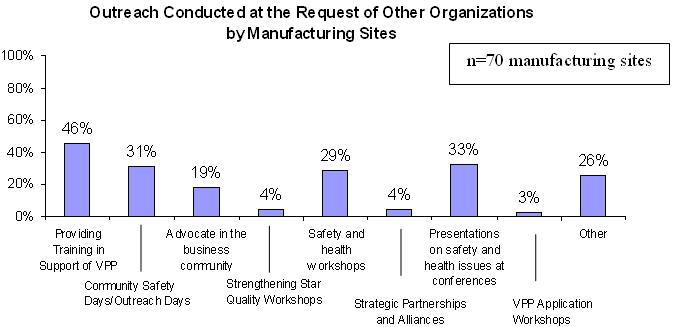
Text Version of Chart Data:
Chart Title: Outreach Conducted at the Request of Other Organizations by Manufacturing Sites
Chart Type: Vertical Bar
Chart Elements: 9 - One bar for each Outreach activity showing the percentage of sites
Values:
- Providing Training in Support of VPP = 46%
- Community Safety Days/Outreach Days = 31%
- Advocate in the business community = 19%
- Strengthening Star Quality Workshops = 4%
- Safety and health workshops = 29%
- Strategic Partnerships and Alliances = 4%
- Presentations on safety and health issues at conferences = 33%
- VPP Application Workshops = 3%
- Other = 26%
n=70 manufacturing sites
When segmenting these data by employee size, some smaller sample sizes appeared. However, we present
these data because when considered overall, a much lower number of respondents conducted outreach at
the request of other organizations and therefore, this sample may be representative of those who
have done these activities.
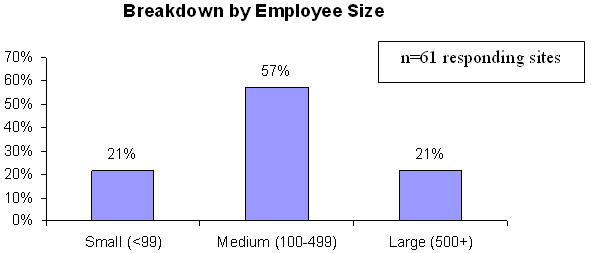
Text Version of Chart Data:
Chart Title: Breakdown by Employee Size
Chart Type: Vertical Bar
Chart Elements: 3 - One bar for each employee range showing the percentage of sites
Values:
- Small (<99) = 21%
- Medium (100-499) = 57%
- Large (500+) = 21%
n=61 manufacturing sites
When segmenting outreach activities for other organizations by employee size of site, some
differences were apparent. Small- and medium-sized sites did more of providing training in support
of VPP and presentations on safety and health issues at conferences
while larger sites did more community safety days/outreach days and
safety and health workshops for other organizations.
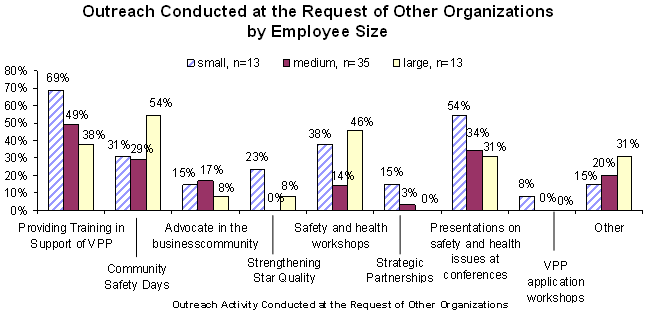
Text Version of Chart Data:
Chart Title: Outreach Conducted at the Request of Other Organizations by Employee Size
Chart Type: Vertical Bar
Chart Elements: 27 - Three bars for each Outreach Activity showing the percentage of sites
Values:
- Small, n=13
- Providing Training in Support of VPP = 69%
- Community Safety Days = 31%
- Advocate in the business community = 15%
- Strengthening Star Quality = 23%
- Safety and health workshops = 38%
- Strategic Partnerships = 15%
- Presentations on safety and health issues at conferences = 54%
- VPP Application Workshops = 8%
- Other = 15%
- Medium, n=35
- Providing Training in Support of VPP = 49%
- Community Safety Days = 29%
- Advocate in the business community = 17%
- Strengthening Star Quality = 0%
- Safety and health workshops = 14%
- Strategic Partnerships = 3%
- Presentations on safety and health issues at conferences = 34%
- VPP Application Workshops = 0%
- Other = 20%
- Large, n=13
- Providing Training in Support of VPP = 38%
- Community Safety Days = 54%
- Advocate in the business community = 8%
- Strengthening Star Quality = 8%
- Safety and health workshops = 46%
- Strategic Partnerships = 0%
- Presentations on safety and health issues at conferences = 31%
- VPP Application Workshops = 0%
- Other = 31%
5.0 PAST DATA COLLECTION EFFORTS
The third and final section of the Web questionnaire consisted of data collected on the sites’
injury and illness data prior to their approval into VPP. Gallup collected data from sites for the
five years prior to acceptance into the program. In total, of the 380 sites that responded to the
questionnaire, approximately 80 were approved into VPP after December 31, 2002, which would require
them to submit data for this questionnaire on OSHA 300 logs [NOTE: 300 logs were required as of
January 1, 2002, however, because we collected data starting with the year prior to approval, for
those who were approved in 2002 and before, we would have only collected 200 log data]. Thirty sites
responded to the questionnaire who were approved in 2004 and 50 sites were approved in 2003. Of the
80 sites that qualified to use at least one year of 300 logs, only 25 sites filled out the 300 logs
on the questionnaire for the years needed. For that reason, the analysis provided below is for only
those sites who submitted all their injury and illness data on OSHA 200 logs, which would be those
sites approved into VPP on or before December 31, 2002, for a total of 295 sites or 92% of all sites
that provided data.
The final part of this section discusses how these same sites have performed on their injury and
illness data once they were accepted into the VPP. Gallup did not collect these data, but these data
were submitted to Gallup by OSHA. We present the data for comparative purposes only.
The remainder of the analysis for this section was based on time-sensitive information and
specifically asked the question, to what extent does time prior to VPP acceptance play a role in the
injury and illness rates of a given site. Or, in other words, is it the case that the further away
from VPP acceptance a given site is, the worse its injury and illness rates are? In addition, in the
analysis, our intention was to review individual differences from year-to-year to understand if any
given year had more of a change in injury and illness rates than any other year.
To answer these questions, several statistical analyses were undertaken. For all analyses, Total
Case Incident Rate (TCIR) and Days Away from work, Restricted work, or job Transfer injury and
illness (DART) rates were used as proxies for injury and illness rates.
READING THE CHARTS BELOW: Because we asked respondents for data from the five years prior to their
acceptance in VPP, year 1 indicates one year prior to their acceptance into VPP, year 2 indicates
two years prior to acceptance into VPP, etc.
First, we examined the mean scores of both TCIR and DART rates for the five years prior to
acceptance into VPP.
