
Hydrogen and Clean Fuels
Central Hydrogen Production
The focus of the Hydrogen from Coal Program Central Production RD&D effort is on those technologies that maximize hydrogen production and separate hydrogen from coal-derived synthesis gas, including efforts that reduce processing steps, combine functions, and significantly improve efficiency.
FutureGen |
DOE’s FutureGen initiative will serve as a research platform to establish the technical feasibility, economic viability, and broad acceptance of co-producing electricity and hydrogen from coal with zero emissions, including CO2. |
FutureGen is a government/ industry cost-shared project to build a 275-megawatt Integrated Gasification Combined-Cycle (IGCC) test facility for evaluating cutting-edge technologies, including those being developed by this and other R&D programs.
|
|
The initial step to produce hydrogen from coal involves coal gasification to produce synthesis gas, the same technology that can be used to produce electricity in integrated gasification combined cycle (IGCC) power plants. One promising option to improve the flexibility of gasification-based processes, called “co-production”, is to make both electric power and hydrogen by burning part of the clean syngas in a gas turbine, and converting the remainder to pure hydrogen, as in the DOE’s planned FutureGen test facility.
Today’s unit operations for hydrogen production from syngas include gas cleanup to remove impurities, heat exchange to cool and reheat the gas to match process requirements, water-gas-shift (WGS) catalytic reactors to maximize hydrogen content, and processes to separate hydrogen from other gases such as pressure swing absorption (PSA), cryogenics, or low temperature membrane systems. These processes are effective but also are expensive, complex, and energy-intensive. To meet the goals of the program, the cost of current technologies must be reduced. This can be done by improving efficiency of the process, and reducing capital and operating costs. Technologies that can combine or simplify the hydrogen production steps will make the overall process more efficient and less costly.
Central Production RD&D has three main thrusts. Advanced membrane technologies are under development that may allow more efficient separation of hydrogen and CO2. Process intensification technologies can be developed that combine multiple processes and simplify downstream processing. Advanced concepts may be found to produce hydrogen from coal in more direct or efficient ways.
R&D Needs
The synthesis gas must be cooled from more than 1,800ºF as it leaves the gasifier to ambient temperature for conventional gas cleanup. The gas must then be re-heated to 650–700ºF for the first of two water gas shift (WGS) catalytic reactors for production of additional hydrogen. WGS requires several steps because of unfavorable chemical equilibria at higher temperatures, and slow kinetics at lower temperatures. Complex systems with a large number of process units require a larger plant footprint and are nearly always more difficult to improve in terms of efficiency. “Process intensification,” in which multiple process function technologies are integrated into one process step – such as combined gas cleanup, WGS reaction, and hydrogen separation – offers potential advantages in scalability of the design, as well as better efficiency and lower costs.
- One such process intensification is combining advanced WGS catalysts with hydrogen separation membranes (see below) to form a “membrane reactor” that synergistically improves the percentage of hydrogen in the syngas at the same time that it separates out a pure hydrogen stream. Such systems can eliminate the need for two separate stages, potentially reducing capital costs.
- Impurities in the synthesis gas may act as poisons, deactivating the WGS catalyst and damaging the structural integrity of the catalyst bed. Improved catalysts and reactor systems are needed to maintain catalyst activity, and may, in some cases, reduce gas cleanup requirements upstream of the WGS reactor.
- Efficiency requirements for advanced concepts (i.e., process intensification) may require “warm gas cleanup” which will have higher levels of sulfur than conventional cleaning, which may in turn require water-gas shift and membrane separation with sulfur, ammonia and chloride tolerances that are higher than current technologies.
Several advanced technology options are under development to separate and purify hydrogen from cleaned and hydrogen-maximized syngas. Some of these are membrane-based and make use of microporous, metallic, or ceramic membranes operating at elevated temperatures, with a variety of chemical and/or physical mechanisms that provide separation. Successful separation membranes must have high hydrogen flux at low pressure drops, tolerance to contaminants, especially sulfur, low cost, and operation at system temperatures of 250 – 500°C. Some hydrogen membrane technologies at the research phase have the potential to provide hydrogen purity above 99.99 percent. Other technologies focus on removal of CO2 from the gas stream. However, there are barriers that must still be overcome to reduce the cost and meet the other requirements. A better understanding of membrane separation mechanisms may give rise to new ideas. Methods must be found to improve separation and throughput and prevent membranes from becoming less effective over time. Scaleup studies must determine their potential for lower cost and efficient operation in integrated systems. Large-scale manufacturing methods for defect-free membranes and modules must be developed. Better ways are needed to make high-temperature, high-pressure seals using ceramic substrates. To protect fuel cells, the separation processes must remove carbon monoxide in hydrogen product streams to less than 10 parts per million (ppm), and sulfur-containing compounds to less than 10 parts per billion (ppb).
