Making some of the world's most water-repellent
surfaces has become an ORNL niche.
|
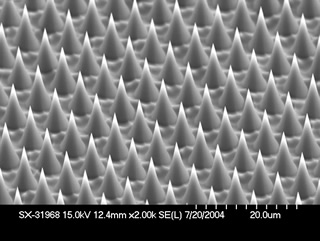
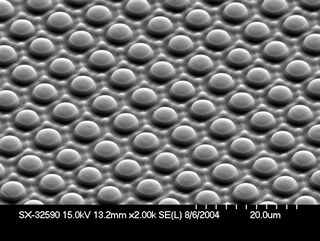
By varying the chemistry of the etching process and the glass composition, researchers produce different surface microstructures and aspect ratios that range from flat tops to cones with long needlelike structures.
|
In July 2003 when Brian D'Urso and his wife Vicky arrived at Oak Ridge National Laboratory as Eugene P. Wigner Fellows, Brian learned he had to find a new project quickly. The project he was supposed to join had fallen apart.
Two recollections from his days as an undergraduate at the California Institute of Technology and as a graduate student at Harvard University merged into a project idea. At Caltech, where he met his future wife, Brian heard a talk by Naval Research Laboratory scientists about a technique for making nanochannel glass. He found the technique fascinating. A few years later at Harvard, he heard a talk about superhydrophobic materials—waterproof surfaces that repel water almost as well as the water lily and young poplar tree leaves in East Tennessee.
"Unfortunately, honeysuckle vine leaves are also superhydrophobic," D'Urso says with a twinkle in his eye. "If you spray these leaves with Roundup, the herbicide beads up and rolls off to the ground. It's hard to get Roundup to stick. I don't think honeysuckle evolved to defeat Roundup but it works that way."
D'Urso shared his idea with his mentor, John Simpson, who suggested that the two write a proposal for seed money to cover the cost of Simpson's time on the project and the necessary research equipment. The seed money was granted by ORNL's internal funding program.
Over the next few years D'Urso, a physicist, and Simpson, an optical scientist, evolved into a team that can produce the world's most water-repellent surfaces over increasingly large areas by making either sheets or powder-based coatings.
During that time they worked with Mark Reeves of ORNL's technology transfer office to prepare patent applications. Today they hold several patents on a variety of new water-repellent materials that conceivably could be licensed to industrial firms or companies that have military contracts.
The possibilities are virtually limitless. Water sticking to windshields and rain-soaked clothing can be annoying. Cars hydroplaning over slightly wet road surfaces can be dangerous. Well-soaked building materials can morph into moldy health hazards.
The friction felt by water swishing against the hulls of ships causes drag, slowing the transport of commercial products between countries. A surface treatment with spikes might discourage algae from sticking to a ship's hull. One solution might be to coat these items with highly water-repellent powder-based paint. Another could be to cover them with highly waterproof sheets.
"Over the past five years, we have been focused on making extremely superhydrophobic materials and optimizing other properties," D'Urso says. "The purpose of the seed money project was to demonstrate that we could make a superhydrophobic material. Winning the seed money was a critical starting point that launched what turned out to be an interesting project."
In late 2003, the ORNL team contacted Naval Research Lab experts on nanochanneling to find out which glasses they should use for various applications.
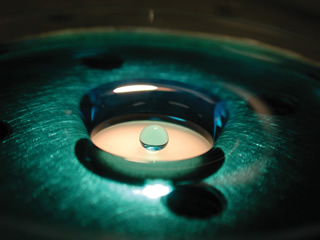
When water strikes the superhydrophobic disk, each drop is repelled to the water on one side. John Simpson calls this phenomenon the "Moses effect," after the Biblical leader who parted the Red Sea.
|
|
The ORNL physicists decided to use an outside company rather than the Naval Research Lab to make a desired material by glass drawing without disclosing the property they were trying to achieve.
"The company's glass experts said, 'This approach using glass drawing won't give you a material with nanoscale or micronsized channels,'" D'Urso says. "We replied, 'That's OK, we'll worry about what it turns into after that.' We were not trying to make a channeled structure. Rather, we were attempting to produce spikes in an ordered pattern on the surface. We got the material back, etched it with hydrofluoric acid, then processed and coated it to make a superhydrophobic material.
"The first time we made a glass product, it was extremely superhydrophobic. In fact, this first material is probably the most superhydrophobic we ever made because our first scanning electron microscope images showed that the spikes are really ordered and extremely sharp."
The researchers observed very little contact between water and the solid spiky surface. Air flowed through the pockets between the spikes.
"It was a great model to start with," D'Urso says. "We were excited because the behavior of the material was fantastic."
The spikes have a good aspect ratio—they are very tall compared with their average width and are highly protruding from the surface. The material cannot be made using standard lithography or etching processes.
At the end of summer 2005, D'Urso's financial support from his Wigner Fellowship and seed money was expended, so he and Simpson applied for and received Laboratory Directed Research and Development funding for Oct. 1, 2005 through Sept. 30, 2007.
The purpose of the LDRD project was to expand the range of superhydrophobic materials that could be made in the ORNL lab. Because they had demonstrated the value of the selected fabrication technique in making the first material, they received technology maturation funding to purchase a glass drawing tower so they could fabricate superhydrophobic glasses themselves.
For the LDRD project, D'Urso and Simpson continued to develop differential etching techniques to create spikes in materials drawn from the tower. Think of a pencil that consists of a "core" of graphite surrounded by wooden pencil "cladding." Sharpening the pencil is similar to etching the glass surface to get a spike.
In the first drawn-glass structure made at ORNL, the core glass was Pyrex, brand name for heat- and chemical-resistant glassware used for cooking. The cladding glass, which has a different composition, was the amorphous material used by the ORNL glass shop to make glass-to-metal seals.
"In differential etching, we immerse the core glass and cladding glass in hydrofluoric acid solution, which attacks both glasses made by glass drawing," D'Urso says. "The cladding glass is etched faster than the core glass. We first get an array of cores inside the cladding glass. The core glass starts to protrude because the cladding glass is etched back faster than the core glass."
The cores are etched from the sides and the top. They become sharpened because the tip of each protruding core is exposed to the acid for a longer time than the base of the core. Eventually the cores are sharpened like a pencil; any further etching removes more material but the tip remains sharp.
The first materials they made had spikes 7 microns apart—smaller than human hair, which averages 50 microns across. In the LDRD project, the researchers were able to shrink the spacing between spikes to 1 micron and even smaller.
"We could make one material and then vary the chemistry of the etching process to get different microstructures and aspect ratios varying from flat tops to long needlelike structures," D'Urso says. "To vary the aspect ratio, we used glasses of different composition or simply changed the etching process."
They also made glasses that spontaneously separated into two different structures, or phases, when heat treated. The two phases penetrated each other, creating a "spinodal" structure. "The two phases have a different composition," D'Urso says. "By using differential etching, we could get one phase to protrude, creating surface roughness."
The scientists also found that, by controlling the size of the protruding surface features, they could make superhydrophobic glasses that are transparent. Such glasses might be useful for windshields.
In 2006 the researchers experimented with different polymers and discovered they could make some polymers superhydrophobic. Simpson concentrated on making superhydrophobic powders by crushing and milling spinodal glass to create nanotextured particles that bond to glass surfaces. D'Urso focused on producing superhydrophobic polymer sheets.
For D'Urso, the collapse of his first ORNL project opened the door to another with tremendous potential.—Carolyn Krause
View Water-Repellent Glass Video
|