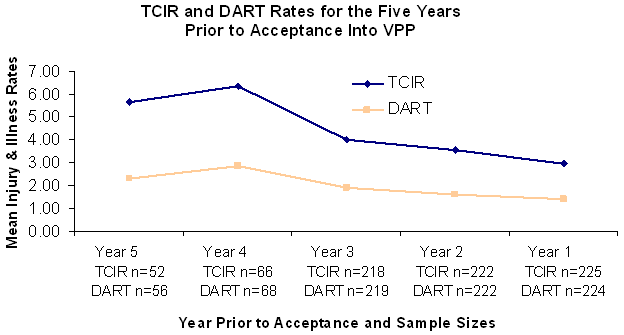
Text Version of Chart Data:
Chart Title: TCIR and DART Rates for the Five Years Prior to Acceptance Into VPP
Chart Type: Line Graph
Chart Elements: 2 - One line for TCIR and one for DART showing the mean scores for the five years
prior to acceptance into VPP
Values:
- TCIR
- Year 5, n=52: 5.66
- Year 4, n=66: 6.36
- Year 3, n=218: 4.00
- Year 2, n=222: 3.53
- Year 1, n=225: 2.94
- DART
- Year 5, n=56: 2.31
- Year 4, n=68: 2.87
- Year 3, n=219: 1.88
- Year 2, n=222: 1.62
- Year 1, n=224: 1.42
FINDING: There was a clear "bump" in the injury and
illness rates in year 4 (four years prior to VPP approval). The most dramatic change in all five
years occurs between year 4 and year 3, as shown in the following chart. This can be explained
because once sites start preparing for VPP, injury and illness rates tend to increase because
sites start implementing better record keeping and reporting procedures. This usually can be
identified four years prior to VPP approval. Additionally, as sites’ safety and health management
systems improve, injury and illness rates tend to decline in the three years prior to VPP
approval. |
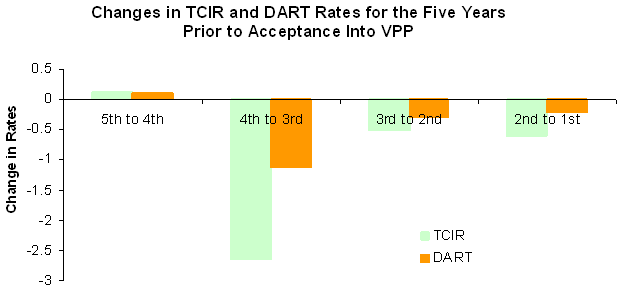
Text Version of Chart Data:
Chart Title: Changes in TCIR and DART Rates for the Five Years Prior to Acceptance
Chart Type: Vertical Bar
Chart Elements: 8 - Two bars for each year change showing the change in rates for both TCIR and DART
Values:
- TCIR
- 5th to 4th = 0.13
- 4th to 3rd = -2.65
- 3rd to 2nd = -0.51
- 2nd t0 1st = -0.6
- DART
- 5th to 4th = 0.11
- 4th to 3rd = -1.11
- 3rd to 2nd = -0.29
- 2nd t0 1st = -0.21
Additional analysis was performed to see if the fourth year phenomenon occurred regardless of size
of company and SIC code. Although the pattern was much more distinct among the small sites, the
trend of a fourth year drop in sites’ injury and illness rates was also clear in the medium and
large sites.

Text Version of Chart Data:
Chart Title: TCIR Rates for the Five Years Prior to Acceptance Into VPP by Employee Size of Site
Chart Type: Line Graph
Chart Elements: 3 - One line for each employee size of site showing the TCIR rate for each year prior to
acceptance into VPP
Values:
- TCIR Small, n=32
- Year 5 = 4.1
- Year 4 = 8.39
- Year 3 = 4.32
- Year 2 = 3.94
- Year 1 = 3.18
- TCIR Medium, n=56
- Year 5 = 7.5
- Year 4 = 7.15
- Year 3 = 4.1
- Year 2 = 3.38
- Year 1 = 3.02
- TCIR Large, n=28
- Year 5 = 3.68
- Year 4 = 4.22
- Year 3 = 3.49
- Year 2 = 3.72
- Year 1 = 2.56
*NOTE: Small is <99 employees, medium is 100-499 employees, large is 500+ employees per site
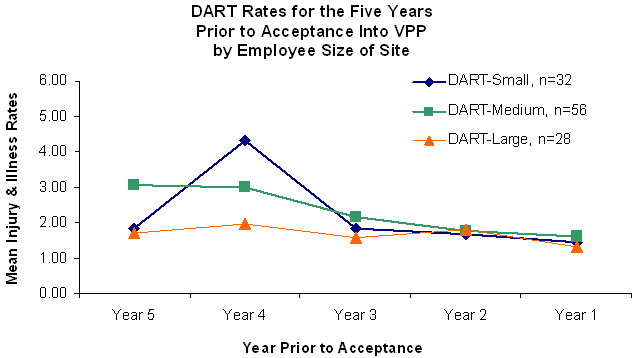
Text Version of Chart Data:
Chart Title: DART Rates for the Five Years Prior to Acceptance Into VPP by Employee Size of Site
Chart Type: Line Graph
Chart Elements: 3 - One line for each employee size of site showing the DART rate for each year prior to
acceptance into VPP
Values:
- DART Small, n=32
- Year 5 = 1.84
- Year 4 = 4.31
- Year 3 = 1.85
- Year 2 = 1.69
- Year 1 = 1.46
- DART Medium, n=56
- Year 5 = 3.07
- Year 4 = 2.99
- Year 3 = 2.17
- Year 2 = 1.78
- Year 1 = 1.6
- DART Large, n=28
- Year 5 = 1.7
- Year 4 = 1.96
- Year 3 = 1.59
- Year 2 = 1.81
- Year 1 = 1.31
*NOTE: Small is <99 employees, medium is 100-499 employees, large is 500+ employees per site
When examining sites by SIC codes, only three SIC divisions had sufficient sample for analysis —
manufacturing, transportation, and services — they were grouped as follows.
Division |
Major Groups Included |
Division D: Manufacturing |
Food and Kindred Products, Tobacco Products, Textile
Mill Products, Apparel, Lumber, Furniture, Paper, Printing, Chemicals, Petroleum, Rubber, Leather,
Stone, Primary Metals, Fabricated Metal Products, Industrial and Commercial Machinery,
Electronics, Transportation Equipment, Measuring, analyzing, and Controlling Instruments |
Division E: Transportation, Communication, Electric,
Gas, and Sanitary Services |
Railroad, Transit, Motor Freight, USPS, Water
Transportation, Air Transportation, Pipelines, Transportation Services, Communications, Electric,
Gas, and Sanitary Services |
Division I: Services |
Hotels, Personal Services, Business Services,
Automotive Repair, Miscellaneous Repair, Motion Pictures, Amusement, Health Services, Legal
Services, Educational Services, Social Services, Museums, Membership Organizations, Engineering,
Accounting, Research, Private Households, Miscellaneous Services |
The most dramatic difference was seen in the transportation industry where there was a large bump in
injury and illness rates. A similar bump in the manufacturing industry was shown, while the service
industry showed a gradual decline over time.