Some advanced concepts may significantly change the gasification process itself. Chemical looping is an advanced concept for producing and separating streams of hydrogen and CO2 from mixed gases and trace constituents. In chemical looping processes, combustion or gasification of a fossil fuel occurs in two steps: 1) air is used to oxidize a metallic oxygen carrier; 2) the metallic oxide carrier is used to oxidize a fuel (with the carrier reduced to a lower oxidized state). In this process, the carrier is circulated in two separate reactors: a combustion or gasification step where the oxygen carrier reacts with the fuel, and an oxygen regeneration step in which the carrier is oxidized with air. This process is an alternative to expensive cryogenic oxygen production, and may have advantages to membrane separation of oxygen since the two-step looping process can occur at low pressures. The process can result in separate streams of hydrogen and CO2 without use of membranes.
Goal and Milestones – Central Production Pathway
Goal: By the end of 2015, demonstrate a 60 percent efficient, near-zero emissions, coal-fueled hydrogen and power co-production facility which reduces the cost of hydrogen by 25 percent compared to current coal-based technology.
Milestones:
- By the end of 2008, make a go/no-go decision on further development of advanced WGS reaction technologies
- By the end of 2011, complete development of pre-engineering modules for producing high-purity hydrogen, based on integrated process studies
- By the end of 2013, complete design and construction of engineering scale modules for hydrogen production from coal gasification combined-cycle co-production plant
- By the end of 2015, demonstrate hydrogen modules integrated into a near-zero emission plant concept producing hydrogen and electric power with sequestration at a 25 percent lower cost (to produce hydrogen)
Accomplishments and Current Activities
Accomplishments since the 2004 program start include development of a commercially ready microporous hydrogen separation membrane, scale-up of a hydrogen separation ceramic membrane for FutureGen, development of novel metal alloys and cermet membranes, testing of membranes in a high pressure hydrogen test facility, development of specialized membrane seals brazing techniques, development of bench-scale membrane reactors for membrane testing, and development of computational models to predict membrane performance. Pilot-scale fabrication tests were conducted for one-meter-long hydrogen membranes.
Current research topics in the Central H2 Production Pathway include the following objectives:
- Develop advanced shift catalysts that are more active and are impurity-tolerant, conduct the WGS reaction using a high-temperature membrane without added catalyst, and develop integrated shift-membrane separation technology.
- Link hydrogen separation membrane development work to material surface studies in order to understand effects of impurities and operating conditions on membrane performance, identify low-cost materials, and develop membrane seal and fabrication technologies for module preparation and scale-up.
- Conduct RD&D for other advanced separation systems such as PSA, solvents, and reverse selective systems. Develop reverse selective membranes, advanced adsorption, hydrates, or other novel technologies for the cost-effective capture of CO2 from mixed gas streams.
- Develop polishing filter technologies that enable hydrogen product streams to meet fuel quality requirements for PEM fuel cells efficiently and at low cost.
- Investigate novel process concepts that integrate several processes – gas cleanup, WGS reaction, and hydrogen separation – into one step, and investigate novel, “out-of-the-box” technologies that can produce hydrogen from coal directly or indirectly.
- Demonstrate and test advanced technologies to confirm laboratory, bench-scale, and pre-engineering module results.
Hydrogen Central Production Pathway R&D projects are listed in the table below.
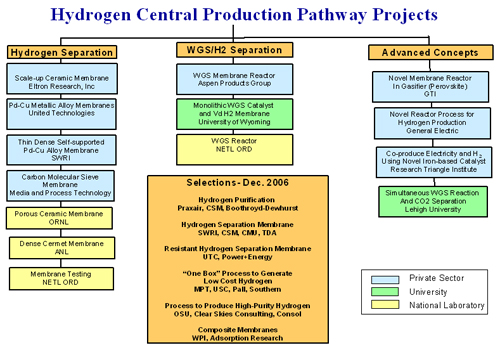
The following are recent fact sheets for Hydrogen and Clean Fuels Central Production Pathways projects:
Other program elements within Hydrogen & Clean Fuels Technology include the following:
|