Case Studies
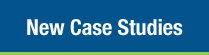
- Alliant Techsystems, Incorporated (PDF 666 KB)
- Owens Corning (PDF 659 KB)
- Southern California Gas Company (PDF 1.7 MB)
The Industrial Technologies Program's (ITP) Save Energy Now effort is helping U.S. industry reduce energy use, increase productivity, and avoid carbon emissions. Below you will find links to case studies that highlight the cost and energy savings achieved by manufacturers that have participated in Save Energy Now energy assessments.
While the findings vary for each plant, the case studies provide industry- and system-based examples of improvements your company can make to reduce energy consumption. Oftentimes savings can be achieved with a small investment and simple payback. Each case study features:
- A summary page with key findings
- Detailed information on manufacturing processes
- Energy savings recommendations
- Results and lessons learned
These publications are available as Adobe Acrobat PDFs. Download Adobe Reader.
Boise Inc.
Energy Assessment | |
Cost Savings |
$1 million |
---|---|
Natural Gas Savings |
154,000 MMBtu |
System Type |
Steam |
Industry |
The Boise Inc. paper mill in St. Helens, Oregon, lowered package boiler stack oxygen levels, modified existing piping to recover waste heat, and reduced the steam supplied to a parasitic load for a simple payback of less than 1 month. Information about the assessment was shared with other Boise Inc. mills.
Read the case study (PDF 528 KB)
Chrysler LLC
Energy Assessment | |
Cost Savings |
$627,000 |
---|---|
Natural Gas Savings |
70,000 MMBtu |
System Type |
Steam |
Industry |
Automotive |
Chrysler LLC's truck and minivan assembly complex in St. Louis, Missouri, optimized boiler operation, reduced boiler blowdown, and implemented an ongoing steam trap inspection and repair program and achieved a simple payback of just over 2 months. The assessment methodology is also being shared with other Chrysler plants.
Read the case study (PDF 578 KB)
Dow Chemical Company
Energy Assessment | |
Cost Savings |
$1.9 million |
---|---|
Natural Gas Savings |
272,000 MMBtu |
System Type |
Steam |
Industry |
Repairing steam leaks and replacing nonfunctional steam traps were easy, cost-effective steps that yielded Dow Chemical Company's Hahnville, Louisiana, plant a quick payback. The company also implemented ongoing steam trap maintenance and leak management programs.
Read the case study (PDF 550 KB)
Goodyear
Energy Assessment | |
Cost Savings |
$875,000 |
---|---|
Natural Gas Savings |
93,000 MMBtu |
System Type |
Steam |
Industry |
Automotive |
Goodyear's tire plant in Union City, Tennessee, optimized boiler operation, improved load management, and insulated tire presses for a simple payback of 2.5 months. The methodology and results from the assessment are also being shared with and applied to several other Goodyear facilities.
Read the case study (PDF 711 KB)
J.R. Simplot
Energy Assessment | |
Cost Savings |
$335,000 |
---|---|
Natural Gas Savings |
75,000 MMBtu |
System Type |
Steam |
Industry |
The J.R. Simplot Company's Don Plant in Pocatello, Idaho, optimized boiler operation, improved condensate recovery, and fixed steam traps and leaks for a simple payback of 6.5 months. Results are being shared with other Simplot facilities and other recommendations identified during the assessment are under consideration.
Read the case study (PDF 525 KB)
Kaiser Aluminum
Energy Assessment | |
Cost Savings |
$360,000 |
---|---|
Natural Gas Savings |
45,000 MMBtu |
System Type |
Process Heating |
Industry |
The Kaiser Aluminum plant in Sherman, Texas, adjusted controls and made repairs to a furnace for a simple payback of 1 month. Kaiser adopted DOE's Process Heating Assessment and Survey Tool (PHAST) software as the corporate diagnostic tool and has used it to evaluate process heating systems at five other aluminum plants.
Read the case study (PDF 637 KB)
Owens Corning
Energy Assessment | |
Cost Savings |
$252,000 |
---|---|
Utility Incentives |
$251,000 |
System Type |
Pumping, fan, compressed air |
Industry |
The Owens Corning glass fiber manufacturing plant in Santa Clara, California, used financial incentives from Silicon Valley Power (SVP) to cost-effectively implement several energy savings projects in its pumping, fan, and compressed air systems. These savings in turn enabled SVP to keep average power prices low and reduce emissions.
Read the case study (PDF 659 KB)
Shaw Industries
Energy Assessment | |
Cost Savings |
$872,000 |
---|---|
Natural Gas Savings |
93,000 MMBtu |
System Type |
Steam |
Industry |
Textiles |
The Shaw Industries carpet manufacturing plant #20 in Dalton, Georgia, optimized boiler operation and installed waste heat exchangers on two processes in the dye house and an economizer on one boiler, for a payback of 1.7 years. These results prompted plant #4, also located in Dalton, to participate in an assessment.
Read the case study (PDF 532 KB)
Terra Nitrogen
Energy Assessment | |
Cost Savings |
$3.5 million |
---|---|
Natural Gas Savings |
497,000 MMBtu |
System Type |
Steam |
Industry |
Terra Nitrogen's ammonia and fertilizer plant in Verdigris, Oklahoma, upgraded to more efficient condensing turbines and installed a loop dehydrator. To identify even more energy-saving opportunities, plant employees plan to continually analyze their steam system using DOE's Steam System Assessment Tool (SSAT) software tool.
Read the case study (PDF 497 KB)
U. S. Steel
Energy Assessment | |
Cost Savings |
$760,000 |
---|---|
Natural Gas Savings |
95,000 MMBtu |
System Type |
Process Heating |
Industry |
The U. S. Steel Minntac plant in Mt. Iron, Minnesota, identified energy savings opportunities in its process lines and validated natural gas savings from new burners that were installed prior to the assessment. The success led to additional assessments at U. S. Steel plants in Indiana and Michigan.
Read the case study (PDF 599 KB)
West Linn Paper Company
Energy Assessment | |
Cost Savings |
$379,000 |
---|---|
Natural Gas Savings |
497,000 MMBtu |
System Type |
Steam |
Industry |
West Linn Paper Company surveyed steam traps, added insulation, and re-evaluated the positioning of several steam headers to achieve savings. The plant, which is located in West Linn, Oregon, is utilizing DOE's SSAT software to consistently evaluate new projects.
Read the case study (PDF 636 KB)
Steel Industry
Save Energy Now Reveals New Opportunities for Steel Manufacturers to Reduce Costs and Energy Use (PDF 645 KB)
Related Links
The following links offer more information on plant assessments and resources for saving energy.
- Find companies similar to yours that have received assessments through the Participating Plants Web page.
- See ITP's BestPractices case studies for other demonstrated energy and process improvement projects and plant assessments.
- Identify energy savings opportunities in your company by utilizing ITP resources such as software tools, technical publications, and training.
For additional information, please contact the EERE Information Center online or call 1-877-337-3463.