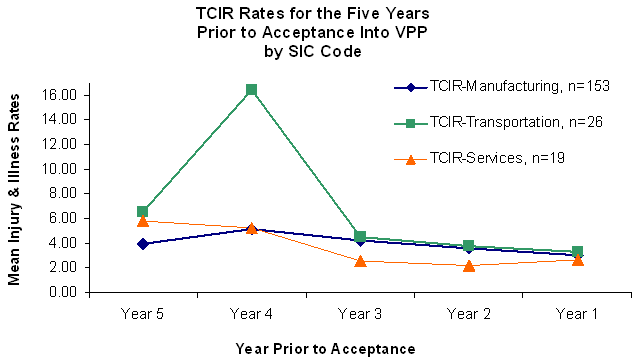
Text Version of Chart Data:
Chart Title: TCIR Rates for the Five Years Prior to Acceptance Into VPP by SIC Code
Chart Type: Line Graph
Chart Elements: 3 - One line for each SIC code showing the TCIR rate for each year prior to
acceptance into VPP
Values:
- TCIR Manufacturing, n=153
- Year 5 = 3.95
- Year 4 = 5.15
- Year 3 = 4.21
- Year 2 = 3.62
- Year 1 = 3.04
- TCIR Transportation, n=26
- Year 5 = 6.59
- Year 4 = 16.42
- Year 3 = 4.57
- Year 2 = 3.79
- Year 1 = 3.3
- TCIR Services, n=19
- Year 5 = 5.79
- Year 4 = 5.28
- Year 3 = 2.6
- Year 2 = 2.22
- Year 1 = 2.65
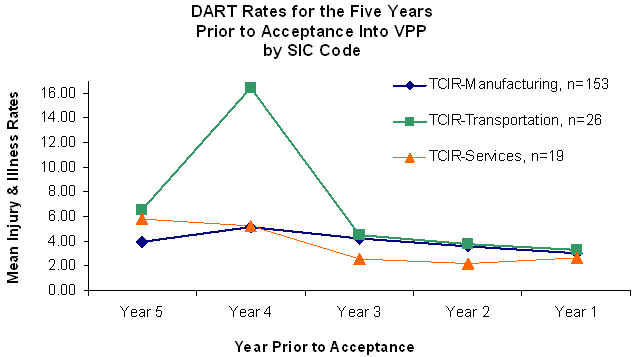
Text Version of Chart Data:
Chart Title: DART Rates for the Five Years Prior to Acceptance Into VPP by SIC Code
Chart Type: Line Graph
Chart Elements: 3 - One line for each SIC code showing the DART rate for each year prior to
acceptance into VPP
Values:
- TCIR Manufacturing, n=153
- Year 5 = 3.95
- Year 4 = 5.15
- Year 3 = 4.21
- Year 2 = 3.62
- Year 1 = 3.04
- TCIR Transportation, n=26
- Year 5 = 6.59
- Year 4 = 16.42
- Year 3 = 4.57
- Year 2 = 3.79
- Year 1 = 3.3
- TCIR Services, n=19
- Year 5 = 5.79
- Year 4 = 5.28
- Year 3 = 2.6
- Year 2 = 2.22
- Year 1 = 2.65
But were these jumps in rates significant if we compared them over time? The answer, as shown in the
following graph, is yes.
The following graph shows mean TCIR rates for each of the years 1 through 5 prior to VPP approval.
The line for each year indicates the spread of the means (a listing of all the means) for that year.
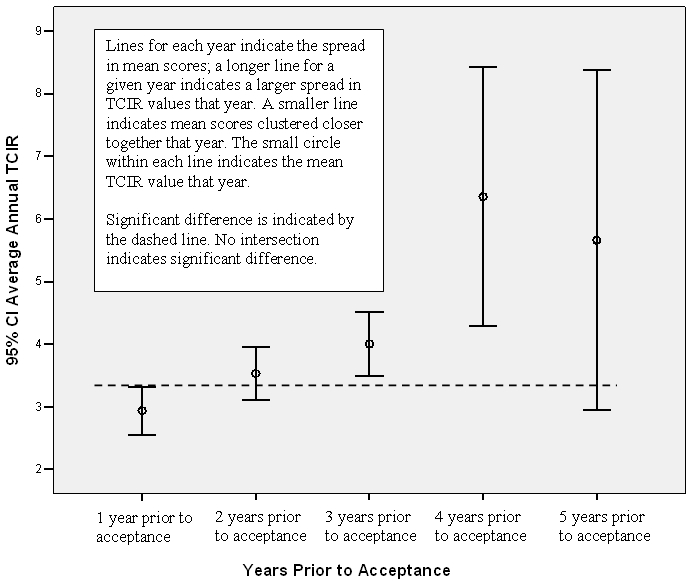
Text Version of Chart Data:
Chart Title: N/A
Chart Type: Vertical Line Graph
Chart Elements: 5 - Lines for each year indicate the spread in mean scores; a longer line for a
given year indicates a larger spread in TCIR values that year. A smaller line indicates mean scores
clustered closer together that year. The small circle within each line indicates the mean TCIR value
that year.
Significant difference is indicated by the dashed line. No intersection indicates significant
difference.
Values:
- Year 5 = 5.66
- Year 4 = 6.36
- Year 3 = 4.00
- Year 2 = 3.53
- Year 1 = 2.94
From this chart, we note several items of interest. First, the fourth year prior to acceptance has
significantly different TCIR rates than rates in either the first or second years prior to
acceptance (there is no intersection between these years). And the third year prior to acceptance is
significantly different from the first year prior to acceptance (again, no intersection). From this,
we deduce that the fourth year is indeed a significant "bump" from the first and second years and,
that by the third year prior to acceptance, there is still significant work to be done to achieve
those rates needed to be accepted into VPP (if we assume that rates seen in year one prior to
acceptance are nearly the same as rates needed for acceptance). The second point of interest is that
the spread of the means (the line) for the fifth year is the longest of any year with the fourth
year being the second longest. It is not until three years out from VPP acceptance that the mean TCIR rates for sites appear to converge. However, recall that a significant difference occurs
between the third and first year such that although TCIR rates are converging, they are only
converging together, not necessarily declining significantly.
These same charts were computed by SIC and by size of company. No other significant differences were
noted.
So, what is happening in year 4 that is causing such dramatic behavior? Although dates of events are
unknown, respondents were asked if any of the following lists of events or activities had occurred.
Event or Activity |
# of Respondents Indicating Event
Occurred |
Increase in workers' comp |
48 |
Changes in management/ownership |
45 |
Special emphasis program in industry |
26 |
OSHA inspection, other |
21 |
OSHA consultation |
14 |
Increase in casualty rates |
12 |
OSHA inspection for fatality |
8 |
OSHA cooperative program |
8 |
OSHA inspection for catastrophe |
1 |
TOTAL |
183 |
An increase in workers’ compensation and changes in management/ownership were the two events that
occurred most often among those sites that applied for VPP acceptance. Since the dates when these
activities occurred are unknown, this information is provided merely for the reader’s interest.
The information available for each of the years presents a subset of what comprised the TCIR and
DART rates. Less than one-half of respondents who gave TCIR and DART rate information also gave
specifics on the log data they submitted, and it is through this information that further analysis
can be performed by year. Reviewing the specifics within the OSHA 200 logs, the identical pattern to
the TCIR and DART data emerges among one variable, Question 7f, Total Number of Disorders Associated
With Repeated Trauma.
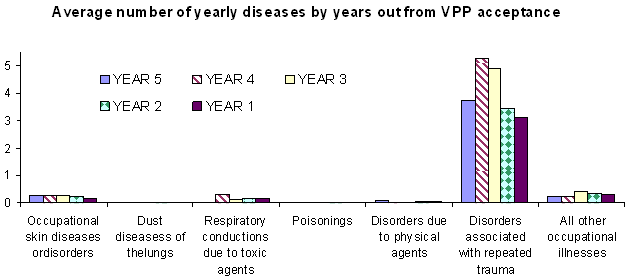
Data shown is from the 200 Log Data |
Text Version of Chart Data:
Chart Title: Average number of yearly diseases by years out from VPP acceptance
Chart Type: Vertical Bar
Chart Elements: 20 - One line for each year showing the number of diseases by type
Values:
- Occupational skin diseases or disorders
- Year 5 = 0.27
- Year 4 = 0.29
- Year 3 = 0.28
- Year 2 = 0.26
- Year 1 = 0.16
- Dust diseases of the lungs
- Year 5 = 0
- Year 4 = 0.01
- Year 3 = 0.03
- Year 2 = 0.02
- Year 1 = 0.01
- Dust diseases of the lungs
- Year 5 = 0.03
- Year 4 = 0.33
- Year 3 = 0.13
- Year 2 = 0.18
- Year 1 = 0.17
- Poisonings
- Year 5 = 0.02
- Year 4 = 0.01
- Year 3 = 0.03
- Year 2 = 0.03
- Year 1 = 0
- Disorders due to physical agents
- Year 5 = 0.09
- Year 4 = 0.05
- Year 3 = 0.03
- Year 2 = 0.07
- Year 1 = 0.06
- Disorders associated with repeated trauma
- Year 5 = 3.75
- Year 4 = 5.29
- Year 3 = 4.91
- Year 2 = 3.43
- Year 1 = 3.13
- All other occupational illnesses
- Year 5 = 0.24
- Year 4 = 0.23
- Year 3 = 0.41
- Year 2 = 0.36
- Year 1 = 0.3
With 7f, the pattern is similar to the TCIR and DART rates that showed a bump in the fourth year
prior to VPP acceptance, and then tapered off to the first year prior to VPP acceptance. In none of
the other disease categories did this same pattern occur. Due to low response rates among these
specific injury categories, these data cannot be further broken down by either SIC or by number of
employees.
FINDING: It is with the disorders associated with
repeated trauma injury that an analogous pattern of an increase in TCIR and DART rates emerges in
the fourth year prior to VPP approval. This finding is possibly associated with sites’ increased
injury and illness record-keeping and reporting that tends to occur four years prior to VPP
approval as sites prepare for VPP. |
5.1 "Future" TCIR and DART Rates
The final step in this section is to look at these same sites and their progression once they
obtained VPP status. The OSHA team provided data from 1995 approval dates and later. The following
chart shows TCIR and DART rates overall for the five years following a given site’s acceptance into
VPP.
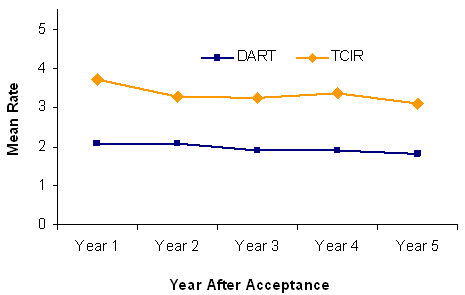
Text Version of Chart Data:
Chart Title: N/A
Chart Type: Line Graph
Chart Elements: 2 - One line for TCIR and one for DART showing rates overall for the five years
following a given site’s acceptance into VPP
Values:
- DART
- Year 1 = 2.07
- Year 2 = 2.08
- Year 3 = 1.89
- Year 4 = 1.90
- Year 5 = 1.82
- TCIR
- Year 1 = 3.73
- Year 2 = 3.28
- Year 3 = 3.26
- Year 4 = 3.37
- Year 5 = 3.10
As the chart shows, once the site is admitted into VPP, its rates remained fairly flat with a slight
decrease over time. This small decrease is seen more clearly when broken down by employee size of
site.

Text Version of Chart Data:
Chart Title: DART Rates After Acceptance
Chart Type: Line Graph
Chart Elements: 3 - One line for each employee size of site showing the DART rate for each year
after acceptance
Values:
- DART Small, n=20
- Year 1 = 2.84
- Year 2 = 3.39
- Year 3 = 2.63
- Year 4 = 3.03
- Year 5 = 1.78
- DART Medium, n=35
- Year 1 = 2.41
- Year 2 = 2.21
- Year 3 = 1.83
- Year 4 = 1.92
- Year 5 = 1.76
- DART Large, n=25
- Year 1 = 1.54
- Year 2 = 1.35
- Year 3 = 1.35
- Year 4 = 0.87
- Year 5 = 0.92
As the DART and TCIR rates show, over time, there was a decrease shown by five years out from VPP
acceptance in all categories, most notable in the small- and medium-sized firms.
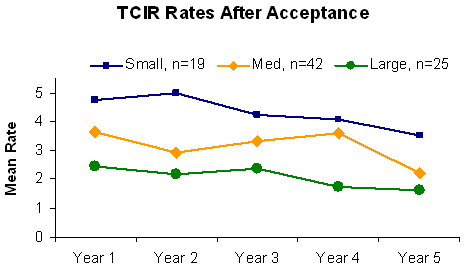
Text Version of Chart Data:
Chart Title: TCIR Rates After Acceptance
Chart Type: Line Graph
Chart Elements: 3 - One line for each employee size of site showing the TCIR rate for each year
after acceptance
Values:
- TCIR Small, n=19
- Year 1 = 4.73
- Year 2 = 4.99
- Year 3 = 4.23
- Year 4 = 4.06
- Year 5 = 3.52
- TCIR Medium, n=42
- Year 1 = 3.63
- Year 2 = 2.91
- Year 3 = 3.34
- Year 4 = 3.59
- Year 5 = 2.21
- TCIR Large, n=25
- Year 1 = 2.45
- Year 2 = 2.17
- Year 3 = 2.39
- Year 4 = 1.76
- Year 5 = 1.61
Sample sizes were not sufficient to perform this analysis by SIC code.
6.0 CONCLUSIONS AND RECOMMENDATIONS
6.1 Mentoring Program — Conclusions
- The mentoring program, although not recent, has shown a renewed interest among new participants in
the VPP. Because of that, there is an opportunity to use these "new" mentors to recruit new
participants into the VPP.
- There is an attrition rate among mentors. After approximately five years in VPP, the amount of
mentoring conducted by a site falls off. OSHA needs to be aware of this timeframe and consider
interventions that can be used to reinvigorate interest and commitment among this group.
- There is also a burden issue to be aware of. Respondents were willing to mentor about one site
each. Therefore, knowing who is currently mentoring a site and who is not can help predict the
availability of potential mentors.
- The acceptance rate into VPP by those who have been mentored is at 46% acceptance, and there is a
potential to convert more mentees to VPP status, especially since 75% of respondents said they
conducted mentoring with non-VPP bound sites.
- It is interesting to note that overall, manufacturing sites mentor less than do other SIC codes.
There is a potential to increase the amount of mentoring occurring among manufacturing sites,
particularly because that is the majority of the sites who are in VPP.
- Not surprisingly, the larger a site is, the more mentoring it does.
- Mentors appear to be dividing their time equally between mentoring inside and outside their
companies, although most spend more time mentoring inside their companies. One-third said they were
required to mentor within their own company.
6.2 Outreach Program — Conclusions
- As with mentoring, there is a renewed interest in outreach activities (although to somewhat of a
lesser extent than with mentoring). Since many respondents are fairly new to VPP, the number of
years they have conducted outreach activities is approximately four years.
- While 69% of respondents said that there was someone at their sites that had done mentoring in the
past year, less than one-half said they had done outreach.
- In general, medium-sized sites (those between 100 and 499 employees) tended to do more outreach
activities than sites of other sizes.
- There are some distinct preferences that exist between the size of the sites and what type of
outreach activity they prefer to perform (see charts and graphs inside this report for a full list
of preferences by size of company).
- The activity most participated in, regardless of whom it was for, was providing training in
support of VPP.
- Most of the outreach activities are conducted outside of the respondent’s own company. The only
exception was with conducting safety and health workshops and
providing training in support of VPP where just under one-half are
conducting these workshops within their own companies.
- There is also room for growth in outreach. Respondents, in general, said they would be willing to
do an additional 11 hours of outreach activities per site on behalf of OSHA and an additional 11
hours per site on the behalf of non-OSHA organizations.
6.3 Past Data Collection — Conclusions
- There is a significant increase in TCIR rates that occurs four years out from a site’s acceptance
into the VPP. The rates increase from the fifth to the fourth year and then drop from there until
the site reaches its acceptance date.
- This pattern is most prevalent among the transportation industry respondents, although it also
exists in the manufacturing industry as well.
- It is only within the service sector where a steady decline occurs, starting from five years out
and no bump is apparent.
- The bump pattern occurs most dramatically with smaller sites, although it is present among medium
and large sites as well.
- When examining the log data further, a fourth-year bump pattern also occurs with the injury of
disorders associated with repeated trauma.
6.4 Recommendations for Future Data Collection Efforts
This cross-sectional study was designed to collect data at one point in time only. Collecting data
in a one-time effort produced instructive information, albeit information that required extensive
effort from respondents. The following list includes recommendations that Gallup has for OSHA to
continue collecting these data over time so that future efforts will be focused solely on analysis
and not on data collection.
- Mentoring and outreach activities can be incorporated into the yearly log data that VPP
participants submit to OSHA and collects on a yearly basis. The questions asked will depend on what
type of data OSHA is interested in collecting.
- Information on secondary participation at mentoring and outreach activities could also be
captured on an annual basis by VPP participants submitting yearly logs to OSHA.
- Sufficient data are currently being captured by OSHA to assess change over time. However, these
data need to be kept in a database that ensures the goodness of the data, which allows the sites to
change names, etc. over time, and to keep an accurate record of the data. The existing database,
which OSHA maintains, is what should be focused on to ensure quality data.
- Currently, all VPP acceptances need to provide the logs for three years prior to acceptance into
VPP. Given the bump that appears in the fourth year prior to acceptance, OSHA may seek to expand
that data collection to the four or five years prior to acceptance into VPP.
- In terms of providing guidance for other OSHA programs, there are some developments to share. But
nearly all of the data elements gathered in the third section of this study could have been gathered
by OSHA by expanding the information that VPP sites submit before they are accepted into the
program. Other information gathered in this effort, i.e. mentoring and outreach, are both specific
to the VPP. Programs such as the Strategic Partnership Program, should gather data specific to their
programs before they begin and comparatively assess if there is a change once the programs finish
(because there is a start and stop date). TCIR and/or DART rates can work as can the other log data
collected. We recommend that OSHA collect as much log data as possible for analysis.
- It is also important to note that collecting data retrospectively is a difficult, inexact and
burdensome process. To the extent that data can be collected throughout the life of a program, the
data will be that much more reliable and accurate.
7.0 VERBATIMS
The final question in the OSHA questionnaire asked respondents to give any information on successes
they had achieved in the past year. The following is a list of responses received by the
participants.
- VPP has given our safety program a benchmark to work with. It also has given us a chance to see
other excellent safety programs to help us improve our program.
- Through the VPP program there is a greater participation in plant and company safety programs.
- Drilling Specialties Company Alamo Plant continued its outstanding safety performance in 2004 by
completing the year without an OSHA recordable injury. This makes the fifth consecutive year without
a recordable injury, a significant accomplishment. As of December 31, 2004, the plant's employees
had worked 2,120 days without a recordable injury. OSHA recognized Drilling Specialties Company
Alamo Plant A Division of Chevron Phillips Chemical Company LP, outstanding safety record by
awarding its Star of Excellence to the facility in 2004. Drilling Specialties Company Alamo Plant A
Division of Chevron Phillips Chemical Company LP, earned the CPChem Safety Excellence Award for the
fourth consecutive year.
- VPP is a wonderful program. We are totally committed to what VPP stands for. It has helped us
achieve a tremendous improvement in safety and health at our facility. Our current statistics are:
Recordable rate 0.63, DAWC rate 0.21 and our DART rate is 0.21.
- VPP has raised the facilities safety awareness and increased employee participation greatly.
- Incident rates 80% below national average for similar facilities. Completed 22nd consecutive year
as a STAR site, longest in the VPP.
- VPP has allowed continued involvement with union employees and management. Recently, our VPP
Coordinator, Richard Marion, has joined the Board of Directors for the City of Fond du Lac's Safety
Council.
- Led to us getting the National Safety Council 2004 Industry Leader Award.
- We have seen our colleagues more involved in safety and health issues. Our colleagues own the
program now. We are pleased to be able to mentor another site this year. I am also an SGE, and I
participate on two assessments of other sites as a SGE twice per year.
- Though not directly related to our participation in the VPP, Pfizer would like to share the news
that the White Hall site has been accepted into EPA's National Environmental Performance Track. We
feel that by developing the health and safety management systems that we needed for the VPP, we also
advanced the caliber of our environmental management systems.
- Two LP sites mentored by LP Houlton have pending applications and two more sites will apply in
2005. All LP OSB sites will apply for VPP status by 2007.
- The VPP is an excellent program. Participation in the program has made us a safer and stronger
organization. It has also promoted teamwork.
- Attaining VPP Star status has set the bar high at the Illinois Refining Division. In 2004, we had
our safest year on record! Also, we developed an internal VPP STAR Team after achieving VPP Star
status in 1999. This team has been extremely effective in promoting VPP throughout the year.
- Because of the emphasis that VPP places on management commitment and employee participation, we
are now seeing an environment where employees take responsibility and have authority for reporting
hazards and unsafe conditions. Employee participation increases every year. We have not seen a lost
time injury for 2 years now.
- The VPP process is an excellent program that has helped to take our safety and health program from
the written form to a living form on the work floor of our facility. It has helped make the program
more about the people it was meant to help than that of just being told this is how you will do it.
It has empowered the employees of our facility to take ownership of and responsibility for our
safety and health program and has helped to take the us and them (labor and management) idea out and
replace it with us.
- AMAT-Austin is well on the path toward developing a total environmental, health and safety (EHS)
culture. Heightened employee awareness, involvement, and ownership continue to drive success. During
2004, the Volume Manufacturing Organization (VMO) became ISO 14001 certified and was recommended for
the Texas Commission on Environmental Quality (TCEQ) National Leader program as well as the United
States Environmental Protection Agency (USEPA) Performance Track Leadership program. Applied
Materials, Inc. is the first semiconductor equipment company to achieve all three designations. In
addition to becoming ISO 14001 certified, the Harris Branch and Spectrum Drive facilities were
awarded the Occupational Safety & Health Administration (OSHA) Voluntary Protection Program (VPP)
'Superstar Among Stars' award for achieving a lost-time injury incidence rates 75% lower than the
North American semiconductor industry average. At least 10 Austin manufacturing departments have
reached the impressive milestone of 1000 days without lost-time injury and the savings from improved
safety performance continue to add to the Company's bottom line. During 2004, AMAT-Austin received
an Award of Honor from the Texas Safety Association for "outstanding service and worthy
accomplishments in accident prevention contributing to a safer Texas in 2003." In addition, ITT
Hartford, (AMAT-Austin's Workers' Compensation insurance carrier) recognized AMAT-Austin for
achieving 3.5 million hours worked without a lost-time accident. Finally, AMAT-Austin reduced its
OSHA Lost-Time Severity Rate (SR) by 25% resulting in over $420k savings in direct and indirect
accident cost. The current business environment will continue to challenge the organization.
Maintaining ISO 14001 certification will require continual process improvement. There is still more
to do to achieve our vision of world-class EHS performance. We must integrate environmental
management into the mainstream of our company through increased awareness, involvement and ownership
of environmental issues and opportunities. During 2005, AMAT-Austin will expand its environmental
focus while maximizing stakeholder awareness, involvement and ownership. The benefits to the company
will be lower cost, increased efficiency, and higher morale."
- We achieved 83% total employee participation in the safety program, the highest ever.
- VPP has impacted our facility in very positive way. Employees were energized through the process
and it served as a catalyst to bring our facility together to achieve a common goal. Its benefits
outweigh the negatives. I highly recommend the process to all who are interested.
- We started a committee to help other sites within our company apply and obtain VPP status.
- One of our resident contractors was approved for STAR status.
- The VPP Site at PPL Holtwood, LLC has not had an OSHA recordable event since 2001. We received our
approval into VPP in November 2002. Other PPL work sites with small numbers of employees in
Pennsylvania, New York, Connecticut, New York, and Maine have reduced their number of OSHA
recordable events since being introduced to the VPP program.
- Perhaps, one of the most outstanding successes we have achieved in the last year has been the the
Recognition of our Second Consecutive National VPPPA Achievement Award Winner. Not only does this
award speak well of the employee but it also speaks well of all the employees which support this
individual. In addition, last year we experienced a significant increase in our management
leadership and employee involvement. Lastly, I would like to point out the cooperative relationship
we have driven with OSHA, other companies and the VPPPA.
- The site has seen a reduction in their business risk insurance premium of 1 million dollars a year
as the result of changes made to site programs and procedures that were implemented as part of the
VPP initiative. In addition, the site has realized a reduction of $250,000 dollars a year in workers
compensation premiums. The site safety culture has been improved and employees are excited to work
at a VPP facility.
- I feel the VPP program has added to the component of Safety at this workplace. Value is always
needed to reinforce the core of Safety. It is my hope that OSHA continues to hold these companies to
a higher level and not try to expand the VPP numbers just for the sake of numbers. VPP should be a
level that is hard to attain. We at Monsanto mentor each site through the process of VPP. We discuss
this topic at different intervals throughout the year. Non-VPP sights gain insight to the process
through the help of locations currently holding the VPP status. Mason City Monsanto helps to relay
Safety through Community projects and by inviting a regional seed company to our Safety meetings.
The hope here is to spread the awareness of our program to these areas.
- In the short time since we have become a Star VPP site there has been a noticeable increase in
employee awareness and participation in all safety activities. This has shown up as well in their
private lives as well as their professional ones. As the first Star site in the National Park
Service the staff at the monument feel that this program is well worth the effort involved.
- In December of 2004 we went from Merit to Star in less than 2 years.
- As mentor in Region VI Outreach organization, both organizations, being mentored, were recommended
for STAR status. This site has two participating SGE (Special Government Employee). Three new SGEs
were trained are available for VPP audits. Used networking with other VPP sites to increase our
safety and health programs (sharing experience). We, as well, were able to provide our experience to
other sites.
- During 2004, we had only one recordable injury. We won first place for our sic code in Manufacture
Alabama Safety Achievement Program. We received a rating of OUTSTANDING based on Corporate Safety
Audit and scored the highest score in our company.
- After entering The VPP program we have experienced one recordable-lost time injury, Dec. 2004,
resulting from a slip on ice. Employee cut his ear which required stitches and days away from work.
- Expanded activities in Interdependent Stage of Safety Journey: 2004 Implemented 'Off The Job Home
& Safety' employee awareness program, Virtual Incident Investigation event, and monthly Behavioral
Safety Samplings. 2005 Goals Receive Responsible Care certification. Achieve 100% employee
participation in one or more safety team responsibilities. Received the 2004 Governor's Award for
Safety Excellence from the Department of Labor & Industry for demonstrated commitment to providing a
safe working environment for Pennsylvania workers through the successful implementation of
comprehensive accident and illness prevention programs and practices. Governor Rendell's safety
initiative provides Pennsylvania employers and employees with the information and technical
assistance needed to develop comprehensive safety practices in the workplace. It also recognizes the
successful employer-employee joint safety programs, which result in the achievement of safety
excellence. Received Rohm and Haas Corporate Safety Achievement Award for zero injuries from
September 2002 - August 2004. Received the American Chemistry Council award for outstanding safety
performance during calendar year 2003. Received Certificate of Recognition from the Berks County
Board of Commissioners for being the recipient of the 2004 Governor's Award for Safety Excellence.
The event aired live on Berks Community Television (BCTV). Received Certificate of Radiological
Safety from Applied Health Physics, Inc. regarding the use of the SEM Philips XL30 for imaging and
elemental analysis of powder coatings. The inspection results comply with accepted radiological
safety standards as specified by the appropriate state and federal regulations. The R&D Center
received the Perfect Record Award from the National Safety Council (Alan C. McMillan - President)
for operating 75,141 employee hours without occupational injury or illness involving days away from
work January 1 through December 2003. The R&D Center received the Excellence Achievement Award from
the National Safety Council (Alan C. McMillan - President) for recognition of outstanding efforts in
occupational safety performance 2004. The R&D Center LAMINEER program was nominated for and received
the American Chemical Society's 2004 Regional Industrial Innovation Award. This award distinguishes
the successful innovations of industrial chemists and chemical engineers that contribute to the
health of their local and regional economy. Awards are given to individuals and teams whose creative
innovations have contributed to the commercial success of their company and, consequently, to the
good of the community and society. The VPP experience has been a rewarding and worthwhile process.
It has helped us focus and take a good program to an even better one. Employee involvement with
management commitment is the key to success.
- We were recommended to continue as a VPP Star site in October 2004 by our VPP Review Team and
received approval from OSHA in February 2005. Our employees reached a milestone of working 1,000,000
consecutive hours without an employee missing a day of work due to a work related injury or illness
on September 24, 2004 dating back to October 17, 2000. This is the 2nd highest work hour record in
our history with our all time record being 1,535,000 hours set in February 1998.
- Our VPP program has proved very successful. It challenges us to raise the bar each year, and has
helped drive new programs to enhance our division's safety. We saw the successful implementation of
several programs, including a pre-task safety checklist and a hazard recognition program.
- At our site we have gone two years without a recordable and are closing in on 2000 days without
any lost time. Since becoming A VPP Star site safety awareness has increased greatly on the job and
at home as well. Employees are more involved with all safety aspects at the site. Becoming a VPP
Star site was one of the best changes that has happened to us.
- We have had 2 years with no LTA's as of February 27, 2005. Employees are aware of the importance
of safety and health in the workplace and are doing things the right way - not rushing to get a job
done, rather focusing on the safe and sure way to complete a task. Our facility has been recognized
for 2 Best Practices by OSHA in 2004, at the time of our sites re-certification of STAR status.
Employee safety is a top priority of our facility. A group effort to work as a team and open
communications between management and employees benefits us greatly.
- Have been a VPP site since 1993. Started manufacturing in 1992. In the last 10 years TCIR is 1.2
(~ 1/3 BLS for SIC). TCIR = Zero last two years. All Site resident contractors are VPP (or waiting
approval); 1) maintenance contractor, J.E.Merit, is VPP for many years, and 2) warehouse group, WSI
was recommended for approval in Jan. 2005. We have never had a lost days away from work case ever!!
VPP is working well for us!!
- Successful star re-certification. We have been a Star site for over 20 years making it difficult
to provide information on rates prior to becoming a Star site.
- In our January 2003 VPP Re-Approval On-Site, a Compliance Officer team member speculated that we
might be challenged when integrating new-hires into our workforce, since it was mature and made up
of experienced dedicated employees transferred to the facility under the terms of existing Labor and
Wage Agreements as a result of manufacturing mill closures and the resultant restructuring of our
business. We are pleased to report that, thanks to a very comprehensive candidate selection process
and the efforts of our policy/program Champions from the Bargaining Unit, we have successfully
managed to bring several new employees through the orientation and integration process and have them
on board as safe, efficient, productive additions to our workforce.
- Have worked with two companies started in VPP. Participated as an SGE on an audit during March
2005.
- Our CEO Chuck McElrea, has committed our entire organization to becoming VPP Certified (including
our two sales centers). As an organization, we offer workplace safety and health coaching to our
customers.
- Our site finished 2004 with its lowest injury frequency in history (2.4). It also had an
injury-free streak between 2003 and 2004 of 228 days! The site behavioral based safety program,
involving peer-to-peer feedback, has increased significantly. The site has better than 75%
participation by employees.
- SUCCESS STORIES: OP2 Completed 636 days without a recordable as of 1/13/05. Plant Maintenance
Services: Completed over 46 months with a recordable injury to company personnel. Completed 22
months of 100% participation in the EAGLES process. Lab: Significant reduction in number of
evacuations: Air in-take improvement. Replaced lab hoods. Completed pre-job checklists, identified
deficiencies in both procedures and equipment. Installed an enclosed funnel system for PFO sample
dumping. Labeled gas cylinders at manifold for better identification. Implemented Level 1 permit for
gas delivery. Mid Plant: Mid Plant concentrated a large portion of its resources in 2004 on Safety
and environmental priorities. One new program that was added during the year was the pre-job
planning audits. Specific industry high risk areas related to safety were focused upon during the
year. Slips, Trips, and Falls: A list was generated on structural at risks associated with
platforms, handrails, ladders, and grating. Modifications to date include platform revisions or
additions, ladders modified, landings added, straps added to ladder cages, and grating replacement.
Resolution of list continues into 2005, currently revising ladders in IPOH. Waste Water project
engineered solutions to mitigate flooding and trapped water. These will be implemented in 2005-06.
SMA alley way was resurfaced to allow for run off and avoid algae accumulation. Chain operators,
pipe revisions, and temporary scaffolding platforms were installed to make equipment more
accessible. Thermal Exposures: Area inspection conducted to identify and mitigate thermal exposures.
In 2004 10 items were closed. Steam trap drains were revised as well as wire cages installed to
prevent contact. Added insulation to newly identified burn hazards. Rerouted some PSV discharge
piping. PPE: Designated goggle areas were re-assessed in 2004. Re-defined areas were painted and
required signs installed. Specific job tasks were reviewed. PPE requirements were adjusted as
necessary. Procedure revisions were made to capture any PPE requirement changes. Fire Suppression
Systems: Replaced MP firewater tank and upgraded pumps. Replaced several underground header main
valves with new easy open style. Upgraded several fire monitors. Electrical: Identified equipment
where old grounding grid design was inadequate. Implemented project to upgrade grounding in all
areas that are deficient by today's standards. Installed continuity indicators on all truck
loading/unloading stations in MP. Completed all identified conduit and junction boxes in need of
repair. Process: Implemented controls to prevent high O2 in PolyBd refining section. Reliability:
Increased PolyBd and SMA to record reliability eliminating at risk tasks. Replaced/upgraded several
tank floating roof seals.
- Facility surpassed 4 years w/o lost time incident. Facility has currently worked over 1500 days
w/o lost time incident. There has been an increase in hourly employee safety activities and
attendance to the SC meetings. More hourly employees involved with inspections. The VPP has improved
involvement and changed the way the facility employees look at safety and safety participation.
- Re-enactment Accident Video, VPP Mentoring, Annual Health Fair, Safety Behavioral Audits are some
of our success stories from last year.
- Re-certification of VPP Star status.
- Excellent program, keeps getting better.
- VPP has initiated a safety culture in our workplace that wasn't there prior to VPP.
- The site VPP lead has become a BOD for Region II, the site has also been recognized by OSHA and
the DOH as having an outstanding self-evaluation program."
- I feel that VPP is a great program and it promotes a strong safety presence in our facility.
- We have been re-certified last Sept. 2004. Participating in VPP is beneficial in that it holds
managements feet to the fire to walk the talk. It has also increased employee awareness and
participation in their own safety through employee created procedures and continuous improvement
projects through hazard ID.
- VPP has been a focus point for our safety program. It is a well deserved tribute to a group of
employees working together to make their workplace as safe as it could be. This is an excellent
program.
- The VPP program has been a great tool to get the employees involved in our safety program. It has
also been a good outreach tool for other plants in our area. It's a great program.
- Great program. We actually did more outreach but didn't want to double dip with our sister site
for this survey.
- Great program. Really got our employees involved in safety. Good outreach program to other sites.
- Continuous Star among Superstar status with 85.6% below BLS average for 2004.
- Our site is a medium size chemical plant with about 450 employees and have been a VPP STAR site
since 1995. Every year we assemble a cross functional team of about 12 employees to conduct our Self
Evaluation. We typically conduct surveys/interviews and collect data to assess all of our safety
processes/programs and we average 25 recommendations per year to help us improve. Our
recommendations are reviewed and approved by our Plant Safety Counsel and are critical for setting
the safety direction of our plant. The VPP requirement to conduct this Self Evaluation every year
ensures its priority and management commitment to excellence and continuous improvement ensures a
thorough job is done each year. Were it not for VPP, we would not voluntarily commit the resources
needed to conduct this value added Self Evaluation every year.
• During the onsite pre-approval evaluation held from August 18-21, 2003, the facility was commended
for 3 Best Practices. They included: Machine Guarding, Housekeeping and Ergonomics.
• Installed fall protection system that now incorporates all work areas where fall protection is
required.
• Since attaining VPP Star our annual TIR has steadily declined to a record of 0 for 2004.
• Our facility recently celebrated three million man hours without a lost time accident. Since we
are a small facility (currently 170 employees), this represents almost ten years. We feel that
becoming a part of the VPP has played an important part in helping us to be injury free. We place
special emphasis on working safely every day.
- Was re-certified as a Star site in April 2004.
- Although VPP is a good tool, we implemented VPP at the same time we were implementing a management
system so not all credit can be given to VPP causing the turnaround of our site. It was a part of
the whole. I agree with the principles of VPP but feel I have to do more now than I had to do prior
to VPP to continue to be in VPP. It is almost a disincentive to join as we can implement the
concepts and have a safe site but without the hassle. OSHA should consider lessening the burden for
those sites that prove they have an acceptable program and focus on the industries that continue to
have injuries above the industry rate. The whole purpose of VPP should be to prove to OSHA that we
are managing our site and they do not have to worry about us and then they can focus on the people
that are not interested in safety and health.
- VPP is employee driven and provide a point of pride for the organization for their effort.
- Success is in participation. All levels are engaged in Safety & Health, both at work and at home.
Continuous improvement in many aspects, other than recordables.
- In the course of constantly trying to improve our process, we have implemented a Residual Risk
Reduction process in which we take tasks in the plant, analyze them and quantify the risk level,
find countermeasures for the highest risk parts of the job, and then measure the % improvement. This
gives us a great process for quantifying the risk levels of tasks, and measuring improvements. We
fully implemented this process the end of 2003 and are now reaching 2 full years without a recordable injury.
- We are proud to be a VPP Star site and continue to strive to provide a safe work environment for
our employees. Our facility converted the emergency codes to the universal codes recommended by the
Florida Hospital Assn. The code system was very useful and came in handy when the hurricanes hit the
state and other facilities had to evacuate patients. The coding system facilitated the influx to our
hospital. We also received grant money for Emergency Preparedness for decontamination in the event
of bio-terrorism.
- The main achievement in the past year is the vast improvement we have in employee participation in
the safety process.
- We received recognition as a VPP Star Site in 2004. We are proud of this accomplishment. We work
closely with industry in the area and the contractors on-site to ensure that we are promoting
continuous improvement in safety. Although we do not spend many hours specifically mentoring on VPP,
we spend at least 15 hours a month promoting safety improvements with visitors, contractors or other
sites within our organization.
- The VPP is a great process because it forces you to track safety data and follow up on your safety
program. It causes you to take a good look at continuous improvement knowing that you will be
measured on the outcomes.
- Our facility is going through a lot of changes during 2004 and 2005. We are going from a Manual
Operation to Automation. One of the biggest successes we have seen in our facility is employee
involvement. The Management together with the Unions and VPP Coordinators has shown to the employees
that their voice counts. Management has involved the employees on making decisions for the best of
the Operation and the Safety of our employee. Employees at this facility no longer think Management
does not care when it comes to safety.
- VPP as a whole has been instrumental in decreasing our plants illness and injury rate by
instituting a formula and cooperation among management and employees. Basic safety thought processes
are deeply instilled in our employees and through continuous efforts by both employees and
management have made working in the plant a safer environment.
- The disciplined approach VPP instills in a company H&S management system allows for continuous
improvement from year to year.
- GE Rail Sayre was recognized by OSHA during the 2004 VPP Star recertification as having 3 'Best
Practices.' They are published in the 2005 VPPPA Best Practice Directory. Programs recognized are:
Employee Involvement, Tracking of H&S Systems, Ergonomics
- This is an organized union work site. Employees view the VPP Program as a mechanism to formally
involve them in the workplace safety and health process.
- VPP has improved labor/management relations. In addition to providing a safer work environment, we
have had improvements made in other areas as well, such as production and employee morale.
- Our VPP Team meets semi-annually to review how we are doing. They are active in trying to keep VPP
alive. Our 'Safety Pays' questions seem to help keep people interested in VPP. We ask 3 VPP
questions each week and the person who is asked that question, gets a small prize if they answer it
correctly
- Our VPP Team meets semi-annual to review how we are doing. They are active in trying to keep VPP
alive. Our 'Safety Pays' questions seem to keep people interested in VPP. We ask 3 VPP Questions
each week and the person who is asked the question, gets a small prize if they answer it correctly.
- JRC was re-certified in 2004 with only minor findings.
- The VPP has been a huge part of the overall success of the Occidental Taft Plant. In the past year
the facility has completed 4 years without a recordable incident. The VPP program as well as other
plant programs have played a huge part in this success.
- Recertification recommendation given in January 2005.
- VPP is a great thing for all it has helped change the thinking of management in the postal service
which in turn has helped to prevent some injuries.
- Success stories for our site - 10 months without OSHA recordable - Safe maintenance TA and
Hurricane Ivan - No reportable spills or releases - October fire drills - VPP has been very positive
for our site as to employee safety.
- Very worthwhile program that has seen many successes at our site. Employee involvement in the
safety program has dramatically increased while injuries and illnesses have decreased.
- TCIR 2004 7.18, DART 2004 4.19, LTI 2004 .79; Received the OSHA-STAR Designation.
- In 2004 we reached a milestone of 500,000 man hours without a lost time accident. Because of the
low number of employees it took us 10 years to reach this milestone.
- Number of employees in 1995 & 1996 are estimates.
- We continue to maintain our Level of Zero OSHA Recordables and Zero Lost-Time Incidents, having
past 2,100 consecutive days without an OSHA Recordable or Lost-Time Incident. Working with sister
Sites in Shady Hills, Florida and Franklin, Georgia with their VPP Application.
- Because of efforts to improve over 2003 we instrumented a rate reduction plan and monitored all
activities very closely. The rate was reduced and the efforts are continuing.
- VPP has challenged our entire project to enhance our safety observation process, and a transition
into more behavior based observations is in process now, and additional quality on supervisory and
management observation processes is also in place.
- As a corporate contact for VPP, I have seen our sites continue to improve their injury/illness
rates, get more employees involved in the ownership of the safety processes, and the severity and
costs associated with these events decline.
- Valero Management continues to demonstrates its commitment in safety & health by
sponsoring/supporting: Monthly safety meetings, Job Safety Analysis, Safety and Health Committees
(Valero & Contractor), Safety Network Team, Valero Volunteer Committee, VPP Promotions Committee,
Health Wellness Assessments Program, Voluntary Asbestos Medical Monitoring Program, beginning all
meetings with a safety topic, Weekly toolbox meetings, Environmental Health and Safety
Walk-A-Round's, Monthly Clean Sweep Housekeeping Program. In addition the Refinery Vice
President/General Manager and Union President jointly signed a Letter of commitment to VPP. Also,
Corporate Management has hired a Director of VPP to guide each Valero refinery in their pursuit of
VPP.
- Being a part of the VPP program has helped our plant and company tremendously. We have achieved
safety numbers in our company that we did not think were possible but through the help of our VPP
and OSHA teams we have made great strides in injury reduction.
- We have only been a VPP site for less than 1 year. We have made presentations to our corporate
EH&S group in an attempt to increase VPP interest at the corporate level. We have also made a
presentation to Arkansas VPPPA members on employee involvement.
- As we just became a VPP facility a few months ago, we have not had much chance to mentor others.
We did host a visit from Houston's Veteran's Administration Hospital and plan to visit there to do a
presentation on VPP in the near future. I have also added an OSHA/VPP presentation to the agenda of
the Texas Association of Healthcare Facilities Management annual conference, which will be attended
by approximately 200 hospital representatives. Look for more hospitals in Texas to be VPP in the
next 3-4 years.
- We have improved the status of the facility equipment guarding, and we have seen increased
interest in the VPP program from our contractors and other Covanta facilities.
- The VPP effort has caused all our associates to become much more involved in the plant safety
process. All associates seem to pay much closer attention to each others actions than prior to the
process. We have placed detailed audits into operation, that looks at specific operational
behaviors; thus removing unsafe behaviors from the production floor.
- Working without having a recordable incident. Identifying and implementing Engineering Controls
that enhanced the operation and safety at the site. Continually improving safety awareness.
- Our success in the last year is with employee involvement, and thanks to Bill Harrington with OSHA
who is there to constantly give us support and offer suggestions to keep our employees involved.
- VPP is a great program that allows employees to drive the safety in the facility. Our facility has
improved tremendously since becoming a VPP site.
- Site had zero injuries and illnesses for Solutia employees for the first time in our history.
Combined injury/illness rate for company employees and contractors an all time low (0.62).
- Great program, plant is seeing a reduced injury rate as well as more employee involvement in the
safety program since we became a VPP site.
|